Inductive Sensors: Demystifying the Working Principle of Inductive Proximity Sensors
Table of Contents
What is an Inductive Sensor?
An inductive sensor is a device that uses electromagnetic induction to detect the presence of metallic objects without physical contact. These sensors are widely used in industrial environments to monitor the position, presence, or absence of objects, and are essential components in automation systems.
They are known for their robustness, reliability, and ability to operate in wet or dirty conditions.
In the context of industrial automation, inductive sensors play a crucial role in ensuring the smooth operation of machinery and equipment. For instance, in a manufacturing plant, these sensors can be used to detect the position of a robotic arm, ensuring it moves to the correct location to perform its task.
Moreover, in product manufacturing, inductive sensors can help verify the presence of metallic components in a product, ensuring quality control. They are the silent workhorses of modern industry, constantly monitoring and providing feedback to control systems, ensuring precision and efficiency.
How Do Inductive Sensors Work?
The working principle of an inductive proximity sensor revolves around the concept of electromagnetic induction. The sensor contains a coil of wire wound around a ferrite core, which generates a magnetic field when an alternating electric current flows through it.
When a metal object enters the magnetic field, it disrupts the field, causing eddy currents to be induced in the metal target.
These eddy currents create their own magnetic field, which opposes the sensor’s field. This interaction leads to a change in the oscillation amplitude of the oscillator within the sensor, which is detected by the sensor’s internal circuit.
This change in oscillation indicates the presence of a metal object. The sensor then generates an output signal, which can be used to trigger an action or provide feedback to a control system. For example, if you want to know more about the different types of PLCs, you can check out our page on PLC.
Here’s a table summarizing the key steps in the operation of an inductive sensor:
Step | Description |
---|---|
1 | The sensor creates an electromagnetic field using an oscillator and a coil. |
2 | A metallic object enters the electromagnetic field. |
3 | Eddy currents are induced in the metallic object, creating an opposing magnetic field. |
4 | The oscillator detects a change in the oscillation amplitude due to the interaction of the magnetic fields. |
5 | The sensor’s internal circuit processes the change in oscillation and generates an output signal, indicating the presence of the metallic object. |
What are the Different Types of Inductive Sensors?
There are primarily two types of inductive sensors: analog and digital (or switching) sensors. Analog inductive sensors provide a continuous output signal that varies proportionally with the distance between the sensor and the metal object.
This makes them ideal for applications where precise distance measurement is required.
Digital or switching inductive sensors, on the other hand, have a fixed sensing range and provide a binary output that changes state when a metal object is detected within that range.
They are commonly used as proximity switches to detect the presence or absence of an object. When choosing between analog and digital, it’s important to understand that analog will cost more but provide more detailed feedback. For more information on industrial automation components, check out our product offerings on Mitsubishi Servo.
What is the Sensing Range of an Inductive Sensor?
The sensing range of an inductive sensor, also known as the operating distance, is the maximum distance at which the sensor can reliably detect a metal object.
This distance is influenced by several factors, including the size and material of the metal target, the size and shape of the sensor coil, and the sensor’s operating frequency.
It’s important to note that the type of metal being detected also affects the sensing range. For instance, ferromagnetic materials like iron have a higher correction factor compared to non-ferromagnetic materials like aluminum.
This means that an inductive sensor will generally have a longer sensing range for iron objects than for aluminum objects of the same size. Factor 1 sensors are a special type of inductive sensor that have the same sensing range for all types of metal.
The correction factor is a multiplier that must be applied to the rated operating distance to determine the actual operating distance for a specific type of metal. The operating distance is the maximum distance at which the sensor can reliably detect the target.
What are Inductive Sensors Used For?
Inductive sensors are used to detect metallic objects in a wide range of industrial applications. They are commonly employed to detect the position of machine parts, the presence of metal components in a product, or the passage of objects on a conveyor belt.
Moreover, inductive sensors can also be used for speed sensing, counting, and even for detecting the presence of specific types of metals. Their ability to operate without physical contact makes them ideal for use in harsh environments where other types of sensors might fail.
They provide accurate and timely feedback to control systems, helping to prevent errors and improve productivity. It is important to understand that inductive sensors will also detect a thin foil of aluminum or copper and not just a solid piece of metal.
How Do Analog Inductive Sensors Differ from Digital Inductive Sensors?
As mentioned earlier, analog inductive sensors provide a continuous analog signal that is proportional to the distance between the sensor and the metallic object.
This output signal can be a current or a voltage signal, depending on the specific design of the sensor. Analog sensors are typically used in applications where precise distance measurements are required.
Digital or switching inductive sensors, on the other hand, have a fixed sensing distance and provide a binary output that changes state when a metallic object is detected within that distance.
These sensors are often used as proximity switches to indicate the presence or absence of an object. For instance, in a manufacturing plant, a digital inductive sensor might be used to detect when a product has reached a specific point on a conveyor belt, triggering a robotic arm to perform an operation on the product.
If you’re interested in learning more about sensor applications, our page on Omron offers additional insights.
What are Some Common Applications of Inductive Sensors?
Applications of inductive sensors are diverse and span across various industries. In the automotive industry, they are used to detect the position of gears, shafts, and other metallic components in engines and transmissions.
In the metalworking industry, they are used to monitor the position of cutting tools and workpieces.
In the packaging industry, inductive sensors are used to detect the presence of products on conveyor belts and to ensure that containers are properly filled. They are also used in robotics, material handling, and many other fields where the detection of metallic objects is required.
