Cómo transferir un programa de PLC a un nuevo PLC
Tabla de contenido
Introducción: Por qué su sistema PLC necesita urgentemente una actualización de su "cerebro"
En los entornos de fabricación altamente automatizados actuales, el PLC funciona como el "cerebro" del sistema de control comercial. Gestiona silenciosamente cada actividad en la línea de montaje, garantizando la precisión y el rendimiento del proceso. Sin embargo, varios sistemas PLC que han estado en funcionamiento durante un año o más están pasando gradualmente de ser activos valiosos a ser un lastre latente. Es posible que no sean compatibles con los protocolos de red modernos, tengan una capacidad de procesamiento de datos limitada, se enfrenten a costos de mantenimiento desorbitados debido a la caducidad de las piezas de repuesto y, lo más importante, representen una barrera invisible para la transformación digital de una empresa. Por lo tanto, implementar una tecnología PLC y migrar los sistemas tradicionales a un sistema de nueva generación es una medida importante para que las empresas conserven su lado tecnológico, mejoren la durabilidad operativa y adopten la fabricación inteligente. Si bien el proceso es complejo, se puede lograr a la perfección con una preparación precisa y un enfoque científico, reduciendo el tiempo de inactividad de la producción y generando un valor comercial considerable.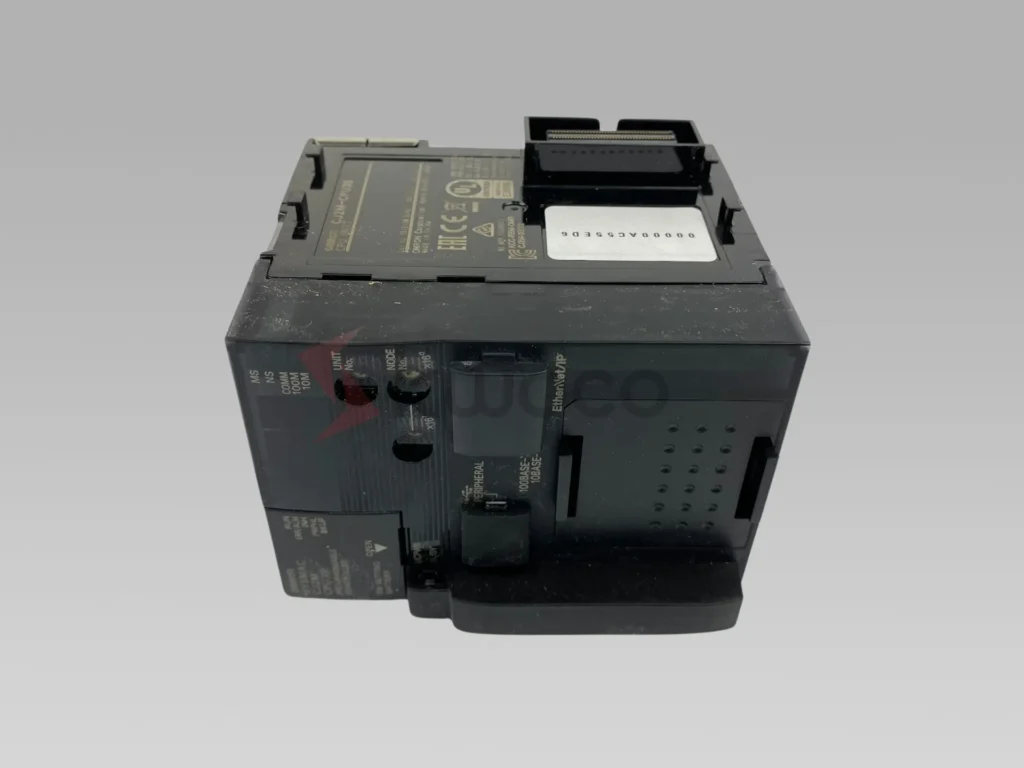
I. Planificación y evaluación meticulosas antes de la migración del PLC
Una migración eficaz comienza con una preparación completa. Antes de tocar cualquier tipo de código o hardware, es fundamental una preparación estratégica exhaustiva para evitar la expansión del alcance del proyecto y su fracaso.1. Especificar los impulsores y objetivos de la migración
En primer lugar, abordemos la pregunta central: "¿Por qué estamos emprendiendo esta migración?". Las presiones que la impulsan podrían incluir:Mejora de la eficiencia: Los nuevos PLC cuentan con CPU más rápidas y mayor memoria, lo que les permite encargarse de razonamientos más complejos y reducir los tiempos del ciclo de verificación.Integración de redes y datos: Los sistemas modernos sustentan procedimientos Ethernet industriales modernos como Profinet y EtherNet/IP, lo que ayuda a una combinación perfecta con sistemas MES, ERP y en la nube para sentar las bases para el análisis de información y la anticipación del mantenimiento.Mayor confiabilidad y seguridad del sistema: Los sistemas heredados se enfrentan a los riesgos de las piezas de repuesto descontinuadas, mientras que las líneas de productos PLC completamente nuevas están completamente desarrolladas e incluyen atributos de ciberseguridad robustos e integrados.Expansión práctica: Obtener soporte para funcionalidades avanzadas como control de actividad, visión de equipos y otras tecnologías integradas.2. Realizar una auditoría del sistema y una evaluación de riesgos exhaustivas
