Capacitor Reforming: Bringing Your VFD Back to Life After Storage
Table of Contents
What is a VFD and Why is Capacitor Reforming Important?
A Variable Frequency Drive (VFD) is an essential piece of equipment in many industrial settings. It controls the speed of AC motors by varying the frequency and voltage supplied to the motor. Within the VFD, electrolytic capacitors play a vital role in smoothing out the DC voltage after it’s converted from AC.
These capacitors store electrical charge and ensure a stable DC power supply for the VFD’s internal circuitry. A stable DC bus is essential for the inverter section to function. This creates a variable DC voltage, which is then used to synthesize an AC output to control the motor.
Capacitor reforming is crucial, especially when a VFD has been in storage for an extended period. When a drive is not in use, the oxide layer within the electrolytic capacitors can degrade.
This degradation reduces the capacitor’s ability to hold a charge and can lead to failure when the drive is put back into service. Capacitor forming is the process of restoring this oxide layer, ensuring the capacitor can function properly.
For example, if you have a spare Mitsubishi Inverter, it is good practice to ensure it is periodically energized. Although Mitsubishi inverter is a reliable product and reliable products that minimize such issues, but even the best equipment needs proper maintenance.
How Does the Oxide Layer in Electrolytic Capacitors Degrade?
Electrolytic capacitors are made up of two conductive plates separated by a dielectric material. In aluminum electrolytic capacitors, this dielectric is an extremely thin layer of aluminum oxide. This oxide layer acts as an insulator, allowing the capacitor to store electrical charge.
When a DC voltage is applied across the capacitor, this oxide layer is formed. However, when a capacitor is left unused, especially in humid conditions, this layer can start to break down.
The degradation of the oxide layer is a chemical process. Over time, the electrolyte within the capacitor can react with the oxide layer, causing it to thin and become less effective as an insulator. This process is accelerated by heat and humidity.
As the oxide layer thins, the capacitor’s ability to hold a charge decreases, and its leakage current increases. This means that the capacitor can no longer perform its function effectively within the VFD, potentially leading to operational issues or even catastrophic failure when the drive is powered up. If your drive has been in storage, this is a particularly important consideration.
As experts in the Variable Frequency Drives industry, we’ve seen firsthand the consequences of neglecting this crucial aspect of VFD maintenance. We often deal with cases where machinery and equipment factories face downtime due to capacitor failures.
What is the Capacitor Reforming Process for VFDs?
The capacitor reforming process involves gradually applying a DC voltage to the capacitor to rebuild the oxide layer. This is done by slowly increasing the voltage applied to the capacitor over a period, allowing the oxide layer on the anode to reform.
It’s a bit like physical therapy for your capacitor, gently coaxing it back to full health. This must be done carefully to avoid damaging the capacitor. The goal is to restore the dielectric strength of the oxide layer without causing excessive leakage current.
Step | Description | Time (approx.) |
---|---|---|
Initial Inspection | Visually inspect the capacitor for any signs of damage or leakage. | 5 minutes |
Low Voltage Start | Apply a low DC voltage (around 10% of the rated voltage) to the capacitor. | 1 hour |
Monitor Current | Monitor the leakage current. It should initially be high but gradually decrease as the oxide layer reforms. | Ongoing |
Increase Voltage | Slowly increase the voltage in steps, ensuring the leakage current remains within acceptable limits. | Several hours |
Final Stage | Reach the rated voltage and maintain it for a period to ensure the oxide layer is fully reformed. | 1-2 hours |
Typically, a specialized power supply or a variable transformer is used to control the voltage and current during the reforming process. The process can take anywhere from a few hours to a few days, depending on the condition of the capacitor and the VFD itself. A technician will know how to reform the capacitors.
Can I Reform VFD Capacitors Myself, or Should I Consult a Professional?
While it’s technically possible to reform capacitors yourself, it’s generally recommended to consult a qualified technician, especially if you’re not familiar with electronics repair. Reforming capacitors requires specialized equipment and a good understanding of the process.
Incorrectly reforming capacitors can lead to further damage to the capacitor or the VFD. Applying too much voltage or current too quickly can cause the capacitor to overheat and fail, potentially damaging other components in the drive.
