Relay PLC vs. Transistor PLC: Which One Fits Your Control Needs?
- kwoco-plc.com
- September 21, 2024
- 6:12 am
In the world of industrial automation, selecting the right PLC (Programmable Logic Controller) can significantly impact the efficiency and reliability of your systems. You might be wondering: Relay PLC or Transistor PLC, which one is the best fit for your application? Let’s dive into the differences, advantages, and ideal usage scenarios of each type.
Relay PLCs are the backbone of high-load, high-reliability industrial environments. These PLCs use electromagnetic relays to control inputs and outputs, offering excellent resistance to electromagnetic interference and robust load capacity. But are they always the best choice?
Table of Contents
I’ve been in the field of industrial control products for years, and I’ve seen firsthand how choosing the right PLC can make or break a project. Let’s explore these two types of PLCs to help you make the right decision.
What is a Relay PLC?
- Working Principle: The Relay PLC operates by engaging and releasing electromagnetic relays to establish logical control between inputs and outputs.
- Load Capacity: Typically handles currents up to 5A, making it ideal for high-load applications.
- Response Time: Usually above 10ms, which is relatively slow but sufficient for many mechanical operations.
- Interference Resistance: Due to its mechanical nature, it has excellent resistance to external electromagnetic interference.
What is a Transistor PLC?
- Working Principle: Utilizes the fast switching characteristics of transistors to achieve logic control between inputs and outputs.
- Load Capacity: Typically handles currents below 1A, suitable for low-load applications.
- Response Time: Usually in the microsecond range, much faster than Relay PLCs.
- Power Consumption: Low power consumption due to the low conduction resistance of transistors.
Pros and Cons: Relay PLC vs. Transistor PLC
Relay PLC
- Can drive both AC and DC loads.
- High load rating, often capable of handling several amperes.
- Limited action frequency, not suitable for high-speed operations.
- Mechanical lifespan typically between 1 to several million cycles.
Transistor PLC
- High action frequency, reaching several hundred kHz, perfect for high-speed switching.
- No mechanical wear, theoretically offering unlimited lifespan (though affected by semiconductor properties and temperature).
- Primarily used for DC loads; special design or additional components are needed for AC loads.
- Lower current handling capacity, usually below several amperes.
Power your projects with brand-new, original Omron, Mitsubishi, Schneider PLC – in stock, ready now!
Where Should You Use Each Type?
Servo Motor Control Systems – Best Fit for Transistor PLC
Servo motor control demands high precision and fast response times. Here’s why Transistor PLCs excel in this area:
- Control Precision: Perfect for accurate position and speed control.
- Response Speed: Microsecond-level response meets high-speed control needs.
- PWM Output: Offers precise control signals to drive servo motor amplifiers.
- Real-Time Performance: Ensures timely and consistent control signals.
- Communication Capability: Supports advanced interfaces like EtherCAT or Profinet for high-speed data exchange.
Inverter Drive Systems – Best Fit for Relay PLC
- Load Capacity: Relay PLCs provide outputs of up to several amperes, ideal for driving inverters.
- Interference Resistance: Their mechanical nature offers superior resistance to electromagnetic interference.
- Overload Protection: Safeguards the system by breaking the circuit when current exceeds the rated value.
- Compatibility: Designed with multiple output types for compatibility with various inverters.
- Control Logic: Suitable for complex logic controls, crucial for stable inverter operation.
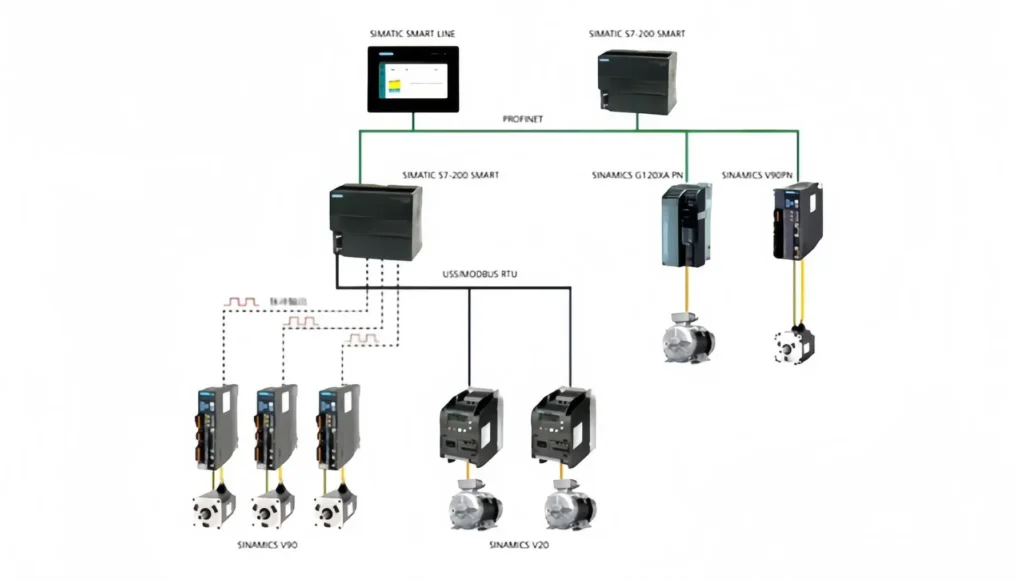
Key Questions to Consider
- What are the load requirements of your application?
- How critical is response time for your control system?
- Are you dealing with high electromagnetic interference?
- Do you need to control AC or DC loads?
- What is the expected operational frequency of your system?
Conclusion
Choosing between a Relay PLC and a Transistor PLC boils down to your specific application needs. Relay PLCs are robust, handle higher loads, and excel in environments with electromagnetic interference. Transistor PLCs offer speed, precision, and energy efficiency, making them the go-to for high-speed and precise control systems. Still unsure? Reach out to discuss your project needs, and we’ll guide you to the best solution.
Ready to upgrade your control system? Contact us ([email protected]) today to find the perfect PLC solution tailored to your needs. Let’s drive your project efficiency to the next level—fast and reliable!
Contact Us
Just fill out your name, email address, and a brief description of your inquiry in this form. We will contact you within 24 hours.
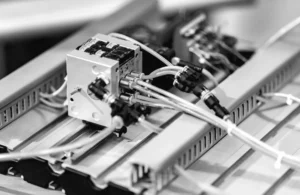
Why Your PLC Needs a Separate Power Supply
Why Your PLC Needs a Separate Power Supply Have you ever wondered why PLC systems often require a separate power
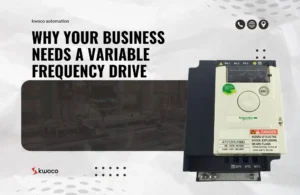
Why Your Business Needs a Variable Frequency Drive
Why Your Business Needs a Variable Frequency Drive When managing industrial operations, optimizing energy efficiency while maintaining performance is crucial.
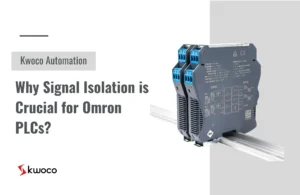
Why Signal Isolation is Crucial for Omron PLCs?
Why Signal Isolation is Crucial for Omron PLCs? In the world of industrial automation, signal interference is a silent killer.