7 Common Servo Motor Failures
- kwoco-plc.com
- September 20, 2024
- 12:15 am
As a seasoned engineer with extensive experience in industrial automation, I’ve seen my fair share of servo motor issues in various applications.
Whether you’re working with Omron, Mitsubishi, Schneider, or other major brands, understanding these common failures can help keep your operations running smoothly. Here’s a breakdown of seven frequent servo motor problems and what you can do to avoid them.
Table of Contents
1. Overheating
Servo motors can overheat due to a variety of reasons, including excessive load, poor ventilation, or incorrect settings in the control system. Overheating is one of the most common issues and can lead to irreversible damage if not addressed promptly. environments.
Why It Happens
Overheating typically occurs when the motor is pushed beyond its designed operational limits. A lack of proper ventilation or cooling in the motor’s environment can also contribute to this problem.
Often, the motor may be operating at higher than recommended speeds or loads, causing internal components to overheat and fail.
Causes of Overheating:
Cause | Description |
---|---|
Excessive Load | Motor operates under a load higher than its rated capacity. |
Poor Ventilation | Inadequate airflow around the motor. |
Incorrect Control Settings | Control system errors leading to improper motor operation. |
Solutions
To avoid overheating, ensure that the motor is operating within its rated specifications. Regularly check the environment for adequate cooling and proper ventilation. Adjust control settings as necessary to match the motor’s operational requirements.
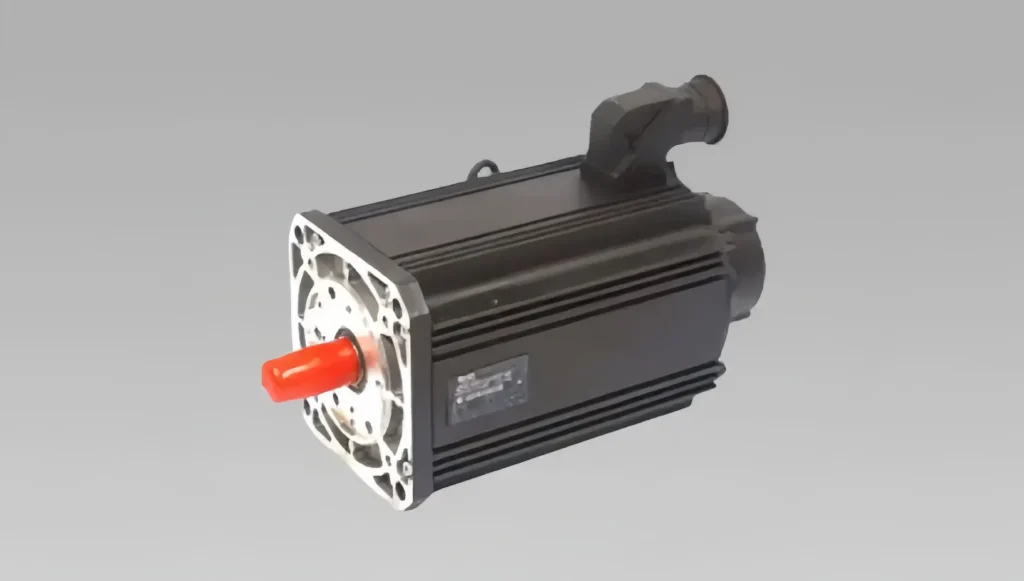
2. Bearing Failures
Bearings are crucial components of servo motors, and their failure can result in significant downtime. Bearing issues are usually caused by contamination, lack of lubrication, or excessive loads.
Why It Happens
Bearings can fail due to contamination from dirt, dust, or other foreign particles entering the motor. This contamination can cause increased friction and wear.
Additionally, inadequate lubrication can lead to overheating and eventual failure. Bearings may also fail when subjected to loads higher than their capacity, leading to excessive stress on the bearing surfaces.
Symptoms of Bearing Failures:
- Unusual noise during operation
- Increased vibration
- Motor shaft wobbling
Solutions
Ensure that the bearings are regularly lubricated and that seals are in good condition to prevent contamination. Implement a maintenance schedule to inspect and replace bearings before they fail.
3. Electrical Failures
Electrical failures can manifest in various ways, such as short circuits, blown fuses, or issues with the motor windings. These failures often stem from power supply problems or insulation breakdown.
Why It Happens
Electrical failures usually occur due to issues like voltage spikes, faulty wiring, or insulation degradation over time. These conditions can cause short circuits within the motor, leading to failures that can damage the windings or other electrical components.
