Comprensión de los PLC: usos de los controladores lógicos programables
Este artículo desmitifica para qué se utiliza un PLC, cómo funciona y por qué es crucial en el panorama industrial actual. Tanto si es nuevo en el concepto como si busca profundizar sus conocimientos, siga leyendo para descubrir el papel fundamental de los PLC en la automatización de los procesos industriales.
Tabla de contenido
¿Qué es un PLC y cómo funciona?
Un controlador lógico programable (SOCIEDAD ANÓNIMA) es una computadora industrial especializada diseñada para automatizar y controlar procesos en tiempo real. A diferencia de las computadoras comunes, los PLC están diseñados para soportar condiciones ambientales adversas, como temperaturas extremas, humedad y ruido eléctrico, lo que los hace ideales para entornos industriales.
Componentes de un PLC
Un sistema PLC típico comprende:
- Unidad central de procesamiento (CPU): El cerebro que ejecuta el programa PLC.
- Módulos de entrada: Recibir señales de dispositivos de entrada como sensores, interruptores y botones.
- Módulos de salida: Envía señales a dispositivos de salida como motores, válvulas y luces.
- Fuente de alimentación: Proporciona la energía necesaria al PLC.
- Dispositivo de programación: Se utiliza para programar y configurar el PLC, a menudo mediante software de programación especializado.
¿Cómo funciona un PLC?
Un PLC funciona recorriendo continuamente tres pasos principales:
- Escaneo de entrada: el PLC recibe datos de entrada de los dispositivos de entrada conectados.
- Ejecución del programa: procesa los datos de entrada utilizando la lógica del programa definida en el programa del PLC.
- Escaneo de salida: envía comandos a los dispositivos de salida en función de los datos procesados.
Este proceso cíclico permite al PLC monitorear y controlar los procesos de manera eficiente, garantizando el funcionamiento preciso de la maquinaria y los sistemas.
¿Por qué se utilizan los PLC en la automatización industrial?
Los PLC se utilizan ampliamente en la automatización industrial debido a su confiabilidad, flexibilidad y eficiencia. A continuación, se indican las principales razones por las que las industrias utilizan PLC:
Fiabilidad y durabilidad
- Diseño robusto: Los PLC están diseñados para funcionar en condiciones difíciles, minimizando el tiempo de inactividad.
- Rendimiento consistente: Proporcionan un control estable sobre los procesos, fundamental para mantener la calidad.
Flexibilidad y escalabilidad
- Estructura modular:PLC modulares como PLC de Mitsubishi Permite una fácil expansión añadiendo módulos PLC.
- Adaptabilidad:Los programas se pueden modificar para adaptarse a los cambios en el proceso de producción sin alterar el hardware.
Operación en tiempo real
- Respuesta inmediata:Los PLC funcionan en tiempo real, lo que garantiza que los procesos reaccionen rápidamente a la entrada.
- Control de precisión:Gestione tareas complejas con alta precisión, esencial para los procesos industriales modernos.
Simplificación de sistemas complejos
- Reemplaza los sistemas lógicos de relé:Simplifica el cableado y reduce los componentes físicos necesarios.
- Solución de problemas mejorada:Es más fácil identificar problemas dentro del programa PLC en comparación con los sistemas tradicionales.
Tipos de PLC: Cómo elegir el controlador lógico programable adecuado
A la hora de elegir un PLC, es esencial comprender los diferentes tipos de PLC.
PLC modulares
- Descripción: Consta de módulos separados para la CPU, entradas, salidas y protocolos de comunicación.
- Ventajas: Altamente escalable y personalizable según necesidades específicas.
- Aplicaciones: Adecuado para procesos complejos que requieren numerosas entradas y salidas.
PLC compactos (PLC estándar)
- Descripción:Unidades todo en uno con capacidades de E/S fijas.
- Ventajas: Rentable y ahorra espacio.
- Aplicaciones:Ideal para tareas de control más simples con requisitos de E/S limitados.
PLC montados en bastidor
- Descripción:Los módulos se montan en bastidores, lo que permite una amplia expansión.
- Ventajas:Admite una gran cantidad de puntos de E/S y alta potencia de procesamiento.
- Aplicaciones:Aplicaciones industriales a gran escala como control de procesos en refinerías de petróleo.
Al seleccionar un PLC, tenga en cuenta factores como:
- Complejidad del proceso: La naturaleza de las tareas y el control requerido.
- Requisitos de E/S: Número y tipo de dispositivos de entrada y salida.
- Condiciones ambientales: Temperatura, polvo y niveles de humedad en el entorno operativo.
- Necesidades de comunicación: Integración con sistemas SCADA, HMI, y otros dispositivos externos.
Marcas como PLC Omron y PLC Schneider Ofrecemos varios PLC con diferentes características de PLC para adaptarse a diversas necesidades industriales.
