How to Solve PLC Communication Problems
- kwoco-plc.com
- June 25, 2024
- 3:24 am
Programmable Logic Controllers (PLCs) are the backbone of modern industrial automation. They are specialized computers designed to manage and control manufacturing processes, machinery, and other industrial equipment.
From assembly lines to complex machinery operations, PLCs ensure everything runs smoothly, efficiently, and safely.
Imagine the chaos if your industrial processes suddenly stopped or malfunctioned. Reliable communication between PLCs and other components is crucial to avoid such scenarios.
Table of Contents
Effective PLC communication ensures that all parts of your automated system are synchronized, data is accurately transmitted, and operations proceed without hiccups.
When communication issues arise, they can disrupt production, leading to downtime, increased costs, and potential safety hazards.
Introduction
The purpose of this article is to guide you through solving common PLC communication problems.
Whether you’re facing connectivity issues, data loss, or synchronization problems, we aim to provide practical solutions to help you maintain seamless industrial operations.
How Do You Communicate with PLC?
Effective communication with Programmable Logic Controllers (PLCs) can be achieved through both direct and remote methods, each suited to specific needs and setups.
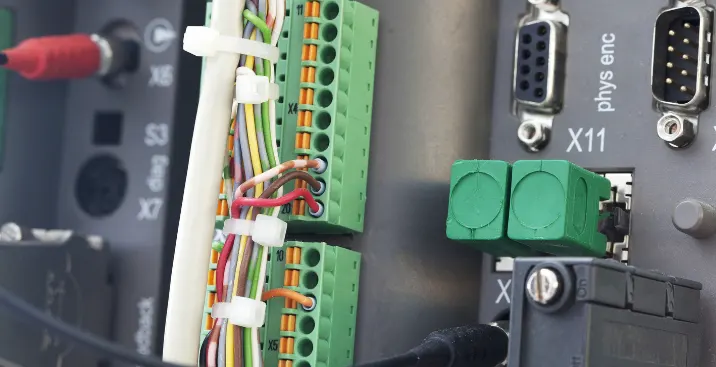
Direct Communication
Human-Machine Interface (HMI) Screens: One of the most user-friendly ways to interact with PLCs is through HMI screens. These interfaces provide real-time data visualization, control options, and diagnostic information, making it easier for operators to monitor and manage processes directly.
Programming Software Interfaces: PLCs are often programmed and configured using specialized software interfaces. These tools, such as Siemens’ TIA Portal, Mitsubishi’s GX Works, and Allen Bradley’s RSLogix 5000, allow engineers to write, test, and upload control logic directly to the PLC, ensuring precise control over industrial processes.
Remote Communication
Network Ethernet Switches and Cables: For remote communication, PLCs are typically connected through network ethernet switches and cables. This setup enables PLCs to exchange data with other devices and systems over a local area network (LAN), facilitating seamless integration and coordination across the entire automation system.
Wireless Communication Methods: In situations where cabling is impractical, wireless communication methods come into play. Technologies like Wi-Fi and industrial wireless standards provide flexibility and mobility, allowing PLCs to communicate over a wireless network without the constraints of physical wiring.
Common Solutions to PLC Communication Problems
Addressing communication problems in PLC systems is critical to maintaining seamless industrial automation operations. Below are essential steps and best practices to troubleshoot and resolve these issues effectively.
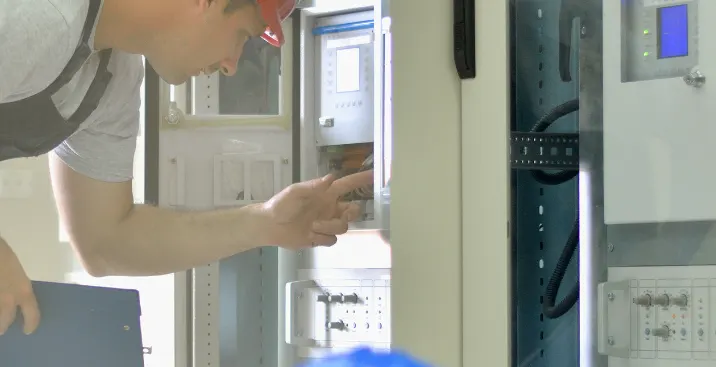
Inspect Ethernet Cables and Network Ethernet Switches: Begin by thoroughly examining all physical connections. Inspect ethernet cables for any signs of wear, fraying, or damage that could impair data transmission. Similarly, check network ethernet switches to ensure they are functioning correctly and that all ports are operational. Proper cable management and the use of high-quality, shielded cables can significantly reduce communication errors.
