Demystifying the Disconnect Switch: Your Essential Guide to Electrical Safety
Table of Contents
What is a Disconnect Switch and Why is it Important?
As someone deeply involved in industrial automation, I’ve seen firsthand the crucial role that disconnect switches play in our daily operations. A disconnect switch, also known as an electrical disconnect or safety switch, is a crucial component in any electrical system.
It’s a manually operated device designed to completely disconnect power from a circuit or piece of equipment. You might ask, why is this so important?
Well, imagine you’re working on a complex piece of machinery in a bustling factory. Suddenly, a malfunction occurs, or you need to perform routine maintenance. The first step to ensuring safety is to cut off the electrical supply.
This is where the disconnect switch comes into play. It allows you to safely interrupt the flow of electrical current, preventing accidents and protecting personnel. It’s not just about preventing electrical shocks; it’s also about protecting the equipment itself from damage due to overcurrent or a short circuit.
In my experience, the importance of a reliable disconnect switch cannot be overstated. It’s the first line of defense in maintaining electrical safety in any industrial setting.
Without it, we’d be exposing ourselves and our teams to unnecessary electrical risks. There was a situation in my plant. We had to perform a quick fix on one of our Omron PLC. It is much easier to do it quickly if there is a reliable disconnect switch. In addition, I would like to add that it is simply necessary to provide the factory with a circuit protection capability.
What are the Different Types of Disconnect Switches?
Now, let’s talk about the variety of disconnect switches available. They are not all the same, and choosing the right kind of switch depends on your specific application. The most common distinction is between fusible and non-fusible disconnect switches.
Fusible disconnect switches combine the function of a switch with that of a fuse. This means they not only open and close a circuit but also protect against overcurrent.
These switches are commonly designed so that when an overcurrent situation occurs, the fuse blows, interrupting the circuit and preventing damage to the electrical system.
On the other hand, non-fusible disconnect switches are simpler in switch design; they only serve to open and close the circuit without providing circuit protection. They’re used when overcurrent protection is provided elsewhere in the electrical circuit.
Another type is the battery disconnect switch, which, as the name suggests, is used to isolate a battery from the electrical system. These are crucial in applications where batteries power critical systems, such as in emergency backup power supplies.
We use them extensively in our uninterruptible power supply (UPS) systems to ensure we can safely isolate and maintain the batteries without disrupting the critical operations of our manufacturing plant. A very interesting type of disconnect switch is rotary disconnect switches. In addition, there are many types of switches.
Type | Description | Use Case |
---|---|---|
Fusible | Incorporates fuses to provide overcurrent protection. | Machinery, industrial equipment, lighting circuits |
Non-Fusible | Does not have built-in overcurrent protection. Relies on external fuses or circuit breakers. | Applications where overcurrent protection is elsewhere. |
Battery Disconnect | Designed to isolate batteries from the electrical system. | Emergency power systems, vehicles, marine applications |
Rotary Disconnect | Uses a rotating handle to connect or disconnect the circuit. | Control panels, power distribution |
Heavy-Duty Safety | Robust construction for demanding industrial environments. | Heavy machinery, harsh environments |
Double-Throw Safety | Allows switching between two different power sources. | Backup power systems, generator switchgear |
Fusible vs. Non-Fusible Disconnect Switches: What’s the Difference?
Let’s dive deeper into the differences between fusible and non-fusible disconnect switches, as this is a critical decision point for many industrial applications. Fusible disconnect switches are essentially a two-in-one solution.
They combine fuses with the switch, meaning that when you turn the switch to the off position, you’re not just opening the circuit; you’re also ensuring that if there was an overcurrent situation, the fuses would have blown, providing an added layer of circuit protection.
From my experience in managing a manufacturing plant, I can tell you that fusible disconnect switches offer peace of mind. You know that not only can you quickly disconnect power in an emergency or for maintenance, but you also have a backup safety mechanism in the form of the fuse.
This is particularly important in applications where a short circuit or overcurrent situation could have severe consequences. Non-fusible safety switches do not incorporate fuses.
Non-fusible disconnect switches, on the other hand, are more straightforward. They simply open and close a circuit. They don’t offer the built-in circuit protection that fuses provide.
However, this doesn’t mean they are less safe. In many cases, the circuit protection is handled by other devices in the electrical distribution system, such as circuit breakers. Non-fused disconnect switches are typically simpler in design and may be more cost-effective in situations where separate overcurrent protection is already in place.
How Do Disconnect Switches Work to Ensure Safety?
Disconnect switches are the unsung heroes of electrical safety in industrial environments. But how do they actually work to keep us safe? Essentially, a disconnect switch creates a physical break in the electrical circuit, stopping the flow of electrical current.
This might sound simple, but it’s incredibly effective. When the switch is open, there’s no path for electricity to flow, effectively isolating the equipment or circuit from the power source.
This physical isolation is crucial for several reasons. First, it prevents accidental energization of the circuit while someone is working on it. Imagine a technician performing maintenance on a motor. If the power were to suddenly come back on, the results could be disastrous.
