Revolutionizing Industrial Automation with Advanced Photoelectric Sensor Types
Table of Contents
1. What are Photoelectric Sensors and Why are They Important in Industrial Automation?
As an expert in industrial automation, I’ve seen firsthand the transformative impact of photoelectric sensors. These devices are essential components in modern manufacturing, acting as the “eyes” of automated systems.
Photoelectric sensors detect the presence, absence, or distance of objects without physical contact by emitting a light beam and analyzing the light reflected back. Their ability to provide precise and reliable data makes them indispensable in a wide range of applications.
In the context of industrial automation, photoelectric sensors play a crucial role in enhancing efficiency, improving quality control, and ensuring safety.
By accurately detecting objects, these sensors enable automated systems to perform tasks such as counting, sorting, positioning, and inspecting products with remarkable speed and accuracy.
As the manufacturing world becomes increasingly automated, the demand for sophisticated sensing solutions like photoelectric sensors continues to grow. For example, a case study by Omron showed that implementing photoelectric sensors in a packaging line increased throughput by 20% while reducing errors by 15%.
2. How Do Photoelectric Sensors Work?
Photoelectric sensors operate on a simple yet effective principle. They consist of a light source (emitter) and a light-sensitive detector (receiver). The emitter sends out a beam of light, typically infrared or visible light, and the receiver measures the amount of light that is reflected back or interrupted by an object.
Depending on the sensor type, the way the emitted light interacts with the object and is processed by the receiver determines how the sensor detects the object’s presence, position, or other characteristics.
There are three primary methods that photoelectric sensors use to detect an object: thru-beam, diffuse, and retro-reflective. Thru-beam sensors use two separate housings – one for the emitter and one for the receiver – positioned opposite each other.
Diffuse sensors have the emitter and receiver in the same housing and rely on the light reflected off the object. Retro-reflective sensors also have the emitter and receiver in the same housing, but they use a reflector to bounce the light back to the receiver.
Each method has its advantages and is suited to different applications. For instance, diffuse mode is excellent for detecting objects with varying reflectivity, while thru-beam mode excels in detecting opaque objects.
3. What Are the Main Types of Photoelectric Sensors?
Understanding the various types of photoelectric sensors is crucial for selecting the right one for your specific application. Each type offers unique capabilities and is designed for different sensing scenarios. Here, we will delve deeper into each of the primary sensor types.
- Thru-beam sensors: These are considered to be the most reliable type of photoelectric sensor. They have the longest sensing ranges and are least affected by the properties of the object that is being detected. For instance, in the packaging industry, they are regularly used to detect the presence of boxes on a conveyor belt.
- Diffuse sensors: These are ideal for situations where only one side of the target object is accessible. They work exceptionally well with objects with a high reflectivity surface, such as metal or white paper. A typical application would be to detect parts in a bin.
- Retro-reflective sensors: These are excellent for detecting shiny or transparent objects. They offer longer sensing ranges than diffuse sensors but are less precise than thru-beam sensors. A common use case is detecting bottles on a conveyor line.
- Convergent beam mode sensors: Convergent beam mode sensors utilize a lens to focus the emitted light beam to a small point. This allows the sensor to detect small objects within a specific range precisely.
- Diffused mode with background suppression sensors: Diffused mode with background suppression sensors utilize triangulation to determine the distance to an object and ignore objects beyond a certain distance, making them ideal for detecting objects in front of a reflective background.
Here’s a table summarizing the main types of photoelectric sensors:
Sensor Type | Description | Advantages | Disadvantages | Typical Applications |
---|---|---|---|---|
Thru-beam | Uses two separate housings: emitter and receiver. | Longest sensing range, most reliable, unaffected by object surface/color. | Requires access to both sides of the target, more complex installation. | Object detection on conveyors, safety curtains |
Diffuse | Emitter and receiver in one housing. Detects light reflected off the target. | Simple installation, good for objects with varying reflectivity. | Shorter range than thru-beam, can be affected by object color/surface. | Part detection in bins, level detection |
Retro-reflective | Emitter and receiver in one housing. Uses a reflector. | Longer range than diffuse, good for shiny/transparent objects. | Less precise than thru-beam, can be affected by dust/dirt on the reflector. | Bottle detection, object detection on conveyors |
Background Suppression | Emitter and receiver in one housing, ignores objects beyond set distance. | Ignores background objects, good for precise distance detection. | Shorter range, can be affected by object surface/color. | Precise object detection in front of a background |
Fiber Optic | Uses fiber optic cables to guide light to and from the sensing area. | Ideal for small spaces, harsh environments, can detect small objects. | Shorter range than other types, more complex installation. | Detection in tight spaces, high-temperature environments |
4. What is Thru-beam Sensing Technology and How Does it Enhance Detection?
Thru-beam sensing technology, also known as through-beam or opposed mode, is a highly effective method for object detection in industrial environments.
