Electrical Relay: Understanding the Different Types of Relays
Table of Contents
1. What is a Relay and How Does It Work?
A relay is an electrically operated switch that uses an electromagnet to mechanically operate a switch. Essentially, a relay is used to control a circuit by a separate low-power signal, or where several circuits must be controlled by one signal.
Relays were first used in long-distance telegraph circuits as amplifiers: they repeated the signal coming in from one circuit and re-transmitted it on another circuit. Relays were used extensively in telephone exchanges and early computers to perform logical operations.
When the relay is inactive, there is no power flowing to the relay coil. When the relay is activated, an electrical signal is sent to the relay coil, which generates a magnetic field that moves the armature. The armature then either makes or breaks contact with the switch, completing or breaking the circuit.
The basic operation of a relay involves an input circuit and an output circuit. The input circuit consists of a coil of wire wrapped around a soft iron core.
When an electrical current flows through the coil, it creates a magnetic field. This magnetic field attracts a movable armature, which is connected to a set of contacts. When the armature moves, it either opens or closes the contacts in the output circuit, thereby controlling the flow of electricity in that circuit.
A relay is an electrical switch that opens and closes under the control of another electrical circuit. A relay typically consists of a coil of wire (the electromagnet), an armature, a spring, and a set of electrical contacts. The coil is wrapped around a core, usually made of iron.
When a current flows through the coil, it creates a magnetic field that attracts the armature. The armature is a movable part of the relay that is connected to the contacts. The spring holds the armature in its default position when no current flows through the coil.
2. Why are Relays Important in Industrial Automation?
In industrial automation, relays are essential components for controlling high-voltage or high-current circuits with a low-voltage control signal.
They provide electrical isolation between the control circuit and the load circuit, enhancing safety and preventing damage to sensitive electronic components.
As an experienced provider in this field, I’ve seen firsthand how relays can enhance the safety and efficiency of industrial processes. Relays are particularly crucial in applications such as motor control, lighting systems, and power distribution.
Relays also enable the automation of complex sequences and processes. For instance, in a machinery and equipment factory, relays can be used to start and stop motors, activate alarms, and control the movement of robotic arms.
This level of control is essential for maintaining productivity and ensuring consistent product quality. They are instrumental in switching devices on and off and are integral in protective systems to detect faults. Relays provide a crucial safety aspect by isolating the control circuit from the load circuit.
Relays can also be used to implement logic functions, similar to digital logic gates. For example, a relay can be configured to act as an AND gate, where the output circuit is only energized if all input circuits are activated.
This capability is valuable in creating sophisticated control systems for industrial applications. The use of relays in industrial automation not only increases efficiency but also extends the life of a relay and other equipment due to precise control mechanisms.
3. What Are the Main Types of Relays?
There are numerous types of relays used in various applications. Some of the most common relay types include electromechanical relays (EMR), solid-state relays (SSR), reed relays, latching relays, and time delay relays.
Each type of relay has unique characteristics and is suited for specific applications. Choosing the appropriate relay type is crucial for the reliable operation of any electrical system.
Each type has its advantages and is designed for particular applications. Relay applications vary widely, from simple switching tasks to complex control systems.
Electromechanical relays are the most common type of relay and are widely used in industrial automation. They consist of a coil, an armature, and a set of contacts.
When the coil is energized, the armature moves and either opens or closes the contacts. Solid state relays, on the other hand, use semiconductors to switch the load circuit. They have no moving parts, which makes them more reliable and less prone to wear and tear.
Reed relays are another type of relay that is commonly used in applications requiring high speed and long life. They consist of two or more reed switches enclosed in a glass tube.
The reed switches are activated by a magnetic field, which can be generated by a coil or a permanent magnet. Latching relays are designed to remain in their last switched state even after the control signal is removed.
They are useful in applications where power consumption needs to be minimized. In conclusion, understanding the different types of relays is crucial. The relay does not use moving parts to switch the circuit. It is important to understand the different relay contact types to ensure proper operation.
