How to Troubleshoot PLC Power Supply Issues?
- kwoco-plc.com
- July 6, 2024
- 5:55 am
Table of Contents
The PLC (or Programmable Logic Controller) is a powerful device at the heart of modern automation systems. PLCs are designed to control machinery and processes, ensuring everything runs smoothly and efficiently. However, like any critical component, PLCs are not immune to power supply issues, which can disrupt the entire operation.
Introduction
This article is your go-to guide for identifying and solving PLC power supply problems. Whether you’re a seasoned engineer or a purchasing manager overseeing automation projects, you’ll find practical insights to keep your systems running seamlessly.
We’ll cover common symptoms of power supply issues, diagnostic tips, and effective solutions to ensure your automation setup remains reliable and efficient.
Understand the PLC Power Supply
A PLC power supply is a critical component in the realm of industrial automation. It provides the necessary electrical power for the operation of Programmable Logic Controllers (PLCs).
Without a reliable power supply, PLCs cannot function effectively, leading to potential disruptions in automated processes. The PLC power supply ensures that the controllers receive a stable and continuous flow of electricity, which is essential for maintaining the precision and efficiency of automation systems.
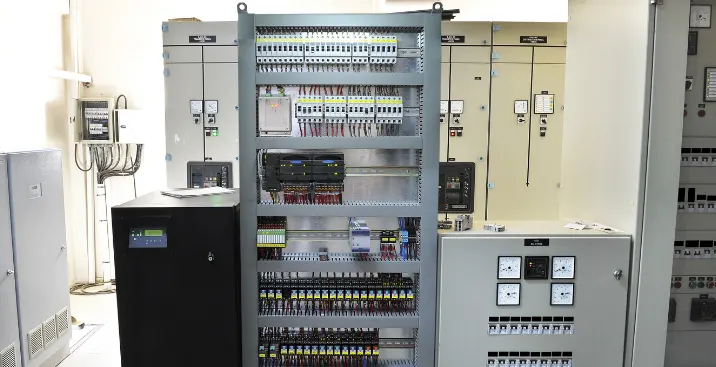
Common PLC Power Supply Problems
Identification
Power supply issues in PLCs can manifest in several ways. Do you notice any of the following?
- – Unexpected shutdowns or reboots?
- – Inconsistent operation or erratic behavior?
- – Overheating of the power supply unit?
- – Indicator lights showing abnormal status?
- – Error messages related to voltage supply?
Causes
Several factors can lead to PLC power supply problems. Power surges and outages are among the most frequent causes. Surges, often caused by lightning strikes or switching operations in the power grid, can overwhelm the power supply unit, leading to failures.
Outages, on the other hand, result in a complete loss of power, disrupting PLC operations. Faulty components, such as capacitors, transformers, or diodes within the power supply unit, can degrade over time or fail abruptly, causing instability in the power provided to the PLC.
Poor or deteriorating wiring connections can also contribute to inconsistent power delivery, resulting in intermittent faults and operational issues.
Understanding these common problems and their root causes is essential for developing effective maintenance strategies.
By employing diagnostic tools and maintaining a proactive approach to monitoring power quality, organizations can significantly reduce the risk of PLC power supply failures and ensure continuous, reliable operation of their automation systems.
Effects of Power Supply Failure on PLCs
PLC Program and Power Supply Failure
When a PLC power supply fails, the immediate impact is on the PLC program execution. The PLC program, which contains the logic and instructions for controlling the automation process, is halted.
This interruption can cause the system to stop functioning as designed, leading to unexpected machine behavior and potential safety hazards. Furthermore, if the power failure is prolonged, there may be a loss of volatile memory data, requiring the program to be reloaded or reset once power is restored.
Output and CPU Power Failure
The output of a PLC is directly tied to its CPU’s operational status. When the CPU power fails, all outputs controlled by the PLC are affected.
This typically results in the outputs defaulting to a predefined safe state, often an OFF state, to prevent any unintended operations. This safety mechanism is critical in preventing machinery from continuing to run uncontrollably, which could lead to equipment damage or safety incidents.
However, this also means that any ongoing processes are abruptly stopped, which can disrupt production lines and require extensive recovery efforts.
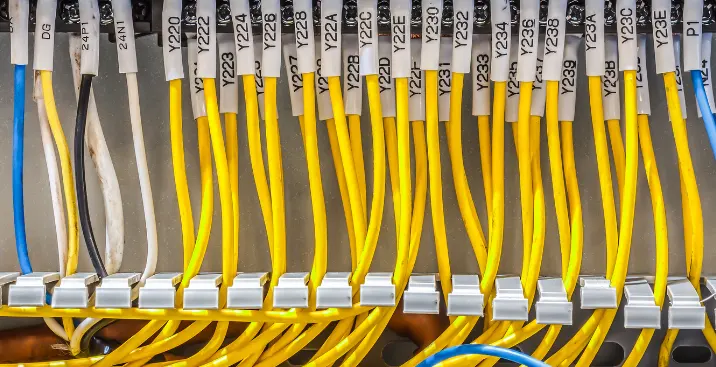
General Effects
- Operational Downtime: The immediate cessation of automation processes leads to production halts, which can cause significant delays and financial losses.
- Data Loss: Depending on the PLC’s memory configuration, critical data stored in volatile memory may be lost, requiring reprogramming or reinitialization of the system.
- Equipment Safety Risks: Sudden power loss can create unsafe conditions for machinery and operators if not properly managed by fail-safe mechanisms.
- Maintenance and Recovery: Power supply failures often necessitate thorough inspections and repairs, increasing maintenance costs and recovery time.
How Do You Diagnose PLC Power Supply Issues?
