Güvenlik PLC'si Nedir? Güvenlik ve Otomasyonu Anlamak
Güvenlik PLC'si, özel bir türdür PLC bir otomasyon sistemi içindeki güvenlikle ilgili işlevleri yönetmek ve izlemek için tasarlanmıştır. Standart PLC'lerin aksine, güvenlik PLC'leri katı güvenlik standartlarına uymak için üretilmiştir ve olası tehlikelerin etkili bir şekilde azaltılmasını sağlar.
İçindekiler
Güvenlik PLC’si Nedir?
Bir Güvenlik PLC'si, endüstriyel bir ortamda güvenlikle ilgili görevleri ele almak için özel olarak tasarlanmıştır. Bu cihazlar, makinelerin güvenli ve öngörülebilir bir şekilde çalışmasını sağlayarak kaza riskini azaltmak için tasarlanmıştır.
Güvenlik PLC'lerinin mimarisi, güvenilirliği artırmak ve arıza olasılığını en aza indirmek için yedekli bileşenleri içerir.
Güvenlik PLC'lerinin Temel Özellikleri
- Entegre Güvenlik Fonksiyonları: Güvenlik PLC'leri, güvenlik açısından kritik operasyonları izleyen özelliklerle donatılmıştır. Arızaları ve anormallikleri tespit ederek sistemin uygun şekilde yanıt vermesini sağlayabilirler.
- Güvenlik Standartlarına Uygunluk:Güvenlik PLC'leri, elektrik/elektronik/programlanabilir elektronik güvenlikle ilgili sistemlerin fonksiyonel güvenliğini tanımlayan IEC 61508 gibi uluslararası güvenlik standartlarına uymalıdır.
- Program Akış Kontrolü:Güvenlik PLC'lerinde etkili program akış kontrolü, güvenlik fonksiyonlarının güvenli ve öngörülebilir bir şekilde yürütülmesini garanti eder.
Güvenlik PLC'lerinin Uygulamaları
Güvenlik PLC'leri aşağıdakiler de dahil olmak üzere çeşitli uygulamalarda kullanılır:
- Makine Güvenliği:İşçileri korumak için ışık perdeleri ve emniyet kilitleri gibi güvenlik cihazlarını kontrol ederler.
- Süreç Otomasyonu: Tehlikeli ortamlarda, güvenlik PLC'leri güvenliği koruyarak süreçlerin otomasyonunu sağlar.
Güvenlik PLC'leri Standart PLC'lerden nasıl farklıdır?
Her iki PLC türü de otomasyonda önemli roller oynarken, güvenlik PLC'leri ve standart PLC'ler farklı işlevlere sahiptir. Standart PLC'ler öncelikle genel kontrol görevleri için kullanılırken, güvenlik PLC'leri koruma operasyonlarına odaklanır.
Farklılıklar Açıklandı
- İşlevsellik: Standart PLC'ler rutin operasyonel görevleri güvenlik hususlarını düşünmeden yönetirken, güvenlik PLC'leri güvenlik fonksiyonlarını programlamalarına entegre eder.
- Güvenlik Bütünlüğü Seviyeleri (SIL): Güvenlik PLC'leri, standart PLC'lerin karşılamadığı belirli SIL gereksinimlerini karşılamalıdır. Bu, güvenlik PLC'lerini tehlikeli durumlarda daha güvenilir hale getirir.
- Programlama Karmaşıklığı: Güvenlik PLC programlaması genellikle ek güvenlik önlemleri ve protokolleri içerdiğinden standart PLC programlamaya kıyasla daha karmaşıktır.
Doğru PLC'yi Seçmek
Bir güvenlik PLC'si ile standart bir PLC arasında karar verirken aşağıdakileri göz önünde bulundurun:
- Güvenlik Gereksinimleri:Uygulamanız tehlikeli ortamları kapsıyorsa, güvenlik PLC'sini tercih edin.
- Mevzuata Uygunluk:Sektörünüzle ilgili güvenlik standartlarına uyumu sağlayın.