¿Cómo se programan los PLC? Comprensión de los lenguajes de programación de los PLC
Los PLC se programan utilizando lenguajes de programación especializados que instruyen al PLC sobre cómo responder a condiciones de entrada específicas.
Lenguajes de programación de PLC comunes
- Lógica de escalera (diagrama de escalera)
- Lenguaje de programación de PLC más comúnmente utilizado.
- Se asemeja a la lógica de relé tradicional, lo que lo hace intuitivo para los ingenieros familiarizados con los circuitos eléctricos.
- Ideal para operaciones sencillas de control y secuenciación.
- Texto estructurado
- Lenguaje textual de alto nivel similar a Pascal.
- Adecuado para funciones y algoritmos matemáticos complejos.
- Diagrama de bloques de funciones (FBD)
- Lenguaje gráfico que utiliza bloques para representar funciones.
- Excelente para control de procesos analógicos y bloques de funciones.
- Diagrama de funciones secuenciales (SFC)
- Representa los procesos como una serie de pasos y transiciones.
- Útil para procesos por lotes y funciones secuenciales.
- Lista de instrucciones
- Lenguaje textual de bajo nivel parecido al código ensamblador.
- Eficiente pero menos intuitivo debido a su sintaxis concisa.
Conceptos de programación
- Entradas y salidas: Comprender cómo los dispositivos de entrada, como sensores e interruptores, afectan las salidas.
- Lógica de control: Desarrollar la lógica del programa que define la relación entre entradas y salidas.
- Temporizadores y contadores: Gestionar eventos en función del tiempo o de conteos.
- Manejo de datos: Trabajar con variables, matrices y almacenamiento de datos.
Software de programación
Los fabricantes suelen proporcionar software de programación propietario para sus PLC. Este software incluye herramientas para escribir, simular y depurar programas de PLC.
Para utilizar un PLC de forma eficaz es necesario estar familiarizado con estos conceptos y lenguajes de programación. Al aprovechar el lenguaje adecuado, los ingenieros pueden crear sistemas de control eficientes y robustos.
PLC, sistemas SCADA y HMI: ¿cómo funcionan juntos?
En el ámbito de la automatización industrial, los PLC a menudo funcionan junto con sistemas SCADA y HMI para formar un sistema de control integrado.
PLC (controladores lógicos programables)
- Role: Ejecutar el control a nivel de máquina o proceso.
- Funcionalidad: Procesar datos de entrada y controlar dispositivos de salida en tiempo real.
HMI (Interfaces hombre-máquina)
- Role: Proporcionar una interfaz entre operadores y máquinas.
- Funcionalidad: Muestra datos del proceso, permite entradas de usuario y visualiza estados del sistema.
- Ejemplos: Interfaz hombre-máquina Proface, Interfaz hombre-máquina Mitsubishi.
Sistemas SCADA (Supervisión, Control y Adquisición de Datos)
- Role:Supervisar y controlar varios PLC en una instalación o región.
- Funcionalidad:Recopilar datos de los PLC, proporcionar control de supervisión y facilitar el análisis de datos.
- Importancia:Crítico para operaciones a gran escala como plantas de tratamiento de agua y redes eléctricas.
Protocolos de comunicación
- Objetivo:Habilite el intercambio de datos entre PLC, HMI y sistemas SCADA.
- Protocolos comunes:Modbus, Profibus, Ethernet/IP.
- Beneficios:Permite control coordinado, registro de datos y monitoreo remoto.
Al integrar estos sistemas, las industrias logran una automatización perfecta, una mayor eficiencia y mejores capacidades de toma de decisiones.
Aplicaciones de los PLC en la automatización industrial
Los PLC se utilizan en diversas industrias debido a su versatilidad. A continuación, se muestran algunas aplicaciones típicas:
Fabricación
- Líneas de montaje:Controlar brazos robóticos, transportadores y máquinas herramienta.
- Control de calidad:Monitorear los parámetros de producción para garantizar la consistencia.
Sector Energético
- Generación de energía: Gestionar turbinas, generadores y sistemas de distribución.
- Petróleo y gas:Controlar operaciones de perforación y sistemas de tuberías.
Gestión del agua y los residuos
- Plantas de tratamiento:Regular bombas, mezcladores y dosificación de productos químicos.
Industria automotriz
- Líneas de producción:Coordinar tareas complejas en el montaje de vehículos.
Automatización de edificios
- Sistemas HVAC:Controla la calefacción, la ventilación y el aire acondicionado.
- Sistemas de iluminación:Automatiza la iluminación según la ocupación o la hora del día.
Al utilizar un PLC, las industrias pueden automatizar procesos, mejorar la seguridad, reducir el error humano y optimizar las operaciones.
Ejemplo del mundo real: control de toda una línea de producción
Un PLC puede gestionar una línea de producción completa mediante:
- Recepción de entradas: Recopilación de datos de sensores (temperatura, presión, proximidad).
