Comment résoudre les problèmes de communication PLC
- kwoco-plc.com
- 25 juin 2024
- 03h24
Les automates programmables industriels (PLC) constituent l'épine dorsale de l'automatisation industrielle moderne. Il s'agit d'ordinateurs spécialisés conçus pour gérer et contrôler les processus de fabrication, les machines et autres équipements industriels.
Des chaînes de montage aux opérations de machines complexes, les PLC garantissent que tout fonctionne correctement, efficacement et en toute sécurité.
Imaginez le chaos qui pourrait survenir si vos processus industriels s'arrêtaient soudainement ou fonctionnaient mal. Une communication fiable entre les automates et les autres composants est essentielle pour éviter de tels scénarios.
Table des matières
Une communication PLC efficace garantit que toutes les parties de votre système automatisé sont synchronisées, que les données sont transmises avec précision et que les opérations se déroulent sans problème.
Lorsque des problèmes de communication surviennent, ils peuvent perturber la production, entraînant des temps d’arrêt, une augmentation des coûts et des risques potentiels pour la sécurité.
Introduction
Le but de cet article est de vous guider dans la résolution des problèmes courants de communication PLC.
Que vous soyez confronté à des problèmes de connectivité, de perte de données ou de synchronisation, nous visons à fournir des solutions pratiques pour vous aider à maintenir des opérations industrielles transparentes.
Comment communiquez-vous avec PLC ?
Communication efficace avec les automates programmables industriels (Automates programmables) peut être réalisée par des méthodes directes et à distance, chacune adaptée à des besoins et des configurations spécifiques.
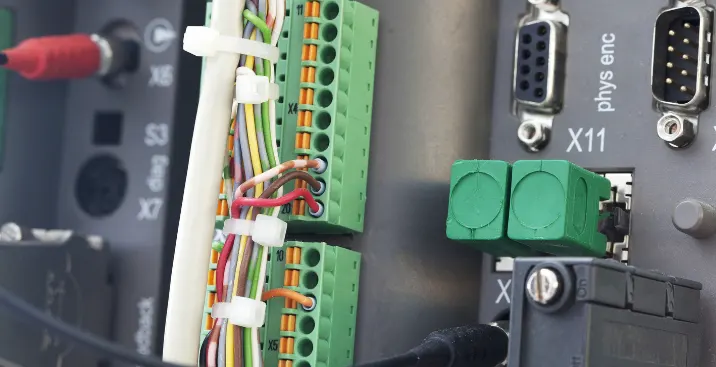
Communication directe
Écrans d'interface homme-machine (IHM) : L’un des moyens les plus conviviaux d’interagir avec les PLC est via IHM écrans. Ces interfaces fournissent une visualisation des données en temps réel, des options de contrôle et des informations de diagnostic, ce qui permet aux opérateurs de surveiller et de gérer directement les processus.
Interfaces du logiciel de programmation : Les automates programmables sont souvent programmés et configurés à l'aide d'interfaces logicielles spécialisées. Ces outils, tels que TIA Portal de Siemens, GX Works de Mitsubishi et RSLogix 5000 d'Allen Bradley, permettent aux ingénieurs d'écrire, de tester et de télécharger la logique de contrôle directement sur l'automate, garantissant ainsi un contrôle précis des processus industriels.
Communication à distance
Commutateurs et câbles réseau Ethernet : Pour la communication à distance, les automates programmables sont généralement connectés via des commutateurs et des câbles Ethernet réseau. Cette configuration permet aux automates d'échanger des données avec d'autres appareils et systèmes via un réseau local (LAN), facilitant ainsi l'intégration et la coordination transparentes de l'ensemble du système d'automatisation.
Méthodes de communication sans fil : Dans les situations où le câblage n'est pas pratique, les méthodes de communication sans fil entrent en jeu. Des technologies telles que le Wi-Fi et les normes sans fil industrielles offrent flexibilité et mobilité, permettant aux automates programmables de communiquer sur un réseau sans fil sans les contraintes du câblage physique.
Solutions courantes aux problèmes de communication PLC
La résolution des problèmes de communication dans les systèmes PLC est essentielle pour assurer le bon fonctionnement des opérations d'automatisation industrielle. Vous trouverez ci-dessous les étapes essentielles et les meilleures pratiques pour résoudre efficacement ces problèmes.
