How to Choose the Omron PLC That Best Suits Your Needs
- kwoco-plc.com
- June 20, 2024
- 1:03 am
Struggling to find the right PLC for your industrial automation needs? With countless options on the market, it’s easy to feel overwhelmed.
Table of Contents
Selecting the wrong PLC can lead to costly downtimes, inefficiencies, and project delays. Whether you’re a seasoned engineer or a purchasing manager, making the right choice is crucial.
Introduction
Dive into the world of Omron PLCs, renowned for their reliability and performance.
Alongside Omron, brands like Mitsubishi, Schneider, Siemens, and Rockwell Automation offer a variety of options.
This guide will help you navigate these choices, ensuring you find the perfect fit for your specific requirements.
By focusing on the strengths and unique features of Omron PLCs, you’ll gain insights that empower you to make informed decisions, enhancing your operations and achieving optimal results.
Ready to elevate your automation game? Let’s explore how to choose the perfect Omron PLC for your needs.
Understanding PLCs in Industrial Automation
Definition of PLC (Programmable Logic Controller)
Programmable Logic Controllers (PLCs) are specialized computers used to automate industrial processes, ensuring precision and efficiency.
They monitor inputs, make decisions based on pre-programmed logic, and control outputs to automate machinery and processes.
Role of PLCs in industrial automation
In the realm of industrial automation, PLCs are indispensable, managing everything from assembly lines to robotic devices.
They often work hand-in-hand with SCADA (Supervisory Control and Data Acquisition) systems, which provide a higher level of control and data acquisition.
By integrating with SCADA, PLCs enhance monitoring and control capabilities, making complex automation tasks more manageable and efficient.
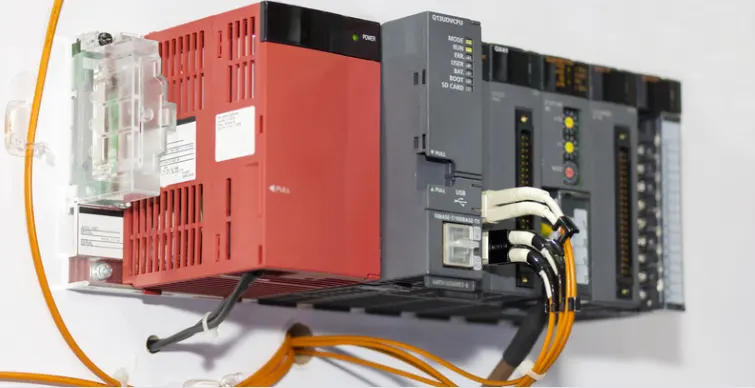
What is PLC and How Does It Work?
Explanation of PLC meaning and functionality
A Programmable Logic Controller (PLC) is a ruggedized computer used for automating industrial processes.
It operates by receiving input signals from sensors or user commands, processing these signals through pre-programmed logic, and sending output signals to control machinery.
Basic components of PLC
A PLC system comprises three primary components: the hardware, which includes the central processing unit (CPU), input/output modules, and power supply.
The programming software, which is used to create the control logic, and the overall PLC system, integrating both hardware and software for seamless operation.
Importance of PLC programming and PLC control systems
PLC programming is crucial as it defines the logic and operations the PLC will perform, ensuring precise control over industrial processes.
Effective PLC control systems enhance operational efficiency, reduce downtime, and ensure safety in automated environments.
Understanding how to program and integrate these systems is essential for anyone involved in industrial automation, making PLCs a cornerstone of modern manufacturing and process control.
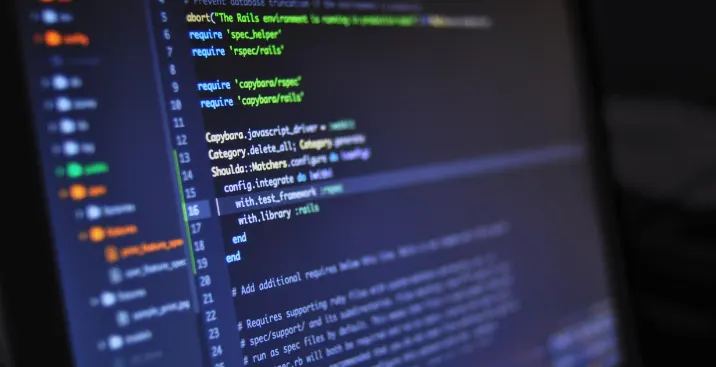
Key Criteria for Choosing the Right PLC
Selecting the ideal PLC for your automation needs involves careful consideration of several key factors:
- Determining Your Specific Automation Needs: Start by assessing the specific tasks and processes you need to automate. This foundational step will guide your decision-making process.
- Application Requirements: Identify the type of automation controllers and interface HMIs necessary for your application. For instance, do you require a simple HMI for basic tasks or an advanced controller for complex operations?
- Input/Output Requirements: Evaluate the number and type of input/output modules needed. This includes considering whether you need analogue input modules for precise data collection or digital outputs for straightforward control tasks.
