Unlock Precision: Mastering Encoders and High-Speed Counters with PLCs
Table of Contents
1. What is an Encoder and Why Use One?
An encoder is a sensor, or more accurately a device used, that converts mechanical motion into an electrical signal. This signal provides valuable information about the motion, such as position, speed, and direction.
Encoders are used in a wide range of applications, from robotics and industrial automation to CNC machines and printing presses. Encoders enable precise motion control and feedback, which is critical for ensuring accuracy and efficiency in these systems.
The main reason to use an encoder is to obtain accurate and reliable feedback on the movement of a rotating object. This feedback allows the control system to monitor and adjust the motion in real-time, preventing errors and optimizing performance.
For example, in a motor control application, an encoder can provide information about the motor’s speed, allowing the control system to adjust the power to maintain the desired rpm.
2. What is a High-Speed Counter (HSC) and How Does it Work?
A high-speed counter (HSC) is a specialized module within a PLC or a standalone device designed to count pulses at very high frequencies.
Unlike standard counters are used within a PLC that may be limited by the PLC’s scan time, an HSC can capture pulses much faster, enabling it to accurately track rapid changes in position or speed. This is crucial in applications include where precise timing and high-resolution measurements are required.
HSCs work by using dedicated hardware to count the incoming pulses. This hardware is optimized for speed and accuracy, ensuring that no pulses are missed.
The HSC can be configured to count up, down, or both, and it can also be configured to trigger an output when a specific count is reached. This makes it a versatile tool for a variety of motion control and measurement tasks.
3. Rotary Encoders: How do rotary encoders measure with the PLC?
Rotary encoders are used to measure the angular position or rotation of a shaft. They typically consist of a rotating disk with a pattern of lines or slots, and a sensor that detects these features as the disk rotates. As the shaft rotates, the encoder generates a series of pulses that are sent to the PLC.
The PLC, often through an HSC module, counts these pulses to determine the angular position or speed of the shaft. The number of pulses per revolution (PPR) is a key specification of the rotary encoder, as it determines the resolution of the measurement.
For example, an encoder with 1000 PPR will provide a higher resolution than one with 100 PPR. The HSC accurately keeps track of the counting the number of pulses and sends that data back to the PLC. The PLC can then use this information for display, control, or data logging purposes.
4. Quadrature Encoders and How They Enhance Accuracy?
Quadrature encoders use two output signals, typically labeled A and B, that are 90 degrees out of phase. This phase difference allows the PLC or HSC to determine the direction of movement.
If signal A leads signal B, the shaft is rotating in one direction; if signal B leads signal A, the shaft is rotating in the opposite direction.
This quadrature encoding technique also enhances the resolution of the measurement. By counting both the rising and falling edges of both signals, the effective resolution is quadrupled.
For example, a quadrature encoder with 1000 PPR can provide a resolution equivalent to a single-channel encoder with 4000 PPR. This increased resolution is particularly valuable in motion control applications where high precision is required.
5. Incremental vs. Absolute Encoders: Which encoder is better for measuring position?
There are two main types of encoders: incremental encoders and absolute encoders. Incremental encoders generate a series of pulses as the shaft rotates, but they do not provide information about the absolute position.
The PLC or HSC must track the counting the number of pulses from a known starting point of reference to determine the current position.
In contrast, absolute encoders provide a unique code for each position of the shaft. This means that the PLC can determine the absolute position immediately upon power-up, without needing to track the counting the number of pulses.
Absolute encoders are more expensive than incremental encoders, but they are often preferred in applications where the retain position information is critical, such as in robotics and CNC machines. If power loss happens or a sudden stop of the motor these encoders will provide accurate reading, which is key to motion control.
6. How to Choose the Right Encoder for Your Application?
Selecting the right encoder for your application requires careful consideration of several factors:
- Resolution: The required resolution depends on the level of precision needed for your application. Higher resolution encoders provide more accurate measurements but may also be more expensive.
- Type: Choose between incremental and absolute encoders based on whether absolute position information is required.
- Environment: Consider the environmental conditions in which the encoder will be used. Some encoders are designed for harsh environments with high temperatures, vibration, or exposure to liquids.
- Interface: Ensure that the encoder’s electrical output signal is compatible with your PLC or HSC. Common interfaces include quadrature, SSI, and Ethernet/IP.
- Size and Mounting: Select an encoder that fits within the available space and can be easily mounted.
Before implementing an encoder for your manufacturing plant make sure to consider the factors above.
