Relays: Types and Applications Guide
Table of Contents
1. What is a Relay and How Does It Work?
A relay is an electrically operated switch. It’s essentially a device that opens or closes circuits electromechanically or electronically. Relays are used to control one circuit by opening and closing contacts in another circuit.
When a relay contact is normally open (NO), there is an open contact when the relay is not energized. Conversely, when a relay contact is normally closed (NC), there is a closed contact when the relay is not energized. In either case, applying electrical current to the contacts changes their state.
Relays are commonly used where it’s necessary to control a circuit by a low-power signal, or where several circuits must be controlled by one signal. I’ve seen firsthand how critical these devices are in industrial settings, particularly in controlling high-power circuits with low-power signals.
For instance, in our manufacturing plants, relays enable small control signals from a PLC to manage the operation of large motors and other heavy machinery, ensuring efficient and safe operation.
A relay is an electrical switch that opens and closes under the control of another electrical circuit. When an electrical current flows through the relay’s coil, it generates a magnetic field that activates the armature, which in turn moves the relay contacts.
2. What are the Main Components of a Relay?
A relay consists of an electromagnet (relay coil), an armature, a spring, and a set of electrical contacts. The electromagnet is formed when a wire coil is wrapped around an iron core.
When an electrical current flows through the coil, it becomes an electromagnet, attracting the armature. The armature is a moving part that opens or closes the contacts. The spring returns the armature to its original position when the relay is deactivated.
Relay diagrams illustrate how these components interact. Inside the relay, the coil and contacts are the most crucial parts. For example, when voltage is applied to the relay coil, the resulting current creates a magnetic field.
This field pulls the armature towards the coil, closing the normally open relay contacts and completing the circuit. This mechanism is fundamental in numerous industrial applications, allowing for the safe and efficient control of high-power devices with precision.
The specific design and construction of relay switches and contacts can vary based on the type of relay and its intended use.
3. Electromechanical Relays (EMR) vs. Solid-State Relays (SSR):
Electromechanical relays (EMRs) use a physical moving part to connect circuits. When the relay coil is energized, it creates a magnetic field that moves a physical armature, which in turn makes or breaks the circuit.
Relays provide electrical isolation between the control circuit and the load circuit.
Solid-state relays (SSRs), on the other hand, have no moving parts. Instead, they use semiconductors like thyristors or transistors to switch the load circuit. Unlike mechanical relays, SSRs offer faster switching times and longer operational life because they lack mechanical components that can wear out.
I often recommend SSRs in applications requiring high switching frequencies or where the environment is harsh on mechanical parts. As relay is an electrically operated switch, understanding the differences between EMRs and SSRs is essential for selecting the appropriate relay for specific applications in industrial automation.
Feature | Electromechanical Relay (EMR) | Solid-State Relay (SSR) |
---|---|---|
Moving Parts | Yes | No |
Switching Speed | Slower | Faster |
Lifespan | Shorter | Longer |
Audible Noise | Yes (clicking) | No |
Sensitivity | Less sensitive | More sensitive |
Electrical Noise | Higher | Lower |
4. What are the Different Types of Relays?
There are various types of relays designed for specific applications. Some common relay types include:
- Electromechanical Relay (EMR): Uses an electromagnet to operate a mechanical switch. Suitable for AC and DC.
- Solid State Relay (SSR): Uses semiconductors to switch the load. Ideal for applications requiring fast switching and long life.
- Reed Relay: Employs a reed switch within the coil. Known for its compact size and fast operation, often used in test equipment.
- Latching Relay: Maintains its contact position even after the input is removed. Requires a separate pulse to reset.
- Polarized Relay: The operation of a polarized relay is dependent on the polarity of the applied voltage.
- Time Delay Relay: The relay contacts are open until the relay has been energized for a preset time.
Each type of relay has unique characteristics that make it suitable for different applications. For example, reed relays are often used in testing equipment due to their small size and fast switching speed, while latching relays are preferred in memory circuits because they maintain their state without continuous power.
Relays are constructed in various electrical and electronic circuit configurations, such as SPST, SPDT, DPST, and DPDT, to meet specific switching needs.
5. How to Choose the Right Relay for Your Application?
Choosing the appropriate relay involves considering several factors:
- Load Characteristics: What is the voltage and current of the load you need to switch?