This technique involves using two separate sensor units: an emitter and a receiver, placed opposite each other. The emitter projects a continuous light beam towards the receiver.
When an object passes between the emitter and the receiver, it interrupts the light beam, causing a change in the light intensity detected by the receiver. This change signals the presence of an object.
One of the key advantages of thru-beam sensors is their long sensing range. Because the emitter and receiver are separate and directly aligned, the light beam can travel a considerable distance without significant loss of intensity.
This makes through-beam sensors ideal for applications where a large sensing area needs to be covered, such as detecting large objects on a conveyor belt or monitoring the entry and exit points of a production line.
For example, a Mitsubishi PLC can be programmed to react based on signals from these sensors, providing integrated control solutions.
Furthermore, thru-beam sensors are known for their reliability. Since detection is based on the interruption of a light beam rather than the reflection of light, these sensors are less susceptible to variations in the object’s surface properties, such as color, texture, or reflectivity.
This makes them suitable for detecting a wide range of objects, including opaque, transparent, and even irregularly shaped items.
5. How Does Diffuse Sensing Technology Work in Object Detection?
Diffuse sensing technology, also known as proximity or reflective mode, is another widely used method in photoelectric sensors. Unlike thru-beam sensors, diffuse sensors house both the emitter and receiver within a single housing.
The emitter projects a light beam, and when an object enters the sensing area, it reflects a portion of this light back to the receiver. The sensor then detects the presence of the object based on the amount of light received.
Diffuse sensors are particularly useful when access to only one side of the target object is possible. They are also effective when the object’s position may vary within the sensing area.
However, the effectiveness of diffuse sensors can be influenced by the object’s surface properties. Objects with high reflectivity, such as shiny or light-colored surfaces, reflect more light and are therefore easier to detect. Conversely, dark or matte objects absorb more light and may be more challenging to detect.
There are variations within diffuse sensing technology. For example, convergent beam mode utilizes a focused light beam to improve the detection of small or transparent objects.
By concentrating the light into a narrow beam, this mode increases the light intensity at a specific distance, making it easier to sense objects with low reflectivity.
6. What is Retro-reflective Sensing Technology?
Retro-reflective sensing is a specialized form of reflective sensing that offers enhanced capabilities compared to standard diffuse sensing. In this configuration, the photoelectric sensor emits a light beam towards a special reflector placed opposite the sensor.
The reflector is designed to return the light directly back to the sensor along the same path. When an object breaks the light beam between the sensor and the reflector, the sensor detects a decrease in the amount of light received, indicating the presence of an object.
One of the primary advantages of retro-reflective sensors is their ability to detect transparent or translucent objects more reliably than diffuse sensors.
This is because even clear objects will cause some degree of light attenuation or scattering when they interrupt the beam.
By detecting these subtle changes in light intensity, retro-reflective sensors can effectively sense objects that might be missed by other types of sensors. A common application is the detection of clear bottles or plastic wrap on a conveyor.
Moreover, retro-reflective sensors generally offer a longer sensing range than diffuse sensors due to the efficient return of light from the reflector.
However, they are not as long-range as thru-beam sensors. It’s important to note that the performance of retro-reflective sensors can be affected by the alignment between the sensor and the reflector.
Proper installation and alignment are crucial for optimal operation. Additionally, dust, dirt, or other contaminants on the reflector or sensor lens can reduce the amount of light reflected back and potentially lead to false readings.
7. How Does Background Suppression Enhance Photoelectric Sensor Accuracy?
Background suppression is an advanced feature in some photoelectric sensors that significantly improves their accuracy, particularly in challenging environments.
This technology allows the sensor to ignore objects beyond a set distance, known as the cutoff distance, while reliably detecting objects within the desired sensing range.
There are two main types of background suppression:
Mechanical background suppression: This method uses a mechanical adjustment, such as a screw, to set the cutoff distance. The sensor is designed to only respond to reflected light that returns within a specific time window, corresponding to the set distance. Light reflected from objects beyond the cutoff distance arrives outside this window and is ignored.
Electronic background suppression: This more sophisticated method uses triangulation to determine the distance to the object. The sensor contains two receiving elements that detect the angle at which the reflected light returns. Based on this angle, the sensor calculates the distance to the object. If the calculated distance is beyond the set cutoff, the sensor ignores the object.
Background suppression is particularly useful when the background is reflective or when objects of varying colors or reflectivity need to be detected against a consistent background.
