Capire i PLC: usi dei controllori logici programmabili
Questo articolo svela a cosa serve un PLC, come funziona e perché è fondamentale nel panorama industriale odierno. Che tu sia alle prime armi con il concetto o che tu voglia approfondire la tua comprensione, continua a leggere per scoprire il ruolo fondamentale dei PLC nell'automazione dei processi industriali.
Sommario
Cos'è un PLC e come funziona?
Un controllore logico programmabile (PLC) è un computer industriale specializzato progettato per automatizzare e controllare i processi in tempo reale. A differenza dei normali computer, i PLC sono costruiti per resistere a condizioni ambientali difficili come temperature estreme, umidità e rumore elettrico, rendendoli ideali per gli ambienti industriali.
Componenti di un PLC
Un tipico sistema PLC comprende:
- Unità centrale di elaborazione (CPU): Il cervello che esegue il programma PLC.
- Moduli di ingresso: Riceve segnali da dispositivi di input come sensori, interruttori e pulsanti.
- Moduli di uscita: Invia segnali a dispositivi di output quali motori, valvole e luci.
- Alimentazione elettrica: Fornisce l'alimentazione necessaria al PLC.
- Dispositivo di programmazione: Utilizzato per programmare e configurare il PLC, spesso tramite software di programmazione specializzato.
Come funziona un PLC?
Un PLC funziona ciclicamente attraverso tre fasi principali:
- Scansione di input: il PLC riceve dati di input dai dispositivi di input collegati.
- Esecuzione del programma: elabora i dati di input utilizzando la logica del programma definita nel programma PLC.
- Scansione di output: invia comandi ai dispositivi di output in base ai dati elaborati.
Questo processo ciclico consente al PLC di monitorare e controllare i processi in modo efficiente, garantendo il funzionamento preciso di macchinari e sistemi.
Perché i PLC vengono utilizzati nell'automazione industriale?
I PLC sono ampiamente utilizzati nell'automazione industriale per la loro affidabilità, flessibilità ed efficienza. Ecco i motivi principali per cui le industrie utilizzano i PLC:
Affidabilità e durata
- Design robusto: I PLC sono progettati per funzionare in condizioni difficili, riducendo al minimo i tempi di fermo.
- Prestazioni costanti: Garantiscono un controllo stabile sui processi, fondamentale per il mantenimento della qualità.
Flessibilità e scalabilità
- Struttura modulare: PLC modulari come Mitsubishi PLC consentono una facile espansione aggiungendo moduli PLC.
- Adattabilità:I programmi possono essere modificati per adattarsi ai cambiamenti nel processo di produzione senza alterare l'hardware.
Funzionamento in tempo reale
- Risposta immediata: I PLC operano in tempo reale, garantendo che i processi reagiscano rapidamente agli input
- Controllo di precisione: Gestire attività complesse con elevata precisione, essenziale per i moderni processi industriali.
Semplificazione dei sistemi complessi
- Sostituisce i sistemi logici a relè: Semplifica il cablaggio e riduce i componenti fisici necessari.
- Risoluzione dei problemi avanzata: È più facile identificare i problemi all'interno del programma PLC rispetto ai sistemi tradizionali.
Tipi di PLC: scelta del controllore logico programmabile giusto
Quando si tratta di scegliere un PLC, è essenziale conoscere le diverse tipologie di PLC.
PLC modulari
- Descrizione: Sono costituiti da moduli separati per CPU, ingressi, uscite e protocolli di comunicazione.
- Vantaggi: Altamente scalabile e personalizzabile in base a esigenze specifiche.
- Applicazioni: Adatto a processi complessi che richiedono numerosi input e output.
PLC compatti (PLC standard)
- Descrizione: Unità all-in-one con capacità I/O fisse.
- Vantaggi: Conveniente e salvaspazio.
- Applicazioni: Ideale per attività di controllo più semplici con requisiti I/O limitati.
PLC montati su rack
- Descrizione: I moduli sono montati su rack, consentendo un'ampia espansione.
- Vantaggi: Supporta un gran numero di punti I/O e un'elevata potenza di elaborazione.
- Applicazioni: Applicazioni industriali su larga scala come il controllo dei processi nelle raffinerie di petrolio.
Quando si seleziona un PLC, considerare fattori quali:
- Complessità del processo: La natura dei compiti e del controllo richiesti.
- Requisiti I/O: Numero e tipo di dispositivi di input e output.
- Condizioni ambientali: Temperatura, polvere, livelli di umidità nell'ambiente operativo.
- Esigenze di comunicazione: Integrazione con sistemi SCADA, HMI (Interfaccia uomo-macchina)e altri dispositivi esterni.
Marchi come PLC di Omron E PLC Schneider offrono vari PLC con diverse funzionalità PLC per soddisfare diverse esigenze industriali.
Come vengono programmati i PLC? Comprensione dei linguaggi di programmazione dei PLC
I PLC vengono programmati utilizzando linguaggi di programmazione specializzati che forniscono istruzioni al PLC su come rispondere a specifiche condizioni di input.