Güvenlik PLC'sinin temel Güvenlik Fonksiyonları nelerdir?
Güvenlik fonksiyonları bir güvenlik PLC'sinin çalışması için hayati öneme sahiptir. Bu fonksiyonlar arızaları tespit etmek ve makinelerin güvenli bir şekilde çalışmasını sağlamak için tasarlanmıştır.
Ortak Güvenlik Fonksiyonları
- Acil Durdurma:Kazaları önlemek için operasyonları derhal durdurmayı amaçlayan temel bir güvenlik fonksiyonu.
- Güvenli Tork Kapalı (STO): Bu fonksiyon, makinenin etkili bir şekilde durdurulması için kritik öneme sahip olan torkun oluşmasını önleyerek motora giden gücü keser.
- Güvenlik İzleme: Güvenlikle ilgili operasyonların sürekli izlenmesi, herhangi bir anormalliğin tespit edilmesini ve derhal ele alınmasını sağlar.
Güvenlik Fonksiyonlarının Uygulanması
Güvenlik fonksiyonlarının entegre edilmesi şunları gerektirir:
- Dikkatli Programlama: PLC programlaması tüm olası arıza modlarını hesaba katmalıdır.
- Düzenli Test: Güvenlik fonksiyonlarının her koşulda doğru şekilde çalışmasını sağlamak için rutin testlerden geçirilmesi gerekir.
Güvenlik Bütünlüğü Düzeylerini (SIL) Anlamak
Güvenlik Bütünlüğü Seviyesi (SIL), bir güvenlik sistemi içindeki güvenlik işlevlerinin güvenilirliğinin bir ölçüsüdür. SIL 1 (en düşük) ile SIL 4 (en yüksek) arasında değişir ve bir güvenlik işlevinin tehlikeli bir olaya yanıt olarak doğru şekilde performans gösterme olasılığını gösterir.
SIL'in Önemi
SIL'i anlamak şunlar için önemlidir:
- Risk değerlendirmesi:Bir prosesle ilişkili risklere bağlı olarak gerekli güvenlik önlemlerinin belirlenmesi.
- Güvenlik PLC'lerinin Seçimi:Seçilen güvenlik PLC'sinin uygulamanız için gerekli SIL'i karşılamasını sağlamak.
IEC 61508'e uygunluk
IEC 61508, çeşitli SIL seviyelerine ulaşmak için gereklilikleri tanımlar ve güvenlik sistemlerinin tasarımı ve uygulanmasına rehberlik eder. Bu standarda uyum, güvenlik PLC'lerinin sağlam ve güvenilir olmasını sağlar.
İşyeri Güvenliği için Güvenlik PLC'leri neden önemlidir?
Güvenlik PLC'lerinin endüstriyel ortamlara entegrasyonu işyeri güvenliğini önemli ölçüde artırır. Makine ve otomasyon süreçleriyle ilişkili riskleri yönetmek için sistematik bir yaklaşım sağlarlar.
İşyeri Güvenliğini Artırmak
- Kaza Önleme:Güvenlik PLC'leri, güvenlik fonksiyonlarını kontrol ederek yaralanmalara veya ölümlere yol açabilecek kazaların önlenmesine yardımcı olur.
- Artan Üretkenlik:Daha güvenli bir çalışma ortamı, çalışanların kendilerini çevrelerinde güvende hissetmeleri nedeniyle çalışanların moralinin ve üretkenliğinin artmasına yol açar.
Mevzuata Uygunluk
Birçok endüstri sıkı güvenlik standartlarına ve yönetmeliklerine tabidir. Güvenlik PLC'lerinin uygulanması yalnızca uyumluluğu garantilemekle kalmaz, aynı zamanda işyeri güvenliğine olan bağlılığı da gösterir.
Sıkça Sorulan Sorular
Güvenlik PLC'leri güvenlik fonksiyonlarını yerine getirmek ve sıkı güvenlik standartlarına uymak üzere tasarlanırken, standart PLC'ler genel kontrol görevleri için kullanılır.