For example, in an application where boxes of different colors are moving along a conveyor with a shiny metal backdrop, a diffused mode with background suppression sensor can reliably detect the boxes while ignoring reflections from the conveyor.
If you want to incorporate background suppression into your operations, we offer specialized Schneider HMI panels that can be integrated with these advanced sensors.
8. What Are the Key Factors Affecting Photoelectric Sensor Performance?
Several factors can influence the performance and reliability of photoelectric sensors. Understanding these factors is essential for selecting the appropriate sensor for a given application and ensuring optimal operation.
Object Properties: The size, shape, color, surface texture, and reflectivity of the target object can significantly impact detection. For example, small, dark, or irregularly shaped objects can be more challenging to detect than large, light-colored, or regularly shaped ones. Similarly, objects with matte surfaces may be harder to sense with diffuse sensors compared to objects with shiny surfaces.
Environmental Conditions: Factors such as ambient light, temperature, humidity, dust, dirt, and chemical exposure can affect sensor performance. For instance, high levels of ambient light can interfere with the sensor’s ability to detect changes in light intensity. Similarly, extreme temperatures or exposure to moisture or chemicals can damage the sensor or degrade its performance over time. For instance, our range of Omron Sensors are designed to withstand harsh environmental conditions, ensuring reliable performance.
Sensing Distance: The distance between the sensor and the target object, as well as the overall sensing range of the sensor, are crucial considerations. Different types of sensors have varying sensing ranges. For example, thru-beam sensors typically have the longest range, while diffuse sensors have a shorter range. Selecting a sensor with an appropriate sensing range for the application is essential for reliable detection.
Alignment and Installation: Proper alignment and installation are critical for optimal sensor performance. Misalignment can lead to missed detections or false triggers. Additionally, ensuring that the sensor is securely mounted and protected from vibration or impact can help maintain its accuracy and longevity.
Response Time: The speed at which a sensor can detect an object and generate an output signal is known as its response time. In high-speed applications, such as counting objects on a fast-moving conveyor, a sensor with a fast response time is essential to keep up with the production rate.
9. What are the Typical Applications of Photoelectric Sensors in Various Industries?
Photoelectric sensors are incredibly versatile and find applications across a wide range of industries. Their ability to provide non-contact detection makes them invaluable in numerous automation processes. Here are some common examples:
Packaging Industry: In packaging, these sensors play a crucial role in ensuring that products are correctly positioned, counted, and packaged. For instance, thru-beam sensors can detect the presence of boxes on a conveyor belt, while retro-reflective sensors can verify the presence of labels or seals. Diffuse sensors can be used for level detection in hoppers or to detect the presence of items in a package.
Material Handling: Photoelectric sensors are essential components in automated material handling systems. They can be used to guide automated guided vehicles (AGVs), control the flow of materials on conveyors, and detect the position of pallets or other loads. For example, sensors can be used to ensure that an AGV stops at the correct location for loading or unloading.
Automotive Industry: In automotive manufacturing, photoelectric sensors are used extensively for part detection, positioning, and inspection. They can detect the presence of components on an assembly line, verify that parts are correctly oriented, and even inspect for defects. For instance, sensors can be used to ensure that a car door is properly aligned before it is welded into place.
Food and Beverage Industry: This industry utilizes photoelectric sensors for a variety of applications, including bottle detection, cap detection, fill-level detection, and label verification. For example, retro-reflective sensors can be used to detect the presence of clear bottles on a filling line, while diffuse sensors can ensure that containers are filled to the correct level. To complement these applications, we offer robust Proface HMI panels, ensuring seamless operation and monitoring of your production lines.
Pharmaceutical Industry: In pharmaceutical manufacturing, photoelectric sensors are used for precise object detection in processes such as counting pills, verifying the presence of vials or syringes, and inspecting packaging for defects. Their ability to provide accurate and reliable detection is critical in this highly regulated industry.
10. How to Choose the Right Photoelectric Sensor for Your Application?
Selecting the right photoelectric sensor requires careful consideration of several factors. Here’s a step-by-step approach to guide you through the process:
Determine the Sensing Method: Based on your application, decide whether thru-beam, diffuse, or retro-reflective sensing is most appropriate. Consider factors such as whether you have access to both sides of the target object, the object’s surface properties, and the required sensing range.
Consider Object Characteristics: Evaluate the size, shape, color, and reflectivity of the objects you need to detect. For instance, if you’re detecting small, transparent objects, a convergent beam or retro-reflective sensor might be suitable. For objects with varying colors or reflectivity, a diffuse sensor with background suppression could be a good choice.
Assess Environmental Conditions: Take into account the environment where the sensor will be operating. If there’s excessive dust, dirt, or moisture, choose a sensor with a suitable IP rating and robust housing. In areas with high ambient light, consider a sensor with good ambient light immunity or use shielding.
