Understanding CNC Spindle Motors: A Complete Guide
Table of Contents
What Is a CNC Spindle Motor?
A CNC spindle motor is a critical component in CNC machines responsible for rotating the cutting tool at high speeds. This rotation allows for precise cutting, drilling, and milling operations. The spindle’s performance directly affects the quality of the surface finish, productivity, and overall efficiency of the machining process.
Key Functions of a Spindle Motor:
- Rotating the Tool: Provides the necessary torque and speed to the cutting tool.
- Precision: Ensures accurate movements for detailed work.
- Power Transmission: Delivers consistent power for various machining operations.
Types of CNC Spindle Motors: Which One Suits Your Needs?
Choosing the right spindle motor depends on your specific application. There are several types of spindle motors, each with its advantages.
1. Belt-Driven Spindles
- How They Work: Use belts to transfer power from the motor to the spindle.
- Advantages: Simple design, easy maintenance.
- Considerations: May produce more vibration and require more space.
2. Integral Motor Spindles
- How They Work: The motor is built directly into the spindle.
- Advantages: Compact design, higher speeds, reduced vibration.
- Considerations: Can be more expensive and complex to repair.
3. Direct-Drive Spindles
- How They Work: Motor is directly connected to the spindle without belts or gears.
- Advantages: High precision, minimal downtime due to fewer moving parts.
- Considerations: Typically used for specialized applications.
4. High-Speed Spindles
- How They Work: Designed for operations requiring speeds exceeding 10,000 RPM.
- Advantages: Improved surface finish, increased productivity.
- Considerations: Require advanced cooling systems and maintenance.
How Do Spindle Motors Work in CNC Machines?
Spindle motors convert electrical energy into mechanical motion to rotate the spindle at desired speeds.
Components of a Spindle Motor:
- Electric Motors: Can be AC induction motors, DC motors, or brushless DC motors.
- Bearings: Support the spindle and allow smooth rotation.
- Cooling Systems: Prevent overheating during high-speed operations.
The Process:
- Power Input: Electricity powers the motor.
- Rotation: The motor generates rotational motion.
- Torque Delivery: Provides consistent torque for varying load conditions.
- Speed Control: Adjusts RPM to match the requirements of the cutting tool and material.
Why Is Choosing the Right Spindle Motor Crucial?
Selecting the appropriate spindle motor impacts the machine’s performance, lifespan, and the quality of the workpiece.
Factors to Consider:
- Material Being Machined: Harder materials may require motors with higher torque.
- Required Speed and Torque: Different applications need specific speed and torque settings.
- Type of Machining Operation: Milling, drilling, or cutting may demand different spindle characteristics.
- Machine Compatibility: Ensure the spindle motor fits the cnc machine specifications.
Benefits of the Right Spindle Motor:
- Increased Productivity: Efficient operations reduce machining time.
- Better Surface Finish: High-quality finishes reduce the need for additional processing.
- Reduced Downtime: Reliable motors minimize maintenance interruptions.
Maintenance and Spindle Repair: Keeping Your Machine Running
Regular maintenance of the machine spindle is vital to sustain performance and extend its lifespan.
Common Maintenance Practices:
- Regular Inspection: Check for signs of wear or damage.
- Lubrication: Proper lubrication of bearings to reduce friction.
- Cooling System Checks: Ensure cooling systems are functioning to prevent overheating.
When to Consider Spindle Repair:
- Excessive Vibration: May indicate bearing wear or imbalance.
- Unusual Noises: Grinding or squealing sounds signal internal issues.
- Decreased Performance: Difficulty maintaining high speeds or torque.
For professional maintenance services, consider reaching out to Servo experts who specialize in spindle repair.
Frequently Asked Questions
It is a critical component that rotates the cutting tool, enabling precise machining operations.
Consider factors like material type, required speed and torque, and compatibility with your machine.
High-speed spindles offer improved surface finishes, increased productivity, and the ability to work on finer details.
Regular maintenance should be scheduled based on usage intensity, but a general guideline is to perform checks every 6 months.
Many issues can be addressed with professional spindle repair, extending the motor’s life without full replacement.
Power your projects with brand-new, original Omron, Mitsubishi, Schneider Servo – in stock, ready now!
Conclusion
- Spindle motors are essential for the precision and efficiency of CNC machines.
- There are various types of spindle motors; choosing the right one depends on your specific needs.
- Regular maintenance and timely spindle repair can significantly extend the life of your machine.
- Understanding your machine’s requirements ensures you find the perfect motor for optimal performance.
- High-quality spindle motors directly contribute to increased productivity and superior outcomes in machining projects.
For more information on automation products like PLC, HMI, and Servo, visit our comprehensive guides on Mitsubishi PLCs and Omron HMIs. If you’re interested in enhancing your CNC setup, explore our selection of Inverters and Sensors to take your machining to the next level.
Contact Us
Just fill out your name, email address, and a brief description of your inquiry in this form. We will contact you within 24 hours.
You May Also Find These Topics Interesting
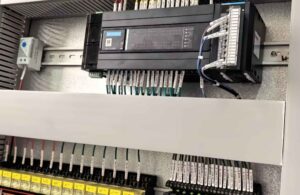
Unlock Precision: Mastering Encoders and High-Speed Counters with PLCs
This article dives deep into the world of encoders and high-speed counters (HSCs), explaining how they interface with Programmable Logic Controllers (PLCs) to provide precise control in industrial automation applications. From understanding rotary encoders to configuring HSC modules, we’ll explore how these technologies work together to enhance speed control, position measurement, and overall system efficiency.

Introduction to Programmable Logic Controllers: Your Gateway to Industrial Automation
This article is a comprehensive guide to Programmable Logic Controllers (PLCs), exploring their fundamental role in modern industrial automation. From machinery and equipment factories to manufacturers and solution providers, PLCs are indispensable for streamlining operations and enhancing productivity. This article delves into the intricacies of PLCs, their programming, and their diverse applications.
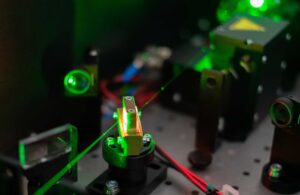
Do Photoelectric Sensors Need Reflectors? Expert Insights
One question that comes up frequently is: Does a photoelectric sensor need a reflector? The answer isn’t a simple yes or no—it depends on the type of sensor and the application’s requirements. Let’s delve into the details to clarify this topic.