Everything You Need to Know About Pneumatic System Components
Table of Contents
Pneumatic System Outline
What is a Pneumatic System and How Does It Work?
A pneumatic system uses compressed air to transmit and control power. The air compressor, a crucial component, pressurizes atmospheric air, which is then filtered and regulated to operate various pneumatic components like valves and cylinders.
These system components work together to perform mechanical work in a wide array of industrial applications. Mitsubishi PLC are often used to control these systems, especially in complex operations.
Pneumatic systems work by applying pressurized air to move a cylinder or power a tool. The flow of air is controlled by valves that direct the compressed air to the appropriate part of the system.
The efficiency and reliability of pneumatic systems make them a popular choice in many industries. Pneumatic systems are used to operate everything from small hand tools to massive industrial machinery.
What Are the Key Components of Pneumatic Systems?
The key components of pneumatic systems include the compressor, valves, cylinders, and an array of pneumatic components that ensure the smooth operation of the system. An air compressor increases the pressure of the air, which is then stored and used to power the system.
Valves control the direction and flow of air, while cylinders convert pneumatic power into mechanical movement. Understanding these key components is crucial to grasping how a pneumatic system functions.
Pneumatic system components are designed to work in harmony to achieve desired mechanical outputs. The compressor generates the compressed air necessary for the system to function. The pneumatic system uses compressed air to perform work by actuating cylinders and other pneumatic devices.
This careful orchestration of components of a pneumatic system allows for precise control and efficient power transmission. For example, in manufacturing, pneumatic actuators are often used to move parts along an assembly line. Omron Sensors play a vital role in detecting the position of these parts.
What Are the Applications of Pneumatic Systems?
Pneumatic systems are widely used across various industries due to their versatility and reliability. One of the most common applications of pneumatic systems is in manufacturing, where they are employed to power assembly lines, operate machinery, and handle materials.
Pneumatics are used in everything from packaging and food processing to automotive assembly and heavy machinery operations.
Beyond manufacturing, pneumatic systems find applications in sectors like construction, transportation, and even dentistry. Pneumatic tools such as drills, hammers, and jackhammers are essential in construction.
In transportation, pneumatic systems power braking systems in trains and buses. Dentists use pneumatic drills for various procedures, showcasing the wide-ranging application of pneumatics in our daily lives. Mitsubishi Servo systems are also used in conjunction with pneumatics to provide precise motion control.
What Are the Advantages of Pneumatic Systems Over Hydraulic Systems?
When comparing pneumatic and hydraulic systems, it’s evident that both have their unique advantages. However, pneumatic systems often have the edge in specific applications. One key advantage is that pneumatic systems use air, which is readily available and non-toxic.
This makes them cleaner and safer to operate, particularly in industries like food processing where contamination is a significant concern.
Moreover, pneumatic systems are typically simpler and less expensive to maintain than hydraulic systems. The components used in pneumatic systems, such as valves and cylinders, are generally more affordable and easier to replace.
This simplicity also makes pneumatic systems more reliable, with fewer points of failure. Additionally, air is less viscous than hydraulic fluid, allowing for faster response times in pneumatic systems. Proface HMI can be integrated to monitor and control these systems, enhancing their efficiency.
A Brief History of Pneumatics
The history of pneumatics dates back to ancient times. Pneumatics is the science that deals with the mechanical properties of air and other gases. Early civilizations used bellows to create airflow for various purposes, including blacksmithing and playing musical instruments.
The modern application of pneumatics began in the 19th century with the development of the first pneumatic tools and systems. During the Industrial Revolution, the need for more efficient and powerful machinery led to the increased use of pneumatics.
In the 20th century, pneumatic technology advanced rapidly. Innovations in compressor technology and the development of more sophisticated valves and cylinders expanded the capabilities of pneumatic systems.
Today, pneumatic systems are integral to many industrial processes, offering a reliable and efficient means of power transmission and control. The continuous evolution of pneumatic system components ensures that pneumatic systems remain at the forefront of industrial automation. For instance, the development of Omron HMI has greatly improved the user interface for controlling these systems.