As a company specializing in industrial automation, we have seen firsthand how inductive sensors can improve the efficiency and reliability of manufacturing processes.
Can Inductive Sensors Detect Non-Metallic Objects?
No, inductive sensors are specifically designed to detect metallic objects. They rely on the principle of electromagnetic induction, which requires the target object to be conductive.
Non-metallic materials like plastic, wood, or glass do not conduct electricity and therefore cannot be detected by inductive sensors.
For the detection of non-metallic objects, other types of sensors such as capacitive sensors or photoelectric sensors are used.
Capacitive sensors detect changes in capacitance caused by the presence of an object, while photoelectric sensors use light to detect objects.
What are the Advantages of Using Inductive Sensors?
Inductive sensors offer several advantages over other types of sensors. They are robust, reliable, and can operate in wet or dirty conditions. They are also resistant to vibration, shock, and extreme temperatures.
Moreover, because they operate without physical contact, inductive sensors have a long service life and require minimal maintenance. They are also relatively inexpensive compared to other sensing technologies.
Here is an example of an inductive sensor being used in a real-world application: A company that manufactures automotive parts uses inductive sensors to detect the presence of metal components in their products. The sensors are mounted on the assembly line and are used to trigger a robotic arm to perform a welding operation.
The use of inductive sensors has helped the company to improve the quality of their products and increase their production efficiency.
How to Choose the Right Inductive Sensor for Your Specific Application?
Choosing the right inductive sensor for a specific application depends on several factors. These include the type of metal being detected, the required sensing range, the operating environment, and the desired output type (analog or digital).
It’s also important to consider the sensor’s size, shape, and mounting options. Some sensors are designed for flush mounting, while others are designed for non-flush mounting.
The choice between these two types depends on the specific requirements of the application. You might also want to consider our selection of Omron HMI products for your industrial automation needs.
Frequently Asked Questions
An inductive sensor operates on the principle of electromagnetic induction. It generates an electromagnetic field, and when a metallic object enters this field, eddy currents are induced in the object. These currents create an opposing magnetic field, which the sensor detects, indicating the presence of the object.
Inductive sensors can detect any type of conductive metal. The sensing range may vary depending on the type of metal due to differences in conductivity and magnetic properties.
Yes, inductive sensors are known for their robustness and can operate reliably in harsh environments, including wet or dirty conditions. They are resistant to vibration, shock, and extreme temperatures. They are generally not affected by non-metallic contaminants such as oil, dirt, or moisture.
Analog inductive sensors provide a continuous output signal that varies proportionally with the distance to the metal target. Digital inductive sensors provide a binary output that switches state when a metal target is within a fixed sensing range.
The correction factor is a multiplier applied to the sensor’s rated operating distance to determine the actual operating distance for a specific type of metal. Different metals have different correction factors due to their varying conductivity and magnetic properties.
Power your projects with brand-new, original Omron, Mitsubishi, Schneider PLC – in stock, ready now!
Conclusion
- Inductive sensors are essential components in industrial automation, used to detect the presence of metallic objects without physical contact.
- They operate on the principle of electromagnetic induction, generating a magnetic field and detecting changes caused by the presence of metal objects.
- There are two main types: analog and digital, each suited for different applications.
- The sensing range depends on factors like the type of metal, sensor size, and operating frequency.
- Inductive sensors are robust, reliable, and can operate in harsh environments.
- Choosing the right sensor involves considering factors like the type of metal, required sensing range, operating environment, and output type.
I hope this comprehensive guide has provided valuable insights into the world of inductive sensors. If you have any further questions about inductive sensors, please don’t hesitate to contact us. We’re always here to help you find the best solutions for your industrial automation needs.
Contact Us
Just fill out your name, email address, and a brief description of your inquiry in this form. We will contact you within 24 hours.
You May Also Find These Topics Interesting
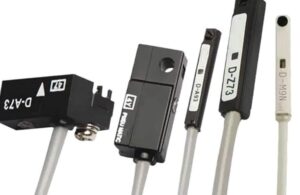
Demystifying Magnetic Switches: A Comprehensive Guide for Industrial Applications
This article provides an in-depth look at magnetic switches, exploring their function, benefits, and applications, particularly within industrial settings. Whether you’re a seasoned engineer or new to the world of industrial automation, this guide will equip you with a thorough understanding of how magnetic switches can enhance your operations. We aim to demystify these devices and showcase why they are a critical component in modern manufacturing and automation systems.
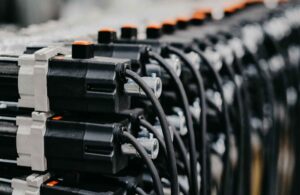
What is The Purpose of a Servo Motor?
Servo motors have become indispensable in modern industrial applications, offering unparalleled precision and control. Whether it’s in robotics, automation, or any system requiring exact movements, servo motors are at the heart of it all. In this article, we’ll explore the purpose of servo motors, their types, and why they are crucial in various industries today.

Introduction to Programmable Logic Controllers: Your Gateway to Industrial Automation
This article is a comprehensive guide to Programmable Logic Controllers (PLCs), exploring their fundamental role in modern industrial automation. From machinery and equipment factories to manufacturers and solution providers, PLCs are indispensable for streamlining operations and enhancing productivity. This article delves into the intricacies of PLCs, their programming, and their diverse applications.