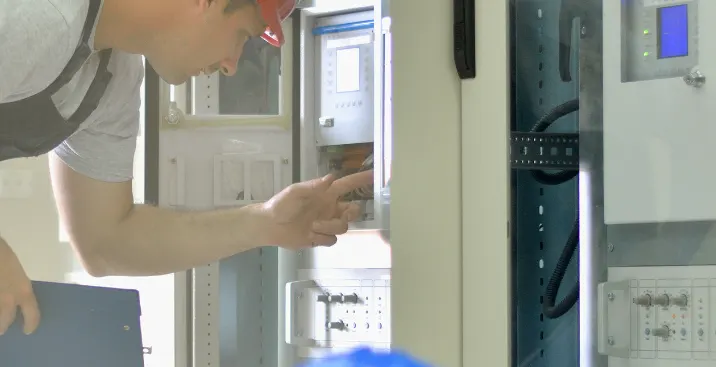
Inspectez les câbles Ethernet et les commutateurs Ethernet réseau : Commencez par examiner minutieusement toutes les connexions physiques. Inspectez les câbles Ethernet pour détecter tout signe d'usure, d'effilochage ou de dommage susceptible de nuire à la transmission des données. De même, vérifiez les commutateurs Ethernet du réseau pour vous assurer qu'ils fonctionnent correctement et que tous les ports sont opérationnels. Une gestion appropriée des câbles et l'utilisation de câbles blindés de haute qualité peuvent réduire considérablement les erreurs de communication.
Assurez-vous que les connexions sont correctes et vérifiez qu'il n'y a pas de dommage : Vérifiez que toutes les connexions sont sécurisées et correctement placées. Des câbles mal connectés ou mal branchés peuvent provoquer des pannes de communication intermittentes. Vérifiez régulièrement que les connecteurs et les ports ne présentent aucun dommage physique ou corrosion susceptible de compromettre l'intégrité de la liaison de communication.
Code PLC correct et paramètres de configuration : La configuration logicielle joue un rôle crucial dans la communication PLC. Assurez-vous que le code PLC est exempt d'erreurs et que les paramètres de configuration sont correctement appliqués. Cela comprend la vérification des adresses IP, des masques de sous-réseau, des passerelles et d'autres paramètres réseau. Des paramètres incorrects peuvent entraîner des pannes de communication et des dysfonctionnements du système.
Assurer la compatibilité entre les produits PLC et les protocoles de communication : Problèmes de compatibilité entre différents produits PLC (tels que les contrôleurs PLC Siemens, Automates programmables Mitsubishi, et Allen Bradley) et les protocoles de communication peuvent également causer des problèmes. Assurez-vous que tous les périphériques du réseau sont configurés pour utiliser des protocoles compatibles et qu'ils peuvent communiquer efficacement. La mise à jour du micrologiciel et du logiciel vers les dernières versions peut aider à résoudre de nombreux problèmes de compatibilité.
Trafic et interférences sur le réseau:Un trafic réseau élevé ou des interférences peuvent perturber les communications PLC. Utilisez des analyseurs de réseau pour vérifier le trafic excessif ou le bruit sur le réseau. La mise en œuvre d'une segmentation du réseau et d'un blindage approprié peut aider à atténuer ces problèmes.
Facteurs environnementaux :Les facteurs environnementaux tels que les températures extrêmes, l'humidité ou les interférences électromagnétiques peuvent affecter la communication PLC. Assurez-vous que votre PLC et votre équipement réseau fonctionnent dans les conditions environnementales recommandées.
Entretien régulier
Vérifications de routine et mises à jour des équipements d'automatisation : Un entretien régulier est essentiel pour éviter les problèmes de communication. Effectuez des contrôles de routine sur tous les équipements d'automatisation, y compris les automates programmables, les commutateurs réseau et les câbles. Recherchez des signes d'usure ou des problèmes potentiels qui pourraient dégénérer en problèmes importants s'ils ne sont pas résolus.
Mesures préventives pour éviter les pannes d'automatisation industrielle des PLC : Mettez en œuvre des mesures de maintenance préventive pour éviter de futures pannes de communication. Cela comprend des inspections programmées, le nettoyage de l'équipement et le remplacement en temps voulu des composants usés. La tenue d'un journal des activités de maintenance et le respect d'un calendrier de maintenance strict peuvent aider à détecter et à résoudre rapidement les problèmes potentiels.
En abordant systématiquement ces problèmes de communication courants, vous pouvez améliorer la fiabilité et l’efficacité de vos systèmes PLC, garantissant ainsi une automatisation industrielle ininterrompue et des performances optimales.
Conseils de dépannage avancés
Pour les problèmes de communication PLC plus complexes, des techniques de dépannage avancées peuvent être utilisées pour identifier et résoudre les problèmes efficacement.
Utiliser les outils de diagnostic
Outils logiciels pour diagnostiquer les problèmes de communication PLC : L'utilisation d'un logiciel de diagnostic spécialisé peut considérablement aider à identifier et à résoudre les problèmes de communication. Ces outils fournissent des informations détaillées sur les performances du réseau, les journaux de communication et les messages d'erreur, vous aidant ainsi à identifier la cause exacte du problème. Bon nombre de ces outils de diagnostic sont conçus pour être compatibles avec différentes marques d'automates programmables, notamment Siemens, Mitsubishi et Allen Bradley.
Outils compatibles avec les contrôleurs PLC Siemens et d'autres marques : Assurez-vous que les outils de diagnostic que vous utilisez sont compatibles avec les contrôleurs PLC spécifiques de votre configuration. Par exemple, Siemens propose une gamme de logiciels de diagnostic qui s'intègrent parfaitement à ses systèmes PLC, fournissant des données en temps réel et des rapports d'erreur complets. De même, d'autres marques ont leurs solutions de diagnostic adaptées à leurs produits, facilitant ainsi un dépannage efficace.
