Défauts courants et dépannage des API Omron
Table des matières
Le fonctionnement stable de ces systèmes est directement lié à l'efficacité de la production, à la qualité des produits et aux coûts d'exploitation. Par conséquent, la capacité à diagnostiquer et à résoudre rapidement et précisément les problèmes est essentielle. Automate programmable Les défauts sont essentiels pour maintenir la compétitivité de base d’une entreprise.
Ce document décrit systématiquement les procédures et techniques de dépannage basées sur des Automate programmable Omron scénarios d'application.
1. Système d'alimentation : la base d'un fonctionnement stable des automates programmables industriels
Une alimentation électrique fiable est essentielle au bon fonctionnement d'un automate programmable. Les pannes d'alimentation électrique entraînent souvent des arrêts immédiats et complets du système.
- Phénomènes courants : L'automate ne parvient pas à s'allumer complètement (aucun indicateur allumé) ou présente un état anormal lors de la mise sous tension (par exemple, la LED ERROR est allumée en continu ou clignote).
- Analyse approfondie des causes :
- Alimentation externe : La tension d'entrée fluctue au-delà de la plage de tolérance spécifiée par l'API (généralement ±10% ou ±15% – consultez le manuel du matériel spécifique), les bornes de câblage sont desserrées ou oxydées provoquant une résistance de contact élevée ou les câbles d'alimentation sont endommagés.
- Module d'alimentation PLC : Défaillance ou dégradation des composants internes (par exemple, fusibles, condensateurs, circuits intégrés de régulation de tension). Pour les automates programmables modulaires, un mauvais contact entre le module d'alimentation et le fond de panier peut également entraîner des problèmes.
- Stratégie de dépannage efficace :
- Vérifier la puissance d'entrée : Utilisez un multimètre étalonné pour mesurer précisément la tension aux bornes d'entrée du module d'alimentation de l'automate. Assurez-vous que la tension est stable et dans la plage spécifiée dans la fiche technique.
- Inspecter les connexions physiques : Vérifiez que tous les câbles électriques sont bien connectés, correctement raccordés et exempts de courts-circuits ou de coupures. Vérifiez l'intégrité des fiches et des prises de courant.
- Éliminer les interférences externes : Vérifiez si des équipements haute puissance branchés sur la même ligne électrique provoquent des perturbations. Envisagez l'installation d'un filtre de ligne ou d'un stabilisateur/régulateur de tension si nécessaire.
- Test de substitution de module : Si des pièces de rechange sont disponibles, remplacez le module d'alimentation existant par un modèle identique afin de déterminer si le défaut provient du module lui-même. Consultez le Site officiel d'Omron pour obtenir des informations et des spécifications sur les modules compatibles.
2. Canaux d'entrée/sortie (E/S) : le pont vers les appareils de terrain
Les modules d'E/S gèrent l'échange de signaux entre l'automate programmable industriel (API) et les équipements de terrain tels que les capteurs et les actionneurs. Les défauts d'E/S empêchent l'API de détecter avec précision les conditions de terrain ou de contrôler correctement les équipements.
- Phénomènes courants : Un point d'entrée spécifique reste constamment allumé ou éteint, ne reflétant pas l'état réel du capteur ; un point de sortie spécifique ne parvient pas à alimenter sa charge (par exemple, électrovanne, voyant lumineux) ou son état est anormal.
- Analyse approfondie des causes :
- Câblage et appareils externes : Capteur ou actionneur défectueux, câblage incorrect (par exemple, incompatibilité NPN/PNP), courts-circuits ou circuits ouverts dans le câblage de terrain, mauvaises connexions des bornes.
- Matériel du module d'E/S : Défaillance de composants internes tels que les optocoupleurs, relais, ou des transistors à l'intérieur du module ; mauvais contact entre le module d'E/S et le fond de panier.
- Configuration et programme : Affectation d'adresse d'E/S incorrecte dans la configuration de l'API ou erreurs de logique de programme empêchant le pilotage correct du point d'E/S correspondant.
- Stratégie de dépannage efficace :
- Observer les indicateurs d’état : La plupart des modules d'E/S Omron disposent de LED d'état pour chaque point, fournissant une indication initiale indiquant si les signaux atteignent le module et si le module tente d'activer les sorties.
