What are Examples of PLC Inputs and Outputs?
- kwoco-plc.com
- September 19, 2024
- 12:58 am
In industrial automation, PLC (Programmable Logic Controller) systems are the brains behind countless processes. But what exactly goes in and out of a PLC? Understanding this is crucial to running efficient operations.
PLC inputs and outputs refer to the devices that send and receive data to and from the PLC. These can include sensors, switches, motors, and lights, among others. The PLC interprets these signals and performs pre-programmed actions based on the input received.
You may be wondering, “What are some real-world examples of PLC inputs and outputs?”
Table of Contents
What are PLC Inputs?
PLC inputs are essentially signals that the PLC reads from devices like sensors or switches. These inputs inform the PLC of conditions happening in the environment.
Some common examples of PLC inputs include:
- Push Buttons: These are manual input devices, such as emergency stops or start buttons. When someone presses a button, the PLC receives a signal to initiate or stop a process.
- Limit Switches: Often used in automated machinery, these switches send signals when a moving part reaches a specific position.
- Proximity Sensors: Used to detect the presence or absence of an object without any physical contact. Common in conveyor belts to detect items passing by.
- Temperature Sensors: These provide data on the temperature of a machine or environment, allowing the PLC to control heating or cooling systems.
- Pressure Sensors: Widely used in industrial environments, pressure sensors inform the PLC about fluid or air pressure levels, triggering processes accordingly.
Each input provides crucial data for the PLC to function correctly. If a sensor fails, the entire system may stop.
What are PLC Outputs?
Now that we understand inputs, let’s move on to outputs. PLC outputs are signals sent from the PLC to devices that perform actions based on the programmed logic.
Here are some examples of PLC outputs:
- Motors: PLCs control motors that drive conveyors, fans, and pumps. The PLC sends signals to turn them on or off, control speed, or change direction.
- Solenoids: A solenoid valve controls the flow of air or liquids. The PLC triggers the valve to open or close based on inputs from pressure or flow sensors.
- Alarms: When certain conditions are met (such as exceeding temperature limits), the PLC can trigger alarms to alert operators.
- Lights: Signal lights are used to indicate the status of a process, like green for “running” or red for “stopped.” The PLC sends outputs to these lights based on the system’s state.
- Relays: Relays control high-powered equipment like heaters or large motors. The PLC outputs a signal to activate or deactivate these relays as needed.
Why Do Inputs and Outputs Matter in Automation?
Without proper input and output configurations, a PLC cannot function. The selection of inputs and outputs directly affects the reliability and efficiency of automated processes. But how do you choose the right ones?
The answer depends on the application. A food processing plant might need temperature sensors and motor controls, while a bottling factory might rely on proximity sensors and solenoids.
What are Digital vs. Analog Inputs and Outputs?
You’ve probably heard of digital and analog signals, but what do they mean in the context of PLCs?
Digital Inputs/Outputs: These are binary, meaning they have two states—on or off. Think of a light switch; it’s either up (on) or down (off). Digital inputs and outputs are simple but widely used in PLC applications.
Analog Inputs/Outputs: Analog signals provide a range of values. For example, a temperature sensor might send an analog signal representing temperatures from 0°C to 100°C. The PLC reads these varying values and adjusts outputs like heaters or fans accordingly.
Both digital and analog inputs and outputs are vital, depending on the complexity of the system.
Power your projects with brand-new, original Omron, Mitsubishi, Schneider PLC – in stock, ready now!
Can PLC Inputs and Outputs Be Wired or Wireless?
Yes, PLC systems can support both wired and wireless connections. However, each has its pros and cons.
Wired Inputs/Outputs: More reliable and immune to interference. However, wired systems can be expensive and difficult to install in large or complex facilities.
Wireless Inputs/Outputs: Easier to install and more flexible, especially in large industrial settings. But they may be subject to interference and can have security concerns.
How Do You Program Inputs and Outputs in a PLC?
For example, through the ladder logic, a graphical programming language resembling electrical diagrams. Each input/output is assigned to a specific address in the PLC’s memory. When the input condition is met, the PLC performs the corresponding output action.
For example, if a push button (input) is pressed, the ladder logic could instruct the PLC to turn on a motor (output).
Conclusion
In industrial automation, PLC inputs and outputs are the foundation of any system. From push buttons and sensors to motors and relays, these components enable machines to operate smoothly and efficiently. Whether you’re using wired or wireless, digital or analog, choosing the right inputs and outputs for your application is key to optimizing performance.
At Kwoco, we specialize in providing high-quality PLCs from brands like Omron, Mitsubishi, and Schneider. If you want to know more about how PLCs can fit into your system, feel free to reach out!
Contact Us
Just fill out your name, email address, and a brief description of your inquiry in this form. We will contact you within 24 hours.
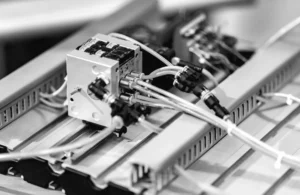
Why Your PLC Needs a Separate Power Supply
Why Your PLC Needs a Separate Power Supply Have you ever wondered why PLC systems often require a separate power
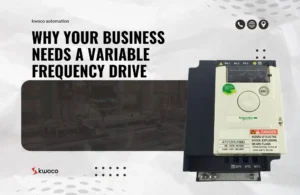
Why Your Business Needs a Variable Frequency Drive
Why Your Business Needs a Variable Frequency Drive When managing industrial operations, optimizing energy efficiency while maintaining performance is crucial.
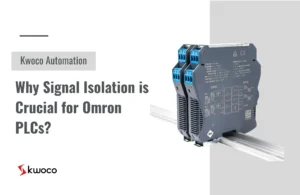
Why Signal Isolation is Crucial for Omron PLCs?
Why Signal Isolation is Crucial for Omron PLCs? In the world of industrial automation, signal interference is a silent killer.