Decoding the Difference Between Servo Motor and Spindle Motor in CNC Applications
Table of Contents
What's the Primary Difference Between Servo Motors and Spindle Motors?
Servo motors and spindle motors are both essential for CNC machine operations, but they serve distinct purposes. A servo motor is mainly responsible for precise position control, moving the machine’s axes to exact locations. In contrast, a spindle motor powers the rotation of the cutting tool, enabling material removal. Think of a servo motor as the “positioner” and a spindle motor as the “cutter.”
Servo motors are designed for accuracy and responsiveness. They use feedback devices like encoders to monitor and adjust their position in real-time, ensuring movements are precise to the micrometer. This makes them ideal for tasks requiring intricate detailing and fine finishes. Spindle motors, on the other hand, are built for speed and power.
They can operate at high RPMs (Revolutions Per Minute) to facilitate efficient cutting, drilling, and milling. Spindle motors often feature robust cooling systems to manage the heat generated during prolonged high-speed operation. Check Servo offers if you are looking for it.
How Do Servo Motors Achieve Precise Position Control?
Servo motors are the workhorses behind the precise movements in a CNC machine. These motors are part of a sophisticated servo system that includes the motor, a controller, and a feedback device, typically an encoder. This closed-loop system allows for unparalleled accuracy in positioning.
The encoder plays a crucial role by providing continuous feedback on the motor’s position and speed to the controller. When a command is given, the controller compares the desired position with the actual position reported by the encoder. It then adjusts the motor’s operation to correct any deviations, ensuring precise position control.
This dynamic feedback loop is what allows servo motors to move to the exact required position, making them essential for detailed work where accuracy is paramount. The motor is used to detect the position of the motor rotor. Servo motors are used in various types of CNC machine tools.
What are the Key Characteristics of Spindle Motors?
Spindle motors are designed to drive the spindle of the machine tool at high speeds, which is critical for cutting, milling, and other machining processes. These motors are typically asynchronous motors or, in some cases, synchronous motors, optimized for maintaining high speeds under varying loads. The spindle motor is a precision asynchronous motor.
One of the defining features of spindle motors is their ability to operate across a wide range of speeds, from very low RPMs for heavy cutting to extremely high speeds for fine finishing work. This speed range is achieved through sophisticated speed regulation mechanisms, often involving a spindle drive that adjusts the power supply to the motor.
Spindle motors also feature robust construction to withstand the forces involved in cutting operations and advanced cooling systems to dissipate the heat generated at high speeds. Spindle motors and servo motors provide high requirements for motion control. The motor is a precision asynchronous motor. The spindle motor is mainly responsible for the spindle load. The speed of the spindle motor varies.
Table: Comparison of Servo and Spindle Motors
Feature | Servo Motor | Spindle Motor |
---|---|---|
Primary Use | Position control, axis movement | Tool rotation, material removal |
Speed | Variable, often lower RPM | High RPM |
Torque | High torque at low speeds | Consistent torque across speed range |
Precision | Extremely high, micrometer level | High, suitable for cutting operations |
Feedback | Encoder for position and speed feedback | May have speed feedback, less focus on position |
Control | Closed-loop control system | Open or closed-loop, focused on speed control |
Cooling | Typically air-cooled | Often liquid-cooled for high-speed operation |
Application | Moving machine parts to precise locations | Driving the cutting tool in CNC machines |
What are the Applications for Servo and Spindle Motors in CNC Machines?
In a CNC machine, servo motors and spindle motors work in tandem to perform complex machining tasks. Servo motors handle the movement of the axes (X, Y, Z, and any additional axes), precisely positioning the workpiece or tool.
Common applications include moving the table, adjusting the height of the cutting head, and rotating multi-axis components. This precision is crucial for operations like engraving, contouring, and creating intricate designs.
Spindle motors, on the other hand, power the rotation of the cutting tool. This rotation is essential for operations like milling, drilling, and turning.
The high speed and constant torque output of spindle motors make them suitable for cutting through various materials, from soft plastics to hard metals. Together, these motors enable CNC machines to perform a wide array of tasks with high efficiency and precision.
The range of speed regulation functions is very wide. Spindle motors and servo motors are used to drive the spindle of the machine tool. A spindle motor is generally an asynchronous motor.
Why is the Difference in Speed Range Significant Between the Two Motors?