- Procesamiento de datos: Ejecutar el programa PLC para determinar las acciones necesarias.
- Control de salidas: Operar motores, actuadores y otros dispositivos para realizar tareas.
- Comunicado: Compartir información con sistemas SCADA y HMIs para monitoreo y control.
Esta integración minimiza el tiempo de inactividad y mejora la productividad.
Preguntas frecuentes
El método más utilizado para programar PLC es el Ladder Logic, que se asemeja a los diagramas lógicos de relés eléctricos. Es intuitivo para quienes están familiarizados con los esquemas de circuitos y es ideal para tareas de control simples o moderadamente complejas.
Los PLC se comunican mediante varios puertos y protocolos de comunicación, como Ethernet/IP, Modbus y Profibus. Estos protocolos permiten el intercambio de datos con HMI, sistemas SCADA y otros dispositivos externos, lo que facilita el control y la supervisión integrados.
- Flexibilidad:Fácilmente reprogramable para diferentes tareas.
- Ahorro de espacio:Reduce la complejidad del cableado.
- Fiabilidad:Tasas de fallos más bajas debido a menos componentes mecánicos.
- Funciones avanzadas:Capacidades como registro de datos, cálculos complejos y comunicación en red.
Considerar:
- Requisitos del proceso:Complejidad y necesidades de control.
- Recuento de E/S:Número de entradas y salidas requeridas.
- Factores ambientales:Condiciones de funcionamiento como temperatura y polvo.
- Escalabilidad:Potencial expansión futura.
- Compatibilidad:Integración con sistemas existentes.
Sí, los PLC pueden procesar señales analógicas (valores variables) y señales discretas (estados de encendido y apagado). Hay módulos de entrada disponibles para varios tipos de señales, lo que permite que los PLC gestionen diversas entradas de datos.
Potencie sus proyectos con PLC Omron, Mitsubishi y Schneider nuevos y originales: ¡en stock y listos ahora!
Conclusión
- Los PLC son computadoras industriales especializadas que se utilizan para automatizar y controlar maquinaria y procesos en tiempo real.
- Funcionan procesando datos de entrada de los dispositivos de entrada y controlando los dispositivos de salida según la lógica de control programada.
- La programación de un PLC implica el uso de lenguajes como lógica de escalera, texto estructurado y diagrama de bloques de funciones.
- Los tipos de PLC incluyen PLC modulares, PLC compactos y PLC montados en bastidor, cada uno adecuado para diferentes aplicaciones.
- Los PLC a menudo funcionan junto con HMI y sistemas SCADA para formar soluciones de automatización integrales.
- La elección de un PLC requiere tener en cuenta la complejidad del proceso, las necesidades de E/S, las condiciones ambientales y la escalabilidad.
- Los PLC se utilizan en diversas industrias, mejorando la eficiencia, la confiabilidad y la seguridad en las operaciones.
¿Buscas PLC nuevos y originales para tus proyectos? En Kwoco, tenemos en stock los PLC más recientes de las mejores marcas como Omrón, Mitsubishi, y SchneiderCompre con confianza: envío rápido, calidad garantizada. ¡Compre ahora!
Contáctenos
Simplemente complete su nombre, dirección de correo electrónico y una breve descripción de su consulta en este formulario. Nos comunicaremos con usted dentro de las 24 horas.
Categoría de producto
Productos en oferta
También te pueden interesar estos temas
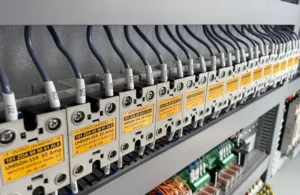
PLC de relé vs. PLC de transistor: ¿cuál se adapta a sus necesidades de control?
PLC de relés frente a PLC de transistores: ¿cuál se adapta a sus necesidades de control? En el mundo de la automatización industrial, seleccionar el controlador PLC adecuado
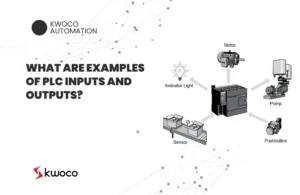
¿Cuáles son ejemplos de entradas y salidas de PLC?
¿Cuáles son los ejemplos de entradas y salidas de PLC? En la automatización industrial, los sistemas PLC (controlador lógico programable) son el cerebro detrás
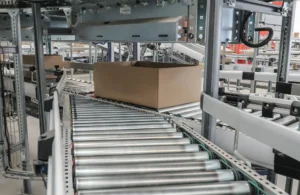
¿Qué detectan los sensores fotoeléctricos?
Quizás te preguntes, ¿qué detectan exactamente los sensores fotoeléctricos?
En pocas palabras, los sensores fotoeléctricos detectan la presencia o ausencia de un objeto mediante luz. Son componentes esenciales en la automatización y se utilizan en diversas industrias para garantizar que los procesos se ejecuten de manera fluida y eficiente.