4. How Do Electromechanical Relays (EMR) Function?
Electromechanical relays operate based on the principle of electromagnetism. When a current flows through the relay coil, it generates a magnetic field that attracts the armature. The armature is connected to one or more sets of contacts.
Depending on the design of the relay, the contacts may be normally open (NO) or normally closed (NC). A relay is an electrical switch that opens and closes under the control of another electrical circuit.
When the relay coil is energized, the armature moves, causing the contacts to either close or open, thereby completing or breaking the circuit.
EMR relays are commonly used in applications where a low-voltage control signal needs to switch a high-voltage or high-current load circuit.
They provide excellent electrical isolation between the control circuit and the load circuit, making them suitable for use in harsh industrial environments. The relay is activated when current flows through the coil.
For instance, in a motor control application, an EMR relay can be used to turn a motor on or off based on a signal from a PLC or another control device. The relay is energized, the contacts change their state. The relay becomes a crucial component in the system.
One of the key advantages of electromechanical relays is their ability to handle high currents and voltages. They are also relatively inexpensive and easy to replace.
However, they have some limitations, such as slower switching speeds compared to solid-state relays and susceptibility to mechanical wear and tear. A relay is designed to withstand various environmental conditions.
The relay requires careful consideration when selecting the right type. The relay activates when the control circuit is energized.
5. What is a Solid State Relay (SSR) and How Does It Differ from EMR?
A solid-state relay (SSR) is an electronic switching device that uses semiconductors, such as thyristors or transistors, to switch a load circuit on or off. Unlike electromechanical relays, SSRs have no moving parts.
This makes them more reliable, faster, and quieter. They also have a longer lifespan since there are no mechanical components to wear out. Inside the relay, there are various components that work together. The relay switches between on and off states. When the relay is deactivated, the contacts return to their original state.
SSRs are particularly useful in applications that require frequent switching, high-speed operation, or operation in environments where noise or vibration is a concern. They are commonly used in lighting control, motor control, and heating control applications.
Solid-state relays often incorporate features like zero-voltage switching and optical isolation to enhance performance and safety. The relay consists of a coil and a set of contacts. Relays are often used in complex circuit designs.
However, SSRs have some limitations compared to EMRs. They typically have a higher on-state voltage drop, which can lead to increased power dissipation and heat generation.
They are also more susceptible to damage from voltage spikes and overcurrent conditions. Despite these limitations, solid-state relays are an excellent choice for many industrial automation applications due to their reliability and performance characteristics.
The relay is used to control high-power circuits. The relay is also a crucial part of many safety systems.
6. What are Reed Relays and Their Specific Applications?
Reed relays are a specialized type of relay that uses reed switches as the switching elements. A reed switch consists of two thin, ferromagnetic reeds enclosed in a hermetically sealed glass tube.
When a magnetic field is applied to the switch, the reeds are attracted to each other and make contact, completing the circuit. Reed relays are known for their fast switching speeds, low contact resistance, and long lifespan. These relays remain in their last position even when power is removed. Relays are constructed to be durable and reliable.
They are commonly used in applications that require high reliability and durability, such as in test and measurement equipment, telecommunications systems, and medical devices. Reed relays are also suitable for switching low-level signals due to their low contact resistance and minimal signal distortion.
One significant advantage of reed relays is their ability to operate in harsh environments. They are resistant to shock, vibration, and moisture, making them ideal for use in automotive, aerospace, and industrial applications.
However, reed relays have some limitations. They are generally not suitable for switching high currents or voltages, as the thin reeds can be easily damaged by excessive current flow.
They are also more expensive than some other types of relays, such as electromechanical relays. Despite these limitations, reed relays offer excellent performance and reliability in many specialized applications. They are also used to test a relay in various applications.
7. How to Choose the Right Relay for Your Application?
Choosing the appropriate relay for a specific application requires careful consideration of several factors, including the voltage and current requirements of the load circuit, the characteristics of the control circuit, the operating environment, and the desired switching speed and lifespan.
As an expert in industrial automation, I always advise my clients to start by defining their specific needs and constraints. Relays are typically used in circuits that require isolation.
