What Is an Encoder? Basics of How It Works
Table of Contents
What Is an Encoder in Automation?
An encoder is a device that senses mechanical motion and converts it into an electrical signal. This signal can be used to determine position, speed, or direction. In automation systems, encoders provide critical feedback that allows for precise control of machinery.
Encoders are widely used in industries ranging from manufacturing to automotive assembly lines. For instance, in an automotive assembly line, encoders help ensure that parts are placed accurately and that robotic welders perform with high accuracy.
How Does an Encoder Work?
So, how does an encoder work? At its core, an encoder attaches to a motor shaft or other moving part. As the shaft rotates, the encoder generates pulses that represent movement. These pulses, known as a pulse signal, are then sent to a control system.
There are various technologies behind encoders, with optical encoders being among the most common. In an optical encoder, a beam of light emitted from an LED passes through a code wheel patterned with opaque lines. As the wheel rotates, the light is either blocked or passed through, creating an electrical signal that corresponds to movement.
Types of Encoders: Absolute and Incremental
When it comes to encoders, there are two main types: absolute encoders and incremental encoders.
Absolute Encoders
An absolute encoder provides a unique position value or data word at every point of rotation. This means that even if power is lost, the encoder can accurately report its position upon restart. Absolute encoders provide a unique digital code for each angular position, which is crucial in applications where knowing the exact position is essential.
Incremental Encoders
An incremental encoder, on the other hand, generates pulses relative to movement. These pulses can be counted to track position or speed but do not provide a specific position value upon startup. Incremental encoders are simpler and often used where only relative movement needs to be monitored.
Difference Between Absolute and Incremental Encoders
Understanding the difference between absolute and incremental encoders is key to choosing the appropriate encoder for a specific application.
- Precision: Absolute encoders offer higher precision as they detect and report exact positions.
- Startup Behavior: Incremental encoders require a reference point at startup, while absolute encoders do not.
- Complexity: Incremental encoders are generally less complex and more cost-effective.
For applications like robotics or machine tools where exact position data is critical, absolute encoders are preferred. In contrast, incremental encoders are suitable for applications like speed monitoring or direction sensing.
Applications of Encoder Technology in Motion Control Systems
Encoders play a pivotal role in various motion control systems. Here are some common applications:
- Industrial Automation Systems: Encoders are used to control motors, actuators, and other moving parts with high resolution and accuracy.
- Robotics: In robotic systems, encoders help in precise movement and positioning, ensuring tasks are performed correctly.
- Elevator Systems: An encoder in the control system ensures that elevator doors open level with the floor, enhancing safety.
- Medical Devices: Equipment like MRI machines and robotic surgical devices rely on encoders for precise movement.
- Automotive Industry: Encoders are found in vehicles for functions like steering control, braking systems, and assembly line automation.
Frequently Asked Questions
A rotary encoder measures rotational movement and attaches to a rotating shaft, while a linear encoder measures straight-line motion. Both convert motion to an electrical signal but cater to different types of movement.
Optical encoders use light (usually from an LED) and code wheels to detect movement, offering high accuracy. Magnetic encoders use magnetic fields and are typically more robust in harsh environments.
Encoders provide feedback on position and speed, allowing the control system to make precise adjustments. Without encoders, systems would lack the ability to operate with the necessary precision.
Yes, adding an encoder to a stepper motor can enhance its performance by providing feedback, which is especially useful in applications requiring precise control.
Power your projects with brand-new, original Omron, Mitsubishi, Schneider PLC – in stock, ready now!
Conclusion
- Encoders convert motion to an electrical signal used by control devices.
- Absolute encoders provide unique position values, while incremental encoders generate pulses relative to movement.
- Encoders are essential in various industries, including automation, robotics, and the automotive sector.
- Choosing the right encoder depends on the application’s need for precision, complexity, and environment.
- Understanding how encoders work helps in designing efficient and high-accuracy motion control systems.
Looking for new, original PLCs for your projects? At Kwoco, we stock the latest PLCs from top brands like Omron, Mitsubishi, and Schneider. Shop with confidence—fast shipping, guaranteed quality! Buy Now
Contact Us
Just fill out your name, email address, and a brief description of your inquiry in this form. We will contact you within 24 hours.
You May Also Find These Topics Interesting
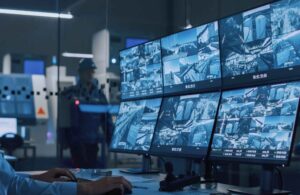
What is DCS? A Guide to Distributed Control Systems
Distributed Control Systems (DCS) have revolutionized the way industries manage and control complex processes. This comprehensive guide will delve into the architecture, benefits, and applications of DCS, explaining why understanding this technology is essential for modern industrial automation and control.
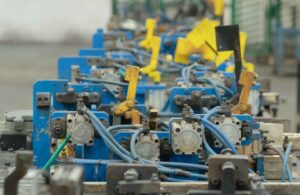
Limit Switches Explained: Types, Uses, and Working Principles
Limit switches are a critical component in numerous devices and machines, playing a key role in detecting the presence or absence of an object. Whether it’s a refrigerator door or an industrial machine, limit switches are behind-the-scenes heroes, performing functions that ensure smooth operation and safety.
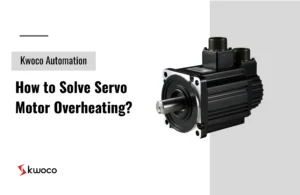
How to Solve Servo Motor Overheating?
10 Essential Insights About OMRON PLC CJ2 Series Overheating issues with servo motors can disrupt operations and cause unnecessary downtime,