The Complete Guide to Programmable Logic Controllers (PLCs)
- kwoco-plc.com
- September 26, 2024
- 1:47 am
In the fast-evolving world of industrial automation, Programmable Logic Controllers (PLCs) have emerged as crucial components in enhancing efficiency, reliability, and flexibility in manufacturing and process control. From assembly lines to robotic systems, PLCs are the backbone of modern automation.
This guide aims to demystify PLCs, explore their applications, and provide insights into their functionality, ensuring that both novices and seasoned professionals can harness their power effectively.
Table of Contents
What is Programmable Logic Controllers (PLC)?
Programmable Logic Controllers (PLCs) are industrial digital computers designed to control manufacturing processes or machinery. They receive input signals from sensors and other devices, process these signals according to predefined logic, and then output commands to actuators and machinery. This ability to process multiple inputs and outputs makes PLCs indispensable in various industries.
Common Terms in PLC
- Inputs and Outputs (I/O): PLCs have input modules that receive data from various sensors (e.g., temperature, pressure) and output modules that send commands to devices (e.g., motors, lights).
- Logic Programming: PLCs use ladder logic, function block diagrams, or structured text for programming. This allows for creating complex control logic in a way that is easier to visualize and understand.
- Scan Cycle: PLCs operate in a continuous loop, known as the scan cycle, which includes reading inputs, executing the control program, and updating outputs.
What Are the Key Features of a PLC?
PLC systems boast several unique characteristics that make them indispensable.
- High Reliability: Most PLCs utilize single-chip microcomputers. They come equipped with protective circuits and self-diagnosis features, enhancing system reliability.
- Flexibility: Before PLCs, hardwired control systems were the norm. The advent of PLCs revolutionized this by allowing control tasks to be programmed through software.
- Ease of Installation: No special machine rooms or stringent shielding measures are necessary. As long as sensors and actuators connect properly to the PLC’s I/O terminals, the system functions seamlessly.
- Scalability: Can be expanded to accommodate additional devices and processes.
- Cost-Effective: Reduces downtime and maintenance costs through efficient operation.
How PLCs Work
Understanding the functionality of PLCs involves several components and processes:
1. Input/Output Modules
- Input Modules: These connect sensors and switches to the PLC, converting real-world signals into a format the PLC can understand.
- Output Modules: These send signals to actuators, controlling devices like motors, lights, and valves.
2. The Central Processing Unit (CPU)
The CPU is the brain of the PLC. It processes input signals, executes the control program, and generates output signals. It performs operations based on a predefined sequence, ensuring the system functions as intended.
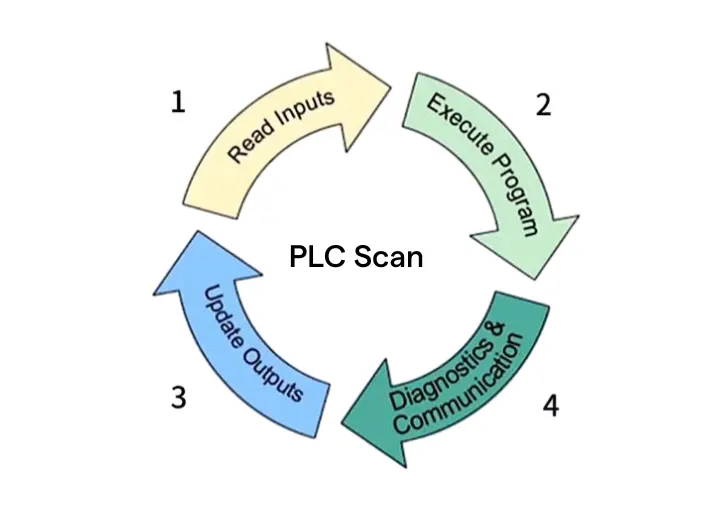
3. PLC Programming
PLCs are programmed using various languages, with the most common being Ladder Logic. This graphical representation resembles electrical relay logic, making it intuitive for engineers:
- Ladder diagram language (LD): Ladder diagram language is the first programming language used by PLC and is also the most commonly used programming language for PLC. It evolved from the schematic diagram of the relay control system. The systems are similar, but there are certain differences in the use of symbols and expressions.
