Comprehensive Guide to DC Motor and Controller
Table of Contents
What is a DC Drive and How Does it Work
A DC drive is a motor controller that regulates the speed and torque of a DC motor. It achieves this by adjusting the voltage supplied to the motor. The basic principle behind a DC drive is to take an AC power supply and convert it into a DC output using a rectifier.
The DC output is then modulated to control the motor speed and torque. DC drives are designed to provide precise motor control, making them ideal for applications requiring accurate speed regulation and torque control.
DC drives typically consist of several key components:
- Rectifier: Converts AC input voltage to DC voltage.
- Controller: Modulates the DC output to control the motor’s speed and torque.
- Field Winding: In some DC motors, a field winding is used to generate the magnetic field necessary for motor operation.
DC drives can be used in various motor applications, including:
- Conveyor systems.
- Servo systems.
- Spindle drives.
- Industrial machinery.
One common type of DC drive is the PWM (Pulse Width Modulation) drive. PWM drives work by rapidly switching the DC voltage on and off. The ratio of on-time to off-time determines the average voltage applied to the motor, effectively controlling its speed.
These drives are known for their efficiency and ability to provide smooth motor performance even at low speeds.
What are the Different Types of DC Drives and Their Applications?
DC drives come in various types, each designed to meet specific application needs. Understanding the different types of DC drives and their applications is crucial for selecting the right drive for a particular task. Here, we explore some common types of DC drives and their uses:
- Unidirectional DC Drives: These drives are designed to operate a DC motor in one direction only. They are typically used in simple motor applications where only one direction of rotation is required. For example, a conveyor belt that only needs to move forward can utilize a unidirectional DC drive.
- Bidirectional DC Drives: These drives allow a DC motor to operate in both forward and reverse directions. Bidirectional drives are more complex than unidirectional drives and often include features such as dynamic braking and regenerative motor control. They are commonly used in applications like robotics, servo systems, and positioning systems where precise motion control is necessary.
DC drives are also classified based on their control features and capabilities:
- Basic DC Drives: These drives offer fundamental speed control capabilities and are suitable for applications with minimal control requirements. They typically adjust the motor speed by varying the DC voltage applied to the motor.
- Digital DC Drives: These advanced drives incorporate digital control algorithms to provide precise motor control. Digital DC drives often include features such as feedback control, coordinated control, and computer control interfaces. They are ideal for complex motion control applications requiring high accuracy and flexibility.
- Servo Drives: A specialized type of DC drive, servo drives are used in high-precision motion control applications. They are often paired with servo motors and provide exceptional speed and position control. Servo drives are commonly found in industrial automation systems, robotics, and CNC machinery.
How to Choose the Right DC Drive for Your Application?
Selecting the appropriate DC drive for your application involves considering several factors to ensure optimal motor performance and system efficiency. Here are some key considerations:
- Motor Type: Identify the type of DC motor you are using. Different motor types, such as brushed or brushless DC motors, may require specific drive types. For instance, brushless DC motors often require more sophisticated drives with advanced control features.
- Application Requirements: Determine the specific requirements of your application. Factors such as the need for precise speed control, torque control, and position control will influence your choice of DC drive. For example, applications requiring precise positioning, such as Mitsubishi Servo systems, will benefit from servo drives.
- Control Features: Evaluate the control features offered by different DC drives. Digital DC drives provide advanced control algorithms, feedback control, and computer control interfaces, making them suitable for complex motion control applications.
- Environmental Conditions: Consider the operating environment of your motor and drive. Industrial environments may require drives with robust construction and protection against factors such as dust, moisture, and temperature variations.
Comparison of DC Drive Types
Drive Type | Key Features | Typical Applications |
---|---|---|
Unidirectional DC | Single direction operation, basic speed control | Conveyor belts, fans, simple machinery |
Bidirectional DC | Forward and reverse operation, dynamic braking | Robotics, positioning systems, HMI controlled equipment |
Basic DC | Fundamental speed control, voltage adjustment | Simple industrial machinery, Omron PLC, fans |
Digital DC | Advanced control algorithms, feedback control | Complex motion control, industrial automation, CNC machinery |
Servo Drives | High-precision speed and position control, servo motors | Industrial automation, robotics, high-precision machinery such as Schneider Servo |
Regenerative DC Drives | Energy recovery during braking, efficient operation | Cranes, hoists, elevators, electric vehicles |
Choosing the right DC drive involves a thorough understanding of your motor and application requirements. By carefully evaluating these factors, you can select a drive that provides the necessary control features and performance for your specific needs.
