How to Choose a Power Supply for a PLC
- kwoco-plc.com
- June 28, 2024
- 7:13 am
When it comes to industrial automation, choosing the right power supply for your Programmable Logic Controller (PLC) is crucial.
Without a reliable power source, your entire automation system could be at risk. But with so many options on the market, how do you make the right choice?
Table of Contents
Imagine your production line coming to a halt because of a power supply failure. It’s a scenario no engineer or purchasing manager wants to face.
The downtime, the cost implications, and the frustration of finding and fixing the issue can be overwhelming. Choosing the wrong power supply can lead to significant losses and operational inefficiencies.
Introduction
In this guide, we’ll explore how to select the perfect power supply for your PLC. We’ll break down the key factors you need to consider and highlight trusted brands like Omron, Mitsubishi, Schneider, and Siemens.
These industry leaders offer reliable solutions that can ensure your PLC systems run smoothly and efficiently.
What Factors Should You Consider?
Voltage Requirements
Ensure the power supply voltage matches your PLC’s needs. Common voltage levels include 24V DC and 230V AC.
However, the exact voltage requirements can vary between different brands and models. For example, Omron, Mitsubishi, Schneider, and Siemens PLCs may have specific voltage requirements that need to be met to ensure optimal performance.
Mismatched voltages can damage components or cause operational issues.
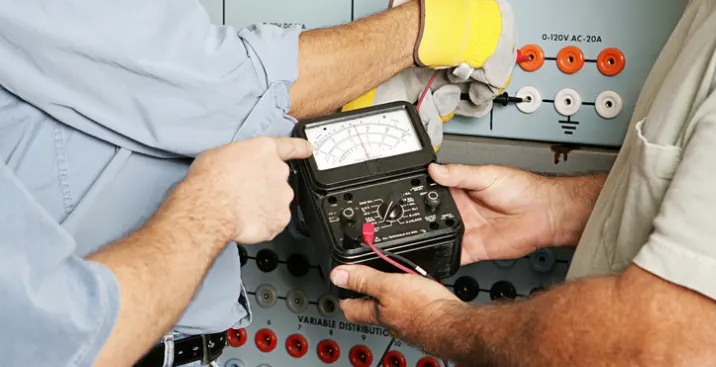
Current Requirements
Understanding the current requirements of your PLC system is equally important. To calculate the current requirements, you need to consider the total power consumption of the PLC and all connected devices.
This includes input/output modules, sensors, and actuators. Factors such as the number of connected devices, the operational load, and the power consumption of each component will affect the overall current consumption. It’s crucial to ensure that your power supply can deliver sufficient current to meet these needs.
For instance, if your PLC system has multiple modules and peripherals, you may need a power supply with a higher current rating to support the entire system without overloading. Accurate calculation and consideration of both voltage and current requirements will help you choose a power supply that ensures reliable and efficient operation of your PLC system.
Power Supply Calculations
Calculating Power Supply Needs
- List All Components: Identify all the devices that will be connected to the PLC, including input/output modules, sensors, and actuators.
- Check Specifications: Refer to the manufacturer’s specifications to find the power consumption (in watts or milliamps) for each component.
- Sum the Power Consumption: Add up the power consumption of all components to get the total power requirement. For example, if your PLC consumes 10W, each I/O module consumes 5W, and you have four modules, the total power requirement is 10W + (5W * 4) = 30W.
- Include a Safety Margin: Add a safety margin (typically 20-30%) to account for future expansions and to ensure reliable operation. In this example, the total power requirement would be 30W * 1.3 = 39W.
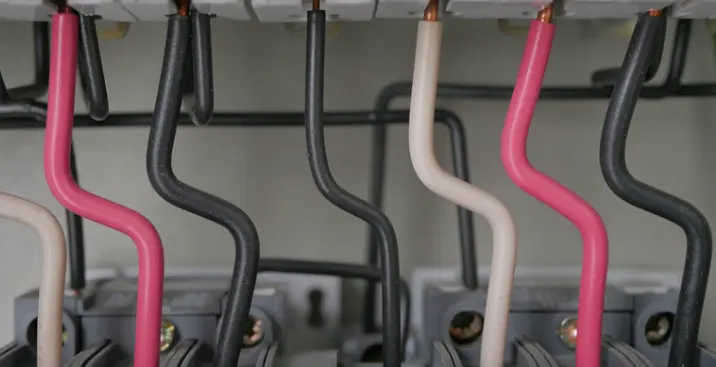
Sizing Your Power Supply
- Under-sizing: If the power supply is under-sized, it may not provide enough power, leading to system instability, frequent resets, or even damage to components.
- Over-sizing: While over-sizing is generally safer, excessively large power supplies can be less efficient, more expensive, and take up unnecessary space.