It’s always best to err on the side of caution and seek professional help when dealing with VFDs and their components. Also, remember to consult the manual when performing maintenance. For instance, if you are working with an Omron PLC, the manufacturer’s guide will provide specific instructions.
How Often Should I Reform Capacitors in Stored VFDs?
The frequency of capacitor reforming depends on several factors, including the age of the VFD, the storage conditions, and the manufacturer’s recommendations.
Generally, it’s a good idea to reform capacitors in stored VFDs every 6 to 12 months. This prevents excessive degradation of the oxide layer and ensures that the drive will be ready for use when needed.
If you have spare VFDs in storage, it’s crucial to establish a regular maintenance schedule that includes capacitor reforming. This proactive approach can save you from unexpected downtime and costly repairs when you need to put the spare drive into service.
Regular maintenance is key to maximizing the lifespan of your equipment. We recommend that factory solution companies implement such schedules to maintain their inventory of VFDs.
This will help prevent further issues, such as needing to repair or replace a new drive due to capacitor failure.
What are the Risks of Not Reforming Capacitors in a VFD?
Not reforming capacitors in a VFD that has been in storage can lead to several problems, ranging from reduced performance to complete failure of the drive.
When you power up a VFD with degraded capacitors, you risk a sudden and potentially catastrophic failure.
Here are some of the potential consequences:
- Reduced VFD lifespan: Degraded capacitors can shorten the overall lifespan of the VFD.
- Increased leakage current: A degraded oxide layer leads to higher leakage current, which can cause the capacitor to overheat and fail.
- Unstable operation: The VFD may not operate correctly, leading to inconsistent motor control.
- Complete VFD failure: In the worst-case scenario, the capacitor can fail catastrophically, potentially damaging other components within the drive and causing significant downtime.
It’s always more cost-effective to reform the capacitors than to deal with a complete VFD failure. We strongly advise manufacturers and machinery and equipment factory operators to prioritize capacitor maintenance.
How Do I Choose the Right Voltage and Current for Capacitor Reforming?
Choosing the correct voltage and current for capacitor reforming is critical to the success of the process. The voltage should be gradually increased, starting from a low level and slowly approaching the capacitor’s rated voltage. The current should be limited to prevent overheating and damage to the capacitor.
The specific voltage and current values will depend on the capacitor’s specifications and the reforming equipment being used. It’s essential to consult the capacitor’s datasheet or the VFD manufacturer’s recommendations for specific guidelines. The initial voltage should be about 10-20% of the rated voltage.
As the layer is formed, the voltage is applied incrementally. The voltage can then be increased in small steps. When applying power, always refer to the manual for the recommended procedure. The power supply needs to be monitored.
If you are unsure, seek professional assistance to ensure the process is performed correctly. The correct procedure will ensure the drive is operational for when you need to install it.
What are the Signs That a VFD Capacitor Needs Reforming?
There are several signs that a VFD capacitor may need reforming:
- The VFD has been in storage for an extended period: If a drive has been sitting idle for six months or more, the capacitors likely need reforming.
- Bulging or leaking capacitor: Physical signs of damage, such as a bulging capacitor case or electrolyte leakage, indicate that the capacitor is failing and needs to be replaced rather than reformed.
- The VFD fails to power up correctly: If the VFD doesn’t power up or operates erratically after being in storage, the capacitors may be the culprit.
- Error codes related to the DC bus: Many VFDs have diagnostic features that can indicate problems with the DC bus, which could be related to capacitor issues.
If you observe any of these signs, it’s essential to address the issue promptly. We emphasize the importance of regular inspection and maintenance to identify potential problems before they lead to failures.
If you have a Proface HMI connected to your system, it can often display error codes that help diagnose issues with the VFD.
How Does Capacitor Reforming Extend VFD Life?
Capacitor reforming extends VFD life by restoring the health of the electrolytic capacitors, which are critical components within the drive. By rebuilding the oxide layer, reforming ensures that the capacitors can perform their function effectively, providing a stable DC voltage for the VFD’s internal circuitry.