Linguaggi di programmazione PLC comuni
- Logica a scala (diagramma a scala)
- Linguaggio di programmazione PLC più comunemente utilizzato.
- Assomiglia alla logica dei relè tradizionali, risultando intuitivo per gli ingegneri che hanno familiarità con i circuiti elettrici.
- Ideale per semplici operazioni di controllo e sequenziamento.
- Testo strutturato
- Linguaggio testuale di alto livello simile al Pascal.
- Adatto per funzioni matematiche e algoritmi complessi.
- Diagramma a blocchi funzionali (FBD)
- Linguaggio grafico che utilizza blocchi per rappresentare funzioni.
- Eccellente per il controllo di processo analogico e il blocco funzionale
- Diagramma funzionale sequenziale (SFC)
- Rappresenta i processi come una serie di passaggi e transizioni.
- Utile per processi batch e funzioni sequenziali.
- Elenco delle istruzioni
- Linguaggio testuale di basso livello simile al codice assembly.
- Efficiente ma meno intuitivo a causa della sintassi concisa.
Concetti di programmazione
- Ingressi e uscite: Comprendere come i dispositivi di input, come sensori e interruttori, influenzano gli output.
- Logica di controllo: Sviluppo della logica del programma che definisce la relazione tra input e output.
- Timer e contatori: Gestione degli eventi in base al tempo o ai conteggi.
- Trattamento dei dati: Lavorare con variabili, array e archiviazione dati.
Software di programmazione
I produttori spesso forniscono software di programmazione proprietario per i loro PLC. Questo software include strumenti per scrivere, simulare e debuggare programmi PLC.
L'utilizzo efficace di un PLC richiede familiarità con questi concetti e linguaggi di programmazione. Sfruttando il linguaggio appropriato, gli ingegneri possono creare sistemi di controllo efficienti e robusti.
PLC, sistemi SCADA e HMI: come funzionano insieme?
Nell'ambito dell'automazione industriale, i PLC spesso funzionano insieme ai sistemi SCADA e HMI per formare un sistema di controllo integrato.
PLC (controllori logici programmabili)
- Ruolo: Eseguire il controllo a livello di macchina o di processo.
- Funzionalità: Elaborare i dati di input e controllare i dispositivi di output in tempo reale.
HMI (Interfacce uomo-macchina)
- Ruolo: Fornire un'interfaccia tra operatori e macchine.
- Funzionalità: Visualizza i dati di processo, consente input utente e visualizza gli stati del sistema.
- Esempi: Interfaccia utente Proface, Interfaccia utente Mitsubishi.
Sistemi SCADA (controllo di supervisione e acquisizione dati)
- Ruolo: Supervisionare e controllare più PLC in una struttura o regione.
- Funzionalità: Raccogliere dati dai PLC, fornire controllo di supervisione e facilitare l'analisi dei dati.
- Importanza: Fondamentale per operazioni su larga scala come impianti di trattamento delle acque e reti elettriche.
Protocolli di comunicazione
- Scopo: Abilita lo scambio di dati tra PLC, HMI e sistemi SCADA.
- Protocolli comuni: Modbus, Profibus, Ethernet/IP.
- Benefici: Consentono il controllo coordinato, la registrazione dei dati e il monitoraggio remoto.
Integrando questi sistemi, le industrie ottengono un'automazione fluida, una maggiore efficienza e migliori capacità decisionali.
Applicazioni dei PLC nell'automazione industriale
I PLC sono utilizzati in vari settori grazie alla loro versatilità. Ecco alcune applicazioni tipiche:
Produzione
- Linee di montaggio: Controllare bracci robotici, trasportatori e macchine utensili.
- Controllo di qualità: Monitorare i parametri di produzione per garantirne la coerenza.
Settore energetico
- Produzione di energia: Gestire turbine, generatori e sistemi di distribuzione.
- Petrolio e gas: Controllare le operazioni di perforazione e i sistemi di condotte.
Gestione dell'acqua e dei rifiuti
- Impianti di trattamento: Regolamentare pompe, miscelatori e dosaggi chimici.
Industria automobilistica
- Linee di produzione: Coordinare attività complesse nell'assemblaggio dei veicoli.
Automazione degli edifici
- Sistemi HVAC: Controllare il riscaldamento, la ventilazione e l'aria condizionata.
- Sistemi di illuminazione: Automatizza l'illuminazione in base alla presenza di persone o all'ora del giorno.
Utilizzando un PLC, le industrie possono automatizzare i processi, migliorare la sicurezza, ridurre gli errori umani e ottimizzare le operazioni.
Esempio pratico: controllo di un'intera linea di produzione
Un PLC può gestire un'intera linea di produzione:
- Ricezione degli input: Raccolta dati dai sensori (temperatura, pressione, prossimità).
- Elaborazione dei dati: Esecuzione del programma PLC per determinare le azioni necessarie.
- Controllo delle uscite: Azionamento di motori, attuatori e altri dispositivi per eseguire attività.
- Comunicare: Condivisione delle informazioni con sistemi SCADA e HMI per il monitoraggio e il controllo.