Common Electrical Failures:
Failure Type | Description |
---|---|
Short Circuit | Caused by faulty wiring or damaged insulation. |
Blown Fuses | Typically a result of overcurrent conditions. |
Motor Windings Issues | Degradation of the winding insulation leading to breakdowns. |
Solutions
To prevent electrical failures, regularly inspect wiring and connections. Use surge protection devices to shield the motor from voltage spikes. Additionally, ensure that motor windings are checked periodically for signs of wear.
4. Encoder Failures
Encoders are critical for providing feedback on the motor’s position and speed. When encoders fail, the motor may lose its precise control, leading to performance issues or shutdowns.
Why It Happens
Encoder failures often result from environmental factors such as vibration, contamination, or electrical noise. Mechanical misalignment can also cause the encoder to provide inaccurate readings, impacting motor performance.
Signs of Encoder Failures:
- Inconsistent speed control
- Erratic motor movement
- Positioning errors
Solutions
To mitigate encoder failures, ensure the encoder is properly aligned and protected from environmental contaminants. Use shielded cables to reduce electrical noise interference.
5. Mechanical Misalignments
Mechanical misalignments can significantly impact servo motor performance, leading to vibrations, increased wear, and eventual component failure.
Why It Happens
Misalignments occur when the motor shaft and the load it drives are not properly aligned. This can result from improper installation, wear over time, or external forces acting on the motor.
Common Misalignment Types:
Misalignment Type | Description |
---|---|
Parallel | Shafts are not aligned along a straight line. |
Angular | Shafts are at an angle to each other. |
Combination | Involves both parallel and angular issues. |
Solutions
Use precision alignment tools during installation and conduct regular checks to ensure proper alignment. Correct misalignments immediately to prevent long-term damage.
Power your projects with brand-new, original Omron, Mitsubishi, Schneider Servo – in stock, ready now!
6. Contamination and Dust Ingress
Servo motors are sensitive to contamination, especially in industrial environments. Dust, dirt, and other particles can enter the motor, leading to reduced performance and mechanical failure.
Why It Happens
Contamination typically happens when seals degrade or are improperly installed, allowing foreign materials to enter the motor. Dust and dirt can damage internal components, increase wear, and lead to overheating.
Impact of Contamination:
- Increased friction
- Shortened motor lifespan
- Potential electrical shorts
Solutions
Ensure that all seals are intact and properly fitted. Regularly clean the environment around the motor and consider using protective covers if necessary.
7. Excessive Vibration
Excessive vibration is often a sign of underlying issues such as imbalance, misalignment, or bearing failure. If left unchecked, it can cause severe damage to the motor.
Why It Happens
Vibration can be caused by imbalanced loads, incorrect mounting, or internal motor issues like worn bearings. Excessive vibration not only affects motor performance but also accelerates wear and tear.
How Vibration Affects Motors:
- Loosens components
- Damages bearings
- Leads to misalignment
Solutions
Identify and correct the source of vibration as soon as possible. Use vibration analysis tools to detect and diagnose issues early, and ensure proper balancing during installation.
Conclusion
Servo motors are critical components in automation, and their reliability is essential. By understanding these common failures and implementing preventative measures, you can extend the life of your servo motors and maintain peak performance. Regular maintenance, proper installation, and timely inspections are key to preventing these common issues.
KWOCO offers brand new and original Omron, Mitsubishi, Delta servo motors in stock and ready for immediate shipment. Contact us now for a free quote.
Contact Us
Just fill out your name, email address, and a brief description of your inquiry in this form. We will contact you within 24 hours.
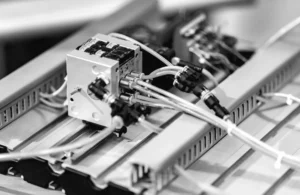
Why Your PLC Needs a Separate Power Supply
Why Your PLC Needs a Separate Power Supply Have you ever wondered why PLC systems often require a separate power
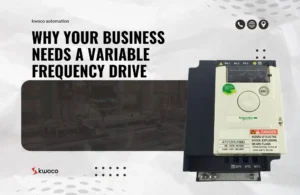
Why Your Business Needs a Variable Frequency Drive
Why Your Business Needs a Variable Frequency Drive When managing industrial operations, optimizing energy efficiency while maintaining performance is crucial.
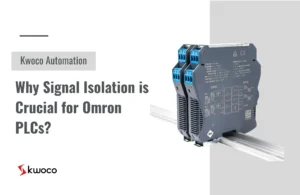
Why Signal Isolation is Crucial for Omron PLCs?
Why Signal Isolation is Crucial for Omron PLCs? In the world of industrial automation, signal interference is a silent killer.