PLC Counter Programming: A Complete Guide for Automation 2024
From basic concepts to advanced implementations, we’ll explore how counters can enhance your control systems and improve manufacturing efficiency.
Table of Contents
What Are PLC Counters and Why Are They Essential in Automation?
In the world of programmable logic controllers, counters are fundamental building blocks that keep track of events or occurrences in an automated system. These powerful instructions allow you to monitor and control various industrial processes with precision and reliability.A counter is essentially a memory location that either increments or decrements based on input conditions. Whether you’re working with an Omron PLC or other brands, understanding counter functionality is crucial for effective automation programming.
How Do Different Types of Counter Instructions Work?
There are several types of counter instructions commonly used in PLC programming:
- Count-Up (CTU) counters
- Count-Down (CTD) counters
- Count-Up/Down (CTUD) counters
Each counter type consists of key elements:
- Input (CU for count up, CD for count down)
- Reset input
- Preset value (PV)
- Accumulated value (ACC)
- Done bit (DN)
The Mitsubishi PLC and other manufacturers implement these counter types with slight variations in their programming software.
What Are the Best Practices for Counter Implementation?
When implementing counters in your ladder logic programming, consider these essential practices:
- Proper Reset Configuration
- Always initialize counters at program start
- Include manual reset capabilities
- Consider automatic reset conditions
- Preset Value Management
- Use variables instead of hard-coded values
- Document preset value changes
- Consider process requirements carefully
Working with Schneider PLCs or any other brand requires attention to these fundamentals for reliable operation.
Common Counter Applications in Industrial Settings
Counters find extensive use in various industrial applications:
Application | Counter Type | Common Usage |
---|---|---|
Part Counting | CTU | Production tracking |
Batch Processing | CTUD | Recipe management |
Tool Life | CTD | Maintenance scheduling |
Conveyor Control | CTU | Package sorting |
Integration with HMI systems allows operators to monitor and adjust counter parameters easily.
Troubleshooting Counter Programming Issues
Common issues with counter programming include:
- Overflow conditions
- Incorrect reset timing
- Missing done bit implementation
- Improper data type selection
Frequently Asked Questions
Implement overflow detection and use appropriate data types for your application range.
Timers measure duration while counters track discrete events or occurrences.
High-speed counters are specifically designed for rapid pulse counting and may not be necessary for slower applications.
Select based on whether you need to count up to a target or down from a starting value.
Power your projects with brand-new, original Omron, Mitsubishi, Schneider PLC – in stock, ready now!
Key Takeaways
- Counter instructions are essential for tracking events in industrial automation
- Proper implementation requires understanding of different counter types
- Best practices ensure reliable counter operation
- Regular maintenance and monitoring prevent common issues
- Integration with HMI systems improves operator interaction
Remember these critical points when working with PLC counters:
- Always initialize counters properly
- Document your counter implementations
- Consider process requirements carefully
- Test reset conditions thoroughly
- Monitor for overflow conditions
- Maintain proper backup procedures
Contact our automation experts for personalized assistance with your PLC programming needs.
Contact Us
Just fill out your name, email address, and a brief description of your inquiry in this form. We will contact you within 24 hours.
You May Also Find These Topics Interesting
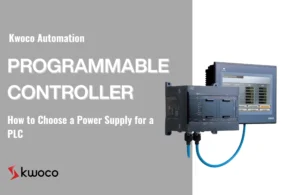
How to Choose a Power Supply for a PLC?
How to Choose a Power Supply for a PLC When it comes to industrial automation, choosing the right power supply
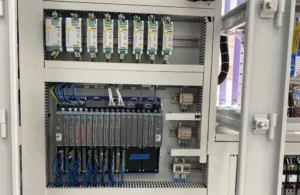
The Complete Guide to Programmable Logic Controllers (PLCs)
The Complete Guide to Programmable Logic Controllers (PLCs) In the fast-evolving world of industrial automation, Programmable Logic Controllers (PLCs) have
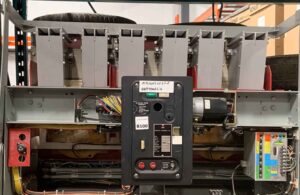
Demystifying the Air Circuit Breaker: Your Comprehensive Guide
This article delves into the fascinating world of air circuit breakers (ACBs), explaining their function, types, working principles, and applications. Whether you’re a seasoned professional in the industrial automation sector or simply curious about the technology that powers our modern world, this comprehensive guide will provide you with all the essential knowledge you need about ACBs, making it a worthwhile read for anyone interested in understanding these critical components of electrical systems.