What is a Level Sensor? Understanding Types and Applications
In this blog post, we will explore the various types of level sensors, their functionalities, and their ideal applications.
Table of Contents
What Are Level Sensors?
Level sensors are instruments used to detect and measure the levels of liquids, solids, or granular substances within containers or tanks. These devices work by converting detected level data into electrical signals, which can then be used for monitoring and controlling processes.
Level sensors can be categorized into point level sensors and continuous level sensors:
- Point Level Sensors: Detect whether a substance has reached a specific level.
- Continuous Level Sensors: Provide real-time, precise level measurements as the level rises or falls.
Additionally, level sensors can be classified based on their contact with the material being measured:
- Invasive Sensors: Make direct contact with the substance.
- Non-Contact Sensors: Use sound or electromagnetic waves for measurement.
Types of Point Level Sensors
1. Capacitance Level Sensors
Capacitance sensors use an electric field to detect the level of liquids or solids.
- Advantages: Small, accurate, low-cost, and have no moving parts.
- Limitations: Require calibration and are suitable only for specific liquids.
- Applications: Ideal for storage tanks in water treatment facilities.
2. Optical Level Sensors
These sensors use infrared light to detect the presence of liquid.
- Advantages: Compact, unaffected by high pressure or temperature, and maintenance-free.
- Limitations: Require cleaning if the lens becomes dirty.
- Applications: Used as low-level indicators for oil, coolant, or hydraulic systems.
3. Conductivity (Resistance) Level Sensors
Conductivity sensors rely on electrodes and current flow to sense liquid levels.
- Advantages: Affordable, simple to use, and durable.
- Limitations: Only suitable for conductive liquids and may erode over time.
- Applications: Commonly used for high or low-level detection in storage tanks.
4. Vibrating (Tuning Fork) Level Sensors
Tuning fork sensors measure levels based on vibration frequency changes.
- Advantages: Compact, cost-effective, and maintenance-free.
- Limitations: Invasive and suitable only for specific materials.
- Applications: Widely used in mining, food processing, and chemical industries.
5. Float Switches
Float switches detect levels by opening or closing a circuit as a float moves up or down.
- Advantages: Cost-effective, straightforward, and non-powered.
- Limitations: Have moving parts, are large in size, and offer limited precision.
- Applications: Frequently used for high or low-level detection in liquid storage tanks.
Types of Continuous Level Sensors
1. Ultrasonic Level Sensors
Ultrasonic sensors emit sound waves to measure levels based on wave reflection time.
- Advantages: Non-contact, self-cleaning, compact, and unaffected by material properties.
- Limitations: Expensive and sensitive to environmental conditions.
- Applications: Suitable for hot liquid storage tanks in industrial plants.
2. Radar (Microwave) Level Sensors
Radar sensors use microwaves to determine levels by measuring signal reflection time.
- Advantages: Accurate, unaffected by temperature or pressure, and suitable for various materials.
- Limitations: High cost and limited detection range.
- Applications: Ideal for measuring levels in hot asphalt tanks or storage of viscous substances.
Choosing the Right Level Sensor
When selecting a level sensor, consider:
- Material Properties: Is the substance liquid, solid, or granular?
- Measurement Requirements: Do you need precise data or a simple high/low indicator?
- Environmental Conditions: Consider temperature, pressure, and cleanliness of the application area.
- Cost and Maintenance: Balance between affordability and ease of upkeep.
Common Applications of Level Sensors
Level sensors are used in a variety of industries, including:
- Automotive: Fuel level monitoring.
- Manufacturing: Liquid storage management.
- Food and Beverage: Level control in production lines.
- Mining: Measurement of materials in silos.
- Household Appliances: Ice makers and washing machines.
Power your projects with brand-new, original Omron, Mitsubishi, Schneider PLC – in stock, ready now!
Conclusion
Level sensors are indispensable tools for ensuring precision and reliability in liquid and solid level monitoring. By understanding the types, functionalities, and applications of these sensors, you can make informed decisions to enhance operational efficiency in your specific use case.
Whether you’re managing industrial processes or designing everyday appliances, the right level sensor can make all the difference.
If you’re looking for an industrial sensor supplier, contact Kwoco. We provide globally shipped, brand-new original sensors from top brands like Omron and Keyence.
Contact Us
Just fill out your name, email address, and a brief description of your inquiry in this form. We will contact you within 24 hours.
You May Also Find These Topics Interesting
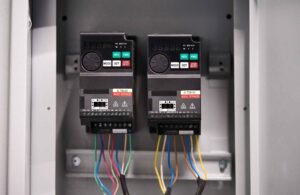
Variable Frequency Drives (VFD): Complete Guide to Motor Control
A comprehensive guide to variable frequency drives (VFDs) – the technology that’s revolutionizing motor control in industrial applications. Whether you’re an engineer, technician, or facility manager, this article will help you understand how VFDs work and why they’re crucial for modern motor applications.
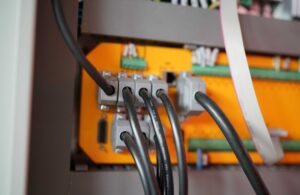
PLC Output Types: Essential Guide for Automation Engineers
In the world of industrial automation, understanding PLC output types is crucial for effective control system design and implementation. This comprehensive guide will walk you through the various types of PLC outputs, their applications, and how to choose the right one for your specific needs.
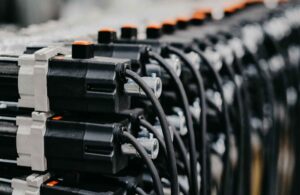
What is The Purpose of a Servo Motor?
Servo motors have become indispensable in modern industrial applications, offering unparalleled precision and control. Whether it’s in robotics, automation, or any system requiring exact movements, servo motors are at the heart of it all. In this article, we’ll explore the purpose of servo motors, their types, and why they are crucial in various industries today.