Ensure Proper Connections and Check for Any Damage: Verify that all connections are secure and correctly placed. Loose or improperly connected cables can cause intermittent communication failures. Regularly check connectors and ports for any physical damage or corrosion, which might compromise the integrity of the communication link.
Correct PLC Code and Configuration Settings: Software configuration plays a crucial role in PLC communication. Ensure that the PLC code is error-free and that configuration settings are correctly applied. This includes verifying IP addresses, subnet masks, gateways, and other network parameters. Incorrect settings can lead to communication breakdowns and system malfunctions.
Ensure Compatibility Between PLC Products and Communication Protocols: Compatibility issues between different PLC products (uch as Siemens PLC controllers, Mitsubishi PLCs, and Allen Bradleys) and communication protocols can also cause problems. Ensure that all devices on the network are configured to use compatible protocols and that they can communicate effectively. Updating firmware and software to the latest versions can help resolve many compatibility issues.
Network Traffic and Interference:High network traffic or interference can disrupt PLC communications. Use network analyzers to check for excessive traffic or noise on the network. Implementing network segmentation and proper shielding can help mitigate these issues.
Environmental Factors:Environmental factors such as extreme temperatures, humidity, or electromagnetic interference can affect PLC communication. Ensure that your PLC and networking equipment are operating within the recommended environmental conditions.
Regular Maintenance
Routine Checks and Updates for Automation Equipment: Regular maintenance is vital for preventing communication problems. Conduct routine checks on all automation equipment, including PLCs, network switches, and cables. Look for signs of wear or potential issues that could escalate into significant problems if left unaddressed.
Preventive Measures for Avoiding PLC Industrial Automation Failures: Implement preventive maintenance measures to avoid future communication failures. This includes scheduled inspections, cleaning of equipment, and timely replacement of worn components. Keeping a log of maintenance activities and adhering to a strict maintenance schedule can help in early detection and resolution of potential issues.
By systematically addressing these common communication problems, you can enhance the reliability and efficiency of your PLC systems, ensuring uninterrupted industrial automation and optimal performance.
Advanced Troubleshooting Tips
For more complex PLC communication issues, advanced troubleshooting techniques can be employed to identify and resolve problems effectively.
Use Diagnostic Tools
Software Tools for Diagnosing PLC Communication Issues: Utilizing specialized diagnostic software can significantly aid in identifying and troubleshooting communication issues. These tools provide detailed insights into network performance, communication logs, and error messages, helping you pinpoint the exact cause of the problem. Many of these diagnostic tools are designed to be compatible with various PLC brands, including Siemens, Mitsubishi, and Allen Bradley.
Tools Compatible with Siemens PLC Controllers and Other Brands: Ensure the diagnostic tools you use are compatible with the specific PLC controllers in your setup. For instance, Siemens offers a range of diagnostic software that integrates seamlessly with their PLC systems, providing real-time data and comprehensive error reporting. Similarly, other brands have their diagnostic solutions tailored to their products, facilitating efficient troubleshooting.
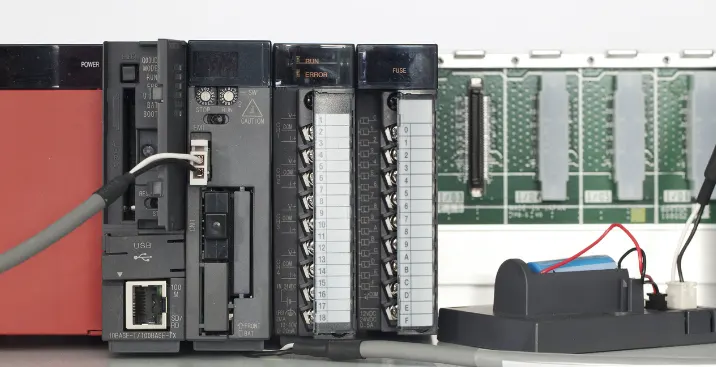
Consult Manufacturer Guidelines
Refer to Manuals and Support from Brands Like Omron, Mitsubishi, and Schneider: Manufacturer guidelines and manuals are invaluable resources for resolving PLC communication issues. They contain detailed instructions, troubleshooting steps, and technical specifications that can guide you through the process. Brands like Omron, Mitsubishi, and Schneider provide extensive documentation and support services, including online resources and technical support teams, to assist with complex issues.