The speed range is a critical factor that differentiates servo motors from spindle motors. Servo motors typically operate at lower speeds but offer high torque, which is essential for precise positioning.
They can quickly accelerate and decelerate, allowing for rapid changes in direction and speed while maintaining accuracy. This makes them ideal for tasks requiring frequent starts and stops or intricate movements.
Spindle motors, in contrast, are designed for high-speed operation. They need to maintain consistent speeds, even under load, to ensure smooth and efficient cutting.
The wide speed range of spindle motors allows for versatility in machining operations, from slow, heavy cuts to fast, fine finishes. The ability to adjust the speed is crucial for optimizing the cutting process based on the material and the type of operation being performed. The area between the rated speed of the spindle is the constant power area.
Frequently Asked Questions
An encoder provides feedback on the motor’s position and speed, allowing for precise control and adjustments in a closed-loop system.
While a spindle motor can technically move an axis, it is not designed for precise positioning and lacks the feedback mechanisms found in servo motors.
A spindle motor is better suited for high-speed cutting due to its ability to maintain high RPMs under load.
The controller receives feedback from the encoder and adjusts the motor’s operation to match the desired position and speed.
Regular maintenance includes checking for wear and tear, ensuring proper lubrication, and monitoring the cooling system for spindle motors.
Power your projects with brand-new, original Omron, Mitsubishi, Schneider Servo – in stock, ready now!
Conclusion
- Servo motors excel in precise position control, making them ideal for detailed work. If you’re on the hunt for a reliable Mitsubishi Servo, you know that precision and performance are non-negotiable.
- Spindle motors are designed for high-speed tool rotation, crucial for cutting and milling operations. Omron PLC is a device often used together with spindle motors.
- Encoders provide essential feedback for servo motor accuracy.
- Spindle motors often require advanced cooling systems due to high-speed operation. Are you considering a Schneider HMI for your next project? There are many good options.
- The combination of servo and spindle motors enables the versatility and precision of CNC machines.
- Understanding the differences between these motors is essential for optimizing CNC machine performance.
- Regular maintenance ensures the longevity and reliability of both motor types. Choosing the right Proface HMI can significantly enhance user interaction and control in your automation projects.
- Technological advancements continue to enhance the capabilities of servo and spindle motors. For those in need of reliable industrial components, exploring Mitsubishi PLC options might be the next step in ensuring your machinery runs smoothly.
Contact Us
Just fill out your name, email address, and a brief description of your inquiry in this form. We will contact you within 24 hours.
You May Also Find These Topics Interesting
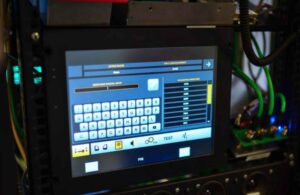
Understanding HMI: Revolutionizing Your Manufacturing Interface
The Human Machine Interface (HMI) is your window into the complex world of industrial automation. It’s the interface that allows operators to interact with machines and PLC systems, providing real-time data and control. In this article, we’ll delve into the world of HMIs, explore their functionality, and understand how they can significantly benefit your manufacturing operations.
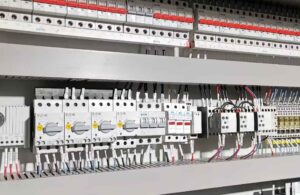
Proximity sensor vs Photoelectric sensor
This article delves into the fascinating realm of proximity sensors and photoelectric sensors, exploring their functionalities, differences, and applications. Whether you’re a seasoned engineer in a machinery and equipment factory or a solution provider seeking the best automation components, understanding these sensor types is crucial. As an industrial automation and control products manufacturing plant, we’re here to illuminate the intricacies of these vital components, ultimately guiding you toward informed decisions for your projects.
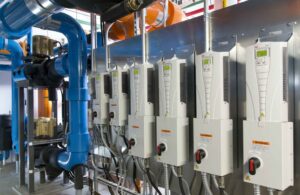
Comprehensive Guide to DC Motor and Controller
This comprehensive guide delves into the intricacies of DC drives, essential components in various industrial automation and motion control systems. Understanding DC drives is crucial for anyone involved in designing, operating, or maintaining systems that require precise control of motor speed and torque. Whether you are looking to enhance your knowledge or choose the right DC drive for your application, this guide provides the insights you need.