- Utiliser la fonction « Forcer » (à utiliser avec précaution) : Dans le logiciel de programmation (par exemple, CX-Programmer ou Sysmac Studio), utilisez la fonctionnalité Forcer ON/OFF. Cela permet de tester directement si un point de module de sortie peut gérer sa charge, ou d'observer si l'état d'un point d'entrée peut être remplacé manuellement dans le logiciel. Cela permet de différencier les problèmes externes du module/programme. Remarque : le forçage des E/S contourne la logique normale et peut entraîner un comportement inattendu de la machine ; soyez extrêmement prudent.
- Vérifier les circuits externes : Débranchez le câblage de terrain des bornes du module. Utilisez un multimètre, un générateur de signaux ou un équipement de test approprié pour tester directement le fonctionnement du capteur/actionneur et l'intégrité des câbles de connexion.
- Échange de modules et tests croisés : Remplacez le module d'E/S suspect par un module identique et en bon état, provenant d'un autre emplacement ou d'un module de rechange (notez qu'une reconfiguration de l'adresse peut être nécessaire selon la série et la configuration de l'automate). Vérifiez si le défaut se localise au niveau du module ou de l'emplacement/canal.
3. Logique et mémoire du programme : garantir la stabilité du cœur de contrôle
Le programme utilisateur est l'intelligence centrale de l'automate programmable, dictant son comportement de contrôle. Les erreurs qui y sont commises ont un impact direct sur le fonctionnement du système.
- Phénomènes courants : L'équipement fonctionne contrairement à la séquence logique prévue, le système s'arrête ou génère des erreurs dans des conditions spécifiques, le téléchargement ou le chargement du programme échoue.
- Analyse approfondie des causes :
- Erreurs de logique du programme : Logique conditionnelle incomplète, conflits de timing, erreurs algorithmiques, conditions de course, boucles infinies.
- Problèmes de traitement des données : Débordement de données, incompatibilités de type de données pendant les opérations, variables intermédiaires critiques écrasées involontairement.
- Problèmes de mémoire : Corruption dans les zones de mémoire du programme ou des données (moins fréquente, mais possible en raison d'un bruit électrique important, d'une fin de vie ou d'un choc physique) ; épuisement de la batterie entraînant la perte de données rémanentes (pour les automates utilisant une RAM alimentée par batterie).
- Incompatibilité de version : Incompatibilité entre la version du micrologiciel de l'API, la version du logiciel de programmation utilisée ou la dépendance du programme à des versions de blocs de fonctions spécifiques.
- Stratégie de dépannage efficace :
- Surveillance et débogage en ligne : Exploitez les capacités de surveillance en ligne du logiciel de programmation. Observez l'état d'exécution en temps réel des échelons du ladder ou des sections de code, suivez les valeurs des variables et suivez le flux logique étape par étape. Utilisez des points d'arrêt pour interrompre l'exécution à des moments précis et effectuer une analyse détaillée.
- Vérification et comparaison des programmes : Assurez-vous que le programme en cours d'exécution dans l'automate correspond à la version maître enregistrée sur le poste de travail d'ingénierie. Effectuez des sauvegardes régulières du programme. Utilisez la fonction de comparaison du logiciel, si disponible.
- Interpréter les codes d'erreur : Lorsque l'API entre en état d'erreur (indiqué par le voyant d'erreur et des indicateurs/registres spécifiques), connectez-vous au logiciel de programmation pour lire le code d'erreur et le message détaillés. Consultez les manuels de référence du matériel et des instructions Omron de la série d'API concernée pour comprendre la signification du code et les actions recommandées. Le respect de pratiques de programmation structurées, telles que celles décrites dans la norme CEI 61131-3, peut contribuer à minimiser les erreurs logiques.
- Vérifier l'état et les diagnostics de l'API : Utilisez les fonctions de diagnostic du logiciel de programmation pour vérifier l'état général de l'API, y compris l'état de la mémoire, la tension de la batterie (le cas échéant), le temps de cycle et les erreurs système.
4. Réseau de communication : les artères de l'échange d'informations
Les systèmes d’automatisation modernes impliquent souvent une communication en réseau entre plusieurs automates programmables, IHM, Variateurs de fréquence, systèmes de vision et autres appareils intelligents.
- Phénomènes courants : L'automate ne parvient pas à communiquer avec un système hôte (SCADA/HMI) ou d'autres périphériques réseau, les données de communication sont erronées ou perdues par intermittence, les indicateurs d'état du réseau sur les modules/ports se comportent de manière anormale.
- Analyse approfondie des causes :
- Lien physique : Câbles réseau (Ethernet) ou câbles série (RS232/485) endommagés, connecteurs desserrés, mise à la terre du blindage incorrecte, résistances de terminaison manquantes ou incorrectes (essentielles pour RS485/CAN).