Regular capacitor reforming, especially for stored VFDs, prevents the capacitors from degrading to the point of failure. This proactive maintenance approach can significantly extend the lifespan of the VFD and reduce the likelihood of unexpected downtime. It also prevents the need to purchase a new drive. Think of it as preventative medicine for your VFD.
What is the Connection Between Industrial Automation and VFD Maintenance?
Industrial automation relies heavily on the reliable operation of equipment like VFDs. In modern automation systems, VFDs are used to control a wide variety of AC motors in various applications, from conveyor belts to pumps to fans.
Proper VFD maintenance, including capacitor reforming, is essential to maintaining the overall health of your industrial automation system. As a provider of automation solutions, we understand this connection intimately.
Neglecting VFD maintenance can lead to equipment failures, disrupting your automation processes and causing costly downtime. By implementing a proactive maintenance schedule that includes capacitor reforming, you can ensure that your VFDs remain in optimal condition, supporting the smooth operation of your automated systems.
We’ve seen how proper maintenance can make a significant difference in the performance and reliability of industrial automation systems. Contact us to learn more about our automation solutions and how we can help you optimize your operations.
Frequently Asked Questions
If your VFD has been in storage for over six months, or if you notice signs of capacitor failure like bulging, leakage, or erratic VFD operation, it’s likely time for capacitor reforming.
No, it’s best to use a specialized power supply or a variable transformer that allows you to precisely control the voltage and current applied to the capacitor.
Applying excessive voltage can cause the capacitor to overheat, potentially leading to permanent damage or even an explosion.
No, capacitor reforming is a maintenance procedure to restore the health of existing capacitors, while capacitor replacement involves installing new capacitors.
The process can take anywhere from a few hours to a couple of days, depending on the condition of the capacitor.
Power your projects with brand-new, original Omron, Mitsubishi, Schneider Servo – in stock, ready now!
Conclusion
Here are the most important takeaways regarding capacitor reforming in VFDs:
- Capacitor reforming is a crucial maintenance procedure, especially for VFDs that have been in storage.
- The process involves gradually applying voltage to rebuild the degraded oxide layer in electrolytic capacitors.
- Regular reforming can significantly extend the lifespan of your VFDs and prevent unexpected downtime.
- It’s generally recommended to seek professional assistance for capacitor reforming to avoid damaging the VFD.
- Proper VFD maintenance, including capacitor reforming, is essential for the reliable operation of industrial automation systems.
- Neglecting capacitor reforming can lead to VFD failure, causing costly downtime and potentially damaging other equipment.
Contact Us
Just fill out your name, email address, and a brief description of your inquiry in this form. We will contact you within 24 hours.
You May Also Find These Topics Interesting
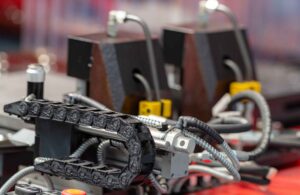
5 Types of Servo Motors: The Ultimate Guide
Servo motors are integral components in modern automation, robotics, and control systems. They offer precise control over motion, which is essential in various industrial and commercial applications. Understanding the different types of servo motors can help you choose the right one for your project. In this guide, we’ll explore the five main types of servo motors, their workings, applications, and advantages.
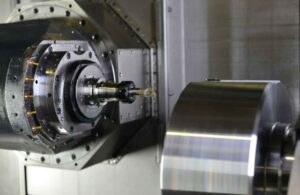
Decoding the Difference Between Servo Motor and Spindle Motor in CNC Applications
This article dives into the distinctions between servo motors and spindle motors, two critical components in the world of CNC machinery. Understanding these differences is crucial for anyone involved in industrial automation, from seasoned engineers to those new to the field. We’ll explore their unique characteristics, applications, and how they contribute to the precision and efficiency of CNC machines.
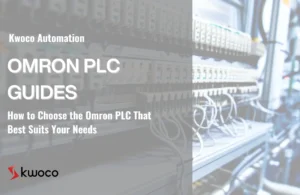
How to Choose the Omron PLC That Best Suits Your Needs
How to Choose the Omron PLC That Best Suits Your Needs Struggling to find the right PLC for your industrial