Easy Guide: Connecting Omron PLC via Ethernet
- kwoco-plc.com
- October 10, 2024
- 8:32 pm
Don’t worry; I’m here to help you solve this problem today. As an engineer at Kwoco, I deal with this kind of task often. Let me introduce you to the two most common methods.
There are two common ways to connect Omron PLC to Ethernet: one is using a PLC network adapter, and the other is using an Ethernet card. A PLC network adapter can receive Ethernet signals and convert them into serial communication signals, making it easier to transmit to the PLC. An Ethernet card, on the other hand, is installed directly into the PLC, generates Ethernet signals, and then translates them into serial communication signals for the PLC.
Both methods have their own advantages. The choice between them depends largely on your project needs, budget, and technical skills. If you’re unsure about which one to choose, don’t worry, let’s keep reading.
Table of Contents
How to Choose Between a PLC Network Adapter and an Ethernet Card?
Using a PLC Network Adapter: This method is suitable for PLCs that do not have a native Ethernet interface. The network adapter can convert Ethernet signals into serial communication signals (such as RS232/RS485), allowing the PLC to communicate with other network devices. Common use cases include using serial-to-Ethernet converters like Exemys devices for remote connectivity and data transmission.
Using an Ethernet Card/Module: For PLCs that support expansion, you can install an Ethernet module to enable Ethernet communication. For example, Omron’s CJ2M or CP1L series PLCs can achieve Ethernet communication by installing modules like the CP1W-CIF41. This allows the PLC to use the FINS protocol for data transmission directly, offering faster communication speeds and easier configuration.
Both methods require setting up the IP address and ensuring it matches the network environment to establish a stable connection. The choice between an adapter and an Ethernet card depends on the PLC model and project requirements.
The advantage of using a PLC network adapter is that it is simple and low-cost, and it does not require significant modifications to the PLC. This is suitable for projects with limited budgets and a need for quick setup.
An Ethernet card, however, is ideal for projects that require higher speed and more stable communication. Although the initial investment may be higher, in the long run, the stable connection and efficient transmission speed can save you a lot of trouble.
How to Ensure a Stable Connection?
Choosing the right device is just the first step. To ensure that your PLC connects stably via Ethernet, you need to pay attention to certain details in the setup and installation process, such as IP address configuration and the choice of communication protocol.
- The IP address of the PLC needs to match your network environment to ensure smooth data transmission.
- The choice of communication protocol is also important, such as using Modbus TCP or Ethernet/IP, which directly affects the interoperability between the PLC and other devices.
How to Solve Common Connection Issues?
During the PLC connection process, common issues include communication interruptions, IP address conflicts, and slow transmission speeds. These problems may sound troublesome, but they are actually solvable.
- Communication interruptions: Check if the Ethernet cables and connectors are intact; sometimes a small loose connection can cause a big issue.
- IP address conflicts: Ensure that each device has a unique IP address to avoid multiple devices using the same address.
- Slow transmission speed: Consider upgrading your network devices or adjusting bandwidth allocation.
Frequently Asked Questions
1. What settings should be considered when using a PLC network adapter for connection?
When using a PLC network adapter, ensure that the IP address and subnet mask of the device are properly configured to match the existing network. Additionally, check the serial communication settings, such as baud rate and port type (like RS232 or RS485), to ensure proper communication with the PLC.
2. How to configure the IP address when using an Ethernet card with Omron PLC?
When configuring an Ethernet card, you can set the PLC’s IP address using Omron’s programming software (like CX-Programmer). Make sure that the PLC and other devices are on the same subnet to ensure smooth communication between the devices.
3. What are the common issues with Ethernet card or network adapter connections?
Common issues include communication interruptions, IP address conflicts, and slow transmission speeds. It is recommended to check if the cables are connected properly, ensure that each device has a unique IP address, and consider upgrading network devices to improve transmission speeds. If issues persist, try reconfiguring the communication parameters or seek professional technical support.
Power your projects with brand-new, original Omron, Mitsubishi, Schneider PLC – in stock, ready now!
Conclusion
Connecting an Omron PLC to Ethernet is not difficult; as long as you choose the right method and pay attention to the setup, everything will go smoothly. If you still have any questions, feel free to contact me! Want to learn more? Visit my website: www.kwoco-plc.com
Looking for new, original PLCs for your projects? At Kwoco, we stock the latest PLCs from top brands like Omron, Mitsubishi, and Schneider. Shop with confidence—fast shipping, guaranteed quality! Buy Now
Contact Us
Just fill out your name, email address, and a brief description of your inquiry in this form. We will contact you within 24 hours.
You May Also Find These Topics Interesting
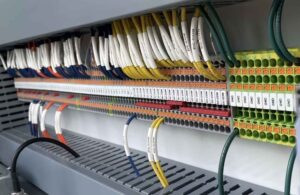
What is PLC Ladder Logic and How Does it Work?
Programmable Logic Controllers (PLCs) are the backbone of industrial automation, and ladder logic is the most popular programming language used to instruct these PLCs. This article delves into the basics of ladder logic, demystifying how it works and why it’s essential for anyone interested in PLC programming to understand. Whether you’re a seasoned engineer or new to automation, this guide will enhance your knowledge and skills.
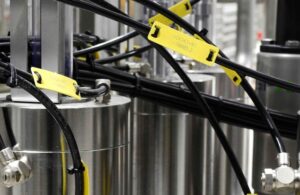
NPN vs PNP Sensors: Key Differences Explained
Understanding the differences between NPN and PNP sensors is crucial for anyone involved in industrial automation. These sensors are fundamental components in control systems, and knowing how they work can greatly enhance the efficiency and reliability of your operations. This comprehensive guide will demystify NPN and PNP modules and sensors, explain their functionality, and help you decide which type is best suited for your applications.
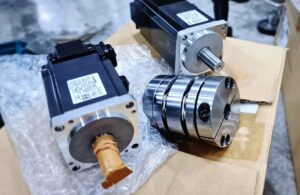
Servo Motor vs Normal Motor: Key Differences Explained
One question that often comes up is, “What is the main difference between a servo motor and a normal motor?” Understanding this distinction is crucial for anyone looking to select the right motor for their application.