To avoid these issues, ensure that your power supply is appropriately sized by accurately calculating the total power requirements and including a reasonable safety margin.
This approach ensures that your PLC system operates smoothly, with sufficient power to handle all connected components without risking system performance or longevity.
Choosing the Right Power Module
Selecting a Power Module
- Compatibility: Ensure the power module is compatible with your specific PLC model and other connected devices. Check the voltage and current requirements to match the power module’s specifications.
- Efficiency: Choose a power module with high efficiency to minimize energy loss and heat generation. Efficient power modules help reduce operational costs and enhance the overall reliability of your system.
- Brand: Renowned brands like Omron, Mitsubishi, Schneider, and Siemens offer high-quality power modules that are well-regarded for their reliability and performance. Compare the features, warranties, and support services provided by these brands to make an informed decision.
Comparison of Power Modules from Leading Brands
- Omron: Known for innovation and reliability, Omron power modules offer robust performance and advanced features like overload protection and energy-saving modes.
- Mitsubishi: Mitsubishi power modules are designed for high efficiency and durability, providing stable power supply solutions suitable for various industrial applications.
- Schneider: Schneider power modules are highly efficient and feature-rich, with options for monitoring and diagnostics to ensure seamless operation.
- Siemens: Siemens power modules are renowned for their reliability and integration capabilities, making them ideal for complex automation systems.
Installation and Safety Tips
- Best Practices for Installing Power Modules:
- Follow Manufacturer Guidelines: Always adhere to the installation instructions provided by the manufacturer to avoid compatibility issues and potential damage.
- Ensure Proper Ventilation: Install power modules in well-ventilated areas to prevent overheating and ensure efficient operation.
- Secure Connections: Make sure all electrical connections are secure and free from corrosion to maintain reliable power delivery.
- Safety Considerations for Industrial Environments:
- Regular Inspections: Conduct routine inspections to check for signs of wear, damage, or overheating in power modules and associated wiring.
- Emergency Shutdowns: Implement emergency shutdown procedures to quickly power down the system in case of a fault or hazard.
- Protective Gear: Ensure that personnel handling power modules wear appropriate protective gear to prevent electrical shocks and injuries.
By carefully selecting the right power module and following best practices for installation and safety, you can enhance the reliability and efficiency of your PLC system, ensuring smooth and uninterrupted operation in demanding industrial environments.
DC Input Considerations
Understanding DC Input
DC input for PLCs involves supplying direct current (DC) power to the PLC system, which is converted from the alternating current (AC) power provided by the mains.
DC input power supplies are crucial for ensuring stable and reliable operation of PLCs and their connected components. These power supplies convert AC power to a consistent DC voltage, typically 24V DC, which is a standard requirement for most PLC systems
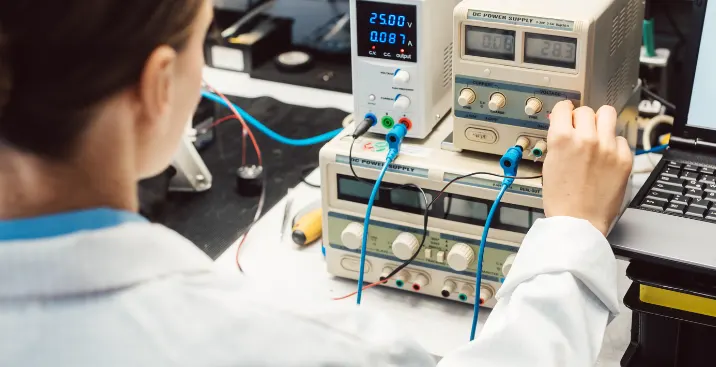
Benefits of Using DC Input Power Supplies
- Stability and Reliability: DC power provides a stable voltage with minimal fluctuations, reducing the risk of system resets or malfunctions.
- Efficiency: DC input power supplies are generally more efficient, with lower energy losses compared to AC power supplies.
- Noise Reduction: DC power reduces electrical noise, which can interfere with sensitive electronic components, ensuring smoother operation and improved performance.
Conclusion
Choosing the right power supply for your PLC involves considering voltage, current capacity, efficiency, redundancy, environmental conditions, certifications, and diagnostics.
By carefully evaluating these factors, you can ensure your PLC system operates reliably and efficiently, minimizing downtime and maximizing productivity.
For any inquiries or further assistance, get in touch with us today. Our team of experts is ready to help you find the perfect power supply and automation parts for your needs.
We offer a wide range of new and original automation components from leading brands like Omron, Mitsubishi, Schneider, and Siemens. Whether you have questions about product specifications or need technical support, we’re here to provide the guidance you need.