Digital vs Analog Servos: Which Is Better for Your RC Motor?
Table of Contents
Outline of the Servo Discussion
What is a Servo Motor and How Does it Work?
A servo motor is a type of motor that allows for precise control of angular or linear position, velocity, and acceleration. It consists of a suitable motor coupled to a sensor for position feedback.
Servos are fundamental in various applications, from RC models to industrial machinery. We have been harnessing the power of servo motors to revolutionize automation control in manufacturing. They are closed-loop mechanisms that incorporate positional feedback in order to control the rotational or translational speed and position.
The motor is controlled with an electric signal, either analog or digital, which determines the amount of movement which represents the final command position for the shaft.
What is Pulse Width Modulation (PWM) in Servos?
PWM is a technique used to control the power supplied to electrical devices, including servos. By varying the width of a pulse of voltage, the average power delivered to the servo can be controlled, thereby influencing its position and speed.
Servos use PWM signals to determine the desired position of the servo arm. The duration of the pulse determines how far the motor turns. For example, a 1.5 millisecond pulse will typically move a servo to its neutral position, which is around 90 degrees for a standard servo.
Our expertise at Servo allows us to fine-tune PWM signals to achieve unparalleled precision in servo operation.
How Does an Analog Servo Function?
Analog servos operate based on the principle of varying voltage. The control circuitry within an analog servo interprets the length of the incoming pulse to determine the position of the servo arm. Analog servos are known for their simplicity and cost-effectiveness.
They receive a pulse from the receiver and adjust the motor accordingly. However, they may not offer the same level of precision as digital servos. A typical analog servo receives a pulse roughly every 20 milliseconds, or 50 pulses per second.
We often recommend analog servos for applications where cost is a primary concern, and the need for high precision is minimal. As an example, one analog servo can provide a balance of cost and performance that is ideal for many general-purpose applications.
The time it takes the servo to move to the desired position depends on how far it needs to rotate. A typical standard servo might take around 0.15 seconds to rotate 60 degrees.
What are the Characteristics of a Digital Servo?
Digital servos are characterized by their use of a microprocessor to process the incoming signal. This allows for faster response times, increased torque, and better holding power compared to analog servos.
Digital servos can also receive and process pulses at a much higher rate, typically around 300 pulses per second, which means they can make much finer adjustments to their position.
They provide better holding power, which means they are better at maintaining their position when under load. Also, digital servos are often more expensive than analog servos, although the prices have been coming down in recent years.
Analog and Digital Servo Motors: A Comparison
When comparing analog and digital servo motors, several factors come into play. Digital servos generally offer better performance in terms of speed, torque, and precision.
There are several advantages to using digital servos. These are programmable: digital servo has a microprocessor, which allows for the customization of the servo’s parameters.
You can adjust things like the servo’s speed, direction, and even the endpoints of its travel.
Feature | Analog Servo | Digital Servo |
---|---|---|
Response Time | Slower | Faster |
Torque | Lower | Higher |
Holding Power | Weaker | Stronger |
Precision | Lower | Higher |
Power Consumption | Lower | Higher |
Cost | Lower | Higher |
Update Rate | Typically 50Hz | Up to 300Hz or more |
Programmability | Limited | Extensive, parameters can be fine-tuned |
Durability | Generally less durable under stress | More robust, often with metal gear sets |
How to Choose Between Analog or Digital Servos?
Choosing between analog or digital servos depends on the specific requirements of the application. If high precision, speed, and torque are critical, digital servos are the way to go.
Digital servos also tend to be more accurate than analog servos because they can make smaller adjustments to their position. This makes them ideal for applications where precision is important.
Can You Use Digital and Analog Servos Together?
In some cases, it is possible to use digital and analog servos together in the same system. However, it is important to ensure that the control system is capable of handling both types of signals. Compatibility issues may arise, and careful consideration is needed.
We at Servo have successfully implemented mixed servo systems, leveraging the strengths of both types to achieve optimal results. One common approach is to use a receiver that can output both analog and digital signals. Some receivers have dedicated channels for each type of servo.
For example, you might use digital servos for the primary flight controls of an RC aircraft, where precision and responsiveness are crucial, and use analog servos for less critical functions, such as landing gear or flaps.
What are the Benefits of Using Digital Servos in RC Applications?
In RC applications, digital servos offer several advantages. Their faster response time and higher torque are particularly beneficial in RC helicopters and airplanes, where precise control is essential for stable flight.
Digital servos also provide better holding power, which is crucial for maintaining the position of control surfaces under load.
Digital servos are usually more expensive than analog servos, but they offer better performance and more features. If you are new to RC, you may want to start with analog servos, as they are less expensive and easier to use. However, if you are looking for the best possible performance, digital servos are the way to go.
How do Servos Impact Automation Control in Manufacturing?