7. How do high-speed counters work with PLCs to Measure Speed Using?
High-speed counters (HSC) are essential components in measuring speed accurately with PLCs. As mentioned, they work independently of the PLC’s scan time, allowing them to capture and process pulses at much higher frequencies than standard PLC inputs.
This capability is crucial for measure speed of rotating equipment, such as motors, where the frequency of the pulses generated by the encoder can be very high.
Here’s how the HSC is used to measure speed:
- The rotary encoder is mechanically coupled to the motor or rotating shaft.
- As the shaft rotates, the encoder generates pulses.
- These pulses are fed into the HSC module.
- The HSC counts the number of pulses over a specific time interval.
- The PLC then reads the count value from the HSC and calculates the speed (rpm) based on the encoder’s number of pulses per revolution and the time interval.
For example, if an encoder with 1000 PPR generates 10,000 pulses in one second, the speed would be calculated as (10,000 pulses / 1000 pulses per revolution) 60 seconds/minute = 600 *rpm.
8. How do encoders use to measure the speed of a motor?
Encoders are typically used to measure the speed of a motor by converting the rotational motion into a series of electrical signals (pulses). These pulses are then processed to determine the rpm or angular velocity of the motor.
The process involves the following steps:
- A rotary encoder is attached to the motor shaft.
- As the motor rotates, the encoder generates pulses at a rate proportional to the speed of the motor.
- These pulses are fed into a counter or an HSC, which counts the number of pulses over a specific time period.
- The motor control system then calculates the speed based on the encoder’s resolution (pulses per revolution) and the count value.
The system can then adjust the power supplied to the motor using an inverter, in order to achieve speed control.
9. What are Some Common Applications of Encoders and High-Speed Counters?
Encoders and HSCs are used in applications across various industries, including:
- Industrial Automation: Position measurement and speed control in automation systems, such as conveyor belts, robotic arms, and packaging machines.
- CNC Machines: Precise motor control and position measurement in milling machines, lathes, and routers.
- Printing Presses: Accurate registration and tension control in printing processes.
- Material Handling: Measure the position and speed of materials in automated storage and retrieval systems.
- Elevators: Measure the position and speed control of elevator cars.
- Textile Industry: Controlling the tension and speed of yarns and fabrics in weaving and knitting machines.
These encoders provide real-time monitoring and control, ensuring safety and precision in these processes. These applications exemplify how industrial automation relies on encoders and high-speed counters.
10. Troubleshooting Common Encoder and HSC Issues
Even with proper installation and setup, you may encounter issues with your encoder and HSC system. Here are some common problems and troubleshooting tips:
- Incorrect Readings: Verify the encoder’s wiring and ensure that the HSC is properly configured. Check for electrical noise or interference that could be affecting the signal.
- Missing Pulses: Ensure that the HSC’s input frequency is sufficient for the encoder’s output signal. Reduce the distance between the encoder and HSC to minimize signal degradation.
- Direction Errors: Check the wiring of the quadrature signals to ensure that they are correctly connected. Verify the HSC’s direction mode setting.
- HSC Overflow: Ensure that the HSC’s counter range is sufficient for your application. Consider using a larger counter or scaling the input signal.
- Electrical Noise: Caused by other electrical equipment can interfere with the encoder signal. Shielded cables and proper grounding can help mitigate this issue.
By systematically checking these potential issues, you can quickly identify and resolve problems with your encoder and HSC system.
11. Maple Systems and Encoders: Is Maple Systems a good choice?
Maple Systems offers a range of HMI (Human Machine Interface) products that can be seamlessly integrated with encoders and PLCs. Maple Systems HMIs can display real-time data from encoders, such as position, speed, and direction.
They also allow operators to monitor and control encoder-related parameters, such as HSC settings and thresholds.
Integrating maple systems HMIs with encoders and PLCs provides a comprehensive solution for industrial automation. The HMI can serve as a central point for data visualization, control, and alarm management.
The programming software often supports ladder logic, so it will be easy to program with familiar concepts.
12. The Future of Encoders and HSCs
The technology behind encoders and HSCs continues to evolve, driven by the increasing demands of industrial automation and robotics. Some of the key trends include:
- Higher Resolution: Encoders with finer resolution are enabling more precise position measurement and control.
- Wireless Encoders: Wireless encoders are eliminating the need for physical cables, simplifying installation and reducing maintenance costs.
- Smart Encoders: Encoders with built-in processing power are capable of performing advanced diagnostics and data analysis.
