Understanding HMI: Revolutionizing Your Manufacturing Interface
Table of Contents
1. What is an HMI (Human Machine Interface)?
The HMI stands for human machine interface. It’s the crucial interface that bridges the gap between humans and machines. Think of it as the dashboard for your industrial processes.
More formally, the hmi is a device or software application that allows operators to monitor and control industrial equipment and processes. It presents this data in a graphical and easily understandable format.
It is the user interface that allows users to visualize data from a PLC or other industrial control system.
Using the human-machine interface, operators can oversee real-time operations, adjust settings, and respond to alerts, ensuring optimal performance and progress.
In essence, an hmi serves as a control interface and visualization tool. It translates complex machine data into actionable information for the human operator.
This interface that is easy to interpret is what allows quick reaction times. HMIs are used to control and monitor various aspects of a production process, from temperature and pressure to speed and flow rate.
Through a graphical interface, operators can quickly grasp the state of the system and make informed decisions.
2. Why are HMIs Essential in Modern Manufacturing?
In today’s fast-paced manufacturing industry, efficiency and precision are paramount. HMIs are essential because they provide a clear and concise view of complex manufacturing processes.
They enable operators to monitor and control the system in real-time, minimizing downtime and maximizing output. Without an HMI, operators would have to rely on traditional methods, such as physical gauges and manual adjustments, which are prone to human error and can be time-consuming.
HMIs are also instrumental in data collection and analysis. They log real-time data that can be used to identify trends, optimize production process, and improve overall efficiency.
Imagine a manufacturing line where every machine is monitored through a central HMI screen. Operators can see instantly if a machine is underperforming, if there’s a bottleneck, or if any parameters are out of range.
This immediate feedback allows for proactive interventions, preventing costly breakdowns and ensuring smooth operations.
3. How Does an HMI Work with a PLC (Programmable Logic Controller)?
The HMI and the programmable logic controller (PLC) work hand-in-hand to automate industrial processes. The PLC acts as the “brain” of the operation, controlling the machinery based on pre-programmed logic.
The HMI, on the other hand, is the “face” of the system, providing the interface for operators to interact with the PLC.
The PLC sends data to the HMI in real-time, providing updates on various parameters. The HMI then presents this data in a graphical format that is easy for operators to understand.
For example, the HMI screen might display a graph of temperature over time, a bar chart showing production output, or an alarm indicating a fault condition. The operators to monitor and control and operate the machine. PLC systems are used in diverse industries.
HMI provides a means for the operator to send commands back to the PLC. For example, an operator might use the HMI to adjust the speed of a conveyor belt, change the temperature of a furnace, or start/stop a machine.
The HMI allows operators to input these commands, which are then transmitted to the PLC, which executes the changes. This seamless communication between the HMI and PLC is what used to control and monitor the entire industrial process efficiently.
Think about it – HMI becomes a window into the soul of your machines and processes. You can find relevant Omron PLC products for your system through this link: Omron PLC.
4. What are the Different Types of HMIs Available?
The world of HMIs offers a diverse range of options to suit various industrial needs. Here are a few common type of hmi:
- Panel HMIs: These are dedicated hardware and software devices with built-in screens and processors. They are often ruggedized for harsh industrial environments and offer a reliable, self-contained solution.
- PC-Based HMIs: These are software applications that run on standard personal computers. They offer greater flexibility and scalability but may require additional protection to withstand industrial conditions.
- Mobile HMIs: With the rise of mobile technology, mobile hmi are becoming increasingly popular. These hmis used to control and run on smartphones or tablets, allowing operators to monitor the systems from anywhere within the facility. This enables remote monitor and control, and improving reaction times.
The choice of HMI depends on factors such as the complexity of the application, the environment, and the budget. Regardless of the device or software application chosen, the goal remains the same: to provide a clear and intuitive interface for operators.
5. What are the Key Benefits of Implementing an HMI System?
Leveraging HMI in your industrial control system brings a multitude of benefits:
- Improved Efficiency: HMI enables real-time data visualization and control, allowing for faster response times and optimized production process.
- Reduced Downtime: By providing real-time alerts and diagnostics, hmis help to identify and resolve issues quickly, minimizing costly downtime.
