Understanding VFD: What is a Variable Frequency Drive?
A Variable Frequency Drive (VFD) is an electronic device that controls the speed and torque of an electric motor by varying the frequency and voltage supplied to the motor. This capability leads to improved energy efficiency and enhanced operational flexibility in various applications.
Table of Contents
What is a VFD?
The Variable Frequency Drive (VFD) is an essential device in the automation landscape. It serves as a controller that drives an electric motor by varying the frequency and voltage applied to it.
Essentially, a VFD adjusts the speed of an AC electric motor by altering the frequency of the electric supply. This dynamic adjustment allows for precise motor control, enabling smooth acceleration and deceleration, which can significantly enhance the performance and longevity of the motor.
VFDs are commonly used in various applications, including pumps, conveyors, and fans. By controlling the speed of the motor, VFDs help reduce energy consumption and operational costs. Furthermore, they provide better protection for your motor from issues related to mechanical and electrical stress, thus ensuring optimal performance and reliability.
How Do VFDs Work?
VFDs operate by converting the incoming AC power into DC power and then back into a controlled AC output using an inverter. This conversion process involves several key components, including rectifiers, capacitors, and IGBTs (Insulated Gate Bipolar Transistors).
- Rectification: The first step involves rectifying the AC input voltage to DC. This is achieved using diodes or thyristors, which convert the AC power into a pulsating DC form.
- DC Bus Filtering: After rectification, capacitors are used to smooth out the pulsating DC, creating a stable DC voltage. This DC bus provides the necessary power for the inverter stage.
- Inversion: The inverter then converts the DC back into AC by switching the IGBTs on and off rapidly. By varying the switching frequency and duration, the inverter can control the output frequency and voltage supplied to the motor.
This intricate process allows VFDs to finely tune the speed of the motor according to the requirements of the application, achieving significant energy savings and improved efficiency.
Why Use a VFD?
What Are the Benefits of Using a VFD?
VFDs offer numerous advantages that make them a popular choice in industrial settings. Some key benefits include:
- Energy Efficiency: By controlling the motor speed, VFDs can reduce energy consumption by up to 50% in certain applications. This is especially beneficial in processes where the demand for speed varies.
- Improved Process Control: VFDs allow for precise control of motor speed and torque, enabling better operation of pumps, conveyors, and other machinery. This leads to enhanced product quality and consistency.
- Reduced Mechanical Stress: By providing smooth acceleration and deceleration, VFDs minimize mechanical stress on motors and driven loads. This significantly extends the lifespan of mechanical components.
- Lower Installation Costs: VFDs can often eliminate the need for additional mechanical components such as gearboxes and clutches, resulting in lower installation and maintenance costs.
In Which Applications Are VFDs Used?
VFDs are versatile and can be applied across various industries, including:
- Water and Wastewater Treatment: VFDs control the speed of pumps, leading to significant energy savings while ensuring adequate flow rates.
- HVAC Systems: In heating, ventilation, and air conditioning systems, VFDs regulate the speed of fans and compressors, improving energy efficiency and comfort levels.
- Manufacturing: VFDs are widely used in conveyor systems and machinery to maintain consistent product quality through better speed control.
What Are the Different Types of VFDs?
How to Choose the Right VFD Type?
There are several types of VFDs available in the market, each designed to meet specific application needs:
- Voltage Source Inverters (VSI): These are the most common type of VFDs, which convert DC voltage into adjustable AC output. They are widely used for controlling AC motors.
- Current Source Inverters (CSI): CSIs are less common and are typically used in high-power applications. They convert DC current into adjustable AC output.
- Pulse Width Modulation (PWM) Drives: PWM drives are a type of VSI that uses a modulation technique to create a variable frequency output. They are known for their efficiency and are commonly used in various industrial applications.
When choosing a VFD, consider factors such as the type of motor, required speed range, and application specifics to ensure optimal performance.
Frequently Asked Questions
A Variable Frequency Drive primarily controls the speed and torque of an electric motor by adjusting the frequency and voltage supplied to it.
VFDs allow for precise motor speed control, which can lead to significant energy savings by matching motor performance with actual load requirements.
VFDs are primarily designed for AC motors, particularly induction motors. However, some VFDs can also operate with specific types of DC motors.
VFDs generally require minimal maintenance, but it’s essential to regularly check for dust accumulation, ensure proper cooling, and monitor input and output connections.
Yes, many VFDs are designed with protective features to operate safely in hazardous environments. However, it’s vital to select a VFD rated for such conditions.
Power your projects with brand-new, original Omron, Mitsubishi, Schneider VFD – in stock, ready now!
Conclusion
In summary, Variable Frequency Drives (VFDs) are crucial components in modern industrial automation, providing unparalleled control over electric motor systems. They offer numerous benefits, including improved energy efficiency, better process control, and reduced mechanical stress. Understanding how VFDs work and their applications can empower professionals to make informed decisions in optimizing their automation processes.
- VFDs control the speed and torque of electric motors.
- They enhance energy efficiency and reduce operational costs.
- Several types of VFDs are available, including VSI and PWM.
- Regular maintenance ensures optimal performance and longevity.
- VFDs are versatile and applicable across various industries.
Looking for new, original Inverter for your projects? At Kwoco, we stock the latest inverter from top brands like Omron, Mitsubishi, and Schneider. Shop with confidence—fast shipping, guaranteed quality! Buy Now
Contact Us
Just fill out your name, email address, and a brief description of your inquiry in this form. We will contact you within 24 hours.
You May Also Find These Topics Interesting
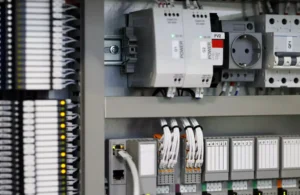
Mastering PLC Panels: A Guide to Reading Wiring Diagrams
As an industrial automation engineer, I deal with PLCs (Programmable Logic Controllers) every day. If you’re like me—deeply interested in automation but often overwhelmed by those complex wiring diagrams—this article is definitely for you.
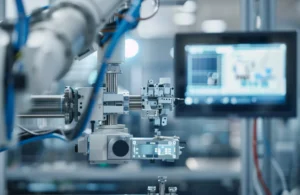
Top 6 HMI Manufacturers in Industrial Automation
Top 6 HMI Manufacturers in Industrial Automation As an engineer at Kwoco with years of experience in the industrial automation
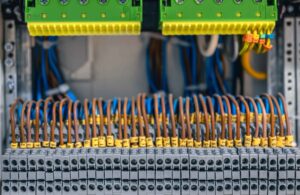
Troubleshooting Common PLC Failures: A Guide to Programmable Logic Controllers
Programmable Logic Controllers (PLCs) are the backbone of modern automation, orchestrating the seamless operation of machinery and industrial processes. However, like any technology, they can encounter issues that disrupt operations.