Servos play a vital role in automation control within manufacturing plants. They provide the precision and reliability needed for automated machinery to perform tasks accurately and consistently.
By integrating servos into manufacturing processes, companies can achieve higher levels of efficiency and productivity. Our team at Servo specializes in developing servo-based solutions that enhance manufacturing operations.
Servo motors are commonly used in a variety of industrial applications, including robotics, CNC machinery, and manufacturing, as well as in simpler devices and toys like remote-controlled cars.
What are the Future Trends in Servo Technology?
The field of servo technology is constantly evolving. We are seeing advancements in materials, such as metal gear sets, which enhance durability and performance.
Digital servos are becoming more sophisticated, with improved processing capabilities and programmability.
Future trends in servo technology are poised to enhance the capabilities of automation control systems significantly. Advancements in materials science are leading to more durable and efficient servos, with innovations such as brushless motors and high-strength composite gears.
Frequently Asked Questions
Analog servos use a potentiometer and simple circuitry to control position based on pulse width, while digital servos use a microprocessor for more precise control, faster response, and programmability.
Digital servos are more expensive due to the inclusion of a microprocessor and more advanced circuitry, which provide enhanced performance features.
Yes, in most cases, you can replace an analog servo with a digital servo, provided your power supply and control system are compatible.
The torque rating of a servo indicates the amount of rotational force it can apply, typically measured in kilogram-centimeters (kg-cm) or ounce-inches (oz-in).
Servo speed refers to how quickly a servo can move its output shaft from one position to another, typically measured in seconds per 60 degrees of rotation (e.g., 0.15 sec/60°). This indicates how long it takes the servo to rotate 60 degrees under no load. A lower number means the servo is faster. For example, a servo rated at 0.12 sec/60° is faster than one rated at 0.18 sec/60°. Servo speed is important for applications where quick movements are needed, such as in RC aircraft or robotics.
Power your projects with brand-new, original Omron, Mitsubishi, Schneider Servo – in stock, ready now!
Conclusion
In summary, the choice between analog and digital servos depends on the specific needs of your application. Here are the most important points to remember:
- Analog servos are cost-effective and suitable for less demanding applications.
- Digital servos offer superior performance in terms of speed, torque, and precision.
- PWM is a key technique for controlling servo position and speed.
- Servos are essential components in automation control within manufacturing plants.
- Advancements in servo technology continue to enhance the capabilities of automated systems.
- It is often useful to use both types of servos in one system.
By understanding these concepts and leveraging our expertise at Servo, you can optimize your use of servo technology to achieve greater efficiency and productivity in your manufacturing processes.
Servo is always ready to help you with automation control in your manufacturing plants. Contact us today to learn more about our solutions and how we can help you achieve your automation goals. Don’t hesitate to visit our Proface HMI page or explore our range of Mitsubishi Servo products. Our Omron PLC selection is also available for those seeking reliable automation components. For any inquiries, feel free to reach out through our Contact page. You might also be interested in our Schneider PLC.
Contact Us
Just fill out your name, email address, and a brief description of your inquiry in this form. We will contact you within 24 hours.
You May Also Find These Topics Interesting
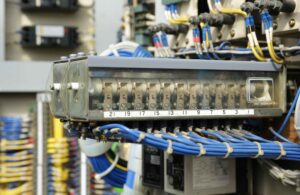
Top 10 Features of Omron PLCs That Make Them Industry Leaders
Programmable Logic Controllers (PLCs) are the backbone of modern industrial automation, and Omron has consistently been at the forefront of this technology. Omron PLCs are renowned for their reliability, versatility, and advanced features, making them a top choice for industries worldwide. In this article, we’ll explore the top 10 features of Omron PLCs that set them apart as industry leaders.
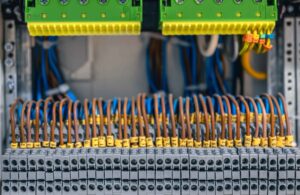
Troubleshooting Common PLC Failures: A Guide to Programmable Logic Controllers
Programmable Logic Controllers (PLCs) are the backbone of modern automation, orchestrating the seamless operation of machinery and industrial processes. However, like any technology, they can encounter issues that disrupt operations.
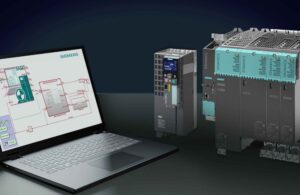
Siemens Drive Fault Code: A Comprehensive Guide to Troubleshooting and Resolution
This article provides a detailed guide to understanding and troubleshooting Siemens drive fault codes. Whether you’re an experienced engineer or new to industrial automation, this comprehensive resource will help you quickly diagnose and resolve issues, minimizing downtime and optimizing productivity. It’s worth reading because it offers practical insights, step-by-step instructions, and expert advice to keep your operations running smoothly.