3-Wire Inductive Proximity Sensors: Complete Guide
In this comprehensive guide, we’ll explore everything from basic principles to practical applications, helping you make informed decisions for your automation needs.
Table of Contents
What Is a 3-Wire Inductive Proximity Sensor and How Does It Work?
A 3-wire inductive proximity sensor is an electronic device that detects metallic objects without physical contact. These sensors use electromagnetic fields to detect the presence or absence of conductive targets. Unlike traditional mechanical switches, inductive sensors offer several advantages:
- No physical contact required for detection
- Long operational life due to no mechanical wear
- High switching frequency capabilities
- Excellent resistance to industrial environments
The sensor operates by generating an electromagnetic field from its sensing face. When a metallic target enters this field, eddy currents are induced in the target, causing a change in the sensor’s oscillator circuit. This change triggers the output to switch states.
PNP vs NPN: Which Output Configuration Should You Choose?
One of the most critical decisions when selecting a 3-wire proximity sensor is choosing between PNP and NPN output types. Let’s break down the differences:
PNP (Sourcing) Output:
- Switches positive voltage to the load
- Common in European applications
- Connects to PLC sinking inputs
- More resistant to electrical noise
NPN (Sinking) Output:
- Switches ground to the load
- Popular in Asian markets
- Connects to PLC sourcing inputs
- Generally less expensive
The choice between PNP and NPN often depends on your existing control system and regional preferences. Learn more about industrial sensors for detailed specifications.
How to Install and Connect Your 3-Wire Proximity Sensor?
Proper installation and connection are crucial for optimal sensor performance. Here’s a step-by-step guide:
- Power Supply Connection:
- Brown wire → Positive DC voltage (typically 12-24V DC)
- Blue wire → Negative/Ground
- Black wire → Output signal
- Mounting Considerations:
- Maintain proper sensing distance
- Avoid interference from nearby metal objects
- Consider environmental factors (temperature, vibration)
- Load Connection:
- Connect the load between the output and power supply
- Ensure proper voltage and current ratings
- Use appropriate surge protection
Check our PLC integration guide for detailed automation system connections.
Common Applications and Industrial Uses
3-wire inductive proximity sensors find widespread use in various industrial applications:
Application | Benefits | Common Industries |
---|---|---|
Position Detection | High accuracy, fast response | Automotive, Packaging |
Metal Detection | Reliable operation, long life | Manufacturing, Mining |
Speed Monitoring | Precise measurement, durability | Conveyor Systems |
These sensors are particularly valuable in automated production lines and robotic applications.
Troubleshooting and Maintenance Tips
To ensure reliable operation, consider these maintenance practices:
- Regular cleaning of the sensing face
- Periodic checking of connection integrity
- Verification of proper alignment
- Monitoring of supply voltage stability
Frequently Asked Questions
Typical sensing ranges vary from 1mm to 40mm, depending on the sensor size and target material.
3-wire sensors offer separate power and output connections, allowing for more flexible integration and better performance.
No, inductive sensors are specifically designed to detect metallic objects only. For non-metallic materials, consider capacitive or photoelectric sensors.
Most sensors include an LED indicator that shows the detection status and proper operation.
Power your projects with brand-new, original Omron, Keyence, Schneider Sensors – in stock, ready now!
Conclusion
Key Takeaways
- 3-wire inductive proximity sensors are essential components in modern industrial automation
- Choose between PNP and NPN outputs based on your system requirements
- Proper installation and maintenance ensure reliable operation
- Regular troubleshooting prevents downtime and extends sensor life
- Consider environmental factors when selecting and installing sensors
Contact our automation experts for personalized assistance with your sensor applications.
Contact Us
Just fill out your name, email address, and a brief description of your inquiry in this form. We will contact you within 24 hours.
You May Also Find These Topics Interesting
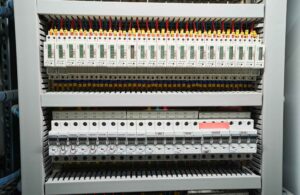
What Is a PLC Panel? A Guide to Electrical Automation
The PLC control panel is the cornerstone of modern industrial automation, orchestrating complex processes with precision and efficiency. Understanding what a PLC panel is and how it functions is essential for anyone involved in industrial operations. This comprehensive guide will illuminate the world of programmable logic controllers and their pivotal role in automating industrial processes.
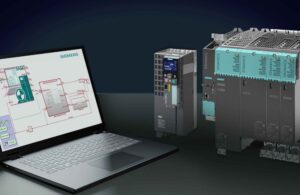
Siemens Drive Fault Code: A Comprehensive Guide to Troubleshooting and Resolution
This article provides a detailed guide to understanding and troubleshooting Siemens drive fault codes. Whether you’re an experienced engineer or new to industrial automation, this comprehensive resource will help you quickly diagnose and resolve issues, minimizing downtime and optimizing productivity. It’s worth reading because it offers practical insights, step-by-step instructions, and expert advice to keep your operations running smoothly.
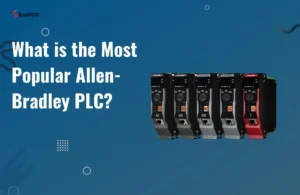
What is the Most Popular Allen-Bradley PLC?
What is the Most Popular Allen-Bradley PLC? If you’re in the automation industry, you’ve probably heard of Allen-Bradley PLCs. They