PLC vs PC: Key Differences in Industrial Automation
Choosing between a PLC and a PC for industrial automation depends on various factors, including the specific application, environmental conditions, and required processing power. PLCs are designed for real-time control in harsh environments, while PCs offer greater flexibility and processing capabilities for complex tasks.
Table of Contents
What is a PLC and How Does it Work?
A Programmable Logic Controller (PLC) is a specialized industrial computer designed to control manufacturing processes or machinery. PLCs are built to withstand harsh environments, including extreme temperatures, humidity, and vibrations. They operate using a real-time operating system that allows them to execute control tasks with high reliability and speed.
PLCs are programmed using various programming languages, with ladder logic being the most common. This graphical programming language mimics electrical relay logic, making it easier for engineers familiar with traditional control systems to adapt. PLCs are equipped with input/output (I/O) modules that connect to sensors and actuators, enabling them to monitor and control machinery effectively.
Key Features of PLCs:
- Rugged Design: Built to endure harsh industrial conditions.
- Real-Time Processing: Capable of executing control tasks in real-time.
- Ease of Programming: Ladder logic and other user-friendly programming languages.
What is a PC and Its Role in Industrial Automation?
A Personal Computer (PC), in the context of industrial automation, refers to a standard computing device that can be used for various applications, including control systems. PCs are versatile and can run complex software applications, making them suitable for tasks that require significant processing power, such as data analysis, visualization, and advanced control algorithms.
Industrial PCs (IPCs) are specifically designed for industrial environments, featuring ruggedized components to withstand dust, moisture, and temperature fluctuations. They often run on operating systems like Windows or Linux, providing flexibility in software choices and integration with other systems.
Key Features of PCs:
- High Processing Power: Capable of handling complex calculations and data processing.
- Versatility: Can run a wide range of applications beyond control tasks.
- User-Friendly Interfaces: Often equipped with graphical user interfaces (GUIs) for easier interaction.
What are the Key Differences Between PLCs and PCs?
Understanding the differences between PLCs and PCs is essential for selecting the right technology for your automation needs. Here are some critical distinctions:
1. Design and Durability
- PLCs are purpose-built for industrial environments, featuring rugged designs that can withstand extreme conditions.
- PCs, while versatile, may require additional protective measures to operate reliably in harsh settings.
2. Processing Capabilities
- PLCs excel in real-time control tasks, making them ideal for applications requiring immediate responses.
- PCs offer superior processing power, suitable for complex data analysis and multitasking.
3. Programming and Flexibility
- PLCs use specialized programming languages tailored for control tasks, which can be less flexible than PC programming.
- PCs can run various software applications, allowing for greater customization and integration with other systems.
4. Cost Considerations
- PLCs are generally more cost-effective for dedicated control tasks due to their specialized nature.
- PCs may incur higher costs when considering the need for ruggedization and additional software licenses.
When Should You Use a PLC Over a PC?
Choosing a PLC over a PC is often dictated by the specific requirements of your application. Here are scenarios where a PLC is the preferred choice:
- Real-Time Control: When immediate response times are critical, such as in safety systems or high-speed manufacturing processes.
- Harsh Environments: In settings with extreme temperatures, dust, or moisture, where a PLC’s rugged design can ensure reliability.
- Simplicity and Reliability: For straightforward control tasks where a PLC’s ease of programming and maintenance can reduce downtime.
What are the Advantages of Using PCs in Industrial Automation?
While PLCs are excellent for many applications, PCs also offer unique advantages that can enhance industrial automation:
- Advanced Data Processing: PCs can handle large volumes of data, making them ideal for applications involving data analytics and machine learning.
- User Interface Flexibility: With PCs, you can create sophisticated user interfaces that improve operator interaction and monitoring.
- Integration Capabilities: PCs can easily integrate with various software systems, enabling seamless communication across different platforms.
Frequently Asked Questions
PLCs are designed to control machinery and processes in real-time, ensuring efficient operation and safety.
Not necessarily; while PCs offer flexibility, PLCs are better suited for real-time control in harsh environments.
The most common programming language for PLCs is ladder logic, but others like structured text and function block diagrams are also used.
Generally, industrial PCs can be more expensive due to their advanced capabilities and the need for ruggedization.
Consider factors such as the complexity of the task, environmental conditions, and required processing power when making your choice.
Power your projects with brand-new, original Omron, Mitsubishi, Schneider PLC – in stock, ready now!
Conclusion
- PLCs are specialized for real-time control in harsh environments.
- PCs offer greater processing power and flexibility for complex tasks.
- The choice between a PLC and a PC depends on specific application needs.
- Understanding the differences can lead to better decision-making in industrial automation.
Looking for new, original PLCs for your projects? At Kwoco, we stock the latest PLCs from top brands like Omron, Mitsubishi, and Schneider. Shop with confidence—fast shipping, guaranteed quality! Buy Now
Contact Us
Just fill out your name, email address, and a brief description of your inquiry in this form. We will contact you within 24 hours.
You May Also Find These Topics Interesting
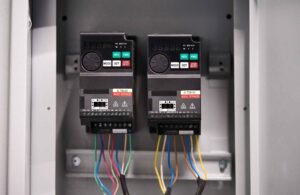
Variable Frequency Drives (VFD): Complete Guide to Motor Control
A comprehensive guide to variable frequency drives (VFDs) – the technology that’s revolutionizing motor control in industrial applications. Whether you’re an engineer, technician, or facility manager, this article will help you understand how VFDs work and why they’re crucial for modern motor applications.
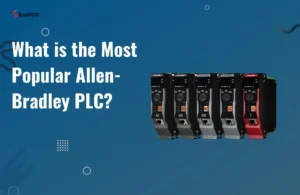
What is the Most Popular Allen-Bradley PLC?
What is the Most Popular Allen-Bradley PLC? If you’re in the automation industry, you’ve probably heard of Allen-Bradley PLCs. They
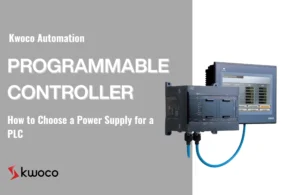
How to Choose a Power Supply for a PLC?
How to Choose a Power Supply for a PLC When it comes to industrial automation, choosing the right power supply