Understanding PLCs: Uses of Programmable Logic Controllers
This article demystifies what a PLC is used for, how it works, and why it’s crucial in today’s industrial landscape. Whether you’re new to the concept or seeking to deepen your understanding, read on to discover the pivotal role of PLCs in automating industrial processes.
Table of Contents
What Is a PLC and How Does It Work?
A Programmable Logic Controller (PLC) is a specialized industrial computer designed to automate and control processes in real time. Unlike regular computers, PLCs are built to withstand harsh environmental conditions such as extreme temperatures, humidity, and electrical noise, making them ideal for industrial settings.
Components of a PLC
A typical PLC system comprises:
- Central Processing Unit (CPU): The brain that executes the PLC program.
- Input Modules: Receive signals from input devices like sensors, switches, and buttons.
- Output Modules: Send signals to output devices such as motors, valves, and lights.
- Power Supply: Provides the necessary power to the PLC.
- Programming Device: Used to program and configure the PLC, often via specialized programming software.
How Does a PLC Operate?
A PLC operates by continuously cycling through three main steps:
- Input Scan: The PLC receives input data from connected input devices.
- Program Execution: Processes the input data using the program logic defined in the PLC program.
- Output Scan: Sends commands to output devices based on the processed data.
This cyclic process allows the PLC to monitor and control processes efficiently, ensuring precise operation of machinery and systems.
Why Are PLCs Used in Industrial Automation?
PLCs are used extensively in industrial automation due to their reliability, flexibility, and efficiency. Here are key reasons why industries use PLCs:
Reliability and Durability
- Rugged Design: PLCs are built to operate under tough conditions, minimizing downtime.
- Consistent Performance: They provide stable control over processes, critical for maintaining quality.
Flexibility and Scalability
- Modular Structure: Modular PLCs like Mitsubishi PLC allow easy expansion by adding PLC modules.
- Adaptability: Programs can be modified to accommodate changes in the production process without altering hardware.
Real-Time Operation
- Immediate Response: PLCs operate in real time, ensuring processes react swiftly to input
- Precision Control: Manage complex tasks with high accuracy, essential for modern industrial processes.
Simplification of Complex Systems
- Replaces Relay Logic Systems: Simplifies wiring and reduces the physical components needed.
- Enhanced Troubleshooting: Easier to identify issues within the PLC program compared to traditional systems.
Types of PLCs: Choosing the Right Programmable Logic Controller
When it comes to choosing a PLC, understanding the different types of PLCs is essential.
Modular PLCs
- Description: Consist of separate modules for the CPU, inputs, outputs, and communication protocols.
- Advantages: Highly scalableand customizable to specific needs.
- Applications: Suitable for complex processes requiring numerous inputs and outputs.
Compact PLCs (Standard PLCs)
- Description: All-in-one units with fixed I/O capabilities.
- Advantages: Cost-effective and space-saving.
- Applications: Ideal for simpler control tasks with limited I/O requirements.
Rack-Mounted PLCs
- Description: Modules are mounted on racks, allowing for extensive expansion.
- Advantages: Support a large number of I/O points and high processing power.
- Applications: Large-scale industrial applications like process control in oil refineries.
When selecting a PLC, consider factors such as:
- Process Complexity: The nature of the tasks and control required.
- I/O Requirements: Number and type of input and output devices.
- Environmental Conditions: Temperature, dust, moisture levels in the operating environment.
- Communication Needs: Integration with SCADA systems, HMIs, and other external devices.
Brands like Omron PLC and Schneider PLC offer various PLCs with different PLC features to match diverse industrial needs.
How Are PLCs Programmed? Understanding PLC Programming Languages
PLCs are programmed using specialized programming languages that instruct the PLC on how to respond to specific input conditions.
Common PLC Programming Languages
- Ladder Logic (Ladder Diagram)
- Most commonly used PLC programming language.
- Resembles traditional relay logic, making it intuitive for engineers familiar with electrical circuits.
- Ideal for simple control and sequencing operations.
- Structured Text
- High-level textual language similar to Pascal.
- Suitable for complex mathematical functions and algorithms.
- Function Block Diagram (FBD)
- Graphical language using blocks to represent functions.
- Excellent for analog process control and function block
- Sequential Function Chart (SFC)
- Represents processes as a series of steps and transitions.
- Useful for batch processes and sequential functions.
- Instruction List
- Low-level textual language resembling assembly code.
- Efficient but less intuitive due to its terse syntax.
Programming Concepts
- Inputs and Outputs: Understanding how input deviceslike sensors and switches affect outputs.
- Control Logic: Developing program logicthat defines the relationship between inputs and outputs.
- Timers and Counters: Managing events based on time or counts.
- Data Handling: Working with variables, arrays, and data storage.
Programming Software
Manufacturers often provide proprietary programming software for their PLCs. This software includes tools for writing, simulating, and debugging PLC programs.
Using a PLC effectively requires familiarity with these programming concepts and languages. By leveraging the appropriate language, engineers can create efficient and robust control systems.
PLCs, SCADA Systems, and HMIs: How Do They Operate Together?
In the realm of industrial automation, PLCs often function alongside SCADA systems and HMIs to form an integrated control system.
PLCs (Programmable Logic Controllers)
- Role: Execute control at the machine or process level.
- Functionality: Process input dataand control output devices in real time.
HMIs (Human-Machine Interfaces)
- Role: Provide an interfacebetween operators and machines.