What are the Advantages of Using DC Drives in Industrial Applications?
DC drives offer several advantages that make them well-suited for various industrial applications. These advantages include:
- Precise Speed and Torque Control: DC drives excel in providing precise control over motor speed and torque. This level of control is essential in applications where accurate motion control is crucial, such as in manufacturing processes, robotics, and automation systems. DC drives allow for fine adjustments to motor speed, enabling smooth acceleration and deceleration, which is beneficial in applications like conveyor systems and material handling equipment.
- High Starting Torque: DC motors are known for their high starting torque, and DC drives can effectively harness this capability. The ability to deliver high torque at low speeds makes DC drives ideal for applications that require substantial force to initiate movement, such as in heavy machinery, cranes, and hoists. This characteristic ensures reliable performance in demanding industrial environments.
- Energy Efficiency: Certain types of DC drives, particularly regenerative drives, offer excellent energy efficiency. Regenerative drives can recover energy during the braking process and feed it back into the power system, reducing overall energy consumption. This feature is particularly advantageous in applications with frequent start-stop cycles, such as elevators and electric vehicles, where energy savings can be significant.
Advantages of DC Drives
- Precise control of speed and torque
- High starting torque
- Energy efficiency with regenerative drives
- Wide speed range and smooth operation
- Simple and robust design
- Ease of control and integration
These advantages make DC drives a preferred choice in many industrial settings. Their ability to provide precise control, handle high starting torque, and offer energy-efficient operation ensures reliable and efficient performance in a wide range of applications.
For example, in a manufacturing plant, DC drives can be used to control the speed of conveyor belts, ensuring smooth material flow and precise positioning. In robotics, DC drives enable accurate movement and positioning of robotic arms, contributing to the overall precision of automated tasks.
How Does a DC Drive Compare to an AC Drive?
When it comes to choosing between DC drives and AC drives, it is essential to understand their differences and respective strengths. Both drive types have unique characteristics that make them suitable for different applications.
DC Drives
- Control Precision: DC drives are renowned for their precise control over motor speed and torque. They can provide smooth and accurate speed regulation, making them ideal for applications requiring fine motion control.
- Starting Torque: DC motors generally offer higher starting torque compared to AC motors. DC drives can effectively manage this high starting torque, making them suitable for heavy-duty applications.
- Complexity: DC drives can be simpler in design compared to AC drives, especially basic DC drives. However, advanced digital DC drives can be quite complex due to their sophisticated control algorithms.
AC Drives
- Variable Frequency Drives (VFDs): AC drives, particularly VFDs, control the speed of AC motors by varying the frequency and voltage of the power supply. This allows for efficient speed control and energy savings.
- Maintenance: AC motors typically require less maintenance than DC motors, as they do not have brushes that wear out over time. This can result in lower maintenance costs and increased reliability.
- Efficiency: AC drives can be more efficient than DC drives in certain applications, especially at higher speeds. VFDs, for example, can optimize motor performance by adjusting the frequency to match the load, leading to energy savings.
Comparison Table: DC Drives vs. AC Drives
Feature | DC Drives | AC Drives |
---|---|---|
Control Precision | Excellent, especially for low-speed and high-torque applications | Good, especially at higher speeds; VFDs offer precise speed control |
Starting Torque | High starting torque | Lower starting torque compared to DC motors |
Maintenance | Higher due to brush wear in DC motors | Lower, as AC motors do not have brushes |
Efficiency | Efficient, especially with regenerative drives | Efficient, especially at higher speeds; VFDs optimize motor performance |
Complexity | Can be simpler in basic designs; advanced digital drives are complex | Generally more complex due to frequency and voltage control |
Cost | Generally lower initial cost for basic drives; higher for advanced digital and servo drives | Higher initial cost, especially for VFDs; potential for long-term savings due to lower maintenance and energy efficiency |
Applications | Conveyors, hoists, cranes, robotics, precision machinery | Pumps, fans, compressors, HVAC systems, general-purpose machinery |
Speed Range | Wide speed range with precise control | Wide speed range, but may require VFDs for precise control |
Torque Control | Excellent torque control, especially at low speeds | Good torque control, but may not match DC drives at very low speeds |
Energy Recovery | Regenerative drives available for energy recovery | Some VFDs offer energy recovery features |
Motor Compatibility | Compatible with DC motors only | Compatible with AC motors only |
In summary, DC drives excel in applications requiring precise control of motor speed and torque, high starting torque, and efficient operation at low speeds.
