What is the Difference Between PLC and CNC?
In my experience as an engineer at Kwoco, understanding the differences between PLC (Programmable Logic Controller) and CNC (Computer Numerical Control) is essential for optimizing your manufacturing processes. Both systems play pivotal roles, but they serve distinct purposes and operate differently.
Table of Contents
Understanding these differences can significantly impact your project’s efficiency and success. Let’s dive deeper into what sets PLC and CNC apart and how each can benefit your operations.
What Exactly is a PLC?
A Programmable Logic Controller, or PLC, is a rugged digital computer used for automation of electromechanical processes. Think of it as the brain behind many industrial machines.
PLCs are designed to handle multiple inputs and outputs, making them ideal for controlling machinery on factory assembly lines, amusement rides, or lighting fixtures. They are highly reliable and can operate in harsh environments, which is why they’re a staple in industries worldwide.
Key Features of PLCs:
- Programmability: Easily programmable using ladder logic or other programming languages.
- Real-time Operation: Capable of real-time responses to changing conditions.
- Scalability: Can be expanded with additional modules to increase functionality.
- Connectivity: Integrates seamlessly with other industrial systems and networks.
What is a CNC?
Computer Numerical Control, or CNC, refers to the automated control of machining tools by means of a computer. It revolutionized manufacturing by enhancing precision and efficiency.
CNC machines interpret coded instructions (G-code) to perform tasks like cutting, drilling, milling, and turning with high accuracy. These machines are essential in industries that require detailed and repeatable processes, such as aerospace, automotive, and electronics.
Key Features of CNC Systems:
- Precision: Achieves high levels of accuracy and repeatability.
- Automation: Reduces the need for manual intervention, increasing productivity.
- Versatility: Capable of performing a wide range of machining operations.
- Integration: Can be integrated with CAD/CAM software for streamlined workflows.
How Do PLC and CNC Differ?
While both PLC and CNC systems are integral to industrial automation, they serve different functions and are used in varying applications.
Purpose and Functionality
PLCs are primarily used for controlling and automating processes. They manage the operations of machinery, ensuring that each component functions in harmony to achieve the desired outcome.
On the other hand, CNC systems are focused on the precise control of machining tools. They handle the detailed movements and operations required to fabricate parts with exact specifications.
Programming and Operation
PLCs are typically programmed using ladder logic, which resembles electrical relay logic, making it easier for engineers familiar with electrical systems to implement.
CNC machines use G-code, a language that directs the tool movements and operations. This programming requires a good understanding of machining processes and CAD/CAM software.
Application Areas
PLCs are versatile and used in a wide range of industries for various automation tasks, from simple control systems to complex manufacturing processes.
CNC machines are specialized for manufacturing tasks that demand high precision and repeatability, such as producing intricate components for machinery, vehicles, and electronics.
When to Use PLC vs. CNC?
Choosing between PLC and CNC depends on your specific needs and the nature of your projects.
Use PLC When:
- You need to automate and control multiple processes or machinery.
- Your application requires real-time monitoring and adjustments.
- Flexibility and scalability are important for your operations.
- You are managing complex systems with numerous inputs and outputs.
Use CNC When:
- Precision machining and high accuracy are critical.
- You are involved in manufacturing parts that require detailed specifications.
- Automation of repetitive machining tasks is needed to enhance productivity.
- Integration with CAD/CAM software is essential for your workflow.
Integration and Compatibility
Both PLC and CNC systems can be integrated into a larger automation framework to enhance overall efficiency.
PLCs can communicate with CNC machines to coordinate complex manufacturing processes, ensuring that each part is produced accurately and efficiently.
At Kwoco, we offer a wide range of PLC and CNC products from reputable brands like Omron, Mitsubishi, Schneider, Panasonic, and Siemens. Our extensive stock ensures that you can find the right components to meet your automation needs.
Benefits of Using PLC and CNC Systems
Implementing PLC and CNC systems can bring numerous advantages to your business.
Advantages of PLC:
- Enhanced Control: Precise management of machinery and processes.
- Improved Reliability: Robust systems that operate consistently under demanding conditions.
- Flexibility: Easy to reprogram for different tasks or modifications in the production process.
Advantages of CNC:
- High Precision: Achieves exact dimensions and tolerances.
- Increased Productivity: Automates complex tasks, reducing production time.
- Consistency: Ensures uniformity across all manufactured parts.
Common Misconceptions
There are several misconceptions about PLC and CNC systems that can lead to confusion.
Misconception 1: PLCs and CNCs are the Same
While both are used in automation, they serve different purposes. PLCs control processes, whereas CNCs handle machining tasks.
Misconception 2: CNCs Don't Require Programming Knowledge
CNC machines require expertise in programming languages like G-code and understanding of machining processes to operate effectively.
Misconception 3: PLCs are Obsolete with Modern Technology
PLCs continue to evolve and remain vital in automation due to their reliability and flexibility.
