Mastering PLC Panels: A Guide to Reading Wiring Diagrams
Understanding what a PLC is and how it functions is essential for effectively diagnosing failures.
Table of Contents
Why Do PLCs Fail?
PLC failures can occur due to various factors, including hardware malfunctions, software issues, and external influences.
Recognizing the common reasons for PLC failures is crucial for maintaining system integrity and minimizing downtime. By delving into these causes, engineers can develop effective troubleshooting strategies.
Common Causes of PLC Failures
- Power Supply Issues: Insufficient power or fluctuations can lead to operational failures.
- Electrical Noise: Interference from nearby equipment can disrupt PLC signals.
- Module Failures: Individual components within the PLC can fail due to wear or damage.
- Configuration Errors: Incorrect settings can cause the PLC to malfunction or operate unpredictably.
- Environmental Factors: Temperature extremes, humidity, and dust can adversely affect PLC performance.
Power Supply Issues: A Major Concern
Power supply failures are one of the most common causes of PLC failures. When a PLC does not receive adequate power, it may reset unexpectedly or operate erratically.
Symptoms of power-related issues include frequent resets and alarms. Regularly checking power supply connections and using uninterruptible power supplies (UPS) can mitigate these risks.
Electrical Noise and Its Effects
Electrical noise, which can be caused by nearby machinery, radio frequency interference, or grounding issues, can lead to PLC malfunctions. Symptoms include erratic outputs and unexpected behavior in the control system.
Implementing proper grounding techniques and using shielded cables can help reduce electrical noise and its impact on PLC operations.
Module Failures: What to Look For
Modules within a PLC, such as input/output (I/O) or communication modules, can fail due to various factors. Common symptoms of module failures include loss of communication and failure to respond to inputs.
Conducting regular inspections and utilizing diagnostic tools like multimeters can aid in identifying module-related issues before they lead to significant problems.
Configuration Errors: A Silent Killer
Configuration errors, often overlooked, can cause substantial problems within PLC systems. These mistakes may arise from incorrect programming or settings within the PLC software.
Regularly reviewing the PLC configuration and utilizing version control can prevent issues stemming from misconfigurations.
Environmental Factors: Don’t Overlook Them
Industrial environments can be challenging for PLCs, with temperature fluctuations, humidity, and dust posing risks to system reliability.
Protecting PLCs with enclosures, ensuring proper ventilation, and conducting environmental assessments are essential steps to mitigate these risks.
The Role of Regular Maintenance
Regular maintenance is vital for preventing PLC failures. Key tasks include:
- Inspecting connections: Ensuring all connections are secure can prevent intermittent failures.
- Cleaning: Keeping the PLC and its surroundings clean helps reduce environmental impacts.
- Updating firmware: Regular updates can improve performance and fix known issues.
FAQs About PLC Failures
What are the most common symptoms of a PLC failure?
The most common symptoms of a PLC failure include erratic or unexpected outputs, failure to respond to inputs, frequent system resets, communication errors with connected devices, and alarms indicating faults. Additionally, users may notice unusual behavior in automated processes, such as inconsistent operation or unexpected stops.
How can I prevent electrical noise from affecting my PLC?
To prevent electrical noise from affecting your PLC, consider implementing the following strategies:
- Use Shielded Cables: Utilize shielded twisted pair cables for signal transmission to reduce electromagnetic interference.
- Proper Grounding: Ensure that all equipment is properly grounded to minimize the effects of electrical noise.
- Keep Cables Away from Noise Sources: Route cables away from heavy machinery and high-voltage lines that may generate electrical noise.
- Install Filters: Use noise filters on power supply lines and signal lines to reduce noise interference.
What should I do if my PLC keeps resetting?
If your PLC keeps resetting, follow these steps:
- Check Power Supply: Ensure that the power supply is stable and providing the correct voltage. Fluctuations can cause resets.
- Inspect Connections: Look for loose or damaged connections, as these can disrupt power and signal integrity.
- Review Program Logic: Check for programming errors that may cause the PLC to reset unexpectedly.
- Examine Environmental Conditions: Ensure that the PLC is operating within its specified temperature and humidity ranges. Excessive heat or moisture can lead to failures.
How often should I perform maintenance on my PLC system?
Maintenance on your PLC system should be performed regularly, ideally every six months to a year, depending on the operating environment and usage. However, certain factors, such as dust accumulation, temperature extremes, and frequency of use, may necessitate more frequent inspections. Regular maintenance tasks should include checking connections, cleaning the system, and updating firmware to ensure optimal performance and reliability.
Power your projects with brand-new, original Omron, Mitsubishi, Schneider PLC – in stock, ready now!
Conclusion
In summary, understanding the common causes of PLC failures is crucial for maintaining operational efficiency in industrial automation. By addressing power supply issues, minimizing electrical noise, preventing module failures, and ensuring proper configuration, you can significantly reduce the risk of PLC failures.
Looking for new, original PLCs for your projects? At Kwoco, we stock the latest PLCs from top brands like Omron, Mitsubishi, and Schneider. Shop with confidence—fast shipping, guaranteed quality! Buy Now
Contact Us
Just fill out your name, email address, and a brief description of your inquiry in this form. We will contact you within 24 hours.
You May Also Find These Topics Interesting
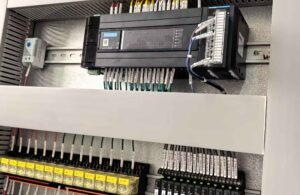
PLC vs VFD: Understanding Programmable Logic Controllers and Variable Frequency Drives
This article delves into the world of industrial automation, exploring the crucial roles of Programmable Logic Controllers (PLCs) and Variable Frequency Drives (VFDs). We’ll break down their functions, compare their strengths and weaknesses, and explain how they work together to optimize industrial processes. Whether you’re in machinery manufacturing, factory solutions, or simply curious about modern automation, this guide will provide a clear understanding of these essential components.
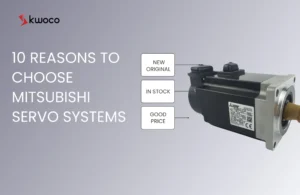
10 Reasons to Choose Mitsubishi Servo Systems
10 Reasons to Choose Mitsubishi Servo Systems Kwoco As a company specializing in automation products, we have extensive experience with
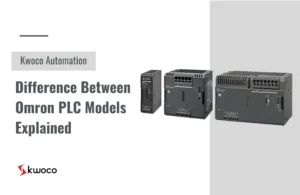
Difference Between Omron PLC Models Explained
Difference Between Omron PLC Models Explained Are you struggling to decide which Omron PLC model best fits your project needs?