CNC Router vs. Spindle: Which Upgrade is Right for Your Manufacturing Plant?
Table of Contents
1. What is a CNC Router and How Does It Work?
A CNC router is a computer-controlled cutting machine that uses a router—a powerful electric motor with a collet to hold cutting bits. It’s commonly used in woodworking and for cutting plastic and other soft materials.
The router is mounted on a gantry and moves along the X, Y, and Z axes, guided by a controller that interprets digital designs. CNC routers are known for their versatility and ease of use, making them popular among hobbyists and professionals alike.
For example, I have personal experience using a CNC router with a Makita router attached. I mainly cut plastic and wood, and I find that the router provides enough power for my needs.
Many CNC enthusiasts in the Onefinity CNC forum share similar experiences, often highlighting how a router can be a cost-effective solution for smaller projects. The Makita router I use, for instance, is relatively inexpensive and easy to replace, which is a big plus.
However, it’s worth noting that a router can be quite loud and may not be suitable for continuous operation over many hours. Despite these drawbacks, I appreciate the simplicity and affordability of using a router on my CNC machine.
If you are looking for a more powerful and precise solution, you might consider exploring our Mitsubishi Servo options.
2. What is a CNC Spindle and What Are Its Main Features?
A CNC spindle is a more robust and precise cutting tool designed for heavy-duty CNC machining. Unlike a router, a spindle is specifically engineered for continuous operation, making it ideal for industrial applications.
Spindles typically come in two variants: air-cooled and water-cooled. A water-cooled spindle uses a cooling system to maintain optimal operating temperatures, allowing it to run for hours at a time without overheating.
In my experience, the spindle’s ability to maintain a certain speed under load is a significant advantage. When I decided to upgrade to a spindle, I noticed a considerable improvement in the quality of my cuts, especially when working with harder materials.
Another aspect I appreciate is the reduced noise level. A water-cooled 80mm spindle runs much quieter than a typical woodworking router, which makes the workshop environment more pleasant.
This difference is crucial when the machine needs to run for hours, as it significantly reduces noise fatigue. For those interested in advanced automation, a spindle offers superior performance and reliability. Consider our Schneider PLC for seamless integration with your spindle.
3. Router vs Spindle: Key Differences in Performance and Applications
When comparing a router vs spindle, several key differences emerge that significantly impact their performance and suitability for various applications. Routers are generally more affordable and easier to set up, making them a popular choice for beginners and hobbyists.
They are well-suited for light-duty tasks, such as cutting wood and plastic. However, routers tend to be louder and less precise than spindles.
On the other hand, spindles are designed for high-precision and heavy-duty applications. They offer better speed control, allowing for more accurate cuts and the ability to work with a wider range of materials, including metals.
In my own experience, switching to a spindle allowed me to achieve much finer details in my projects. The automatic speed control feature ensures that the spindle maintains a constant RPM, even under varying loads, which is crucial for consistent results.
Additionally, spindles tend to be quieter and more durable, making them ideal for continuous operation in industrial settings.
While the initial investment in a spindle is higher, the long-term benefits in terms of performance and reliability often outweigh the costs. If you are looking to enhance your production capabilities, our Omron PLC can provide the necessary control and precision.
Feature | Router | Spindle |
---|---|---|
Cost | Lower | Higher |
Noise Level | High | Low |
Precision | Lower | Higher |
Durability | Moderate | High |
Speed Control | Limited | Advanced (with VFD) |
Cooling | Air-cooled | Air-cooled or Water-cooled |
Applications | Light-duty, Wood, Plastic | Heavy-duty, Metals, Wood, Plastic |
Maintenance | Frequent brush replacement | Less frequent, longer lifespan |
Continuous Use | Not ideal for extended periods | Designed for continuous operation |
Initial Setup | Easier | More complex |
Power | Typically lower (e.g., 1-2 HP) | Higher (e.g., 1.5kW, 2.2kW) |
Collet Types | Limited options (e.g., 1/4″, 1/2″) | Wide range (e.g., ER11, ER20, ER25) |
RPM Range | Fixed or limited variable speeds | Wide range, precisely controlled by VFD |
Vibration | Higher | Lower |
Heat Generation | Higher | Lower (especially water-cooled) |
Weight | Lighter | Heavier |
Common Brands | Makita, Bosch, Dewalt | HSD, Colombo, Chinese brands |
Use Cases | Hobbyist projects, small workshops | Industrial applications, large-scale production |
4. Why Choose a Router for Your CNC Machine?
Choosing a router for your CNC machine can be a practical decision, especially if you’re just starting or have specific needs that align with its capabilities. Routers are typically more affordable than spindles, making them an attractive option for hobbyists or small businesses with limited budgets.
They are also simpler to set up and use, which can be a significant advantage if you’re new to CNC machining.
In my early days of CNC work, I used a Makita router mounted on my machine. It was a cost-effective solution that allowed me to learn the basics of CNC without a significant financial investment.
The router was perfect for cutting softer materials like wood and plastic, and I could easily find replacement parts at local hardware stores. Many users on the Onefinity CNC forum share similar positive experiences, often recommending a router as a starting point.