Questa integrazione riduce al minimo i tempi di inattività e aumenta la produttività.
Domande frequenti
Il più comunemente usato per programmare i PLC è Ladder Logic, che assomiglia ai diagrammi logici dei relè elettrici. È intuitivo per chi ha familiarità con gli schemi dei circuiti ed è ideale per attività di controllo da semplici a moderatamente complesse.
I PLC comunicano tramite varie porte e protocolli di comunicazione come Ethernet/IP, Modbus e Profibus. Questi protocolli consentono lo scambio di dati con HMI, sistemi SCADA e altri dispositivi esterni, facilitando il controllo e il monitoraggio integrati.
- Flessibilità: Facilmente riprogrammabile per diverse attività.
- Risparmio di spazio: Riduce la complessità del cablaggio.
- Affidabilità: Minori tassi di guasto grazie al minor numero di componenti meccanici.
- Funzioni avanzate: Funzionalità quali registrazione dei dati, calcoli complessi e comunicazione di rete.
Considerare:
- Requisiti di processo: Complessità ed esigenze di controllo.
- Conteggio I/O: Numero di ingressi e uscite richiesti.
- Fattori ambientali: Condizioni operative come temperatura e polvere.
- Scalabilità: Possibile futura espansione.
- Compatibilità: Integrazione con i sistemi esistenti.
Sì, i PLC possono elaborare sia segnali analogici (valori variabili) sia segnali discreti (stati on/off). Sono disponibili moduli di input per vari tipi di segnale, consentendo ai PLC di gestire diversi input di dati.
Dai potenza ai tuoi progetti con i nuovi PLC originali Omron, Mitsubishi e Schneider, disponibili in magazzino e pronti da subito!
Conclusione
- I PLC sono computer industriali specializzati utilizzati per automatizzare e controllare macchinari e processi in tempo reale.
- Funzionano elaborando i dati di input provenienti dai dispositivi di input e controllando i dispositivi di output in base alla logica di controllo programmata.
- La programmazione di un PLC comporta l'utilizzo di linguaggi come Ladder Logic, Structured Text e Function Block Diagram.
- I tipi di PLC includono PLC modulari, PLC compatti e PLC montati su rack, ognuno adatto a diverse applicazioni.
- I PLC spesso lavorano insieme ai sistemi HMI e SCADA per formare soluzioni di automazione complete.
- Nella scelta di un PLC è necessario considerare la complessità del processo, le esigenze di I/O, le condizioni ambientali e la scalabilità.
- I PLC vengono utilizzati in vari settori industriali, migliorando l'efficienza, l'affidabilità e la sicurezza delle operazioni.
Cerchi nuovi PLC originali per i tuoi progetti? Da Kwoco, abbiamo in magazzino gli ultimi PLC dei migliori marchi come Omron, Mitsubishi, E SchneiderAcquista con fiducia: spedizione veloce, qualità garantita! Acquista ora
Contattaci
Basta compilare il tuo nome, indirizzo email e una breve descrizione della tua richiesta in questo modulo. Ti contatteremo entro 24 ore.
Categoria di prodotto
Prodotti in saldo
Potresti trovare interessanti anche questi argomenti
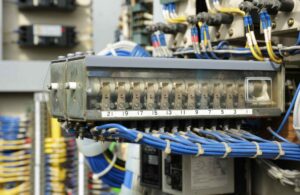
Comprensione degli ingressi analogici nei sistemi PLC: colmare il divario tra segnali digitali e analogici
Gli input analogici sono la linfa vitale dei moderni sistemi di automazione, fungendo da collegamento cruciale tra i processi fisici e i controller digitali come i PLC (Programmable Logic Controller). Comprendere il concetto di input analogici e come differiscono dagli input digitali è essenziale per chiunque sia coinvolto nell'automazione industriale. Questo articolo approfondirà cosa sono gli input analogici, come funzionano nei sistemi PLC e perché comprendere le differenze tra segnali analogici e digitali è fondamentale.
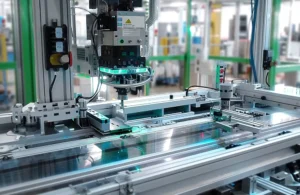
5 tipi di encoder nei servomotori che devi conoscere
In qualità di ingegnere con una vasta esperienza nell'automazione industriale, ho una profonda conoscenza dei servomotori e degli encoder che utilizzano. I sistemi servo sono ampiamente applicati nell'automazione, con gli encoder che fungono da componenti chiave per controllare velocità e posizione in modo accurato.
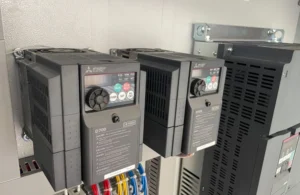
10 codici di allarme servo Mitsubishi comuni e soluzioni: risoluzione dei problemi semplificata!
10 codici di allarme servo Mitsubishi comuni e soluzioni: risoluzione dei problemi semplificata! Nell'automazione industriale, i servoazionamenti sono fondamentali e Mitsubishi