- Compatibility with Existing Systems: Verify that the PLC can seamlessly integrate with your current systems, such as PLC SCADA and other PLC control systems. This ensures smooth communication and coordination across your automation network.
- Future Scalability and Flexibility: Choose a PLC that offers scalability to accommodate future expansion and flexibility to adapt to evolving automation needs. Modular PLCs are often a good choice for their ability to grow with your operations.
- Vendor Support and Software Availability: Ensure the vendor provides robust support and reliable PLC programming software. Access to technical assistance and regular software updates is crucial for maintaining system performance and addressing any issues promptly.
- Environmental Conditions and PLC Safety: Assess the operating environment of your PLC. Ensure it can withstand the conditions it will be exposed to, such as temperature extremes, humidity, dust, or corrosive substances. Additionally, prioritize PLCs with robust safety features to protect both equipment and personnel.
- Budget Considerations: Balance your budget with the necessary functionality. While there are affordable PLC options, ensure they meet your performance and reliability standards without compromising on essential features.
By methodically evaluating these criteria, you can select a PLC that not only meets your current automation needs but also supports future growth and integration, ensuring long-term success and efficiency in your projects.
Life Expectancy of Omron PLC
Omron PLCs are designed for durability, with a typical life expectancy ranging from 10 to 20 years, depending on usage and operating conditions. Several factors can affect the lifespan of a PLC:
- Operating Environment: Exposure to extreme temperatures, humidity, dust, and corrosive substances can shorten a PLC’s life.
- Electrical Interference: Fluctuations in power supply and electrical noise can impact performance and longevity.
- Usage Intensity: Continuous operation and heavy load demands can accelerate wear and tear.
To prolong the life of your Omron PLC, consider these maintenance tips:
- Regular Inspections: Conduct routine checks for signs of wear, damage, or corrosion.
- Clean Environment: Keep the PLC and surrounding area clean to prevent dust and debris accumulation.
- Stable Power Supply: Use surge protectors and maintain stable power conditions to protect against electrical interference.
- Scheduled Maintenance: Adhere to a maintenance schedule for replacing components like batteries and checking connections.
What Kind of PLC Do You Need?
Selecting the right PLC requires a thorough assessment of your automation needs. Consider the following when choosing between various PLC products and controllers:
- Automation Requirements: Determine the complexity of the tasks you need to automate. Simple processes may only require basic PLC controllers, while more complex operations might need advanced models with greater processing power and capabilities.
- Scale and Size: For small-scale applications, compact PLCs like the Omron CP1 series are ideal. Larger operations may benefit from modular PLCs such as the Mitsubishi FX series, which offer scalability and extensive I/O options
- Industry-Specific Needs: Different industries have unique requirements. For example, Siemens S7-1200 PLCs are well-suited for manufacturing and process control, whereas Schneider’s Modicon M340 is excellent for infrastructure and energy management projects.
- Integration Capabilities: Choose PLCs that can easily integrate with existing systems, such as SCADA or HMI, to streamline operations and enhance control.
By matching the right PLC to your specific application, you can ensure optimal performance and efficiency in your industrial automation projects.
Brands Comparison and Recommendations
When comparing Omron PLCs with other leading brands like Schneider, Mitsubishi, and Rockwell Automation, it’s essential to understand their distinct advantages and disadvantages:
- Omron PLC:
- Advantages: Highly flexible, excellent scalability, and robust communication capabilities. Ideal for complex automation tasks.
- Disadvantages: May require more extensive programming knowledge.
- Schneider PLC:
- Advantages: Energy-efficient, with advanced integration features and strong support for building automation and energy management.
- Disadvantages: Can be more expensive and less intuitive for beginners.
- Mitsubishi PLC:
- Advantages: Renowned for reliability and high-speed processing. Perfect for manufacturing and automotive applications.
- Disadvantages: Limited in scalability compared to some competitors.
- Rockwell Automation (Allen-Bradley):
- Advantages: Exceptional integration with a wide range of industrial applications and extensive support network.
- Disadvantages: Higher cost and complexity, which might be overkill for simpler applications.
Recommendations:
- For complex, scalable projects: Omron PLC
- For energy management and building automation: Schneider PLC
- For manufacturing and automotive industries: Mitsubishi PLC
- For comprehensive industrial integration: Rockwell Automation
Choose the brand that best aligns with your specific needs and application requirements to ensure optimal performance and efficiency in your automation projects.
Conclusion
Choosing the right PLC is a critical decision that impacts the efficiency and success of your automation projects.
We’ve covered key points, including understanding your automation needs, evaluating various PLC types and brands, and considering performance, compatibility, scalability, and vendor support.
A thorough evaluation ensures you select a PLC that meets your specific requirements and supports future growth.
At Kwoco, we’re here to support you every step of the way, providing high-quality products and expert guidance.
Ready to enhance your automation projects with the best PLCs on the market? Explore our extensive range of new and original PLC products from top brands like Omron, Schneider, Mitsubishi, and Rockwell Automation.
Whether you need a solution for complex automation tasks or a reliable controller for your manufacturing line, we have the perfect PLC for you. For inquiries and further assistance, don’t hesitate to contact us.