The disconnect switch ensures that this can’t happen. Second, in the event of a fault, such as a short circuit, the disconnect switch can be used to quickly cut off power, preventing further damage and reducing the risk of fire or other electrical hazards.
I’ve always emphasized to my team that operating a disconnect switch is a critical safety procedure. It’s not just about flipping a switch; it’s about understanding the responsibility that comes with it.
You’re literally holding the safety of your team and the integrity of your equipment in your hands. It’s a task that should always be performed with the utmost care and respect for the power of electricity. When the switch disconnects the load, it performs its main function.
What are the Key Features to Consider When Choosing a Disconnect Switch?
Choosing the right disconnect switch for your specific application is paramount. It’s not a one-size-fits-all situation. Several factors need to be considered to ensure the safety and reliability of your electrical system. From my experience, here are the key features you need to evaluate.
First, consider the voltage and current ratings. The switch must be rated to handle the maximum voltage and current that will be flowing through the circuit. Using a switch with inadequate ratings can lead to failure, creating a safety hazard.
Second, think about the type of load you’ll be switching. Is it a resistive load, like a heater, or an inductive load, like a motor? Different types of loads have different switching characteristics, and you need a disconnect switch designed to handle them.
Another important factor is the enclosure. Disconnect switches are often housed in enclosures to protect them from the environment and to prevent accidental contact. The type of enclosure you need depends on the operating conditions.
Will the switch be exposed to dust, moisture, or corrosive substances? If so, you’ll need an enclosure that can provide adequate protection. I always recommend opting for a higher level of protection than you think you need. It’s better to be safe than sorry.
Where are Disconnect Switches Commonly Used in Industrial Settings?
Disconnect switches are ubiquitous in industrial settings. You’ll find them in virtually every facility that uses electricity, from small workshops to massive manufacturing plants. But where are they most commonly used?
One of the most common applications is in motor control circuits. Motors are the workhorses of industry, powering everything from conveyor belts to pumps to fans.
Disconnect switches are used to isolate motors for maintenance, repair, or replacement. They’re also used to protect motors from overloads and short circuits. In my plant, we have disconnect switches on every motor, and they’ve saved us from countless headaches over the years.
Another common use is in power distribution systems. Disconnect switches are used to isolate sections of the electrical system for maintenance or to prevent the spread of faults.
For example, if there’s a problem with one part of the system, a disconnect switch can be used to isolate that section, allowing the rest of the system to continue operating. They’re also used in lighting circuits, HVAC systems, and a wide range of electrical equipment.
What Role Do Enclosures Play in Disconnect Switch Safety?
Enclosures are more than just boxes that house disconnect switches. They play a crucial role in ensuring safety and reliability. As I mentioned earlier, enclosures protect the switch from the environment.
This is especially important in industrial settings, where switches may be exposed to dust, dirt, moisture, chemicals, and other contaminants that could interfere with their operation or create a safety hazard.
But enclosures do more than just protect the switch. They also protect people. By housing the switch in an enclosure, you prevent accidental contact with live parts. This is particularly important in high-voltage applications, where even momentary contact can be fatal. Many electrical applications require an enclosure.
Enclosures also play a role in preventing unauthorized operation of the disconnect switch. Many enclosures are designed to be lockable, meaning that only authorized personnel can access the switch.
This is an important safety feature, as it prevents someone from inadvertently turning the switch on or off, potentially creating a dangerous situation.
How Do I Maintain and Inspect Disconnect Switches?
Regular maintenance and inspection of disconnect switches are essential to ensure their continued safety and reliability. Neglecting maintenance can lead to switch failure, which can have serious consequences. In my experience, a proactive approach to maintenance is always the best policy.
The first step in maintaining disconnect switches is to visually inspect them regularly. Look for signs of wear and tear, such as cracks, loose connections, or corrosion. If you see anything that looks out of place, don’t hesitate to investigate further.
It’s always better to err on the side of caution. There was a case at the factory where we replaced the Mitsubishi HMI. The work was carried out quickly and safely thanks to the disconnect switch.
Another important aspect of maintenance is to periodically operate the switch to ensure that it’s working properly. This helps to prevent the contacts from becoming stuck or corroded.
When operating the switch, pay attention to how it feels. Does it move smoothly, or does it feel stiff or sticky? If it doesn’t feel right, it may need to be cleaned or lubricated.
What are the National Electrical Code Requirements for Disconnect Switches?
The National Electrical Code (NEC) sets the standards for safe electrical installation and maintenance in the United States. It includes specific requirements for disconnect switches, which are designed to protect people and property from electrical hazards.
As someone who’s been in the industry for many years, I can’t stress enough the importance of adhering to the NEC.
One of the key requirements is that disconnect switches must be readily accessible. This means that they must be located where they can be easily reached without having to climb over or remove obstacles.
The NEC also specifies that disconnect switches must be within sight of the equipment they serve, and generally no more than 50 feet from the equipment. This ensures that someone working on the equipment can easily see whether the power is on or off.