Visual Inspection
The first step in identifying PLC power supply problems is conducting a thorough visual inspection. Look for any visible signs of damage or wear on the power supply unit, connectors, and wiring. Burn marks, loose connections, and physical deterioration are clear indicators of potential issues.
Using Diagnostic Tools
Employing diagnostic tools is essential for a more detailed analysis. A multimeter can measure the output voltage and current of the power supply to ensure they meet the specifications required by the PLC. Additionally, a power quality analyzer can detect fluctuations, surges, and other anomalies in the power supply that might affect the PLC’s performance.
Checking Power Supply Voltage and Current
Measure the voltage and current being supplied to the PLC. Compare these readings against the manufacturer’s recommended values. Any deviations can indicate problems with the power supply unit or the electrical infrastructure feeding the PLC.
Error Codes and System Alerts
Modern PLCs often come equipped with diagnostic capabilities that can detect and report power supply issues. Error codes and system alerts displayed on the PLC’s interface can provide valuable clues about the nature and location of the problem. Refer to the PLC’s manual to interpret these codes accurately.
Irregular PLC Behavior
Unusual or erratic behavior in the PLC’s operations is another indicator of power supply problems. This can include intermittent operation, unexpected reboots, or failures to execute commands correctly. Such behavior often points to instability in the power supply, requiring immediate attention to prevent further disruption.
By following these step-by-step identification procedures and paying close attention to specific indicators, technicians can accurately diagnose and address PLC power supply problems, ensuring the stability and efficiency of industrial automation systems.
How to Fix Common PLC Power Supply Issues?
Inspecting and Replacing Faulty Components
Begin with a detailed inspection of the power supply unit and associated components. Identify any faulty parts such as blown fuses, damaged capacitors, or defective transformers. Replace these components with new ones that meet the manufacturer’s specifications to restore the power supply to its optimal condition.
Ensuring Proper Wiring and Connections
Examine all wiring and connections to ensure they are secure and free from corrosion or physical damage. Loose or corroded connections can cause intermittent power issues. Tighten any loose connections and replace any damaged wires. Ensure that the wiring meets the appropriate standards for the PLC’s power requirements.
Using Uninterruptible Power Supplies (UPS)
To protect against power outages and surges, implement an uninterruptible power supply (UPS). A UPS provides a backup power source that can keep the PLC running during short-term power interruptions. It also regulates voltage levels, protecting the PLC from harmful surges and spikes.
Implementing Power Conditioning Equipment
Power conditioners and surge protectors are advanced solutions that enhance power quality. These devices filter out noise, smooth out voltage fluctuations, and protect against surges. By stabilizing the power supply, they ensure that the PLC receives a consistent and clean electrical input, which is crucial for reliable operation.
Following these troubleshooting steps and implementing advanced solutions can significantly reduce the risk of power supply problems in PLC systems. By maintaining proper component integrity and ensuring stable power delivery, you can enhance the reliability and efficiency of your industrial automation processes.
Case Studies and Examples
Mitsubishi PLC Power Supply Issues and Solutions
Mitsubishi PLCs, known for their reliability, can still encounter power supply issues. Common problems include voltage fluctuations and overheating of power supply units. Solutions often involve upgrading to a higher capacity power supply, ensuring adequate ventilation, and incorporating power conditioning equipment to stabilize voltage inputs. Regular maintenance checks and using Mitsubishi’s diagnostic tools can preemptively identify and resolve potential issues.
Schneider PLC Common Problems and Fixes
Schneider PLCs are widely used in various industrial applications but can experience power-related failures such as sudden shutdowns and erratic behavior. Solutions typically involve inspecting and replacing faulty capacitors, ensuring secure wiring connections, and utilizing Schneider’s integrated diagnostic features to pinpoint and address power supply inconsistencies. Implementing a UPS system can also mitigate the impact of power outages and surges.
Omron PLC Power Troubleshooting Tips
Omron PLCs are renowned for their robustness, yet they can face issues like power surges and component failures. Troubleshooting tips include using multimeters to check for consistent voltage supply, replacing damaged power supply units, and ensuring all connections are tight and corrosion-free. Employing power quality analyzers can help detect and resolve subtle power disturbances that might affect the PLC’s performance.
Best Practices for Maintaining PLC Power Supply
Regular Inspections and Testing
Conducting regular inspections and testing is crucial for maintaining the integrity of your PLC power supply. Schedule routine checks to identify and rectify any potential issues before they escalate into major problems.
This includes visual inspections for signs of wear and tear, as well as using diagnostic tools to monitor voltage levels and power quality. Regular testing ensures that all components are functioning correctly and helps to maintain the overall health of the automation system.
Keeping Spare Parts and Components
Having spare parts and components readily available is a key aspect of preventive maintenance. Stock essential items such as fuses, capacitors, and transformers to ensure quick replacements when needed.
This minimizes downtime and ensures that the PLC system can be promptly restored to full functionality in case of component failure. A well-maintained inventory of spare parts can significantly reduce the impact of unexpected power supply issues.
Upgrading to More Reliable Power Supplies
Consider upgrading to more reliable power supplies to enhance the resilience of your PLC systems. Modern power supply units offer improved efficiency, better voltage regulation, and enhanced protection against surges and spikes.
Upgrading to these advanced units can provide a more stable and reliable power source, reducing the likelihood of power-related disruptions and extending the lifespan of your PLC components.
Conclusion
Identifying and solving PLC power supply problems is crucial to maintaining smooth and efficient operations. By understanding the symptoms, using the right tools, and applying effective solutions, you can minimize downtime and extend the life of your equipment. Regular maintenance and advanced troubleshooting techniques further enhance your ability to keep your PLC systems running optimally.
For expert assistance with PLC power supply issues, please contact our team at kwoco. Our specialists are ready to help you ensure the reliability and efficiency of your automation systems.