- Structured text language (ST): Structured text language is a high-level text language that can be used to describe the behavior of functions, function blocks and programs, and can also describe the behavior of steps, actions and transitions in sequential function flow charts
- Sequential function flow chart language (SFC): Sequential function flow chart is also called flow chart or state transition chart, which is a graphical functional description language.
- Function block diagram language (FBD): Function block diagram language uses graphic symbols similar to digital logic gate circuits, with intuitive logic and easy to use.
- Instruction list language (IL): Instruction list programming language is similar to mnemonic assembly language in computers. It is the most basic programming language for programmable controllers.
4. The PLC Scan Cycle
A PLC operates in a continuous loop:
- Input Scan: Reads the status of all input devices.
- Program Execution: Processes the control logic based on the input status.
- Output Scan: Updates the status of output devices based on the program execution.
This cycle ensures that PLCs can respond to changes in real time, maintaining system control.
Common Applications of PLCs
PLCs find applications across numerous sectors. Here are a few examples:
- Manufacturing: In automotive assembly lines, PLCs control robotic arms, conveyor belts, and quality inspection systems.
- Food and Beverage: PLCs manage processes such as mixing, bottling, and packaging to ensure consistency and quality.
- Water Treatment: PLCs regulate chemical dosing, monitor water quality, and control pumps in wastewater treatment facilities.
- Energy: In power plants, PLCs monitor equipment conditions, manage system alarms, and control turbines.
These applications illustrate how PLCs enhance operational efficiency and ensure safety in various industries.
PLC Hardware
- Processor Types: Different PLCs feature varying processor speeds and capacities. Selecting the right one depends on application complexity.
- Power Supply: PLCs require a stable power supply, typically from 24V DC sources.
- Enclosures: Robust enclosures protect PLCs from environmental hazards, ensuring reliable operation in harsh conditions.
PLC Software
- Programming Software: Most PLCs come with proprietary software for programming and diagnostics. Familiarize yourself with these tools for effective system setup.