For example, if you need to switch a high-voltage AC motor using a low-voltage DC control signal, an electromechanical relay or a solid-state relay rated for the appropriate voltage and current would be suitable.
If the application requires high-speed switching or operation in a noisy environment, a solid-state relay would be the better choice. In contrast, if cost is a primary concern and the switching speed is not critical, an electromechanical relay may be more appropriate.
When selecting a relay, it’s essential to consider factors like coil voltage, contact rating, and switching speed.
It’s also important to consider the operating environment. If the relay will be exposed to high temperatures, humidity, or corrosive substances, you’ll need to choose a relay that is designed to withstand those conditions.
Reed relays or hermetically sealed electromechanical relays are often used in such environments. Additionally, consider the expected lifespan of the relay and the frequency of switching.
For applications with high switching cycles, solid-state relays or reed relays may be more suitable due to their longer lifespan and resistance to mechanical wear.
8. What is a Relay Contact and What are the Different Contact Types?
A relay contact is the part of the relay that makes or breaks the electrical connection in the load circuit. The contacts are typically made of a conductive material, such as silver alloy, that can withstand the electrical and mechanical stresses of switching.
There are several different types of relay contacts, each with its own characteristics and applications.
The most common contact types are normally open (NO) and normally closed (NC). NO contacts are open when the relay is not energized and closed when the relay is energized. NC contacts are closed when the relay is not energized and open when the relay is energized.
Some relays have both NO and NC contacts, allowing for more complex switching configurations. For instance, a double-pole, double-throw (DPDT) relay has two sets of NO and NC contacts, enabling it to switch two separate circuits simultaneously.
Other contact types include make-before-break (MBB) and break-before-make (BBM) contacts. MBB contacts ensure that the new connection is made before the old connection is broken, preventing any interruption in the circuit.
BBM contacts, on the other hand, break the existing connection before making the new connection. The choice of contact type depends on the specific requirements of the application. NO contacts are commonly used for turning loads on and off, while NC contacts are often used for safety interlocks or alarm circuits.
9. How to Test a Relay?
Testing a relay involves verifying its proper operation by checking the continuity of the contacts and the resistance of the coil. As someone who has worked with countless relays, I can share a simple yet effective method.
You can use a multimeter or a dedicated relay tester to perform these tests. To test an electromechanical relay, first disconnect it from the circuit and use the multimeter to measure the resistance of the coil. The resistance should match the value specified in the relay’s datasheet.
Next, use the multimeter to check the continuity of the contacts. For NO contacts, there should be no continuity when the relay is not energized and continuity when the relay is energized. For NC contacts, it should be the opposite.
You can energize the relay by applying the appropriate voltage to the coil terminals. Listen for a click sound, which indicates that the armature is moving and the contacts are changing state. Testing a solid-state relay is slightly different since it doesn’t have a coil or mechanical contacts. Instead, you’ll need to check the input and output circuits.
Use the multimeter to measure the voltage drop across the input terminals when the control signal is applied. The voltage drop should match the value specified in the datasheet. Then, check the continuity of the output circuit.
For an SSR, the output circuit should have low resistance when the control signal is applied and high resistance when it’s not. A relay contact is open until the appropriate conditions are met.
10. What are the Common Applications of Relays in Industrial Settings?
Relays are used in a wide range of industrial applications, including motor control, lighting control, power distribution, process control, and safety systems.
In a machinery and equipment factory, relays are commonly used to control the starting and stopping of motors, activate and deactivate conveyor belts, and manage the operation of robotic arms. They are also used in safety circuits to shut down equipment in case of an emergency.
In manufacturing plants, relays play a crucial role in automating various processes, such as temperature control, level control, and flow control. For example, a relay can be used to turn a heating element on or off based on a signal from a temperature sensor.
Similarly, a relay can control a pump to maintain a certain liquid level in a tank. Relays can also be used to implement complex control logic, such as sequencing operations or interlocking different parts of a machine.
Factory solution companies often use relays to integrate different systems and create customized automation solutions for their clients. Relays provide a simple and reliable way to interface between different control systems, sensors, and actuators.