The NEC also has requirements for the type of disconnect switch that can be used in certain applications. For example, it specifies when a fusible disconnect switch is required and when a non-fusible disconnect switch is acceptable.
It also has requirements for the enclosure of the switch, depending on the operating environment. Disconnect switches are commonly used in factories.
Case Studies: Real-World Applications of Disconnect Switches
Let’s look at some real-world examples of how disconnect switches are used in various industries to enhance safety and operational efficiency.
Case Study 1: Automotive Manufacturing Plant
In a large automotive manufacturing plant, disconnect switches are used extensively throughout the facility. One critical application is on the robotic welding lines.
Each robotic welding cell has a dedicated disconnect switch that allows operators to safely isolate the robot for maintenance, programming, or tool changes. This ensures that the robot cannot be accidentally activated while someone is working on it, preventing potential injuries.
Case Study 2: Food Processing Facility
In a food processing facility, hygiene and safety are paramount. Disconnect switches are used on all major pieces of equipment, such as mixers, conveyors, and packaging machines.
The switches are typically housed in stainless steel enclosures that are designed to withstand frequent washdowns. This allows operators to safely isolate equipment for cleaning and sanitization, preventing contamination and ensuring food safety.
Case Study 3: Data Center
Data centers rely on a constant supply of power to keep servers and other critical equipment running. Disconnect switches play a vital role in the power distribution system, allowing technicians to isolate sections of the system for maintenance or upgrades without disrupting the entire data center.
Battery disconnect switches are also used in the uninterruptible power supply (UPS) systems to ensure that the batteries can be safely isolated for maintenance or replacement.
Frequently Asked Questions
The main purpose of a disconnect switch is to provide a means to safely isolate electrical equipment or circuits from the power source, allowing for maintenance, repair, or emergency shutdown without the risk of electrical shock or equipment damage.
A fusible disconnect switch incorporates fuses to provide overcurrent protection, while a non-fusible disconnect switch does not have built-in overcurrent protection and relies on external fuses or circuit breakers.
While a disconnect switch can technically be used to turn equipment on and off, it’s not typically designed for frequent switching. Regular on/off switches, such as those found on Schneider HMI or light switches, are better suited for that purpose. Using a disconnect switch for frequent switching can lead to premature wear and tear.
A lockable disconnect switch means that it can be secured in the off position using a padlock or other locking device. This prevents unauthorized personnel from turning the switch on, ensuring that the equipment remains safely isolated during maintenance or repair.
It’s recommended to visually inspect disconnect switches at least once a year, or more frequently in harsh operating environments. You should also periodically operate the switch to ensure that it’s working properly. Refer to the manufacturer’s recommendations for specific maintenance intervals.
Power your projects with brand-new, original Omron, Mitsubishi, Schneider PLC – in stock, ready now!
Conclusion
- Disconnect switches are essential safety devices that isolate electrical equipment from the power source.
- Fusible disconnect switches provide built-in overcurrent protection, while non-fusible ones do not.
- Choosing the right disconnect switch involves considering voltage, current, load type, and enclosure requirements.
- Disconnect switches are used in a wide range of industrial applications, including motor control, power distribution, and more.
- Enclosures protect disconnect switches from the environment and prevent accidental contact with live parts.
- Regular maintenance and inspection are crucial for ensuring the continued safety and reliability of disconnect switches.
- The National Electrical Code sets standards for the safe installation and use of disconnect switches.
- Adhering to safety protocols and proper use of disconnect switches is paramount in preventing electrical accidents and ensuring a safe working environment.
Remember, a little knowledge about disconnect switches can go a long way in ensuring a safe and productive work environment. Stay safe! Feel free to contact us with any questions.
Contact Us
Just fill out your name, email address, and a brief description of your inquiry in this form. We will contact you within 24 hours.
You May Also Find These Topics Interesting
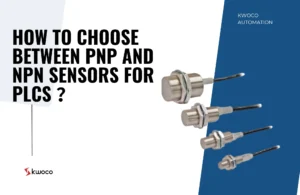
How to Choose Between PNP and NPN Sensors for PLCs ?
How to Choose Between PNP and NPN Sensors for PLCs ? Have you ever found yourself confused when choosing between

Is Relay Output Digital or Analog? Understanding the Basics
Relays, though seemingly simple devices, play an essential role in both our daily lives and industrial applications. But the question often arises: Is the output of a relay analog or digital? This is particularly confusing for those new to industrial automation equipment.
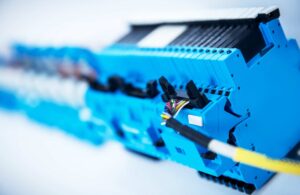
What is a Safety PLC? Understanding Safety and Automation
In an age where automation is integral to operational success, ensuring workplace safety is paramount. Many industries grapple with the question: how can we effectively integrate safety measures into our automation systems? A Safety PLC (Programmable Logic Controller) serves as a robust solution, providing an effective way to manage safety functions while meeting stringent safety standards.