Network Analysis
Monitoring and Analyzing Network Traffic Using Tools for Ethernet Cable Connections: Network analysis tools are essential for monitoring and diagnosing issues within the communication network. These tools allow you to capture and analyze network traffic, identify bottlenecks, and detect anomalies that may be affecting communication. By using network analyzers, you can gain a deeper understanding of the data flow and pinpoint any disruptions or inefficiencies in the ethernet cable connections.
By leveraging these advanced troubleshooting tips, you can address even the most challenging PLC communication problems, ensuring robust and reliable industrial automation systems. Regular use of diagnostic tools, adherence to manufacturer guidelines, and thorough network analysis will help maintain optimal performance and prevent future issues.
What are the 4 PLC Communication Protocols?
Understanding the different PLC communication protocols is essential for ensuring seamless integration and operation within industrial automation systems. Here are four widely-used protocols:
Ethernet/IP
Description and Use in Industrial Automation: Ethernet/IP (Ethernet Industrial Protocol) is a robust and versatile protocol widely adopted in industrial automation. It leverages standard Ethernet technology to facilitate real-time control and information exchange across various devices and systems.
Compatibility with Various PLC Products: Ethernet/IP is compatible with a broad range of PLC products, making it a preferred choice for manufacturers and integrators. It supports seamless communication between PLCs, HMIs, and other automation equipment, ensuring efficient and reliable data transfer.
Modbus
Overview and Advantages: Modbus is a simple, yet powerful communication protocol that allows multiple devices to communicate over a network. Its ease of use and flexibility make it a popular choice in many industrial applications.
Commonly Used with Schneider and Siemens PLC Controllers: Modbus is commonly implemented with Schneider and Siemens PLC controllers. Its widespread adoption and straightforward implementation make it ideal for various automation scenarios, from basic to complex systems.
Profibus
Key Features and Benefits: Profibus (Process Field Bus) is an anti-interference communication protocol that is mainly used in automated industrial control systems. It is an industrial field bus system that realizes real-time data transmission with a data communication speed of 12 MBps.The Profibus protocol is commonly used for communication between various industrial control devices and for communication with sensors, actuators or other field devices.
Integration with Siemens PLCs and Other Automation Controls: Both Profibus and Profinet integrate seamlessly with Siemens PLCs and other automation controls. Their ability to support high-speed communication and large-scale automation systems makes them invaluable in complex industrial setups.
DeviceNet
Applications and Use Cases: DeviceNet is a robust protocol designed for industrial device-level communication. It allows various devices to communicate over a common network, streamlining control and data acquisition processes.
Supported Brands Like Allen Bradleys and Mitsubishi PLCs: DeviceNet is supported by leading PLC brands such as Allen Bradley and Mitsubishi. Its reliable performance and widespread support make it a versatile choice for numerous industrial applications, from simple device control to comprehensive automation systems.
By understanding these four PLC communication protocols, you can better select and implement the appropriate solutions for your industrial automation needs, ensuring efficient and reliable system performance.
Conclusion
Addressing PLC communication problems is crucial for maintaining efficient and reliable industrial automation systems. By checking physical connections, verifying software configurations, and conducting regular maintenance, you can prevent and resolve common communication issues.
Advanced troubleshooting techniques, such as using diagnostic tools, consulting manufacturer guidelines, and performing network analysis, further enhance your ability to maintain optimal system performance.
Additionally, understanding key PLC communication protocols like Ethernet/IP, Modbus, Profibus/Profinet, and DeviceNet ensures seamless integration and operation across various industrial setups.
If you’re facing PLC communication challenges or looking to optimize your automation systems, don’t hesitate to reach out.
Our team of experts is ready to provide professional automated solutions tailored to your needs. Explore our range of high-quality, original automation parts from leading brands like Siemens, Mitsubishi, and Allen Bradley to ensure the best performance for your industrial applications.