- Control Voltage: What voltage is available to energize the relay coil?
- Switching Speed: How quickly does the relay need to operate?
- Environmental Conditions: Will the relay be exposed to extreme temperatures, humidity, or vibrations?
- Lifespan: How many switching cycles does the application require?
For example, in our machinery and equipment factories, we often use solid-state relays for applications requiring fast switching and long life. In contrast, electromechanical relays are preferred for applications where cost is a primary concern and switching speed is less critical.
The current that flows through the relay must be considered to select a relay that can handle the load without overheating. When the relay activates, it should protect the electrical system by isolating the control circuit from the load circuit.
6. How to Test a Relay and Troubleshoot Common Issues?
Test a relay involves checking the continuity of the contacts and the resistance of the coil. A multimeter is a handy tool for this purpose.
- Coil Resistance Test: Measure the resistance across the relay coil terminals. An infinite resistance reading usually indicates an open coil.
- Contact Continuity Test: When the relay is not energized, normally open contacts should show infinite resistance, and normally closed contacts should show zero resistance. When the relay is energized, these readings should reverse.
Common issues with relays include coil burnout, contact welding, and mechanical wear. Regularly testing relays can help identify potential problems before they lead to system failures.
Relays often fail due to excessive current or voltage, so ensuring the relay is rated for the application is crucial. To test a relay, you should check the relay coil and contacts using a multimeter.
7. What are Relay Contact Types and Their Significance?
Relay contact types are categorized based on their configuration and function. Common configurations include:
- Form A (SPST-NO): Single Pole Single Throw – Normally Open. This type of relay has one normally open contact, which closes when the relay is energized.
- Form B (SPST-NC): Single Pole Single Throw – Normally Closed. It has one normally closed contact, which opens when the relay is energized.
- Form C (SPDT): Single Pole Double Throw. Also known as a changeover relay, it has one common terminal and two contacts: one normally open and one normally closed. The SPDT relay can switch between two circuits.
- Form D (SPDT): Make before break.
Understanding these configurations is vital for selecting the right relay for your application. For instance, a Form A relay is suitable for simply turning a load on and off, while a Form C relay can be used to switch between two different loads.
The relay contact material also plays a crucial role in the relay’s performance and lifespan. Relay contact types determine how the relay will switch the load circuit, making it essential to choose the correct configuration for your needs.
8. What is the Life Expectancy of a Relay and Factors Affecting It?
The life of a relay depends on several factors, including the operating environment, switching frequency, and the electrical load being switched.
Electromechanical relays typically have a mechanical life of 100,000 to 1 million operations and an electrical life of 10,000 to 100,000 operations. Solid-state relays, with no moving parts, can have a much longer operational life.
Factors that can shorten a relay’s life include:
- Excessive Current or Voltage: Exceeding the relay’s rated values can lead to overheating and premature failure.
- High Switching Frequency: Frequent switching can cause mechanical wear in EMRs.
- Environmental Factors: Extreme temperatures, humidity, and vibration can also reduce relay life.
Regular maintenance and proper selection can help maximize a relay’s lifespan. It’s also essential to consider the operating environment when choosing a relay. For instance, in harsh industrial environments, we use sealed relays to protect against dust, moisture, and other contaminants.
9. Relay Applications: Where are Relays Commonly Used?
Relays are used in a wide range of applications across various industries. Some common relay applications include:
- Industrial Control Systems: Relays control motors, pumps, and other high-power devices in industrial settings.
- Automotive: Relays are used in vehicles to control lights, horns, and other electrical components.
- Telecommunications: Relays switch signals in telecommunication networks.
- HVAC Systems: Relays control heating, ventilation, and air conditioning equipment.
- Power Distribution: Relays protect electrical circuits and equipment in power distribution systems.
- Consumer Electronics: Relays are used in various electronic devices, such as refrigerators and washing machines.
Relays are versatile components that can be found in numerous applications, from simple household appliances to complex industrial control systems. For example, relays are used to start and stop motors, control lighting circuits, and activate alarms. Relay applications are vast and varied, making them indispensable components in many industries.
10. Future Trends in Relay Technology
The field of relay technology continues to evolve, with ongoing advancements aimed at improving performance, reliability, and efficiency. Some of the key future trends in relay technology include:
- Miniaturization: There is a growing demand for smaller relays that can be integrated into compact electronic devices.