Choosing the Right System for Your Needs
Selecting between PLC and CNC systems involves assessing your specific requirements and project goals.
Consider the following factors:
- Project Complexity: More complex processes may benefit from PLC control.
- Precision Needs: High-precision tasks are best handled by CNC machines.
- Budget: Evaluate the cost-effectiveness of each system based on your budget and expected ROI.
- Scalability: Ensure the system can grow with your business needs.
At Kwoco, we understand the nuances of both PLC and CNC systems. Our team is here to help you make informed decisions, providing technical support and solutions tailored to your needs.
Real-World Applications
Understanding how PLC and CNC systems are applied in real-world scenarios can clarify their differences and uses.
PLC in Action
In a manufacturing plant, PLCs control the assembly line operations. They manage the timing, coordination, and functionality of various machines, ensuring smooth and efficient production.
CNC in Action
In an automotive workshop, CNC machines are used to fabricate precise engine components. They cut and shape metal parts to exact specifications, ensuring each component fits perfectly within the engine assembly.
Future Trends in PLC and CNC Technology
The future of industrial automation is bright, with advancements in both PLC and CNC technologies.
PLC Innovations
- IoT Integration: Enhanced connectivity for smarter automation systems.
- AI and Machine Learning: Improved predictive maintenance and process optimization.
- Enhanced User Interfaces: More intuitive programming and monitoring capabilities.
CNC Innovations
- Advanced Materials Processing: Capabilities to handle new and complex materials.
- Increased Automation: Fully automated production lines with minimal human intervention.
- Improved Precision: Continued advancements in machining accuracy and efficiency.
How Kwoco Can Help
At Kwoco, we pride ourselves on being a leading stockist of original industrial automation products. With over 30 million products in stock, we can supply the PLCs and CNC systems you need from top brands like Omron, Mitsubishi, Schneider, Panasonic, and Siemens.
Our one-stop purchasing service ensures fast product quotations and shipments, coupled with expert technical support and solution assistance. We help you overcome common challenges such as finding reliable suppliers and avoiding counterfeit products.
Frequently Asked Questions
Absolutely. PLCs can control the overall process while CNC machines handle specific machining tasks, ensuring seamless integration and efficiency.
It depends on your specific needs. For process control, PLCs are more versatile, while CNCs are ideal for precise machining tasks. Assess your requirements to determine the best fit.
Choose reputable brands like Omron, Mitsubishi, Schneider, Panasonic, and Siemens, known for their reliability and quality in industrial automation.
We offer comprehensive technical support, solution assistance, and fast shipment services to ensure your operations run smoothly.
Yes, many manufacturers provide training resources, and our team at Kwoco can guide you to the right materials and support.
Power your projects with brand-new, original Omron, Mitsubishi, Schneider PLC – in stock, ready now!
Conclusion
Understanding the differences between PLC and CNC systems is crucial for optimizing your industrial automation processes. At Kwoco, we provide the expertise and products you need to enhance your operations efficiently and reliably.
Looking for new, original PLCs for your projects? At Kwoco, we stock the latest PLCs from top brands like Omron, Mitsubishi, and Schneider. Shop with confidence—fast shipping, guaranteed quality! Buy Now
Contact Us
Just fill out your name, email address, and a brief description of your inquiry in this form. We will contact you within 24 hours.
You May Also Find These Topics Interesting
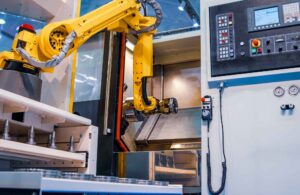
Navigating the Future: Unpacking the Current State of the Industrial Automation Industry
The industrial automation industry is evolving at an unprecedented pace. This article delves into the current state of this dynamic sector, exploring the key trends, market size, and future projections. It’s a must-read because it provides a comprehensive overview of where the industry stands today and where it’s heading, offering valuable insights for anyone interested in or involved with industrial automation.
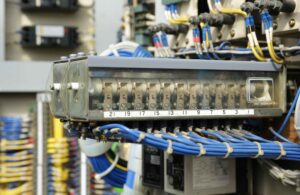
Top 10 Features of Omron PLCs That Make Them Industry Leaders
Programmable Logic Controllers (PLCs) are the backbone of modern industrial automation, and Omron has consistently been at the forefront of this technology. Omron PLCs are renowned for their reliability, versatility, and advanced features, making them a top choice for industries worldwide. In this article, we’ll explore the top 10 features of Omron PLCs that set them apart as industry leaders.
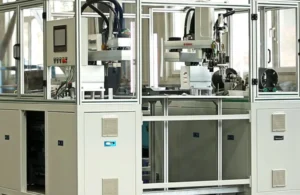
Capacitive vs. Resistive Touch Screens: Which One Is Right for Industrial Use?
Capacitive vs. Resistive Touch Screens: Which One Is Right for Industrial Use? Ever find yourself torn when choosing a touch