- Enhanced Safety: HMIs can display critical safety information and allow operators to monitor and respond to potential hazards.
- Increased Productivity: By streamlining operations and reducing errors, hmis can significantly boost overall productivity.
- Better Data Analysis: HMIs log real-time data that can be analyzed to identify trends, optimize processes, and improve decision-making.
- Reduced Human Error: Automate tasks and clear user-friendly interface reduces the likelihood of human error.
- Remote accessibility: Mobile device and mobile hmis provide remote monitor and control functionalities.
The benefits of HMI extend beyond just the machine and the operator. They impact the entire organization, leading to improved profitability and competitiveness.
6. Where are HMIs Commonly Used?
HMIs are found in a wide range of industries, wherever there’s a need to monitor and control complex systems. Here are a few examples of uses hmi:
- Manufacturing: From automobile manufacturing industry and food processing to pharmaceuticals, hmis are used to monitor and control all aspects of the manufacturing process.
- Oil and Gas: HMIs are used to monitor pipelines, refineries, and offshore platforms, ensuring safe and efficient operations.
- Water and Wastewater Treatment: HMIs are used to monitor and control water levels, pump speeds, and chemical dosages, ensuring clean and safe water supplies.
- Building Automation: Building automation system utilizes HMIs to monitor and control lighting, HVAC, and security systems.
- Healthcare: In the medical field, hmis are used to monitor patient data in real-time, and monitor and control medical devices.
The versatility of HMIs makes them an indispensable tool in any industry that relies on automation systems.
7. What are the Advanced Features of Modern HMIs?
Advanced hmi are constantly evolving to meet the demands of modern industries. Some key features include:
- Remote Access: HMI software often allows remote access via web browsers or mobile device, enabling operators to monitor and control systems from anywhere with an internet connection.
- Data Logging and Analysis: Advanced HMIs can log vast amounts of real-time data and provide tools for analyzing this data to identify trends and optimize processes.
- Alarm Management: HMIs provide sophisticated alarm management systems that can prioritize alarms, notify operators, and track alarm history.
- Recipe Management: For industries that require frequent product changes, hmis can store and manage recipes, allowing for quick and easy changeovers.
- Connectivity: Modern hmis can connect to a wide range of devices and systems, including PLCs, sensors, databases, and enterprise resource planning (ERP) systems.
- Improved data management: Modern HMIs are designed for better improved data management.
- Improving system security: They are also built for improving system security.
These developments in hmi technology are empowering manufacturers to achieve greater levels of efficiency, productivity, and safety. If you are looking for an HMI solution, check out Proface HMI.
8. How Do You Choose the Right HMI for Your Application?
Selecting the right HMI is crucial for maximizing its benefits. Here are some factors to consider:
- Application Requirements: What are the specific monitor and control needs of your application? How many data points need to be displayed? What level of control is required?
- Environment: Will the HMI be exposed to harsh conditions such as extreme temperatures, dust, or moisture? Choose an HMI that is ruggedized for the environment.
- Connectivity: Does the HMI need to connect to specific PLCs, sensors, or other devices? Ensure that the HMI supports the necessary communication protocols.
- User Interface: Is the user interface intuitive and easy to use? Consider the skill level of the operators who will be using the HMI.
- Budget: HMIs range in price from a few hundred dollars to several thousand dollars. Set a budget and choose an HMI that meets your needs without breaking the bank.
- Scalability: Will your needs change in the future? Choose an HMI that can be easily scaled up or down to accommodate future growth.
Consulting with an system integrators or interface software vendor can help you choose the best HMI for your specific needs.
9. What is the Future of HMI Technology?
The future of hmi is bright, with developments in hmi technology promising to revolutionizes industrial automation even further. Some key trends include:
- Increased Use of Augmented Reality (AR): AR will overlay digital information onto the real world, providing operators with even more intuitive and contextualized data.
- More Sophisticated Data Analytics: HMIs will incorporate more advanced data analytics tools, allowing for predictive maintenance, optimized processes, and improved decision-making.
- Greater Integration with the Industrial Internet of Things (IIoT): HMIs will become seamlessly integrated with the IIoT, enabling real-time data sharing and control across the entire enterprise.
- Enhanced Security: With the increasing threat of cyberattacks, HMIs will incorporate more robust security features to protect against unauthorized access and data breaches.