- Configuration des paramètres : Conflits d'adresses IP ou incompatibilités de sous-réseau (Ethernet), débit en bauds, bits de données, bits d'arrêt ou paramètres de parité (série) incorrects, numéros de station/adresses de nœud en double, paramètres de protocole de communication incorrects.
- Charge et interférences du réseau : Trafic réseau excessif provoquant des collisions ou des retards, interférences électromagnétiques (EMI) corrompant les signaux de communication.
- Défaillance du module/port : Dysfonctionnement matériel du port de communication intégré de l'automate ou d'un module de communication complémentaire.
- Stratégie de dépannage efficace :
- Inspecter les connexions physiques et les indicateurs : Vérifiez l'intégrité du câble et la sécurité des connexions aux deux extrémités. Observez les voyants de liaison/activité sur les ports/modules de communication pour obtenir des informations d'état (par exemple, liaison établie, transmission/réception de données).
- Vérifier les paramètres de communication : Vérifiez méticuleusement les paramètres de communication (adresse IP, masque de sous-réseau, passerelle, débit en bauds, parité, adresse de nœud, etc.) sur tous Dispositifs impliqués dans la liaison de communication spécifique. Assurer une cohérence absolue.
- Simplifier le réseau pour les tests : Isolez le problème de communication en testant les connexions point à point. Déconnectez les autres appareils et essayez de communiquer uniquement entre l'automate et un autre appareil. Utilisez des outils standard comme
ping
commande (pour les réseaux Ethernet) ou logiciel de test série/réseau spécialisé. - Utiliser les outils de diagnostic : Les suites logicielles d'Omron, comme CX-One (contenant Network Configurator) ou Sysmac Studio, incluent souvent des outils de diagnostic réseau. Ceux-ci permettent de visualiser le réseau, d'identifier les appareils connectés, de vérifier l'état des nœuds et de surveiller le trafic.
- Consulter la documentation du protocole : Assurez-vous de bien comprendre le protocole de communication utilisé (par exemple, EtherNet/IP, Modbus TCP, RS485 Modbus RTU, FINS d'Omron). Consultez les manuels et les spécifications du protocole Omron pour plus de détails sur la structure des messages, la synchronisation et la gestion des erreurs.
5. Autres problèmes courants et résolutions
Catégorie de défaut | Causes potentielles | Suggestions de dépannage rapide | Mesures préventives |
---|---|---|---|
Défaut du module d'extension | Défaillance matérielle du module, mauvaise connexion au fond de panier, incompatibilité de configuration (table d'E/S), problème de câble de bus | Vérifiez les indicateurs du module, réinstallez fermement le module, vérifiez les connexions des câbles de bus, revérifiez la configuration de la table d'E/S dans le logiciel | Nettoyez régulièrement les emplacements, assurez un montage sécurisé et sauvegardez la configuration |
Surchauffe | La température ambiante dépasse les spécifications, la ventilation/le flux d'air est médiocre, l'accumulation de poussière, la charge excessive du processeur/module | Mesurer la température ambiante, nettoyer les ventilateurs et les évents, vérifier le pourcentage de charge de l'automate (temps de cycle) | Assurez un refroidissement/une ventilation adéquat du panneau de commande, évitez la lumière directe du soleil, effectuez un nettoyage régulier |
Logiciel/Compatibilité | Version du logiciel de programmation incompatible, pilotes manquants, conflits de système d'exploitation sur le PC de programmation | Mettre à jour le logiciel/micrologiciel vers des versions compatibles, installer les pilotes corrects, vérifier les exigences de l'environnement PC | Utiliser les versions logicielles officiellement recommandées, maintenir le système d'exploitation à jour, documenter les configurations logicielles/matérielles |
Module de fonctions spéciales | Défaillance matérielle du module, paramètres incorrects (par exemple, compteur à grande vitesse, sortie d'impulsions) | Testez avec un module de rechange, examinez méticuleusement le manuel du module et les paramètres, utilisez les diagnostics logiciels pour le module | Comprendre parfaitement les capacités du module et les définitions des paramètres, suivre précisément les instructions du manuel |