Auditoría de equipos: Documente meticulosamente el diseño, la versión de la CPU, los módulos de E/S, los componentes de funciones especiales (por ejemplo, contadores de alta velocidad, módulos de posicionamiento) y los componentes de comunicación de red del PLC existente.Auditoría de programas de software: Realice un análisis exhaustivo del programa existente. Comprenda su lógica de control, la estructura del programa (regímenes primarios, subrutinas, interrupciones), los marcos de datos (bloques de datos o BD) y los procedimientos de comunicación y los factores de información utilizados para la interfaz de usuario con sistemas de nivel superior, como Interfaz hombre-máquina (IHM) y SCADA.Evaluación de riesgos: Identifique posibles peligros durante el traslado, como incompatibilidades de conversión de programas, errores de asignación de direcciones de E/S, interrupciones de la comunicación y tiempos de inactividad excesivos en la fabricación. Establezca estrategias de contingencia adecuadas.3. Prepare herramientas y recursos esenciales
Asegúrese de contar con el software de visualización ideal para las plataformas PLC, tanto antiguas como nuevas. Por ejemplo, migrar de un Siemens S7-300 a un S7-1500 requiere la transición de STEP 7 Classic al más eficaz TIA Portal (Totally Integrated Automation Portal). Además, prepare cables de software, tarjetas de memoria y un banco de pruebas dedicado.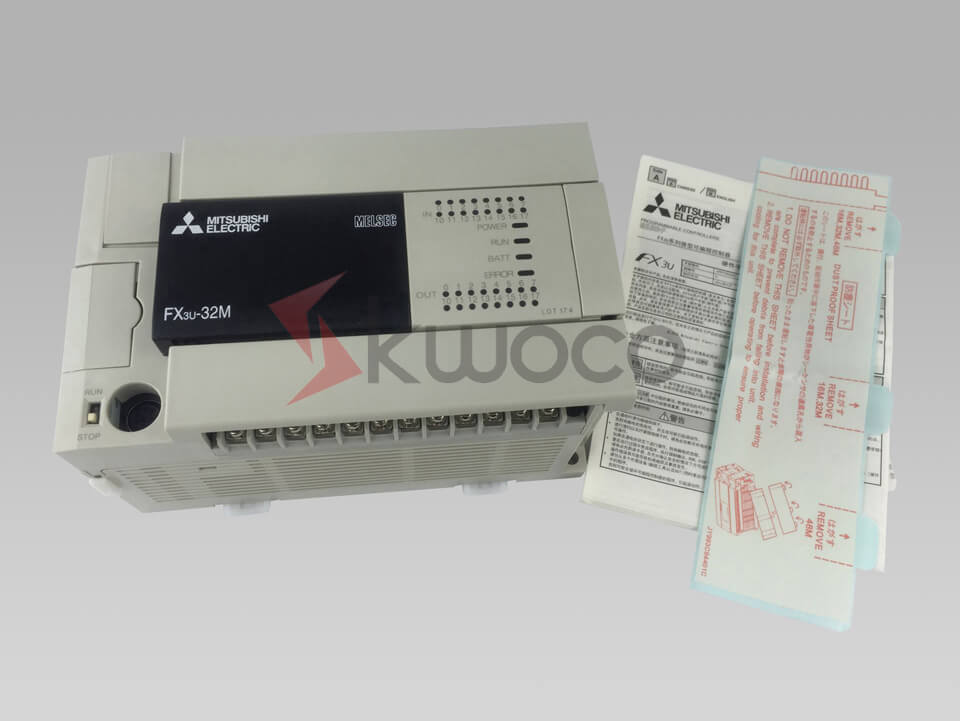
II. La fase central: Conversión del programa PLC y modernización del código
Este es el núcleo técnico del proceso de migración. El desafío no solo reside en equiparar el código, sino también en aprovechar la oportunidad para optimizar y mejorar el programa.1. Copia de seguridad y carga del programa
Antes de iniciar cualquier cambio, realice una copia de seguridad completa del programa, los datos y la configuración del equipo del PLC existente. Esta es la última medida de seguridad de su proyecto. A continuación, utilice el software de programación tradicional para enviar el programa completo a su estación de trabajo de ingeniería.2. Conversión de programas: conversión directa vs. refactorización completa
Hay dos enfoques principales para la conversión de programas:Conversión automatizada/semiautomatizada: Muchos proveedores líderes ofrecen dispositivos de movimiento. El TIA Portal de Siemens, por ejemplo, incorpora una función de migración para convertir tareas del S7-300/400 al sistema S7-1200/1500. Esta técnica permite transformar rápidamente la mayoría de las instrucciones y bloques de datos habituales, pero probablemente requiera ajustes manuales para ciertas instrucciones específicas, código dependiente del hardware (p. ej., P_SEND/P_RECV) o bibliotecas personalizadas.Refactorización manual: Para tareas con razonamiento obsoleto, una estructura compleja o documentación original faltante, una reescritura completa podría ser la opción excepcional. Si bien requiere mayor esfuerzo, esto brinda una oportunidad excepcional para optimizar la estructura del programa, agregar comentarios exhaustivos y adoptar metodologías de programación más confiables (como el uso estándar de bloques de función). Esto mejora sustancialmente la legibilidad y la mantenibilidad a largo plazo del programa.3. Evaluación de los puntos clave de conversión