- Cloud-Based HMIs: Cloud-based hmis will offer greater scalability, flexibility, and accessibility, allowing operators to monitor and control systems from anywhere in the world.
These advancements will empower manufacturers to achieve unprecedented levels of efficiency, productivity, and safety.
10. What are Common Challenges When Implementing an HMI and How to Overcome Them?
Even with the numerous benefits, implementing an HMI can present some challenges:
- Integration Issues: Integrating the HMI with existing PLC systems and other devices can be complex. System integrators can assist in ensuring seamless interface and data transfer.
- Operator Training: Operators need to be properly trained on how to use the HMI effectively. Comprehensive training programs are essential for maximizing the benefits of HMI.
- Security Concerns: HMIs can be vulnerable to cyberattacks if not properly secured. Implementing robust security measures, such as firewalls and access controls, is crucial.
- Data Overload: HMIs can generate a vast amount of data, which can be overwhelming for operators. Carefully designing the user interface to prioritize critical information is essential.
- Cost: The initial cost of implementing an HMI can be a barrier for some companies. However, the long-term benefits of HMI, such as improved efficiency and reduced downtime, often outweigh the initial investment.
By anticipating these challenges and taking proactive steps to address them, you can ensure a successful HMI implementation.
Frequently Asked Questions
It stands for human machine interface and is the interface between the process and machine level for the operator to be able to visualize what is happening.
By providing real-time data and a control interface, hmis allow operators to monitor the performance and progress of the systems.
Yes, many modern hmis offer remote access capabilities, allowing operators to monitor and control systems from anywhere with an internet connection.
HMIs are commonly used in manufacturing, oil and gas, water treatment, building automation, and healthcare, among others.
Consider your specific application requirements, the environment, connectivity needs, user interface preferences, and budget.
Power your projects with brand-new, original Omron, Mitsubishi, Schneider HMI – in stock, ready now!
Conclusion
- HMIs are crucial interfaces that bridge the gap between humans and machines in industrial environments.
- They provide real-time data visualization and control, improving efficiency and reducing downtime.
- HMIs are used in a wide range of industries, from manufacturing to healthcare.
- Choosing the right HMI requires careful consideration of application requirements, environment, and budget.
- The future of HMI technology promises even greater integration with the Industrial Internet of Things and augmented reality.
Consider integrating Mitsubishi HMI into your system for a comprehensive interface solution: Mitsubishi HMI. You can also explore Schneider HMI options for robust and reliable interface: Schneider HMI.
Contact Us
Just fill out your name, email address, and a brief description of your inquiry in this form. We will contact you within 24 hours.
You May Also Find These Topics Interesting

Siemens vs. Omron PLC: Which One Is Right for Your Project?
When choosing a PLC, I often get asked, “Which one is better: Siemens or Omron?” It’s a complex question. As an engineer at Kwoco, my advice is that selecting a PLC isn’t about which brand is better, but which one fits your specific needs.
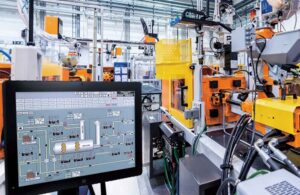
Do Touch Screens Work? Understanding the Technology Behind Touch Input
Touch screens have become an integral part of our daily lives, from smartphones to industrial control panels. But have you ever stopped to wonder how these touchscreens actually work? This article dives deep into the technology behind touch screens, exploring different types, their applications in industrial automation, and what makes them tick. Understanding the intricacies of touchscreen technology will equip you to make informed decisions about implementing them in your machinery and equipment factory, or factory solution company. We’ll explore the common challenges and how you, as a manufacturer, can leverage this tech to improve your processes.
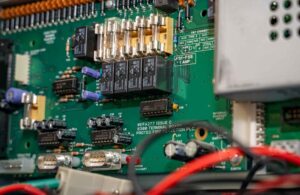
Understanding Sinking vs. Sourcing in PLC Systems
In programmable logic controllers (PLCs), the terms “sinking” and “sourcing” play a critical role in defining the flow of current in digital input and output modules. While the concept may initially seem technical, it is rooted in basic electrical principles and is key to designing efficient and functional PLC systems.