Servo Motor vs Normal Motor: Key Differences Explained
Table of Contents
My Early Experiences with Motors
When I first started in this field, I was fascinated by how different motors operated and how they could be applied to various systems. Normal motors were straightforward and reliable, while servo motors offered precision that seemed almost magical at the time. Let’s delve into what sets them apart.
Understanding Normal Motors
Normal motors, also known as standard AC motors or induction motors, are widely used in industries for their simplicity and durability. They convert electrical energy into mechanical energy through electromagnetic induction, where the interaction between the magnetic field and electric current generates force in the motor.
Key Characteristics of Normal Motors
- Simplicity: They have a straightforward design with fewer components, making them easier to maintain.
- Cost-Effective: Generally less expensive than servo motors, ideal for applications where high precision isn’t necessary.
- Continuous Operation: Suitable for applications that require consistent speed and torque over long periods.
Limitations of Normal Motors
While normal motors are robust, they lack precision control. They operate on an open-loop system, meaning there’s no feedback mechanism to adjust performance in real-time. This can lead to inefficiencies in applications requiring variable speed or position control.
Introducing Servo Motors
Servo motors are designed for precision control of angular or linear position, velocity, and acceleration. They are integral to closed-loop systems, where feedback signals are used to control the motor’s motion accurately.
Key Features of Servo Motors
- Precision Control: Offer high accuracy for position and speed, essential for robotics and CNC machines.
- Feedback Mechanism: Use encoders or resolvers to provide real-time data, allowing adjustments to be made instantly.
- High Efficiency: Adjust their power consumption based on load requirements, leading to energy savings.
How Servo Motors Work
Servo motors receive a control signal that represents a desired output position. The motor’s internal feedback system compares the current position with the desired position and adjusts accordingly. This closed-loop system ensures precise control over motion.
The Main Differences Between Servo Motors and Normal Motors
Control System
- Servo Motors: Utilize closed-loop control systems with feedback for precise adjustments.
- Normal Motors: Operate on open-loop systems without feedback, limiting precision.
Precision and Accuracy
- Servo Motors: Can achieve high levels of accuracy and repeatability.
- Normal Motors: Limited to uncontrolled motions at a constant speed.
Application Suitability
- Servo Motors: Ideal for applications requiring tight control over movement, like robotic arms or precision machining.
- Normal Motors: Best suited for applications where motion control is less critical, such as pumps or fans.
Energy Efficiency
Servo motors adjust power usage based on demand, leading to greater energy efficiency. Normal motors run at a constant speed regardless of load, which can waste energy.
Cost Implications
- Initial Cost: Servo motors are generally more expensive due to their complexity.
- Operational Cost: Can be lower for servo motors because of energy savings and increased efficiency.
Practical Considerations in Choosing a Motor
Assessing Application Needs
When selecting a motor, consider:
- Required Precision: Does the application need precise control over movement?
- Load Variability: Will the motor need to adjust to different loads?
- Speed Control: Is variable speed important for the process?
- Budget Constraints: What are the cost limitations of the project?
Real-World Examples
Normal Motor Application: Using a normal motor for a conveyor belt system where goods are transported at a constant speed.
Servo Motor Application: Implementing servo motors in an assembly robot that requires precise positioning to place components accurately.
My Professional Insights
In my experience, choosing the right motor can significantly impact the efficiency and effectiveness of an industrial system. I recall a project where switching from normal motors to servo motors resulted in a 20% increase in production speed due to better control and reduced errors.
Importance of Technical Support
Having technical support and proper guidance is crucial when integrating servo motors into complex systems. At Kwoco, we provide not only the products but also the expertise to help our clients succeed.
Potential Challenges with Servo Motors
Complexity
Servo motors are more complex and require proper tuning and programming. This complexity can lead to a steeper learning curve for operators and technicians.
Maintenance Requirements
The additional components like encoders and feedback systems mean there are more parts that could fail, necessitating a robust maintenance schedule.
Power your projects with brand-new, original Omron, Mitsubishi, Schneider Servos – in stock, ready now!
Conclusion
Understanding the main differences between servo motors and normal motors is essential for making informed decisions in industrial applications. While normal motors offer simplicity and cost-effectiveness, servo motors provide precision and efficiency that can be critical for advanced manufacturing processes.
As an engineer at Kwoco, I believe in providing solutions that best fit our clients’ needs. Whether it’s helping you select the right motor or providing technical support, we’re here to assist.
Contact Us
Just fill out your name, email address, and a brief description of your inquiry in this form. We will contact you within 24 hours.
You May Also Find These Topics Interesting
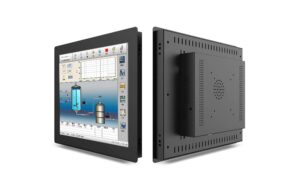
LCD, Digitizer, or Touchscreen Woes? Find the Perfect Industrial Display Solution!
Is your industrial equipment’s display cracked, unresponsive, or simply outdated? Understanding the difference between LCDs, digitizers, and touchscreens is crucial for effective repairs and upgrades. This article dives deep into the world of industrial displays, helping you diagnose problems, choose the right replacement parts, and optimize your machinery for peak performance. We will walk you through what is the digitizer, what is lcd, what is the touchscreen! It’s time to stop guessing and start fixing!
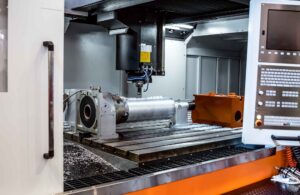
Understanding the Key Components of a CNC Machine
Computer Numerical Control (CNC) machines have revolutionized modern manufacturing, offering unparalleled precision and efficiency. Understanding the components of a CNC machine is essential for anyone interested in machining, whether you’re a seasoned professional or a curious enthusiast. This guide explores the key components that make up a CNC machine, how they work together, and why they’re crucial for producing high-quality parts.
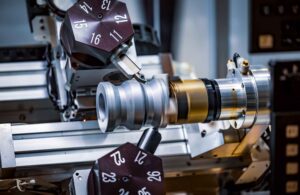
Understanding CNC Spindle Motors: A Complete Guide
CNC spindle motors are the heart of cnc machines, enabling precision and efficiency in modern manufacturing. Whether you’re a seasoned machinist or just curious about how these machines work, this comprehensive guide will shed light on the critical role of spindle motors in CNC technology.