- Enhanced Connectivity: Encoders with Ethernet/IP and other industrial protocols are facilitating seamless integration with PLCs and other automation devices.
- Miniaturization: Smaller, more compact encoders are being developed for applications where space is limited.
These advancements are making them indispensable for a wide range of various industrial applications, offering greater flexibility, accuracy, and reliability.
Want to optimize your industrial control systems? As a leading provider of industrial automation solutions, we at KWOCO understand the critical role that encoders and high-speed counters play in enhancing precision and efficiency.
Specializing in manufacturing plants for industrial control products, machinery, and factory equipment, we offer tailored solutions designed to meet the unique needs of machinery and equipment factories, manufacturers, and factory solution companies.
Contact us today to discover how our expertise can transform your manufacturing processes, ensuring ensuring optimal performance!
Internal Links:
- To enhance the system efficiency, consider using top of the line Omron products.
- When setting up your industrial system, Mitsubishi products are a good choice to consider.
- For a long lasting and robust products, check out the latest Schneider offerings.
- For seamless integration between components, use Proface HMI.
- Don’t forget to use quality cables, browse the Cables catalogue.
- For reliable motor control, check out Mitsubishi Servo solutions.
Frequently Asked Questions
Calibration frequency depends on the application and environmental conditions. Generally, it’s a good practice to calibrate encoders annually or as recommended by the manufacturer to ensure accuracy.
Yes, there are encoders specifically designed for hazardous environments. These encoders are typically explosion-proof or intrinsically safe to prevent ignition of flammable materials.
Single-ended signals are simpler but more susceptible to noise. Differential signals use two wires for each signal, which helps to cancel out noise and improve signal integrity, especially over long distances.
Yes, but it’s usually straightforward. The PLC needs to be programmed to read the encoder’s signals and interpret them correctly. This typically involves using high-speed counter modules and configuring the PLC’s inputs and outputs accordingly with a plc programming.
For incremental encoders, if power is lost, the position information is lost. The system must return to a known reference point to re-establish position. Absolute encoders, on the other hand, retain position information even after a power cycle, eliminating the need for re-referencing.
Power your projects with brand-new, original Omron, Mitsubishi, Schneider PLC – in stock, ready now!
Conclusion
- Encoders convert mechanical motion into electrical signals for precise monitoring and control.
- High-speed counters (HSCs) capture pulses at high frequencies, enabling accurate speed and position measurement.
- Quadrature encoders enhance accuracy by providing directional information and increasing resolution.
- Choosing the right encoder depends on the application’s resolution, type, environment, and interface requirements.
- Proper troubleshooting and maintenance are essential for reliable encoder and HSC system performance.
Contact Us
Just fill out your name, email address, and a brief description of your inquiry in this form. We will contact you within 24 hours.
You May Also Find These Topics Interesting
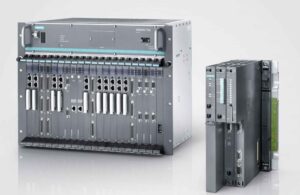
Siemens SIMATIC Controller: The Brain Behind Seamless Automation
This blog post delves into the world of Siemens SIMATIC controllers, explaining why they are a cornerstone of modern industrial automation and highlighting their benefits for machinery and equipment factories, manufacturers, and factory solution companies. We aim to demonstrate how SIMATIC controllers can transform your operations, improve efficiency, and ultimately, drive profitability. As a business specializing in industrial automation and industrial control products for manufacturing plants, we understand the critical role that reliable and adaptable control systems play in today’s competitive landscape.
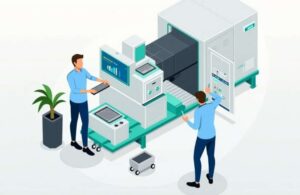
NC vs CNC: Understanding the Differences Between NC and CNC Machines
This article dives into the world of NC (Numerical Control) and CNC (Computer Numerical Control) machines, explaining their key differences and why they are essential in the industrial automation industry. Whether you’re a seasoned professional or new to the field, this piece will provide valuable insights into how these technologies have revolutionized manufacturing and what makes them worth understanding.
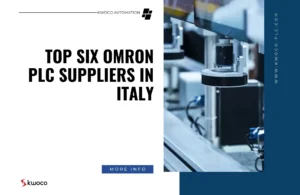
Top Six Omron PLC Suppliers in Italy
Top Six Omron PLC Suppliers in Italy As someone deeply involved in the industrial automation sector, particularly in international trade