Frequently Asked Questions
Pneumatic systems use compressed air to transmit power, while hydraulic systems use liquid, usually oil. Pneumatic systems are generally cleaner, faster, and more cost-effective, whereas hydraulic systems can generate higher forces and are better suited for heavy-duty applications.
The basic components of a pneumatic system include an air compressor, a storage tank, valves, cylinders (also known as actuators), filters, regulators, and lubricators. Each component plays a vital role in ensuring the efficient operation of the system. Pneumatic components such as valves are used to control the flow of air within the pneumatic system.
Pneumatic systems are favored for their cleanliness, safety, and ease of maintenance. They are particularly useful in environments where the risk of contamination must be minimized, such as in food processing and pharmaceuticals. Additionally, the speed and responsiveness of pneumatic systems make them ideal for applications requiring quick, repetitive movements.
Maintenance of a pneumatic system involves regular checks of all components to ensure they are functioning correctly. This includes inspecting and replacing filters, checking for leaks, ensuring proper lubrication, and monitoring the compressor’s performance. Regular maintenance helps prolong the life of the system and prevent unexpected breakdowns.
Yes, pneumatic systems can be designed to operate in harsh environments. By using robust materials and protective enclosures, pneumatic components can withstand extreme temperatures, corrosive substances, and high levels of dust and moisture. This adaptability makes pneumatic systems suitable for various industrial settings.
Power your projects with brand-new, original Omron, Mitsubishi, Schneider PLC – in stock, ready now!
Conclusion
- Pneumatic systems use compressed air to transmit and control power, offering a clean and efficient solution for many industrial applications.
- Key components include the compressor, valves, and cylinders, each playing a crucial role in the system’s operation.
- Pneumatic systems are used across various industries, including manufacturing, construction, transportation, and even dentistry.
- Compared to hydraulic systems, pneumatic systems are often simpler, cleaner, and more cost-effective.
- The history of pneumatics showcases a long evolution from ancient bellows to modern, sophisticated systems used worldwide.
- Regular maintenance is essential to ensure the longevity and reliability of pneumatic systems.
This comprehensive overview provides a clear understanding of pneumatic systems, from their basic principles to their advanced applications. Whether you are an industry veteran or a newcomer, this guide illuminates the enduring importance of pneumatics in modern technology. Schneider PLC are frequently used to enhance the control and efficiency of these systems.
Contact Us
Just fill out your name, email address, and a brief description of your inquiry in this form. We will contact you within 24 hours.
You May Also Find These Topics Interesting
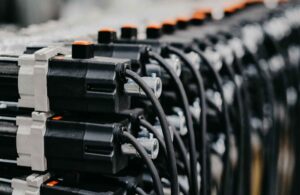
What is The Purpose of a Servo Motor?
Servo motors have become indispensable in modern industrial applications, offering unparalleled precision and control. Whether it’s in robotics, automation, or any system requiring exact movements, servo motors are at the heart of it all. In this article, we’ll explore the purpose of servo motors, their types, and why they are crucial in various industries today.
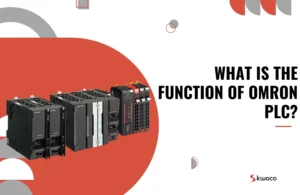
What is the Function of Omron PLC?
What is the Function of Omron PLC? Are you tired of dealing with unreliable control systems that cause delays and
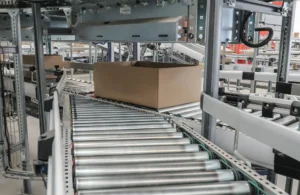
What do Photoelectric Sensors Detect?
You might wonder, what exactly do photoelectric sensors detect?
Simply put, photoelectric sensors detect the presence or absence of an object using light. They are essential components in automation, used across industries to ensure processes run smoothly and efficiently.