Modernización de direcciones y etiquetas: Los esquemas de direccionamiento de E/S y memoria (p. ej., direcciones M y DB) de los PLC nuevos pueden variar con respecto a los de los sistemas tradicionales. Es importante transformar todas las direcciones absolutas codificadas en programas adaptables y simbólicos (programas basados en etiquetas), lo cual es ideal en las presentaciones de PLC actuales.Manejo de discrepancias en el conjunto de instrucciones: Las colecciones de direcciones pueden variar entre las distintas generaciones de PLC. Por ejemplo, algunas instrucciones de comunicación antiguas se sustituyen por instrucciones nuevas y más eficaces en las plataformas actuales. Es necesario consultar atentamente las guías de movimiento del proveedor para realizar sustituciones equivalentes.Configuración de interacción: Actualice las configuraciones tradicionales de serie o MPI/Profibus-DP a procedimientos modernos basados en Ethernet, como Profinet o EtherNet/IP. Restablezca los enlaces de comunicación con dispositivos como HMI. VFD (variadores de frecuencia)y terminales de E/S remotas.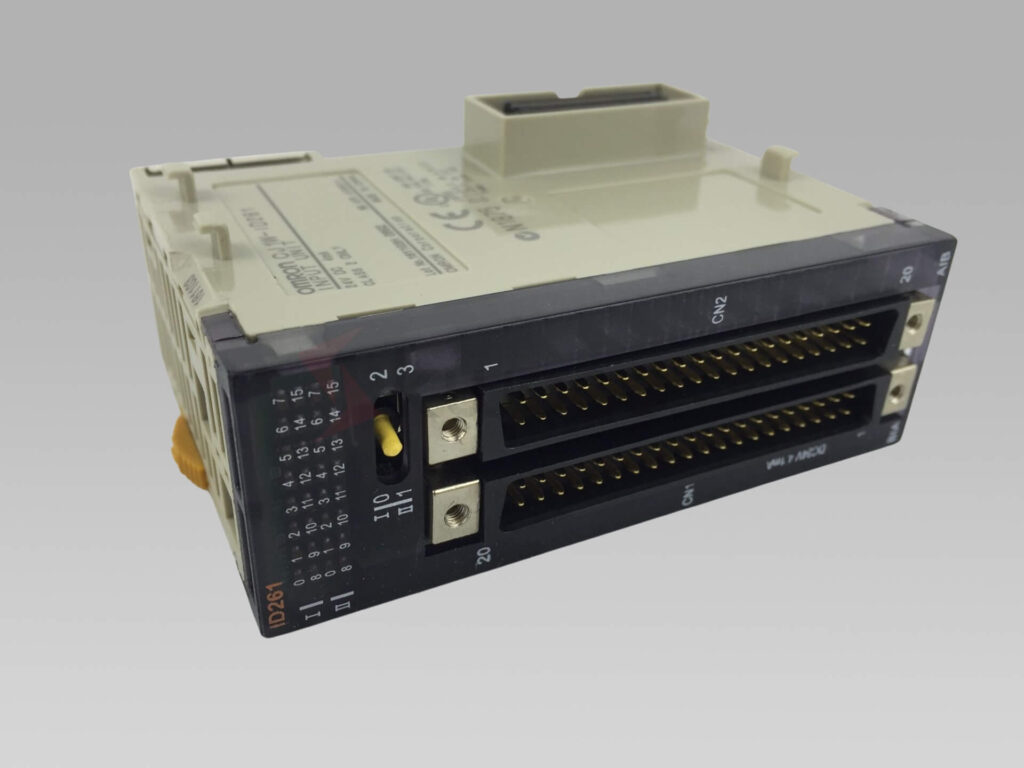
III. Análisis comparativo de las rutas de migración de las plataformas PLC convencionales
Seleccionar la nueva plataforma ideal es fundamental para una migración eficaz. Diversas marcas ofrecen distintas funciones de productos y asistencia para la migración.Dimensión de característica | Siemens | Automatización Rockwell | Mitsubishi Eléctrico |
Ruta de actualización típica | S7-300/400 → S7-1500 | PLC-5/SLC 500 → ControlLogix/CompactLogix | Serie FX/Q → Serie iQ-R/iQ-F |
Software de programación básica | Portal TIA | Diseñador Logix Studio 5000 | Obras GX3 |
Herramientas de apoyo a la migración | TIA Portal tiene herramientas de migración integradas que admiten la conversión directa de proyectos y el análisis de código. | Proporciona una herramienta de traducción para ayudar a convertir proyectos heredados al nuevo formato de la plataforma. | GX Works3 incluye un asistente de importación compatible con archivos de proyectos heredados y proporciona orientación sobre la conversión. |
Ventajas clave | Plataforma altamente integrada con fuerte sinergia hardware-software; conceptos avanzados en programación simbólica y estandarización; potentes funciones de diagnóstico. | Estructura de datos flexible basada en etiquetas con ventajas significativas en aplicaciones de control de procesos; las instrucciones complementarias (AOI) facilitan la reutilización del código. | Amplia línea de productos con una alta relación costo-rendimiento; ampliamente utilizado en máquinas independientes y sistemas de pequeña escala; fuertes capacidades de posicionamiento y control de movimiento. |