- Simulation Software: Before deploying programs, use simulation software to test logic without risking physical equipment.
Types and Classifications of PLCs
PLCs can be classified into different types based on size, functionality, and application:
PLC Types | Description | Use Cases |
Compact PLCs | These are smaller, cost-effective solutions ideal for basic control tasks. | Suitable for small manufacturing processes and building automation. |
Modular PLCs | Composed of separate modules for input/output, CPU, and communication. | Ideal for complex systems requiring flexibility and expansion. |
Safety PLCs | Designed to handle safety-critical applications. | Used in industries like automotive and pharmaceuticals where safety compliance is crucial. |
PLC Manufacturers
The PLC industry is populated by several key players, each contributing to the advancement of automation technologies:
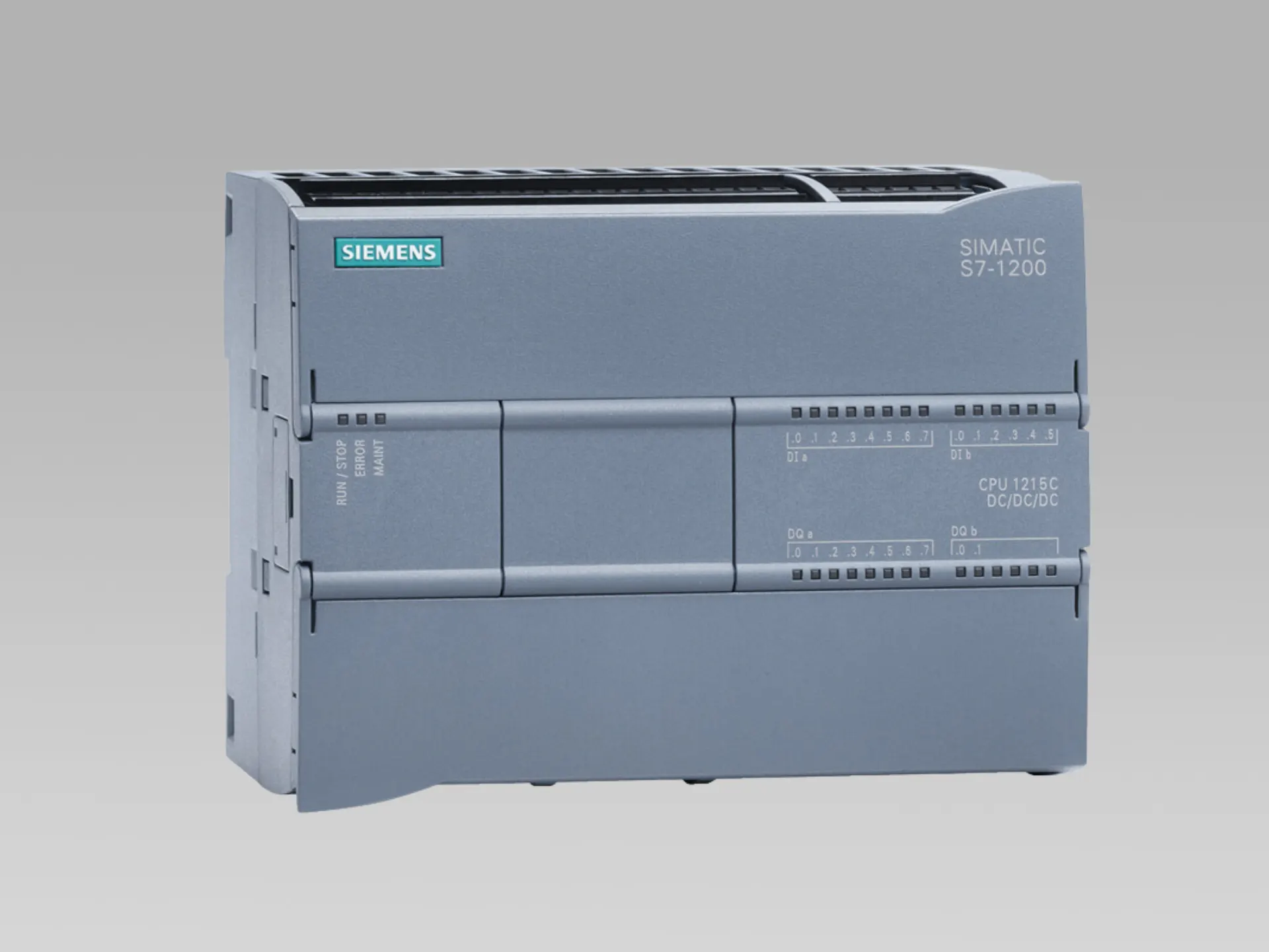
Siemens
Known for their S7 series PLCs, which are widely used in various industrial applications. Browse All PLCs>>
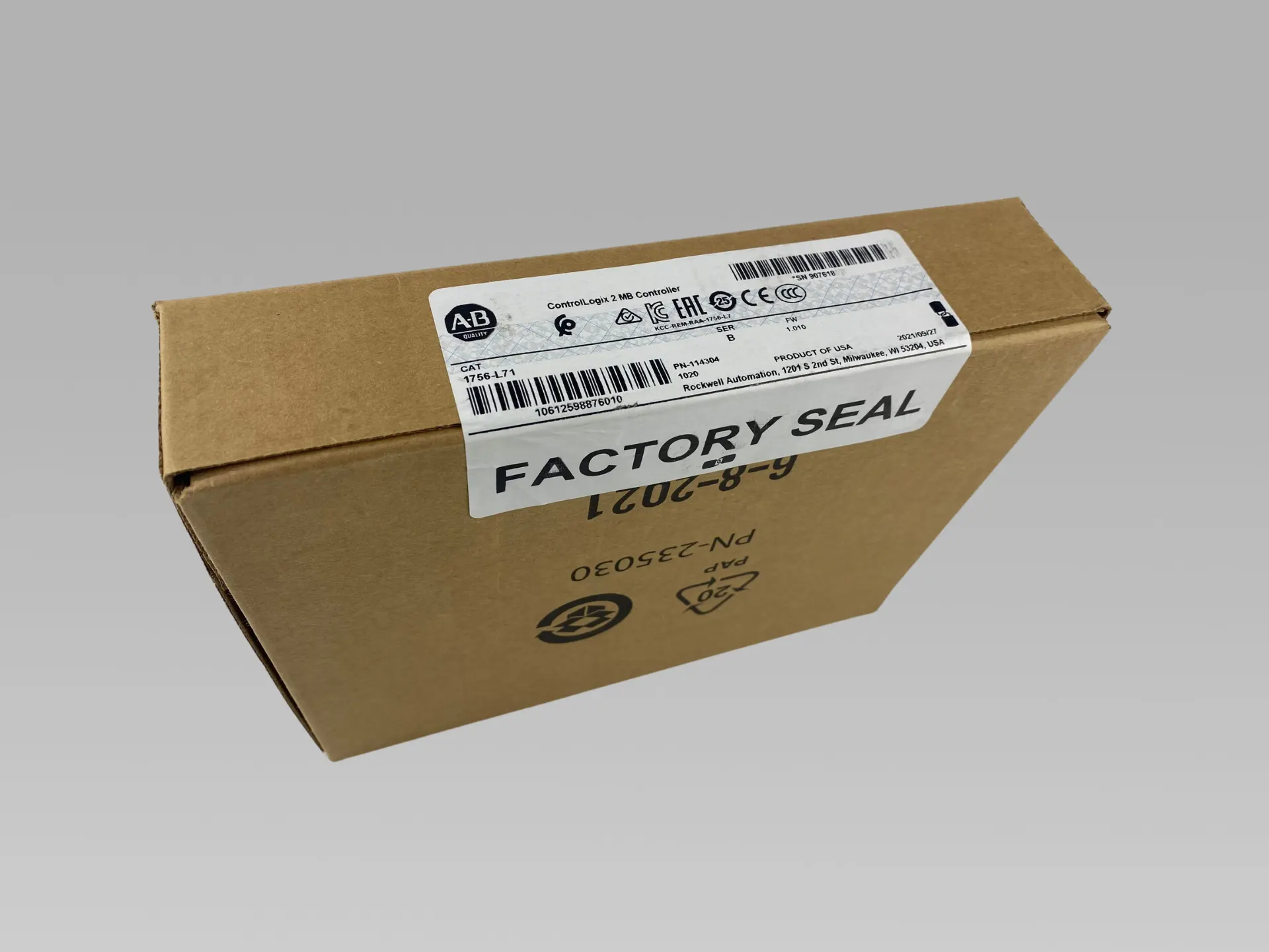
Rockwell Automation
