PLC Programming Guide: Master Industrial Automation
PLC programming is the cornerstone of modern industrial automation, allowing engineers and technicians to control complex manufacturing processes through user-friendly interfaces. By using specialized programming languages like ladder logic and structured text, PLCs can efficiently manage equipment, monitor processes, and ensure precise control of industrial operations. Understanding PLC programming is essential for anyone looking to advance in the automation industry.
Table of Contents
What is PLC Programming and Why is it Important?
PLC programming forms the backbone of industrial automation systems. A programmable logic controller serves as an industrial computer that continuously monitors input values from various sensors and makes decisions based on a custom program to control outputs such as actuators, relays, and motors.The importance of PLC programming lies in its ability to:
- Automate complex manufacturing processes
- Reduce human error in operations
- Increase production efficiency
- Provide reliable control systems
- Enable real-time monitoring and adjustments
How to Choose the Right PLC Programming Language?
When it comes to PLC programming, several standard languages are available, each with its unique advantages:
Ladder Logic (LD)
- Most widely used language
- Based on relay logic diagrams
- Excellent for boolean operations
Structured Text (ST)
- Similar to Pascal and C
- Perfect for complex algorithms
- Supports advanced mathematical operations
Function Block Diagram (FBD)
- Graphical programming approach
- Ideal for process flow representation
- Easy to understand and troubleshoot
Essential Components of PLC Programming
The success of a PLC program depends on understanding its core components:
Input and Output Configuration
- Digital inputs from sensors
- Analog signals from process variables
- Output modules for actuator control
- HMI integration for operator interface
Program Structure
- Main routine
- Subroutines
- Interrupt handlers
- Data blocks
Advanced PLC Programming Techniques
Modern PLC programming has evolved to include sophisticated features:
- Sequential Function Charts (SFC)
- Perfect for step-by-step processes
- Clear visualization of program flow
- Easy maintenance and troubleshooting
- Integrated Safety Systems
- Emergency stop functions
- Safety interlocking
- Compliance with safety standards
Frequently Asked Questions
With dedicated study and practice, basic PLC programming can be learned in 3-6 months, while mastery may take 1-2 years of hands-on experience.
The industrial automation industry offers excellent career opportunities with competitive salaries and growing demand for skilled programmers.
Mitsubishi, Omron, and Schneider are popular choices for beginners due to their user-friendly programming environments and extensive support resources.
Yes, many manufacturers offer free simulation software for learning and testing programs without physical hardware.
Yes, our experts are available to guide you in selecting the perfect products tailored to your project’s unique requirements, ensuring optimal performance.
Power your projects with brand-new, original Omron, Mitsubishi, Schneider PLC – in stock, ready now!
Conclusion
• PLC programming is fundamental to industrial automation
• Multiple programming languages are available for different applications
• Understanding both hardware and software components is crucial
• Regular practice and continuous learning are essential for mastery
• Career opportunities in PLC programming continue to grow
• Safety considerations should always be prioritized
Looking for new, original PLCs for your projects? At Kwoco, we stock the latest PLCs from top brands like Omron, Mitsubishi, and Schneider. Shop with confidence—fast shipping, guaranteed quality! Buy Now
Contact Us
Just fill out your name, email address, and a brief description of your inquiry in this form. We will contact you within 24 hours.
You May Also Find These Topics Interesting
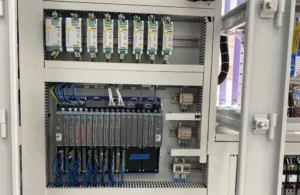
The Complete Guide to Programmable Logic Controllers (PLCs)
The Complete Guide to Programmable Logic Controllers (PLCs) In the fast-evolving world of industrial automation, Programmable Logic Controllers (PLCs) have
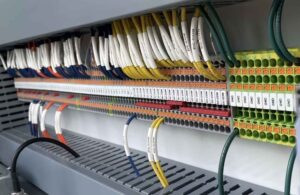
What is PLC Ladder Logic and How Does it Work?
Programmable Logic Controllers (PLCs) are the backbone of industrial automation, and ladder logic is the most popular programming language used to instruct these PLCs. This article delves into the basics of ladder logic, demystifying how it works and why it’s essential for anyone interested in PLC programming to understand. Whether you’re a seasoned engineer or new to automation, this guide will enhance your knowledge and skills.

Is Relay Output Digital or Analog? Understanding the Basics
Relays, though seemingly simple devices, play an essential role in both our daily lives and industrial applications. But the question often arises: Is the output of a relay analog or digital? This is particularly confusing for those new to industrial automation equipment.