Mastering PLC Panels: A Guide to Reading Wiring Diagrams
Table of Contents
What Are PLCs and Their Power Requirements?
Programmable Logic Controllers (PLCs) are specialized computers used for automation of industrial processes. They are designed to handle various tasks, from simple control functions to complex operations in manufacturing environments. Understanding the power requirements of PLCs is essential for ensuring their efficient operation.
PLCs can operate using either AC or DC power, depending on their design and application. Most PLCs are equipped with a power supply unit that converts the incoming power to the required voltage levels. This flexibility allows engineers to choose the most suitable power source based on the specific needs of their automation systems.
Key Features of PLC Power Supplies
- Voltage Compatibility: PLCs typically require a specific voltage range, often 24V DC or 120/240V AC.
- Reliability: A reliable power supply is crucial for maintaining the performance and reliability of PLC systems.
- Efficiency: Choosing the right power supply can enhance the overall efficiency of your automation processes.
AC vs. DC: What’s the Difference?
When discussing PLC power supplies, it’s important to understand the differences between AC and DC power. Each type of power has its unique characteristics and applications in industrial settings.
AC Power
Alternating Current (AC) is the type of electrical current commonly used in homes and industries. It changes direction periodically, making it suitable for long-distance transmission. AC power is readily available in most industrial environments, which makes it a preferred choice for many PLC applications.
DC Power
Direct Current (DC), on the other hand, flows in a single direction. It is often used in applications requiring stable voltage levels, such as in sensors and field devices. Many PLCs can operate on 24V DC, which is a standard voltage for many industrial control systems.
Advantages and Disadvantages
- AC Power:
- Advantages: Easier to transmit over long distances, widely available.
- Disadvantages: Requires conversion for devices that need DC.
- DC Power:
- Advantages: Provides stable voltage, ideal for sensitive electronic components.
- Disadvantages: Less efficient for long-distance transmission.
Understanding these differences helps in making informed decisions about the power supply for your PLC.
How to Choose the Right Power Supply for Your PLC?
Choosing the right power supply for your PLC is crucial for ensuring its optimal performance. Here are some factors to consider:
1. Voltage Requirements
Different PLCs have varying voltage requirements. It’s essential to check the specifications of your PLC to determine whether it operates on AC or DC power. For instance, many PLCs require 120 or 240 volts AC, while others may need 24 volts DC.
2. Application Environment
Consider the environment in which the PLC will operate. AC-powered PLCs are often advantageous in environments where AC power is readily available, while DC-powered PLCs may be preferred in applications requiring lower voltage and higher stability.
3. Power Supply Modules
Many PLC systems come with power supply modules that can convert AC to DC. This flexibility allows for easier integration into existing systems and simplifies installation.
4. Reliability and Efficiency
Ensure that the chosen power supply provides reliable and efficient operation. A good power supply should minimize downtime and enhance the overall productivity of your automation systems.
What Are the Voltage Requirements for PLCs?
Understanding the voltage requirements of your PLC is essential for selecting the appropriate power supply. Here are some common voltage specifications:
Voltage Type | Common Values | Applications |
---|---|---|
AC Voltage | 120V, 240V | General industrial applications |
DC Voltage | 24V, 48V | Sensors, field devices, and control systems |
Importance of Voltage Compatibility
Using the correct voltage is crucial for the safe and efficient operation of PLCs. Overvoltage can damage the PLC, while undervoltage can lead to malfunctioning or erratic behavior. Always refer to the manufacturer’s specifications to ensure compatibility.
External Power Supply Considerations
In some cases, you may need to use an external power supply to meet the voltage requirements of your PLC. This is particularly important in systems where the available power source does not match the PLC’s needs.
Power your projects with brand-new, original Omron, Mitsubishi, Schneider PLC – in stock, ready now!
Conclusion
- PLCs can operate on both AC and DC power.
- Voltage requirements vary; check your PLC specifications.
- Choose a power supply that matches your application environment.
- Reliability and efficiency are key to successful automation.
Looking for new, original PLCs for your projects? At Kwoco, we stock the latest PLCs from top brands like Omron, Mitsubishi, and Schneider. Shop with confidence—fast shipping, guaranteed quality! Buy Now
Contact Us
Just fill out your name, email address, and a brief description of your inquiry in this form. We will contact you within 24 hours.
You May Also Find These Topics Interesting
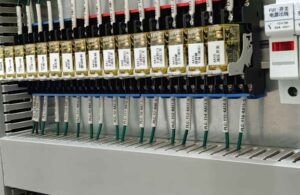
What is a VFD? – How to use one in Applications
Variable Frequency Drives (VFDs) are transforming the landscape of industrial automation by providing unparalleled control over motor speed and energy efficiency. In this comprehensive guide, we’ll delve into what a VFD is, how VFDs work, and how to use one in your applications to achieve optimal performance and energy savings.
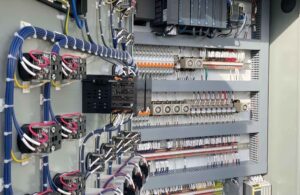
Mastering the Operating Mode of a Timer Switch: A Comprehensive Guide
This article delves into the intricacies of timer switches, offering a comprehensive understanding of their various types, operating modes, and applications. Whether you’re an engineer at a machinery and equipment factory, a manufacturer, or part of a factory solution company, this guide will provide valuable insights into how timer switches can enhance your industrial automation processes.
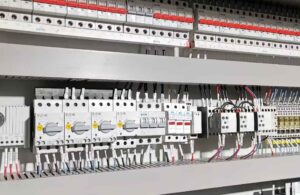
Proximity sensor vs Photoelectric sensor
This article delves into the fascinating realm of proximity sensors and photoelectric sensors, exploring their functionalities, differences, and applications. Whether you’re a seasoned engineer in a machinery and equipment factory or a solution provider seeking the best automation components, understanding these sensor types is crucial. As an industrial automation and control products manufacturing plant, we’re here to illuminate the intricacies of these vital components, ultimately guiding you toward informed decisions for your projects.