What is the Difference Between PLC, SCADA, and DCS?
PLC, SCADA, and DCS each play different roles. Understanding their differences helps optimize your production processes. PLC is a Programmable Logic Controller used to control specific operations; DCS is a Distributed Control System suitable for controlling an entire factory; while SCADA is software used for monitoring and data acquisition.
Table of Contents
Understanding these differences can help you make more informed decisions and enhance your business efficiency. Let’s delve deeper into the specific functions and application scenarios of each system.
How Well Do You Understand PLC, SCADA, and DCS?
PLC (Programmable Logic Controller)
A PLC is a digital computer device specifically designed for industrial process automation. It controls connected output devices through input programs and is widely used in medium to large-scale applications. PLCs are typically used in systems with fewer input and output points, suitable for controlling hundreds of inputs and outputs.
DCS (Distributed Control System)
A DCS is a dedicated system used for continuous or batch manufacturing processes. It consists of multiple powerful PLCs that can control the entire factory’s automation process. When PLCs alone are insufficient to meet the control demands of the entire automation process, a DCS becomes essential as it supports more inputs and outputs.
SCADA (Supervisory Control and Data Acquisition)
SCADA is a design software used for industrial control systems. It allows operators to view the entire process through a graphical interface and remotely access and control local control modules. For example, Omron PLC uses CX-Supervisor as its SCADA software, while Mitsubishi PLC uses Uniware.
SCADA systems not only monitor the process parameters of the entire factory but also allow users to change preset values, enabling more flexible control.
More Related Questions
Which is More Suitable for Small and Medium-Sized Enterprises: PLC or DCS?
For small and medium-sized enterprises, PLCs are usually more suitable because they are cost-effective and easy to deploy. On the other hand, DCS is ideal for large enterprises that require highly integrated and complex control systems.
What Are the Main Advantages of SCADA Systems?
The main advantages of SCADA systems lie in their powerful data acquisition and monitoring capabilities. They can monitor the entire factory’s operational status in real-time, improving response speed and decision-making efficiency.
How to Maintain and Care for PLCs?
To ensure the stable operation of PLCs, regularly check the power supply and connection ports, update software versions, back up programs promptly, and keep the equipment environment clean to prevent dust and moisture from affecting the PLC.
How Is the Security of SCADA Systems Ensured?
The security of SCADA systems can be guaranteed by implementing multi-layered protection strategies, including firewalls, encrypted communications, access controls, and regular security audits. These measures help prevent unauthorized access and potential cyber-attacks.
What Factors Should Be Considered When Choosing a DCS?
When selecting a DCS, consider the system’s scalability, compatibility, vendor support, response time, and system stability to ensure it can meet both current and future production needs.
Power your projects with brand-new, original Omron, Mitsubishi, Schneider PLC – in stock, ready now!
Conclusion
Understanding the differences between PLC, SCADA, and DCS is key to optimizing industrial automation processes. Choosing the right system can not only enhance production efficiency but also ensure quality and reliability. If you have any questions, feel free to contact us at [email protected]. We are committed to providing you with professional technical support and solutions.
Contact Us
Just fill out your name, email address, and a brief description of your inquiry in this form. We will contact you within 24 hours.
You May Also Find These Topics Interesting
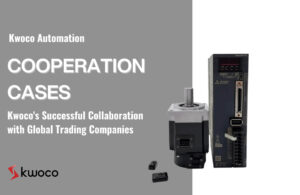
Kwoco’s Successful Collaboration with Global Trading Companies
Kwoco’s Successful Collaboration with Global Trading Companies In today’s global market, the reliability of the supply chain directly influences the
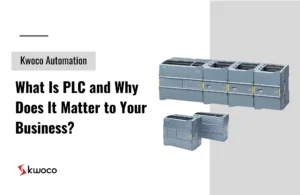
What Is PLC and Why Does It Matter to Your Business?
What Is PLC and Why Does It Matter to Your Business? Feeling overwhelmed by the constant changes in industrial automation
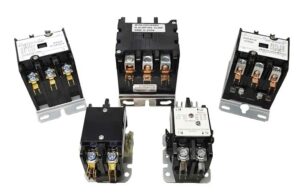
What is a Magnetic Contactor and What is it Used For?
Magnetic contactors are essential components in industrial automation and electrical control systems. They play a crucial role in managing high-power loads and ensuring the safe operation of machinery. This article offers a comprehensive look at magnetic contactors, explaining their functionality, types, and applications. It also covers how these devices contribute to the efficiency and reliability of industrial processes.