Desafíos potenciales | TIA Portal tiene requisitos de sistema más elevados para el PC de ingeniería; el cambio de paradigma del clásico STEP 7 a TIA Portal implica una curva de aprendizaje. | Los costos de hardware pueden ser relativamente altos; la migración de programas entre diferentes familias requiere atención a los detalles. | La compatibilidad de programas entre diferentes series requiere una verificación cuidadosa; algunas instrucciones especiales necesitan modificación manual. |
IV. Nombramiento e integración: garantizar el funcionamiento impecable del nuevo «cerebro»
Cuando se completa la conversión del programa, es importante realizar una evaluación y una puesta en marcha rigurosas para garantizar un cambio de producción sin problemas.1. Simulación fuera de línea y puesta en servicio virtual
Antes de descargar e instalar el programa en el PLC físico, utilice los dispositivos de simulación del software (p. ej., PLCSIM Advanced) para realizar pruebas exhaustivas. Al conectar una HMI virtual e imitar diferentes problemas operativos y situaciones de error, podrá identificar la gran mayoría de los errores lógicos, minimizando considerablemente el tiempo de programación in situ.2. Puesta en servicio in situ
La designación in situ debe realizarse en etapas:Comprobación de E/S: Con los actuadores desconectados, pruebe cada señal de entrada para validar que se lea correctamente y que cada resultado indique que puede ser controlado apropiadamente por el programa.Pruebas específicas de máquinas/funciones: Pruebe las actividades de dispositivos individuales o las funciones del vecindario para asegurarse de que el razonamiento sea correcto.Pruebas de enclavamiento e integración de sistemas: Integre el nuevo PLC directamente en el sistema general. Realice pruebas de comunicación con HMI, SCADA, robots y otros PLC para confirmar la sincronización de todo el proceso de producción.Optimización del rendimiento y pruebas cardiovasculares: Operar el sistema durante un periodo prolongado en condiciones de fabricación reales o de reemplazo. Supervisar su estabilidad, tiempo de respuesta y uso de recursos (carga de CPU, memoria) y realizar las optimizaciones necesarias según los resultados.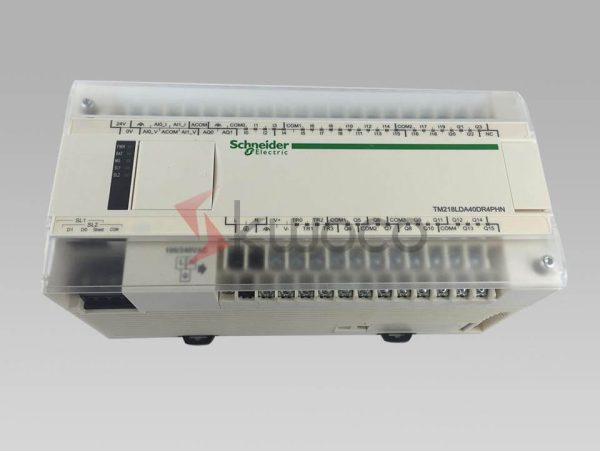
V. Cierre del proyecto: Documentos y capacitación para consolidar el éxito de la migración