AC drives, particularly VFDs, are advantageous in applications requiring efficient speed control at higher speeds, lower maintenance, and energy savings. The choice between DC and AC drives depends on the specific requirements of the application, including factors such as motor type, control needs, operating environment, and cost considerations.
Frequently Asked Questions
- A DC drive is used to control the speed and torque of a DC motor. It is commonly used in industrial applications such as conveyor systems, servo systems, robotics, and other machinery requiring precise motion control.
DC drives control DC motors by adjusting the DC voltage, providing precise speed and torque control, especially at low speeds. AC drives, particularly variable frequency drives (VFDs), control AC motors by varying the frequency and voltage of the power supply, offering efficient speed control and energy savings, especially at higher speeds.
- The main components of a DC drive include a rectifier (to convert AC input to DC output), a controller (to modulate the DC output and control the motor’s speed and torque), and sometimes a field winding (to generate the magnetic field in the motor).
There are several types of DC drives, including unidirectional drives (for single-direction operation), bidirectional drives (for forward and reverse operation), basic DC drives (for fundamental speed control), digital DC drives (for advanced control features), and servo drives (for high-precision motion control).
DC drives are preferred in applications requiring precise control of motor speed and torque, high starting torque, and efficient operation at low speeds. They are particularly well-suited for tasks involving heavy loads, frequent starts and stops, and the need for accurate positioning and motion control.
Power your projects with brand-new, original Omron, Mitsubishi, Schneider PLC – in stock, ready now!
Conclusion
- DC drives are essential for precise control of DC motor speed and torque.
- Different types of DC drives, including unidirectional, bidirectional, basic, digital, and servo drives, cater to various application needs.
- Choosing the right DC drive involves considering motor type, application requirements, control features, and environmental conditions.
- DC drives offer advantages such as precise speed and torque control, high starting torque, and energy efficiency.
- DC drives are preferred in applications requiring accurate motion control, while AC drives are suitable for tasks needing efficient speed control at higher speeds.
Contact us today to learn more about how our range of DC drives, including advanced Mitsubishi PLC and Omron Sensors, can enhance your industrial automation systems.
Contact Us
Just fill out your name, email address, and a brief description of your inquiry in this form. We will contact you within 24 hours.
You May Also Find These Topics Interesting
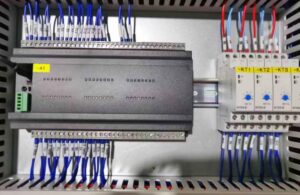
Safety PLC vs. Standard PLC: An Engineer’s Guide
In today’s highly automated commercial settings, the Programmable Logic Controller (PLC) acts as the core “mind” driving manufacturing. Nevertheless, numerous decision-makers and designers struggle to distinguish in between a common PLC and a Security PLC, falling short to completely understand the essential distinctions in their style philosophies, useful applications, and safety guarantees.
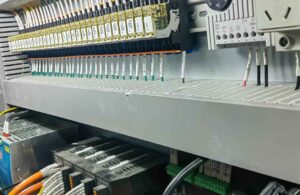
Comprehensive Guide to Photoelectric Sensor Types in Industrial Automation
This article delves into the fascinating world of photoelectric sensors, exploring their various types, functionalities, and applications in industrial automation. We aim to provide a comprehensive understanding of how these detectors are transforming manufacturing processes, enhancing efficiency, and ensuring precision. If you’re involved in the machinery and equipment industry, manufacturing, or providing factory solutions, this article offers valuable insights into leveraging photoelectric sensor technology for your operations, and it explains why reading further will equip you with the knowledge to optimize your automation strategies.
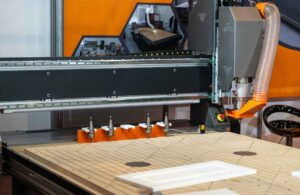
CNC Router vs Spindle: Which to Use?
This article dives deep into the crucial decision of choosing between a router and a spindle for your CNC machine. Whether you’re a seasoned manufacturer or new to CNC technology, understanding the differences between these two vital components is essential for optimizing your production processes. This comprehensive guide will compare spindles and routers, exploring their capabilities, advantages, and disadvantages to help you make an informed decision that aligns with your manufacturing needs and goals.