- Functionality: Display process data, allow user inputs, and visualize system statuses.
- Examples: Proface HMI, Mitsubishi HMI.
SCADA Systems (Supervisory Control and Data Acquisition)
- Role: Oversee and control multiple PLCs across a facility or region.
- Functionality: Collect data from PLCs, provide supervisory control, and facilitate data analysis.
- Importance: Critical for large-scale operations like water treatment plants and power grids.
Communication Protocols
- Purpose: Enable data exchange between PLCs, HMIs, and SCADA systems.
- Common Protocols: Modbus, Profibus, Ethernet/IP.
- Benefits: Allow for coordinated control, data logging, and remote monitoring.
By integrating these systems, industries achieve seamless automation, improved efficiency, and better decision-making capabilities.
Applications of PLCs in Industrial Automation
PLCs are used across various industries due to their versatility. Here are some typical applications:
Manufacturing
- Assembly Lines: Control robotic arms, conveyors, and tooling machines.
- Quality Control: Monitor production parameters to ensure consistency.
Energy Sector
- Power Generation: Manage turbines, generators, and distribution systems.
- Oil and Gas: Control drilling operations and pipeline systems.
Water and Waste Management
- Treatment Plants: Regulate pumps, mixers, and chemical dosing.
Automotive Industry
- Production Lines: Coordinate complex tasks in vehicle assembly.
Building Automation
- HVAC Systems: Control heating, ventilation, and air conditioning.
- Lighting Systems: Automate lighting based on occupancy or time of day.
By using a PLC, industries can automate processes, enhance safety, reduce human error, and optimize operations.
Real-World Example: Control of an Entire Production Line
A PLC can manage an entire production line by:
- Receiving Inputs: Collecting data from sensors(temperature, pressure, proximity).
- Processing Data: Executing the PLC programto determine necessary actions.
- Controlling Outputs: Operating motors, actuators, and other devices to perform tasks.
- Communicating: Sharing information with SCADA systemsand HMIs for monitoring and control.
This integration minimizes downtime and enhances productivity.
Frequently Asked Questions
The most commonly used to program PLCs is Ladder Logic, which resembles electrical relay logic diagrams. It is intuitive for those familiar with circuit schematics and is ideal for simple to moderately complex control tasks.
PLCs communicate using various ports and communication protocols such as Ethernet/IP, Modbus, and Profibus. These protocols enable data exchange with HMIs, SCADA systems, and other external devices, facilitating integrated control and monitoring.
- Flexibility: Easily reprogrammed for different tasks.
- Space Saving: Reduces wiring complexity.
- Reliability: Lower failure rates due to fewer mechanical components.
- Advanced Functions: Capabilities like data logging, complex calculations, and network communication.
Consider:
- Process Requirements: Complexity and control needs.
- I/O Count: Number of inputs and outputs required.
- Environmental Factors: Operating conditions like temperature and dust.
- Scalability: Potential future expansion.
- Compatibility: Integration with existing systems.
Yes, PLCs can process both analog signals (variable values) and discrete signals (on/off states). Input modules are available for various signal types, enabling PLCs to handle diverse data inputs.
Power your projects with brand-new, original Omron, Mitsubishi, Schneider PLC – in stock, ready now!
Conclusion
- PLCsare specialized industrial computers used to automate and control machinery and processes in real time.
- They operate by processing input datafrom input devices and controlling output devices based on the programmed control logic.
- Programming a PLCinvolves using languages like Ladder Logic, Structured Text, and Function Block Diagram.
- Types of PLCsinclude modular PLCs, compact PLCs, and rack-mounted PLCs, each suited to different applications.
- PLCs often work alongside HMIsand SCADA systems to form comprehensive automation solutions.
- Choosing a PLCrequires considering process complexity, I/O needs, environmental conditions, and scalability.
- PLCs are usedacross various industries, enhancing efficiency, reliability, and safety in operations.
Looking for new, original PLCs for your projects? At Kwoco, we stock the latest PLCs from top brands like Omron, Mitsubishi, and Schneider. Shop with confidence—fast shipping, guaranteed quality! Buy Now
Contact Us
Just fill out your name, email address, and a brief description of your inquiry in this form. We will contact you within 24 hours.
You May Also Find These Topics Interesting

Common Faults and Troubleshooting of Omron PLC
As a global leader in automation solutions, Omron provides a comprehensive range of Programmable Logic Controllers (PLCs), including the classic CP series, the powerful CJ series, and the future-oriented NX/NJ series. These controllers are widely deployed across diverse industries such as manufacturing, packaging, logistics, and energy. Serving as the “brain” of automated systems, Omron PLCs execute control logic with precision and coordinate the operation of various components.
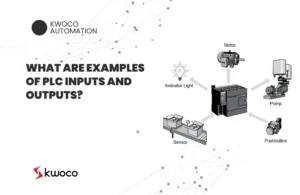
What are Examples of PLC Inputs and Outputs?
What are Examples of PLC Inputs and Outputs? In industrial automation, PLC (Programmable Logic Controller) systems are the brains behind
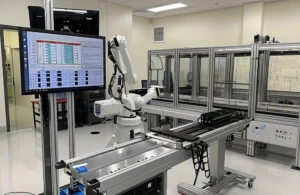
Understanding Human-Machine Interfaces (HMIs) in Industrial Automation
Understanding Human-Machine Interfaces (HMIs) in Industrial Automation In the rapidly evolving world of industrial automation, Human-Machine Interfaces (HMIs) play a