Their Allen-Bradley PLCs are known for robustness and ease of integration in manufacturing systems. Browse All PLCs>>
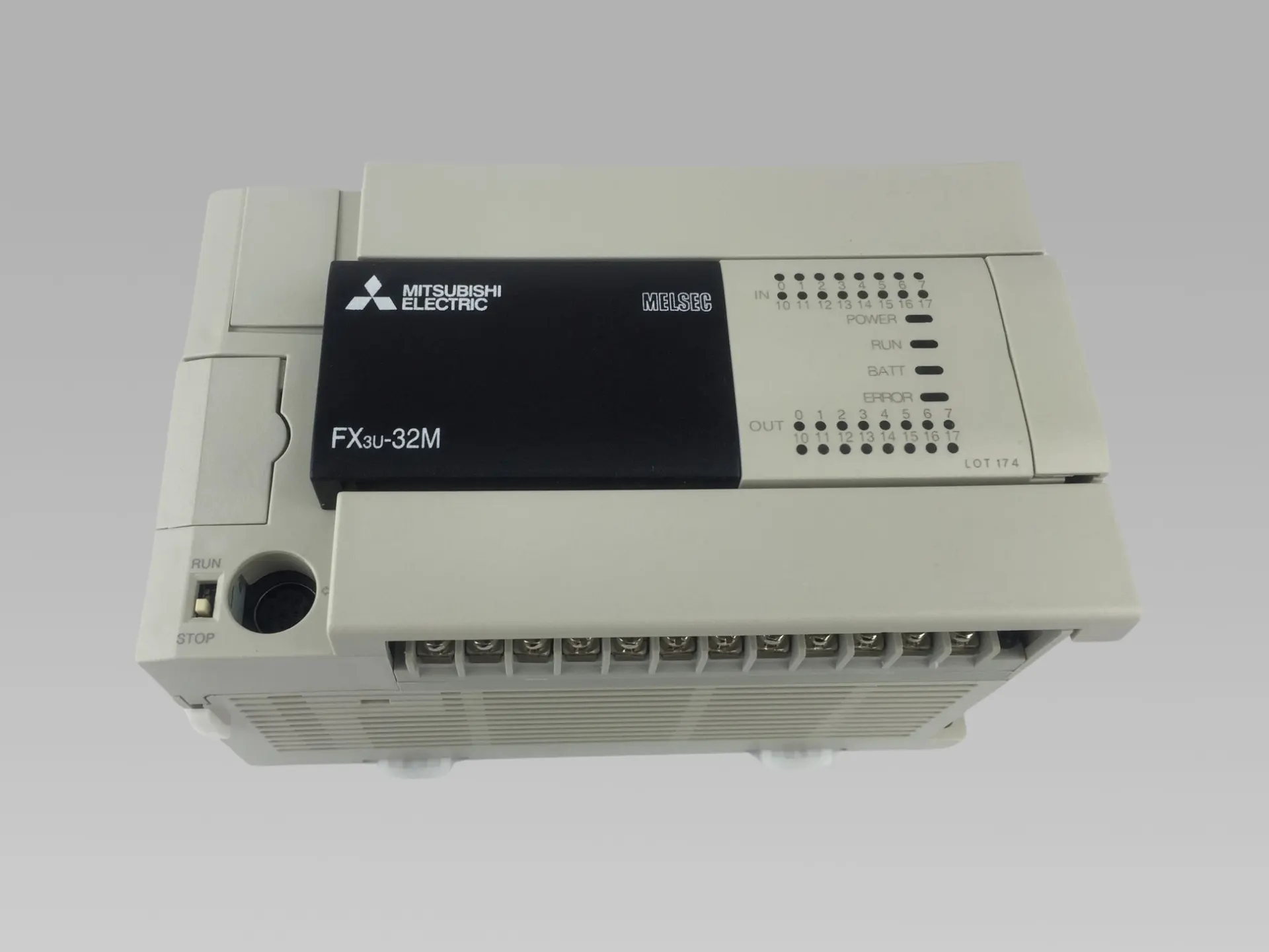
Mitsubishi Electric
Offers a range of PLCs suitable for diverse applications, emphasizing reliability and performance. Browse All PLCs>>
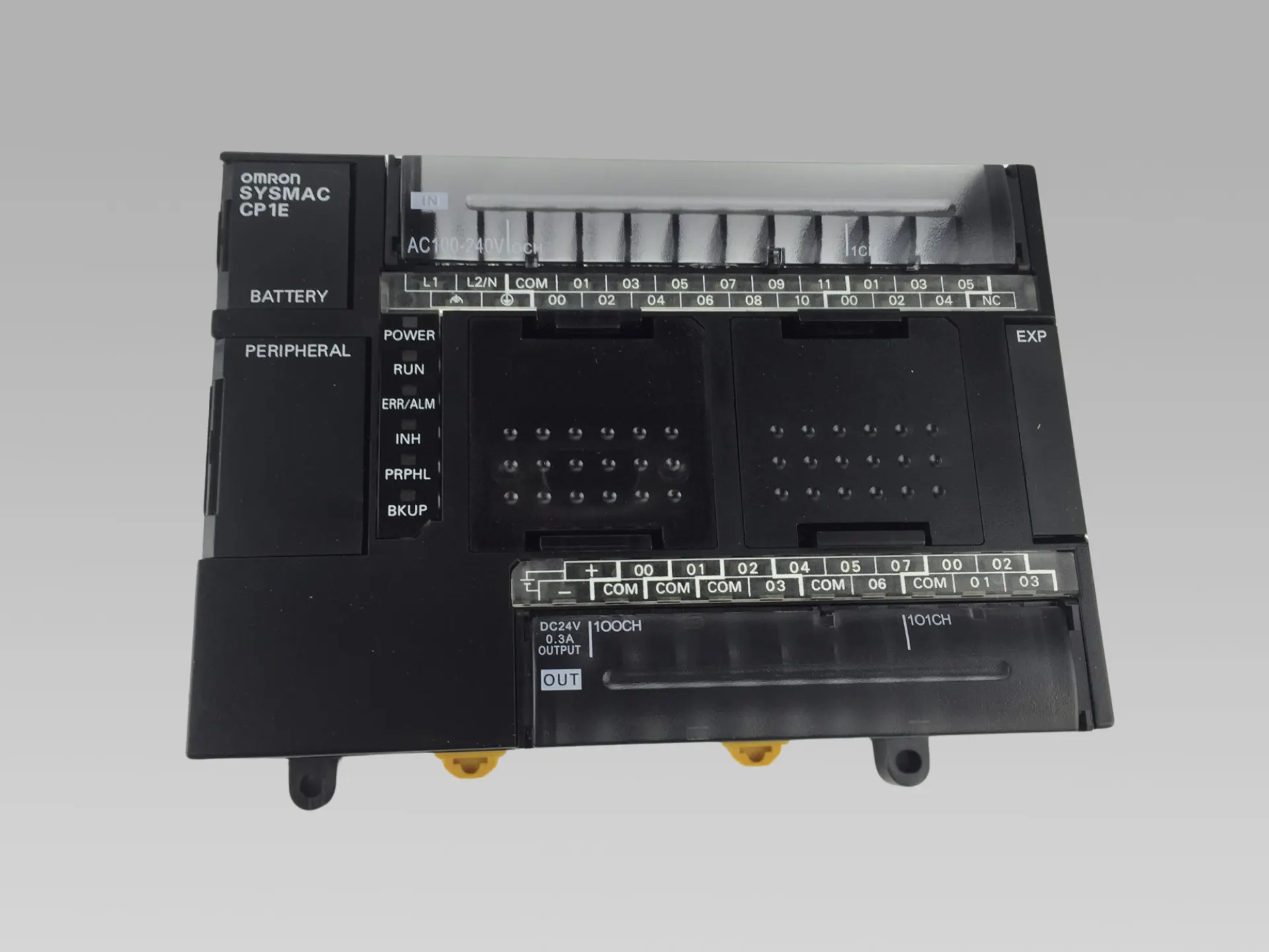
Omron
Their PLCs are well-regarded for flexibility and advanced control options, widely used in smart manufacturing. Browse All PLCs>>
Key Considerations When Selecting a PLC
Choosing the right PLC is crucial. Here are some principles to consider:
- I/O Requirements: Ensure the PLC can handle the necessary inputs and outputs for your application.
- Processing Power: Evaluate the speed and capacity of the CPU.
- Environmental Conditions: Choose a PLC that can withstand the operational environment.
- User Support: Ensure the manufacturer provides adequate technical support and resources.
- Ensure it meets functional requirements while offering the best price-performance ratio.
- Evaluate structural design, installation methods, functionality, response time, and system reliability.
Conclusion
