What You Need to Know About Digital and Analog Inputs in PLCs
- kwoco-plc.com
- September 24, 2024
- 2:15 am
Have you ever wondered how your industrial automation systems communicate with the real world? Understanding the difference between digital and analog inputs in Programmable Logic Controllers (PLCs) is crucial. It can make or break the efficiency of your engineering projects.
Digital inputs are binary, representing on/off states, while analog inputs provide continuous data, allowing for a wider range of control.
In the world of industrial automation, every detail matters. As an engineer at Kwoco, I’ve seen firsthand how these inputs affect system performance and reliability. If you’re responsible for sourcing PLC components or managing engineering projects, this information is vital.
Table of Contents
What Exactly Are Digital and Analog Inputs?
Digital inputs are designed to recognize two distinct states: high (1) and low (0). They’re typically used for devices that operate in a binary fashion, such as limit switches, push buttons, and relays. Digital signals provide a straightforward way to determine whether a device is active or inactive.
On the other hand, analog inputs can process a range of values, making them suitable for devices like temperature sensors, pressure transducers, and flow meters. These inputs convert real-world phenomena into data that PLCs can understand, allowing for precise control over processes.
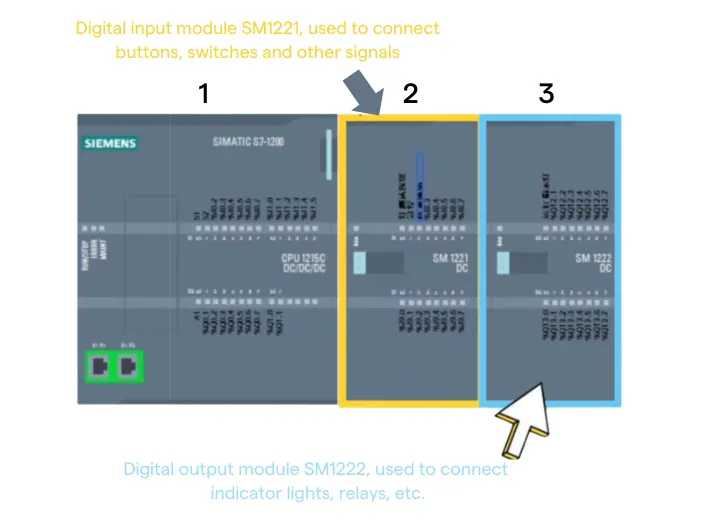
Why Does It Matter?
The choice between digital and analog inputs can significantly impact your project outcomes. Understanding their strengths helps you make informed decisions during the procurement process.
For example, if you’re overseeing a project that requires real-time data monitoring, analog inputs might be your best bet. Conversely, for simple on/off controls, digital inputs are more than adequate.
In this post, we’ll delve deeper into the characteristics, applications, and benefits of each input type.
How Are Digital Inputs Used in Automation?
Digital inputs serve a critical role in industrial automation. They are widely used for controlling machines, monitoring safety systems, and executing basic functions.
For instance, consider a packaging line where a sensor detects whether a box is present. This sensor generates a digital signal that the PLC interprets to start or stop the conveyor belt. Such applications highlight the simplicity and reliability of digital inputs.
What About Analog Inputs?
Analog inputs offer a level of sophistication that digital inputs can’t match. They are essential in applications where conditions vary continuously.
Take temperature control in a manufacturing process. An analog temperature sensor provides real-time data to the PLC, allowing it to adjust heating elements precisely. This level of control can significantly enhance product quality and energy efficiency.
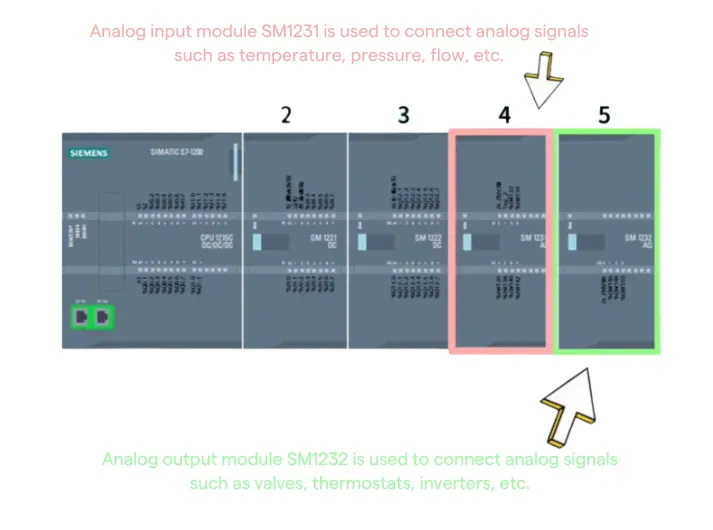
What Are the Key Differences?