Risques liés à la mise à niveau du système | Incompatibilité du micrologiciel/programme après la mise à niveau, corruption des données due à une mise à niveau interrompue | Essentiel : sauvegardez le programme et les données avant la mise à niveau, lisez attentivement les notes de version, assurez-vous d'une alimentation et d'une communication stables pendant la mise à niveau | Choisissez les fenêtres de mise à niveau appropriées, contactez l'assistance technique Omron en cas de doute |
Perspective d'analyse des données : incidence des pannes et impact des temps d'arrêt (exemple illustratif)
Bien que les données précises varient considérablement selon les spécificités des applications et les pratiques de maintenance, l'expérience du secteur suggère certaines tendances dans la distribution des types de pannes. Le tableau suivant présente données illustratives à titre de référence uniquement :
Type de défaut | Fréquence relative estimée | Impact moyen des temps d'arrêt (non préparé) | Impact moyen des temps d'arrêt (diagnostic préparé/qualifié) |
---|---|---|---|
Défaut d'alimentation électrique | Moyen | Élevé (arrêt total du système) | Moyen (nécessite une pièce de rechange) |
Défaut d'E/S | Haut | Moyen (échec de fonction locale) | Faible (identification rapide des points et réparation/remplacement) |
Erreur de logique du programme | Moyen-élevé | Moyen à élevé (comportement erratique/arrêt) | Moyen (selon les compétences de débogage) |
Défaut de communication | Moyen-élevé | Moyen à élevé (défaillance de la liaison système) | Moyen (vérification des paramètres/test de lien) |
Défaut du module matériel | Faible à moyen | Moyen (nécessite une pièce de rechange) | Faible à moyen (remplacement de pièces de rechange) |
Environnemental/Autre | Faible | Faible à moyen | Faible (Améliorer l'environnement/Standardiser les opérations) |
Remarque : Ce tableau est conceptuel et ne représente pas des données statistiques précises.
Conclusion:
Les API Omron sont des composants fondamentaux pour une automatisation industrielle efficace et fiable. Face à des défauts potentiels, il est primordial d'adopter une méthodologie de diagnostic systématique et factuelle.
Des vérifications fondamentales des alimentations et du câblage des E/S à l'analyse complexe de la logique du programme et des réseaux de communication, chaque étape exige une attention méticuleuse et de la patience.
Comprendre les symptômes typiques et les causes profondes de divers défauts, maîtriser le logiciel de programmation et les utilitaires de diagnostic d'Omron et appliquer les stratégies décrites dans ce guide, ainsi que la perspective des données, permettra aux ingénieurs et aux techniciens d'améliorer considérablement l'efficacité du dépannage.
Il est essentiel d’établir des pratiques de maintenance préventive robustes, telles que des inspections régulières, des nettoyages, des sauvegardes de programmes et la surveillance de l’environnement d’exploitation, pour minimiser de manière proactive les occurrences de pannes.
Cette approche garantit des performances et une longévité maximales des systèmes PLC Omron, préservant ainsi la stabilité de la production et permettant en fin de compte une réduction des coûts et des améliorations de l'efficacité.
Pour les problèmes particulièrement complexes ou persistants, il est toujours recommandé de consulter la documentation officielle d'Omron ou de contacter le support technique d'Omron.
Alimentez vos projets avec des PLC Omron, Mitsubishi, Schneider flambant neufs et originaux – en stock, prêts maintenant !
Contactez-nous
Remplissez simplement votre nom, votre adresse e-mail et une brève description de votre demande dans ce formulaire. Nous vous contacterons dans les 24 heures.
Catégorie de produit
Produits en vente à chaud
Ces sujets pourraient également vous intéresser
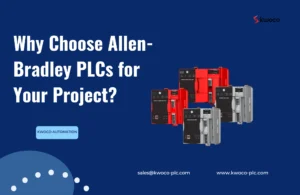
Pourquoi choisir les automates Allen-Bradley pour votre projet ?
Pourquoi choisir les automates Allen-Bradley pour votre projet ? Vous avez du mal à sélectionner l'automate le mieux adapté à vos projets d'ingénierie ? Vous n'êtes pas seul.
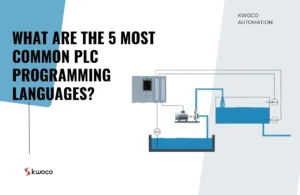
Quels sont les 5 langages de programmation PLC les plus courants ?
Quels sont les 5 langages de programmation PLC les plus courants ? La résolution de problèmes dans l'automatisation industrielle dépend souvent d'un facteur clé :
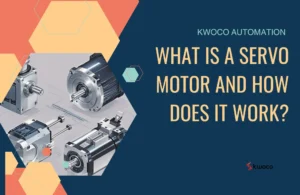
Qu'est-ce qu'un servomoteur et comment fonctionne-t-il ?
Qu'est-ce qu'un servomoteur et comment fonctionne-t-il ? Lorsqu'il s'agit de précision et de contrôle dans l'automatisation industrielle,