Determine the Required Sensing Range: Measure the distance between where the sensor will be mounted and where the objects will be detected. Select a sensor with a sensing range that comfortably covers this distance, keeping in mind that the specified sensing range is usually based on ideal conditions.
Evaluate Response Time: If your application involves high-speed detection, such as counting objects on a fast-moving conveyor, choose a sensor with a fast response time that can keep up with the required speed.
Consider Output Type: Photoelectric sensors offer various output types, such as NPN, PNP, relay, or analog outputs. Select an output type that is compatible with your control system or PLC. We provide compatibility with a wide range of control systems, including Omron PLC, to ensure seamless integration.
Mounting and Installation: Think about how the sensor will be mounted and installed. Some sensors offer more flexible mounting options than others. Ensure that the sensor can be securely mounted and easily aligned for optimal performance.
Special Features: Depending on your application, you might need a sensor with special features such as background suppression, foreground suppression, adjustable sensitivity, or built-in timers.
By systematically evaluating these factors, you can select the photoelectric sensor that best meets your needs, ensuring reliable and accurate detection in your specific application.
Frequently Asked Questions
A photoelectric sensor is a device that uses a light beam to detect the presence, absence, or distance of an object without physical contact.
A thru-beam sensor uses two separate units, an emitter and a receiver, placed opposite each other. The emitter sends a light beam to the receiver, and when an object interrupts the beam, the sensor detects its presence.
Diffuse sensors detect light reflected off the target object, while retro-reflective sensors detect light reflected back from a reflector. Retro-reflective sensors are generally better for detecting transparent or shiny objects.
Background suppression is a feature that allows a photoelectric sensor to ignore objects beyond a set distance, making it more accurate in environments with reflective backgrounds.
Yes, certain types of photoelectric sensors, such as retro-reflective and some specialized diffuse sensors, can reliably detect transparent objects.
Power your projects with brand-new, original Omron, Keyence, Schneider Sensors – in stock, ready now!
Conclusion
- Photoelectric sensors are essential components in modern industrial automation, providing non-contact detection of objects.
- The main types of photoelectric sensors are thru-beam, diffuse, and retro-reflective, each with unique advantages and applications.
- Thru-beam sensors offer long range and high reliability, diffuse sensors are versatile and easy to install, and retro-reflective sensors are good for detecting transparent objects.
- Background suppression enhances sensor accuracy by ignoring objects beyond a set distance.
- Factors such as object properties, environmental conditions, sensing range, response time, and output type should be considered when choosing a photoelectric sensor.
- Photoelectric sensors are used across various industries, including packaging, material handling, automotive, food and beverage, and pharmaceuticals.
- Proper selection and installation of photoelectric sensors are crucial for optimal performance and reliable detection.
- For complex automation needs, integrating sensors with advanced systems like Servo drives can significantly enhance operational efficiency.
By understanding the principles, types, and applications of photoelectric sensors, you can leverage this technology to enhance your automation processes, improve efficiency, and ensure precision in your operations.
Contact Us
Just fill out your name, email address, and a brief description of your inquiry in this form. We will contact you within 24 hours.
You May Also Find These Topics Interesting
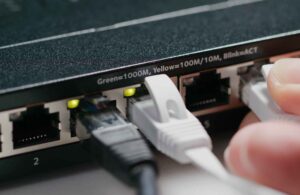
What is Ethernet/IP? Understanding the Industrial Protocol
In today’s rapidly evolving industrial landscape, understanding EtherNet/IP (Industrial Protocol) is crucial for anyone involved in industrial automation and IIoT implementations.
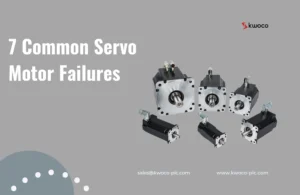
7 Common Servo Motor Failures
7 Common Servo Motor Failures As a seasoned engineer with extensive experience in industrial automation, I’ve seen my fair share
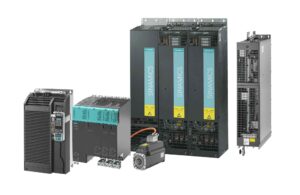
SINAMICS S120 Faults: A Troubleshooting Guide
This article serves as a detailed guide to understanding and resolving SINAMICS S120 fault codes. Whether you’re an experienced engineer or new to industrial automation, this resource provides invaluable insights into the intricacies of SINAMICS S120 drives, helping you diagnose and troubleshoot faults efficiently. With a focus on practical solutions, we aim to equip you with the knowledge necessary to minimize downtime and optimize the performance of your machinery.