- Smart Relays: These relays incorporate microprocessors and communication capabilities, enabling remote monitoring and control.
- Solid-State Relays (SSRs): With advancements in semiconductor technology, SSRs are becoming increasingly popular due to their long life and fast switching speeds.
- Energy Efficiency: New relay designs are focusing on reducing power consumption, contributing to energy savings.
These trends reflect the broader industry shift towards smarter, more efficient, and more integrated automation solutions.
Frequently Asked Questions
A relay is an electrically operated switch used to control one circuit by opening and closing contacts in another circuit. It allows a low-power signal to control a high-power circuit, providing electrical isolation between the two.
An electromechanical relay (EMR) uses a physical moving part (switch) to connect circuits, while a solid-state relay (SSR) uses semiconductors. SSRs offer faster switching times and longer operational life compared to EMRs.
Consider the load characteristics (voltage and current), control voltage, switching speed, environmental conditions, and required lifespan when choosing a relay. For instance, solid-state relays are ideal for applications requiring fast switching and long life, while electromechanical relays are more cost-effective for less demanding applications.
Common issues include coil burnout, contact welding, and mechanical wear. To troubleshoot, use a multimeter to test the coil resistance and contact continuity. Ensure the relay is rated for the application to prevent issues caused by excessive current or voltage.
Common configurations include Form A (SPST-NO), Form B (SPST-NC), and Form C (SPDT). These configurations determine how the relay switches the load circuit, making it crucial to choose the correct one for your specific needs.
Power your projects with brand-new, original Omron, Mitsubishi, Schneider Servo – in stock, ready now!
Conclusion
- Relays are essential components in many electrical systems, providing a way to control high-power circuits with low-power signals.
- There are different types of relays, including electromechanical, solid-state, reed, and latching relays, each with unique characteristics and applications.
- Choosing the right relay involves considering factors such as load characteristics, control voltage, switching speed, environmental conditions, and lifespan.
- Regularly testing and troubleshooting relays can help identify potential issues before they lead to system failures.
- Relays are used in a wide range of applications, from industrial control systems to consumer electronics.
- Advancements in relay technology, such as miniaturization and smart relays, are driving improvements in performance, reliability, and efficiency.
By understanding the different types of relays and their applications, you can make informed decisions when selecting and using these critical components. Whether you’re designing a new control system or maintaining an existing one, a solid grasp of relay technology is invaluable.
For those in the machinery and equipment industry, manufacturing plants, or factory solution companies, leveraging the right relay technology can enhance efficiency, safety, and reliability. Contact us today to learn how our industrial automation solutions can meet your specific needs. Our expertise in industrial control products ensures you receive the best components for your applications, including top-quality Omron sensors, Mitsubishi PLC, Proface HMI, Mitsubishi Inverter and Schneider PLC. We look forward to partnering with you to optimize your operations.
Contact Us
Just fill out your name, email address, and a brief description of your inquiry in this form. We will contact you within 24 hours.
You May Also Find These Topics Interesting

Introduction to Programmable Logic Controllers: Your Gateway to Industrial Automation
This article is a comprehensive guide to Programmable Logic Controllers (PLCs), exploring their fundamental role in modern industrial automation. From machinery and equipment factories to manufacturers and solution providers, PLCs are indispensable for streamlining operations and enhancing productivity. This article delves into the intricacies of PLCs, their programming, and their diverse applications.
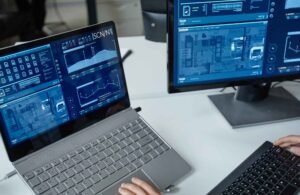
PLC vs PC: Key Differences in Industrial Automation
In the realm of industrial automation, the choice between a Programmable Logic Controller (PLC) and a Personal Computer (PC) can significantly impact operational efficiency and system performance. This article delves into the fundamental differences between these two technologies, helping you make informed decisions for your automation needs.
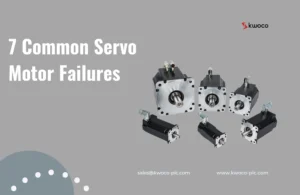
7 Common Servo Motor Failures
7 Common Servo Motor Failures As a seasoned engineer with extensive experience in industrial automation, I’ve seen my fair share