Moreover, a router is much lighter than a spindle, which can reduce the strain on your CNC machine’s stepper motors and z-axis. This can be particularly beneficial if you have a smaller or less robust machine.
However, it’s important to remember that routers are not designed to run for hours at a time, and their noise level can be a drawback in some environments.
5. When Should You Upgrade to a Spindle?
Deciding to upgrade to a spindle is a significant step that can greatly enhance the capabilities of your CNC machine. In my experience, the best time to consider this upgrade is when you need to work with harder materials, require higher precision, or plan to run your machine for extended periods. A spindle offers superior performance in these areas compared to a router.
The VFD (Variable Frequency Drive) that controls the spindle ensures that I can maintain a certain speed under load, which is crucial for achieving consistent results.
Another factor to consider is the noise level. Spindles tend to run much quieter than routers, which can be a significant advantage in a busy workshop. Additionally, the cooling system in a water-cooled spindle ensures that the machine can run for hours without overheating.
This reliability and performance boost make a spindle a worthwhile investment for serious CNC users. Also, do not forget that we have a great option for you, Mitsubishi PLC.
6. How Does a VFD Enhance Spindle Performance?
A Variable Frequency Drive (VFD) is a critical component that significantly enhances the performance of a CNC spindle. It allows for precise control over the spindle’s speed, which is essential for optimizing cutting performance and achieving high-quality results. In my experience, using a VFD has transformed the way I work with my CNC machine.
With a VFD, I can adjust the spindle speed to match the specific requirements of different materials and cutting tools. For example, when working with harder materials, I can set the spindle to a lower RPM to prevent overheating and tool wear.
Conversely, for softer materials, I can increase the speed to improve efficiency. This level of control is not possible with a standard router, which typically operates at a fixed speed.
Moreover, a VFD provides the ability to start and stop the spindle gradually, reducing the mechanical stress on the machine. This feature, known as soft start, prolongs the lifespan of the spindle and other components. The precise control offered by a VFD makes it an indispensable tool for anyone looking to maximize the performance of their CNC spindle.
7. Air Cooled vs Water Cooled Spindles: Which is Better?
Choosing between an air-cooled and water-cooled spindle is an important decision that depends on your specific needs and operating environment. Both types have their advantages and disadvantages, and understanding these can help you make the right choice for your CNC machine.
Air-cooled spindles rely on a built-in fan to dissipate heat. They are generally simpler to install and maintain since they don’t require an external cooling system. In my early days, I considered an air-cooled spindle due to its simplicity.
However, they can be noisier and less effective at cooling compared to water-cooled options, especially during prolonged use.
Water-cooled spindles, on the other hand, use a liquid coolant circulated through the spindle to maintain optimal operating temperatures.
The main advantage of a water-cooled spindle is its ability to operate at lower temperatures, which reduces noise and prolongs the spindle’s lifespan. If you prioritize continuous operation and a quieter work environment, a water-cooled spindle is the better choice. Our Proface HMI can help you monitor and control the temperature of your water-cooled spindle.
8. What Role Do Collets Play in CNC Machining?
Collets are essential components in CNC machining, serving as the interface between the spindle or router and the cutting tool. They are cylindrical sleeves that grip the shank of the cutting tool, ensuring it is held securely and concentrically during operation. The choice of collet can significantly impact the precision and quality of your cuts.
In my experience, using high-quality precision collets has made a noticeable difference in the accuracy of my work. ER20 collets, for example, are known for their excellent grip and minimal runout, which is the amount of wobble in the cutting tool. This precision is crucial when working on intricate designs or using small-diameter tools.
Collets come in various sizes to accommodate different tool shank diameters. It’s important to match the collet size to your cutting tool to ensure a secure fit.
Additionally, regular maintenance and proper tightening of the collet are necessary to maintain accuracy and prevent tool slippage. Using the right collets can enhance the performance of both routers and spindles, making them a vital part of any CNC setup.
9. How to Maintain Your CNC Router or Spindle for Optimal Performance
Maintaining your CNC router or spindle is crucial for ensuring optimal performance, longevity, and the quality of your work. Regular maintenance not only prevents unexpected breakdowns but also helps in achieving consistent and precise results.
From my experience, a well-maintained machine operates more efficiently and produces higher-quality outputs.
For routers, one of the primary maintenance tasks is regularly checking and replacing the brushes. Router brushes wear down over time, and replacing them is essential to maintain the motor’s performance.
Additionally, keeping the router clean from dust and debris is important, especially in a woodworking environment where sawdust can accumulate quickly.
When it comes to spindles, especially water-cooled ones, ensuring the cooling system is functioning correctly is paramount. I regularly check the coolant levels and ensure that the pump and hoses are in good condition.
For air-cooled spindles, it’s important to keep the fan and vents clean to ensure proper airflow. Additionally, periodically checking the collets for wear and ensuring they are properly tightened can prevent issues during operation.