They can also be used to create safety systems that protect personnel and equipment from hazards. For instance, a safety relay can be used to monitor emergency stop buttons, light curtains, and other safety devices, and shut down the machinery if any of these devices are activated.
- Learn more about our Omron product line.
- Discover our range of Mitsubishi automation solutions.
- Explore our Schneider offerings.
- Find out how our Proface HMI can enhance your operations.
- Check out our comprehensive PLC solutions.
- See our relay selection.
Frequently Asked Questions
Reed relays offer fast switching speeds, low contact resistance, and a long lifespan. They are also resistant to shock, vibration, and moisture, making them suitable for harsh environments. A single throw relay can control one circuit at a time.
Consider the voltage and current requirements of the load circuit, the characteristics of the control circuit, the operating environment, and the desired switching speed and lifespan. SSRs are ideal for high-speed switching, while EMRs are better for high-current applications.
You can use a multimeter to check the coil resistance and the continuity of the contacts. For EMRs, listen for a click sound when energizing the coil. For SSRs, check the voltage drop across the input terminals and the continuity of the output circuit. The relay works by using an electromagnet.
Yes, relays are frequently used in safety applications. Safety relays are specifically designed to monitor safety devices like emergency stop buttons and light curtains, and they can shut down machinery if these devices are activated. The relay is an electrical device used in many applications. The relay can switch between different states.
Power your projects with brand-new, original Omron, Mitsubishi, Schneider Servo – in stock, ready now!
Conclusion
- Relays are essential components in industrial automation, providing control and isolation for various circuits.
- Different types of relays, including electromechanical, solid-state, and reed relays, offer unique advantages for specific applications.
- Choosing the right relay involves considering factors such as voltage, current, switching speed, lifespan, and operating environment.
- Relays are used in a wide range of industrial settings, including machinery and equipment factories, manufacturing plants, and factory solution companies.
- Proper testing and maintenance of relays are crucial for ensuring the reliable operation of industrial systems.
- As a leading provider of industrial automation and control products, we offer a comprehensive range of relays and the expertise to help you choose the right solution for your needs.
- Relay applications include power supplies, motor drives, and automotive systems.
- Different relay types like electromechanical relay, solid-state relay, and reed relay serve different purposes.
- Relays provide isolation between the control and load circuits.
Contact Us
Just fill out your name, email address, and a brief description of your inquiry in this form. We will contact you within 24 hours.
You May Also Find These Topics Interesting
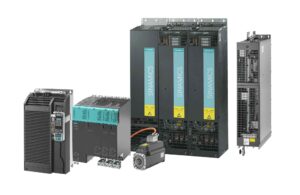
SINAMICS S120 Faults: A Troubleshooting Guide
This article serves as a detailed guide to understanding and resolving SINAMICS S120 fault codes. Whether you’re an experienced engineer or new to industrial automation, this resource provides invaluable insights into the intricacies of SINAMICS S120 drives, helping you diagnose and troubleshoot faults efficiently. With a focus on practical solutions, we aim to equip you with the knowledge necessary to minimize downtime and optimize the performance of your machinery.
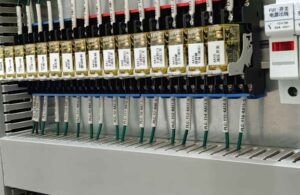
What is a VFD? – How to use one in Applications
Variable Frequency Drives (VFDs) are transforming the landscape of industrial automation by providing unparalleled control over motor speed and energy efficiency. In this comprehensive guide, we’ll delve into what a VFD is, how VFDs work, and how to use one in your applications to achieve optimal performance and energy savings.
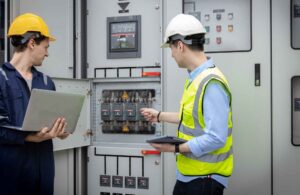
VFD vs VSD: Understanding Key Differences in Motor Control
Are you confused about the difference between Variable Frequency Drives (VFDs) and Variable Speed Drives (VSDs)? This comprehensive guide will clarify these essential motor control technologies, helping you make informed decisions for your industrial applications.