Here are some critical differences between digital and analog inputs:
- Signal Type: Digital inputs are binary, while analog inputs are continuous.
- Complexity: Digital systems are simpler and easier to troubleshoot. Analog systems require more complex wiring and configuration.
- Data Range: Digital inputs are limited to two states, whereas analog inputs can represent a vast range of values.
- Applications: Digital inputs are ideal for on/off controls, while analog inputs excel in measuring variables that change over time.
Which One Should You Choose?
The decision to use digital or analog inputs depends on your specific application. Here are some guiding questions to help you determine the best option:
- What kind of signals does your system need to process?
- Are you dealing with binary states or continuous measurements?
- How important is precision in your application?
- What devices will you be integrating into your PLC?
- Do you require real-time data feedback?
- What are your budgetary constraints?
By answering these questions, you’ll be better positioned to select the right input type for your engineering project.
The Integration Challenge
Integrating digital and analog inputs can be challenging. Many PLCs offer both types of inputs, but the configuration may require specific knowledge.
Proper calibration of analog sensors is essential to ensure accurate readings. If not calibrated correctly, you risk erroneous data, which can lead to poor decision-making.
For digital inputs, wiring and signal integrity are crucial. Faulty connections can result in intermittent signals, causing machinery to operate incorrectly.
Power your projects with brand-new, original Omron, Mitsubishi, Schneider PLC – in stock, ready now!
Real-World Applications
In a real-world setting, both digital and analog inputs are frequently used together to create a comprehensive control system. For instance, a water treatment facility might use digital inputs to monitor pumps while utilizing analog inputs to measure water quality parameters such as pH and turbidity.
This integration allows for a responsive and adaptable system. It can adjust the treatment process based on real-time data, leading to improved outcomes.
Potential Pitfalls to Avoid
While both digital and analog inputs have their advantages, there are common pitfalls to watch for:
- Ignoring Compatibility: Not all sensors are compatible with every PLC. Always verify specifications.
- Neglecting Maintenance: Regular checks on analog sensors are crucial for accuracy.
- Overcomplicating Systems: Sometimes, simple solutions (like using digital inputs) can achieve the desired outcomes without added complexity.
Conclusion
With this knowledge in your toolkit, you’re equipped to make better decisions for your engineering projects. If you have any questions or need support in selecting the right components, don’t hesitate to get in touch. At Kwoco ([email protected]), we’re here to help you achieve your automation goals.
Contact Us
Just fill out your name, email address, and a brief description of your inquiry in this form. We will contact you within 24 hours.
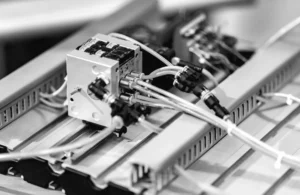
Why Your PLC Needs a Separate Power Supply
Why Your PLC Needs a Separate Power Supply Have you ever wondered why PLC systems often require a separate power
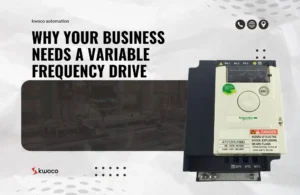
Why Your Business Needs a Variable Frequency Drive
Why Your Business Needs a Variable Frequency Drive When managing industrial operations, optimizing energy efficiency while maintaining performance is crucial.
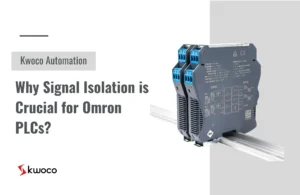
Why Signal Isolation is Crucial for Omron PLCs?
Why Signal Isolation is Crucial for Omron PLCs? In the world of industrial automation, signal interference is a silent killer.