What is DCS? A Guide to Distributed Control Systems
Table of Contents
Understanding Distributed Control Systems (DCS)
A Distributed Control System (DCS) is an automated control system that monitors and controls industrial processes by decentralizing control functions throughout the system. Unlike traditional centralized control systems, a DCS distributes control elements across various locations of a plant or process area.
What Makes Up a DCS?
The components of a DCS include:
- Control Units: Responsible for executing control algorithms and managing control loops.
- Human-Machine Interface (HMI): Allows operators to monitor and control processes.
- Communication Networks: Facilitates data exchange between the systems.
- Data Acquisition Systems: Collects and processes data from sensors and instruments.
These components work together to provide real-time monitoring and control, ensuring efficient control of industrial processes.
DCS Architecture: How Does It Work?
The architecture of a distributed control system is designed to distribute control tasks across multiple controllers and networks. This distributed architecture enhances system reliability and performance by eliminating single points of failure.
Key Features of DCS Architecture
- Distributed Control Functions: Control elements are distributed throughout the system, allowing for real-time monitoring and control.
- Integrated Systems: DCS can be integrated with other systems like SCADA and PLCs for comprehensive control.
- Redundancy: Provides backup systems to ensure continuous operation even if one component fails.
Applications of DCS in Industrial Processes
DCS systems are widely used in industries that require precise control and monitoring of processes, such as:
- Chemical and Petrochemical Plants
- Power Generation Facilities
- Oil and Gas Industries
- Pharmaceutical Manufacturing
Why Use DCS in These Industries?
- Efficient Control: DCS allows for efficient control of production systems.
- Real-Time Monitoring: Operators can monitor and control processes in real-time.
- Safety: Enhances the safety of operations through automated control and monitoring.
- Scalability: Easily scalable to accommodate expanding industrial processes.
By distributing control tasks, DCS enables operators to monitor and control complex industrial processes effectively.
Benefits of Implementing a DCS
Implementing a Distributed Control System offers numerous benefits:
Enhanced Reliability and Performance
- Redundancy: Reduces the risk of system failures.
- Distributed Control: Minimizes the impact of localized issues on the entire system.
Improved Control and Monitoring
- Real-Time Data: Provides operators with real-time data using control algorithms.
- Advanced Control Strategies: Supports advanced control methods for optimized processes.
Integration with Other Systems
- Seamless Integration: DCS can be integrated with PLCs, SCADA systems, and management systems.
- Data Sharing: Facilitates data exchange between the systems for better decision-making.
DCS vs. PLC: What's the Difference?
While both DCS and PLCs (Programmable Logic Controllers) are used in industrial automation and control applications, they serve different purposes.
Distributed Control System (DCS)
- Complex Processes: Ideal for continuous, complex processes requiring precise control.
- Distributed Architecture: Control functions are distributed throughout the system.
- Integrated Control and Monitoring: Combines control and monitoring in one system
Programmable Logic Controller (PLC)
- Discrete Control: Best for discrete control applications like assembly lines.
- Centralized Control: Typically uses a centralized control system.
- Scalability: Easier to scale for smaller applications.
Frequently Asked Questions
A DCS is used to control industrial processes that require precise and reliable control, such as in chemical plants, power generation, and oil refineries. It distributes control functions across the system for efficient control and monitoring.
While both are used for control and monitoring, a DCS is designed for complex, continuous processes with integrated control functions, whereas SCADA systems are used for remote monitoring and control over vast geographic areas.
Yes, a DCS can be integrated with other systems like PLCs, SCADA, and management systems to provide a comprehensive view of the entire process and enhance control strategies.
The main components of a DCS include control units, human-machine interfaces (HMIs), communication networks, and data acquisition systems.
DCS is essential because it provides precise control, real-time monitoring, and improved system reliability, which are crucial for efficient and safe industrial automation and control applications.
Power your projects with brand-new, original Omron, Mitsubishi, Schneider PLC – in stock, ready now!
Conclusion
In summary, a Distributed Control System (DCS) is a vital component in modern industrial automation and control. It allows for real-time monitoring and control of complex industrial processes by distributing control tasks throughout the system. By integrating with other systems and providing advanced control strategies, DCS enhances efficiency, reliability, and safety in various industrial applications.
- DCS Definition: An automated control system with distributed control functions.
- Architecture: Designed to distribute control elements for enhanced reliability.
- Applications: Used in industries requiring precise control of continuous processes.
- Benefits: Improves efficiency, reliability, and integration with other control systems.
- DCS vs. PLC: DCS is for complex processes; PLC is for discrete control applications.
For more information on related automation products, check out our pages on PLC, Mitsubishi, and Schneider PLC.
Contact Us
Just fill out your name, email address, and a brief description of your inquiry in this form. We will contact you within 24 hours.
You May Also Find These Topics Interesting
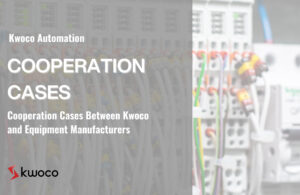
Cooperation Cases Between Kwoco and Equipment Manufacturers
Cooperation Cases Between Kwoco and Equipment Manufacturers KWOCO has become the preferred supplier for an increasing number of equipment manufacturers.
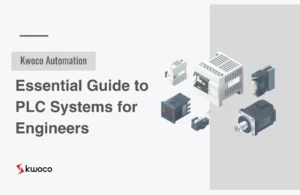
Essential Guide to PLC Systems for Engineers
Essential Guide to PLC Systems for Engineers Do you want to streamline your industrial automation processes but are unsure where
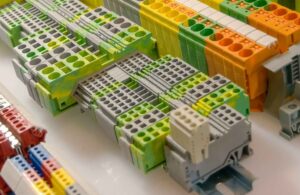
Choosing the Right Terminal Block: A Complete Guide
Terminal blocks are essential components in electrical systems, ensuring organized and secure connections between multiple wires. These devices come in a variety of types and configurations, each suited to specific applications and environments.