Un trabajo exitoso no es sólo aquel que se mantiene sino también aquel que se puede conservar y reconocer durante muchos años.Actualizar la documentación técnica: Cree documentación detallada para el nuevo sistema, incluidos esquemas eléctricos actualizados, listas de verificación de E/S, representaciones de geografía de red, tablas de etiquetas y, lo más importante, una impresión o PDF del programa PLC con comentarios claros y considerables.Capacitación de personal: Proporcionar capacitación organizada para conductores e ingenieros de mantenimiento. El programa debe abarcar la familiarización con el nuevo hardware del PLC, el funcionamiento del nuevo software de programación, los procedimientos de arranque y cierre del sistema, y los métodos estándar de diagnóstico médico de averías.Potencie sus proyectos con PLC Omron, Mitsubishi y Schneider nuevos y originales: ¡en stock y listos ahora!
Conclusión
Migrar un programa PLC a un nuevo sistema es mucho más que una simple copia y pega. Es un trabajo de ingeniería complejo que implica una preparación crítica, gestión de riesgos, una implementación tecnológica cuidadosa y un reconocimiento completo del sistema.
Siguiendo las acciones organizadas que se detallan en este resumen (desde una evaluación exhaustiva previa a la migración y la conversión y la innovación de programas específicos hasta una puesta en marcha y combinación exhaustivas y una documentación y capacitación completas), las empresas pueden transformar este desafío tecnológico en una oportunidad calculada para aumentar su grado de automatización y mejorar su competitividad básica.
Contáctenos
Simplemente complete su nombre, dirección de correo electrónico y una breve descripción de su consulta en este formulario. Nos comunicaremos con usted dentro de las 24 horas.
Categoría de producto
Productos en oferta
También te pueden interesar estos temas
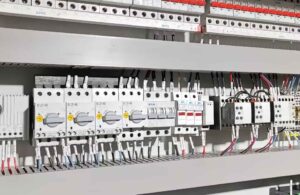
Relés: Guía de tipos y aplicaciones
Este artículo ofrece una mirada profunda a los relés, los héroes anónimos de muchos sistemas eléctricos. Exploraremos los diferentes tipos de relés, sus aplicaciones y cómo funcionan. Ya sea que sea ingeniero, técnico o simplemente sienta curiosidad por cómo funcionan las cosas, esta guía completa le iluminará el fascinante mundo de los relés.
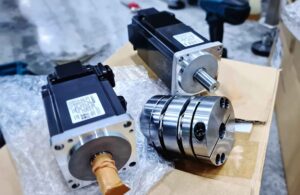
Los 5 principales proveedores de servomotores Mitsubishi en Canadá
Como ingeniero dedicado en Kwoco, he pasado años explorando el panorama de la automatización industrial. Mi experiencia con marcas de renombre internacional como Mitsubishi me ha proporcionado el conocimiento necesario para identificar a los mejores proveedores del mercado.
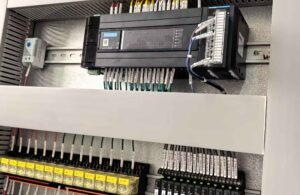
PLC vs VFD: Comprensión de los controladores lógicos programables y los variadores de frecuencia
Este artículo profundiza en el mundo de la automatización industrial, explorando el papel crucial de los controladores lógicos programables (PLC) y los variadores de frecuencia (VFD). Desglosaremos sus funciones, compararemos sus fortalezas y debilidades, y explicaremos cómo trabajan juntos para optimizar los procesos industriales. Tanto si trabaja en la fabricación de maquinaria, soluciones de fábrica o simplemente siente curiosidad por la automatización moderna, esta guía le proporcionará una comprensión clara de estos componentes esenciales.