In summary, understanding PLCs is essential for modern automation. They offer reliability, flexibility, and ease of installation, making them a cornerstone of industrial control systems.
Looking for new, original PLCs for your projects? At Kwoco, we stock the latest PLCs from top brands like Omron, Mitsubishi, and Schneider. Shop with confidence—fast shipping, guaranteed quality! Contact Now([email protected]).
Contact Us
Just fill out your name, email address, and a brief description of your inquiry in this form. We will contact you within 24 hours.
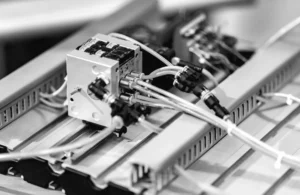
Why Your PLC Needs a Separate Power Supply
Why Your PLC Needs a Separate Power Supply Have you ever wondered why PLC systems often require a separate power
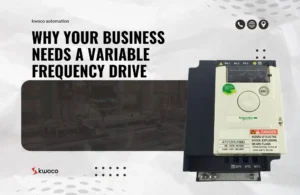
Why Your Business Needs a Variable Frequency Drive
Why Your Business Needs a Variable Frequency Drive When managing industrial operations, optimizing energy efficiency while maintaining performance is crucial.
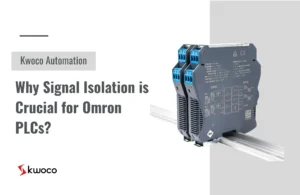
Why Signal Isolation is Crucial for Omron PLCs?
Why Signal Isolation is Crucial for Omron PLCs? In the world of industrial automation, signal interference is a silent killer.