Regular maintenance routines may seem time-consuming, but they are essential for the longevity and performance of your CNC machine. By taking care of your equipment, you ensure that it continues to perform at its best, producing high-quality results for years to come.
10. CNC Router vs Spindle: A Comprehensive Comparison for Manufacturing Plants
Choosing between a CNC router and a spindle is a critical decision for manufacturing plants, as it directly impacts production efficiency, product quality, and overall operational costs. Making the right choice requires a thorough understanding of each option’s capabilities, advantages, and limitations.
CNC routers are often favored for their affordability and ease of use. They are suitable for light to medium-duty tasks and are particularly effective for cutting materials like wood and plastic. In my early days, using a Makita router on my CNC machine allowed me to produce a variety of products without a significant initial investment.
However, routers are not designed for continuous, heavy-duty use and can be quite noisy.
On the other hand, spindles offer superior performance, precision, and durability. They are designed for continuous operation and can handle a wide range of materials, including metals.
Ultimately, the choice between a router and a spindle depends on your specific manufacturing needs. If your plant requires high precision, continuous operation, and the ability to work with a variety of materials, investing in a spindle is the best decision.
However, if your operations involve lighter-duty tasks and you are looking for a cost-effective solution, a router may suffice.
Frequently Asked Questions
The main difference is that a router is typically used for lighter-duty tasks and is more affordable, while a spindle is designed for heavy-duty, continuous operation and offers higher precision and better speed control.
While a router can technically cut some softer metals, it is not ideal for this purpose. Spindles are better suited for cutting metal due to their higher power, precision, and durability.
Water-cooled spindles offer several benefits, including quieter operation, the ability to run for extended periods without overheating, and a longer lifespan due to better temperature management.
Choosing the right collet involves matching the collet size to the diameter of your cutting tool’s shank. Using the correct size ensures a secure grip and accurate cuts.
Maintenance for a CNC spindle includes regularly checking the cooling system (for water-cooled spindles), ensuring proper airflow (for air-cooled spindles), and periodically inspecting and tightening the collets.
Power your projects with brand-new, original Omron, Mitsubishi, Schneider PLC – in stock, ready now!
Conclusion
- Routers are affordable and suitable for light-duty tasks, making them ideal for beginners and hobbyists.
- Spindles offer higher precision, better speed control, and are designed for continuous, heavy-duty operation.
- VFDs enhance spindle performance by allowing precise speed adjustments and gradual starts and stops.
- Water-cooled spindles provide quieter operation and better temperature management compared to air-cooled ones.
- Using the correct collets is crucial for ensuring accurate and secure cutting tool grip.
- Regular maintenance is essential for the longevity and optimal performance of both routers and spindles.
- The choice between a router and a spindle depends on your specific manufacturing needs, including the materials you work with and the required precision and durability.
By understanding these key points, you can make an informed decision that enhances your CNC machining capabilities and supports your manufacturing goals. Remember, investing in the right equipment is crucial for achieving high-quality results and maintaining a competitive edge in the industry.
If you need any components for your CNC machine, such as a high-quality Omron Sensor, feel free to contact us.
Contact Us
Just fill out your name, email address, and a brief description of your inquiry in this form. We will contact you within 24 hours.
You May Also Find These Topics Interesting
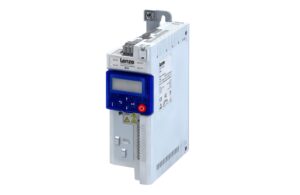
Lenze Drive Error Codes: How to Connect, Operate, and Fix Common Faults
This article provides a comprehensive guide to understanding, troubleshooting, and resolving common fault codes in Lenze drives. If you’re working in industrial automation, particularly with machinery and equipment factories or manufacturing plants, this guide will be an invaluable resource. We delve into the intricacies of Lenze drive error codes, offering practical solutions and expert insights to enhance your operational efficiency and minimize downtime. Understanding these error codes is essential for maintaining the reliability and longevity of your equipment.
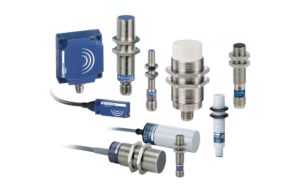
Inductive Sensors: Demystifying the Working Principle of Inductive Proximity Sensors
This article delves into the fascinating world of inductive sensors, explaining how they work, their various types, and their wide-ranging applications in industrial automation. Whether you’re a seasoned engineer or simply curious about these devices, this comprehensive guide will provide valuable insights into the technology that powers numerous industries, making it a worthwhile read for anyone seeking to understand the intricacies of modern sensing solutions.
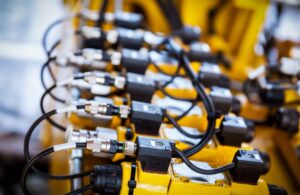
Essential Guide to Sensor Calibration for Industrial Accuracy
Sensor calibration is a fundamental part of industrial measurement, essential for ensuring accuracy, reliability, and safe operation in various process plants. Whether dealing with temperature, pressure, or flow, calibrated sensors provide critical data that helps maintain optimal control of industrial operations.