Güvenlik PLC'leri makine güvenliği, proses otomasyonu ve güvenliğin öncelikli olduğu her türlü uygulamada yaygın olarak kullanılır.
SIL seviyeleri, güvenlik fonksiyonlarının güvenilirliğini belirlemeye yardımcı olur ve farklı süreçlerle ilişkili risklere göre güvenlik PLC'lerinin seçimine rehberlik eder.
Düzenli testler, güvenlik fonksiyonlarının doğru şekilde çalışmasını ve tehlikelerin etkili bir şekilde tespit edilip azaltılmasını sağlar.
Güvenlik standartları, güvenlik PLC'lerinin tasarımı, uygulanması ve çalıştırılması için yönergeler sunarak uyumluluğu ve güvenilirliği garanti altına alır.
Projelerinize yepyeni, orijinal Omron, Mitsubishi, Schneider PLC'lerle güç katın - stokta, hemen kullanıma hazır!
Çözüm
Özetle, güvenlik PLC'leri modern otomasyon sistemlerinde temel bileşenlerdir ve işyeri güvenliğinin önceliklendirilmesini sağlar. Hatırlanması gereken temel noktalar şunlardır:
- Güvenlik PLC'leri güvenlik açısından kritik uygulamalar için tasarlanmıştır.
- Bunlar önemli ölçüde farklıdır standart PLC'ler işlevsellik ve güvenlik standartlarına uygunluk açısından.
- Anlamak Güvenlik Bütünlüğü Seviyeleri (SIL) Uygun güvenlik PLC'sini seçmek için çok önemlidir.
- Güvenli bir çalışma ortamının sürdürülebilmesi için güvenlik fonksiyonlarının düzenli olarak test edilmesi ve izlenmesi gereklidir.
Projeleriniz için yeni, orijinal PLC'ler mi arıyorsunuz? Kwoco'da, en iyi markaların en son PLC'lerini stoklarız: Omron, Mitsubishi, Ve Schneider. Güvenle alışveriş yapın—hızlı kargo, garantili kalite! Hemen Satın Al
Bize Ulaşın
Bu forma adınızı, e-posta adresinizi ve sorunuzun kısa bir açıklamasını girmeniz yeterlidir. 24 saat içinde sizinle iletişime geçeceğiz.
Bu Konuları da İlginizi Çekebilir
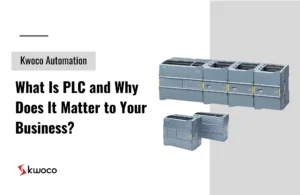
PLC Nedir ve İşletmeniz İçin Neden Önemlidir?
PLC Nedir ve İşletmeniz İçin Neden Önemlidir? Endüstriyel otomasyondaki sürekli değişiklikler karşısında bunalmış hissediyor musunuz?
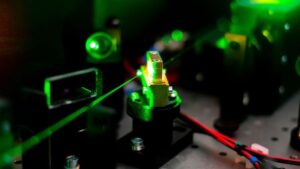
Fotoelektrik Sensör Kablolaması ve Sorun Giderme için Tam Kılavuz
Fotoelektrik sensör kurulumu ve yapılandırmasıyla mı mücadele ediyorsunuz? Bu kapsamlı kılavuz, endüstriyel otomasyon uygulamalarında fotoelektrik sensörlerin kablolanması, kurulumu ve sorun gidermesi hakkında bilmeniz gereken her şeyi size anlatacaktır.
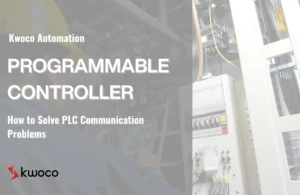
PLC İletişim Sorunları Nasıl Çözülür
PLC İletişim Sorunları Nasıl Çözülür Programlanabilir Mantık Denetleyicileri (PLC'ler) modern endüstriyel otomasyonun omurgasıdır. Bunlar uzmanlaşmıştır