Why Your PLC Needs a Separate Power Supply
- kwoco-plc.com
- September 29, 2024
- 7:32 pm
Have you ever wondered why PLC systems often require a separate power supply module? For those of us in industrial automation, PLCs (Programmable Logic Controllers) are indispensable on the production line.
Yet, the necessity of having an independent power supply is often overlooked. This article will unravel the mystery and explain why having a separate power supply for your PLC is about more than just “keeping the power on.”
First of all, the PLC power module is not just a power source; it also protects and optimizes the entire PLC system. In industrial environments, where complex factory systems often face power fluctuations and electromagnetic interference, a standard power supply simply cannot meet the demands of these high-precision devices. To ensure stable PLC operation, a dedicated power supply module is essential.
Let’s address a few key questions to uncover why this is so important.
Table of Contents
1. Why Can’t a PLC Rely on a Standard Power Source?
You might ask: since the factory already has a power system, why does the PLC need a separate power supply? In reality, a standard power source can be affected by issues such as voltage transients and fluctuations.
In simple terms, “noise” or “power disturbances” in the system can directly impact the PLC’s normal operation, causing control errors or even system shutdowns. For instance, some voltage transients can reach up to 6000V, which is enough to burn out critical PLC components if not handled properly.
One of the main functions of the separate power module is to protect the PLC from such power disturbances. It ensures a stable output voltage, keeping the current and voltage supplied to the PLC within a safe and reliable range. This allows the PLC to perform its control tasks smoothly without interference from external power fluctuations.
2. How Can We Avoid Electromagnetic Interference on a PLC?
In industrial environments, electromagnetic interference (EMI) is unavoidable. These interferences may come from motors, relays, or other high-power devices in operation. In a PLC system, such noise can directly impact signal transmission, leading to system failure. The PLC’s complex control logic and memory units are particularly vulnerable to such interference.
The solution? A separate power module can block EMI paths using isolation transformers or current clamp circuits, ensuring that the PLC’s signals remain undisturbed.
3. How Does a Separate Power Supply Improve PLC Reliability?
You’ve likely realized that each PLC error can lead to significant losses, especially in factories where safety or operational efficiency is critical. If a PLC fails, the entire production line may come to a halt, causing costly downtime.
A separate power supply not only provides a stable current but also uses better power design and integrated isolation technology to ensure long-term, stable PLC operation.
For example, linear voltage regulators within independent power supplies can stabilize the 24V DC output and eliminate current fluctuations caused by other factory equipment. This steady power supply significantly extends the lifespan of your PLC.
4. Understanding the Isolation Between PLC Power and Field Device Power
In a PLC control system, not only does the PLC itself need power, but so do the input and output (I/O) modules. However, PLCs and I/O modules often require separate power supplies. Why?
To prevent electrical noise from field devices from affecting the PLC’s normal operation. If both the PLC and field devices share the same power supply, external current fluctuations can easily pass through the I/O modules and into the PLC, causing misoperations or even shutdowns.
By using separate power supplies for the PLC and I/O modules, you can ensure electrical isolation between the two, preventing potential noise and interference problems.
5. How Does a Separate Power Supply Protect Key PLC Components?
The key components of a PLC include the CPU module, memory, and I/O modules. These parts are extremely sensitive to voltage changes, particularly the memory units, which could lose data or cause the system to restart if voltage becomes unstable.
A separate power supply ensures that the current and voltage supplied to the PLC remain within a safe range through regulation and filtering functions, protecting these critical components.
In addition to voltage regulation, an independent power supply can respond quickly to abnormal power conditions through built-in overvoltage protection, safeguarding the PLC from electrical surges.
6. Why Choosing a Separate Power Supply Reduces Maintenance Costs?
The last question is also the most common: does using a separate power supply mean higher costs? In the short term, purchasing a separate PLC power module does indeed require additional budget. But from a long-term operational and maintenance perspective, it’s actually a cost-saving approach.
A separate power supply not only extends the PLC’s lifespan and reduces downtime, but also lowers the risk of frequent repairs or replacements.
FAQ
Power your projects with brand-new, original Omron, Mitsubishi, Schneider PLC – in stock, ready now!
1. What power supply is required for PLC?
The power supply required for a PLC typically depends on the specifications of the PLC system. Most PLCs use a 24V DC power supply, though some may use 5V or 12V DC depending on the model and application. The power supply needs to convert standard AC voltage (such as 120V or 240V AC) into a stable DC output to power the CPU, memory, and other modules in the system. Always check the manufacturer’s recommendation for the specific voltage and current requirements of your PLC.
2. How to select power supply for PLC?
When selecting a power supply for your PLC, consider the following factors:
- Voltage: Ensure the power supply matches the required voltage for your PLC (commonly 24V DC).
- Current Rating: The power supply should have enough current capacity to support all connected devices and components. For smaller PLC systems, a power supply with 2 to 10 amps may suffice, while larger systems may need 50 amps or more.
- Power Rating: Calculate the total power consumption of the PLC and any connected modules or devices to ensure the power supply can handle the load.
- Environment: Consider the industrial environment. If your system is exposed to electrical noise, temperature extremes, or vibrations, opt for a more robust power supply with protection features like overvoltage, surge suppression, and noise filtering.
3. Why is power supply needed for PLC?
A power supply is crucial for a PLC because it provides the necessary voltage and current to keep the system running. More importantly, it converts high-voltage AC from the grid to a stable DC output, ensuring the CPU, memory, and modules within the PLC receive consistent and clean power. Without a proper power supply, the PLC would be vulnerable to voltage fluctuations, surges, and power interruptions, leading to potential system failures or damage.
Conclusion
In summary, a separate power supply for your PLC is not just crucial for ensuring stable system operation—it also provides a vital safeguard for the efficiency and safety of your factory. By preventing voltage fluctuations, electromagnetic interference, and noise from affecting your PLC system, a separate power supply dramatically improves its reliability and stability.
As an engineer at Kwoco, I understand that choosing the right power supply for your PLC means investing in a more efficient and safer control system. If you have any questions about selecting a power supply for your PLC, feel free to visit our website www.kwoco-plc.com or contact me at [email protected]. We’re here to provide you with professional support and services.
Contact Us
Just fill out your name, email address, and a brief description of your inquiry in this form. We will contact you within 24 hours.
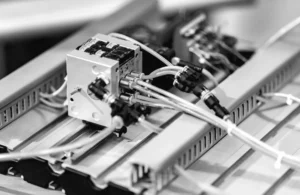
Why Your PLC Needs a Separate Power Supply
Why Your PLC Needs a Separate Power Supply Have you ever wondered why PLC systems often require a separate power
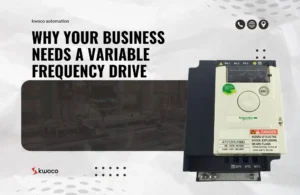
Why Your Business Needs a Variable Frequency Drive
Why Your Business Needs a Variable Frequency Drive When managing industrial operations, optimizing energy efficiency while maintaining performance is crucial.
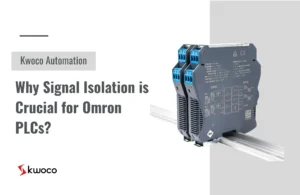
Why Signal Isolation is Crucial for Omron PLCs?
Why Signal Isolation is Crucial for Omron PLCs? In the world of industrial automation, signal interference is a silent killer.