Unlocking the Power of VFDs in Industrial Applications
Table of Contents
What is a VFD and How Does It Work?
A Variable Frequency Drive (VFD) is a type of motor controller that drives an electric motor by varying the frequency and voltage supplied to the motor. But how exactly do VFDs work, and why are they essential in modern industrial applications?
Understanding the Basics of VFD Operation
At its core, a VFD controls the motor speed by adjusting the electrical frequency and voltage supplied to the AC motor. The main components of a VFD include:
- Rectifier: Converts incoming AC power to DC voltage.
- DC Bus: Smooths the converted DC voltage to a stable level.
- Inverter: Converts the DC voltage back to AC with variable frequency and voltage.
By modulating the output frequency and voltage, the VFD allows precise control over motor speed and torque, enabling motors to operate at variable speeds suitable for specific application requirements.
The Science Behind VFDs
VFDs work by:
- Adjusting the Frequency and Voltage: The VFD changes the frequency and voltage supplied to the motor, which in turn controls the speed of the motor.
- Pulse Width Modulation (PWM): Modern VFDs use PWM techniques with insulated gate bipolar transistors to create a simulated AC sine wave that drives the motor efficiently.
- Energy Efficiency: By matching motor speed to load requirements, VFDs help in reducing energy consumption and improving energy efficiency.
Why is Motor Speed Control Vital in Industrial Applications?
Controlling the motor speed is crucial for enhancing productivity, efficiency, and equipment longevity in various industrial applications.
Benefits of Motor Speed Control
- Energy Savings: Adjusting motor speed to match process demands leads to significant energy savings.
- Process Optimization: Precise speed control allows for better process control, improving product quality.
- Reduced Mechanical Stress: Soft starting reduces mechanical shock, extending the life of the electric motor.
Applications Requiring Speed Control
- Pumps and Fans: Variable speed operation adjusts flow rates without mechanical throttling.
- Conveyors: Controls the speed for synchronized processes.
- Mixers and Agitators: Adjusts speed for desired mixing levels.
How to Use a VFD in Your Application
Implementing a VFD involves careful consideration of your application requirements and understanding how to integrate the VFD into your system.
Selecting the Right Type of VFD
- Motor Compatibility: Ensure the VFD is suitable for the type of motor you’re using (e.g., AC induction motor, DC motor).
- Load Characteristics: Identify if your application requires constant or variable torque.
- Environmental Factors: Consider temperature, humidity, and dust levels.
Add Your Heading Text Here
- Proper Wiring: Connect the VFD correctly to the power supply and motor windings.
- Programming Parameters: Set the appropriate frequency and voltage settings for your application.
- Safety Measures: Include protective features like overload protection and emergency stop functions.
Using a VFD for Energy Efficiency
- Adjusting the Frequency and Voltage: Tailor the frequency output to match load requirements, thus optimizing energy consumption.
- Reducing Peak Power Demand: Soft starts reduce peak currents, lowering electrical demand charges.
Frequently Asked Questions
VFDs are primarily designed for AC motors, especially AC induction motors. However, some VFDs can control DC motors or other types of motors with proper configuration.
VFDs reduce energy consumption by operating motors at the necessary speed for the application, rather than running at full speed continuously. This is especially effective in applications like pumps and fans.
The main components include a rectifier, DC bus, and inverter. Together, they adjust the voltage and frequency supplied to the motor.
Yes, VFDs can protect motors from issues like overvoltage, undervoltage, overloads, and can improve the power factor of the motor.
Installation can be straightforward if you follow the vfd manufacturer’s guidelines and ensure compatibility with your system.
Power your projects with brand-new, original Omron, Mitsubishi, Schneider PLC – in stock, ready now!
Applications of VFDs in Industrial Settings
VFDs are versatile and are used across various industries due to their ability to enhance process control and efficiency.
Common VFD Applications
- HVAC Systems: Controlling fans and pumps for climate control.
- Manufacturing: Adjusting speeds of conveyors, mixers, and machine tools.
- Water and Wastewater: Managing pumps to regulate flow and pressure.
- Mining and Metals: Operating crushers and grinding mills.
VFDs in Pumps
- Energy Savings: Significant reduction in power usage.
- Extended Equipment Life: Less wear on mechanical components.
The Future of VFDs in Energy Efficiency
As industries strive for sustainability, VFDs play a crucial role in achieving energy efficiency and reducing operational costs.
Innovations in VFD Technology
- Enhanced Control Algorithms: Improved precision in motor control.
- Integration with IoT: Remote monitoring and optimization.
- Energy Regeneration: Feeding energy back into the grid during deceleration.
Why VFDs are Essential
- Environmental Impact: Lower energy consumption reduces carbon footprint.
- Cost Savings: Decreased energy bills and maintenance costs.
- Process Improvement: Better control leads to higher quality products.
Conclusion
Understanding how to leverage VFDs in your industrial applications can lead to substantial benefits in terms of energy savings, process control, and equipment longevity. By adjusting the frequency and voltage, VFDs offer precise control over motor speed and torque, making them invaluable tools in modern industrial automation.
- VFDs allow for precise control over motor speed, enhancing efficiency.
- Implementing VFDs leads to energy savings and reduced operational costs.
- Proper installation and setup are crucial for optimal VFD performance.
- VFDs are suitable for a wide range of industrial applications.
- Regular maintenance ensures VFD longevity and reliability.
Contact Us
Just fill out your name, email address, and a brief description of your inquiry in this form. We will contact you within 24 hours.
You May Also Find These Topics Interesting
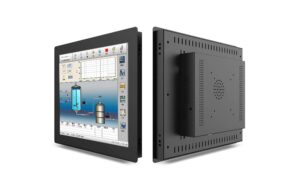
LCD, Digitizer, or Touchscreen Woes? Find the Perfect Industrial Display Solution!
Is your industrial equipment’s display cracked, unresponsive, or simply outdated? Understanding the difference between LCDs, digitizers, and touchscreens is crucial for effective repairs and upgrades. This article dives deep into the world of industrial displays, helping you diagnose problems, choose the right replacement parts, and optimize your machinery for peak performance. We will walk you through what is the digitizer, what is lcd, what is the touchscreen! It’s time to stop guessing and start fixing!
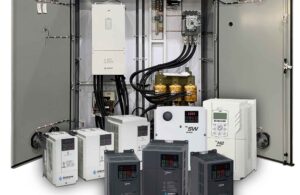
Capacitor Reforming: Bringing Your VFD Back to Life After Storage
This article explores the critical process of capacitor reforming for Variable Frequency Drives (VFDs) that have been in storage. If you’re in the machinery and equipment manufacturing industry or provide factory solutions, understanding this process is crucial to prevent downtime and ensure the longevity of your equipment. We’ll delve into why capacitor reforming is necessary, how it works, and what steps you can take to safeguard your VFDs.
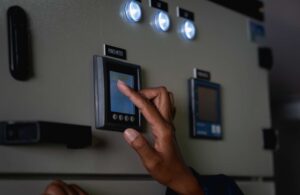
PLC Analog Input & Output: Testing & Troubleshooting Guide
Programmable Logic Controllers (PLCs) are the backbone of many industrial automation systems. They enable precise control over machines and processes, relying heavily on inputs and outputs (I/O) to communicate with external devices.