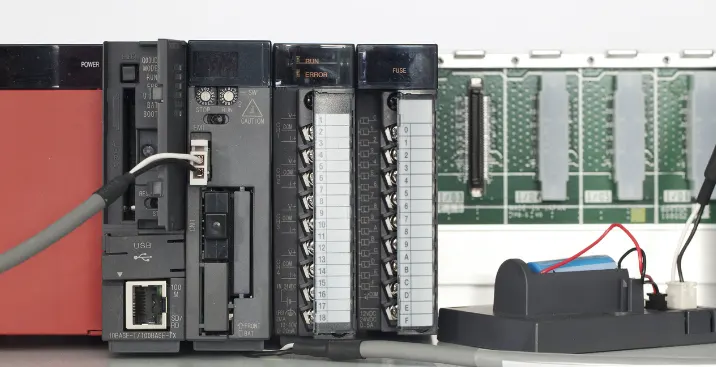
Consulter les directives du fabricant
Consultez les manuels et l'assistance de marques telles que Omron, Mitsubishi et Schneider : Les directives et manuels des fabricants sont des ressources précieuses pour résoudre les problèmes de communication PLC. Ils contiennent des instructions détaillées, des étapes de dépannage et des spécifications techniques qui peuvent vous guider tout au long du processus. Des marques comme Omron, Mitsubishi et Schneider fournir une documentation complète et des services d'assistance, y compris des ressources en ligne et des équipes d'assistance technique, pour aider à résoudre les problèmes complexes.
Analyse de réseau
Surveillance et analyse du trafic réseau à l'aide d'outils pour les connexions par câble Ethernet : Les outils d'analyse réseau sont essentiels pour surveiller et diagnostiquer les problèmes au sein du réseau de communication. Ces outils vous permettent de capturer et d'analyser le trafic réseau, d'identifier les goulots d'étranglement et de détecter les anomalies susceptibles d'affecter la communication. En utilisant des analyseurs de réseau, vous pouvez acquérir une compréhension plus approfondie du flux de données et identifier les interruptions ou les inefficacités dans les connexions par câble Ethernet.
En tirant parti de ces conseils de dépannage avancés, vous pouvez résoudre les problèmes de communication PLC les plus complexes, garantissant ainsi des systèmes d'automatisation industrielle robustes et fiables. L'utilisation régulière d'outils de diagnostic, le respect des directives du fabricant et une analyse approfondie du réseau contribueront à maintenir des performances optimales et à prévenir les problèmes futurs.
Quels sont les 4 protocoles de communication PLC ?
Il est essentiel de comprendre les différents protocoles de communication des automates programmables pour garantir une intégration et un fonctionnement sans faille au sein des systèmes d'automatisation industrielle. Voici quatre protocoles largement utilisés :
Ethernet/IP
Description et utilisation dans l'automatisation industrielle : Ethernet/IP (Ethernet Industrial Protocol) est un protocole robuste et polyvalent largement adopté dans l'automatisation industrielle. Il exploite la technologie Ethernet standard pour faciliter le contrôle en temps réel et l'échange d'informations entre différents appareils et systèmes.
Compatibilité avec divers produits PLC : Ethernet/IP est compatible avec une large gamme de produits PLC, ce qui en fait un choix privilégié pour les fabricants et les intégrateurs. Il prend en charge une communication transparente entre les PLC, les IHM et d'autres équipements d'automatisation, garantissant un transfert de données efficace et fiable.
Modbus
Aperçu et avantages : Modbus est un protocole de communication simple mais puissant qui permet à plusieurs appareils de communiquer sur un réseau. Sa simplicité d'utilisation et sa flexibilité en font un choix populaire dans de nombreuses applications industrielles.
Couramment utilisé avec les contrôleurs PLC Schneider et Siemens : Modbus est couramment utilisé avec les contrôleurs PLC Schneider et Siemens. Son adoption généralisée et sa mise en œuvre simple le rendent idéal pour divers scénarios d'automatisation, des systèmes de base aux systèmes complexes.
Profibus
Principales caractéristiques et avantages : Profibus (Process Field Bus) est un protocole de communication anti-interférences principalement utilisé dans les systèmes de contrôle industriels automatisés. Il s'agit d'un système de bus de terrain industriel qui réalise une transmission de données en temps réel avec une vitesse de communication de données de 12 Mo/s. Le protocole Profibus est couramment utilisé pour la communication entre divers appareils de contrôle industriel et pour la communication avec des capteurs, des actionneurs ou d'autres appareils de terrain.
Intégration avec les automates Siemens et autres contrôles d'automatisation : Profibus et Profinet s'intègrent parfaitement aux automates Siemens et autres commandes d'automatisation. Leur capacité à prendre en charge les communications à haut débit et les systèmes d'automatisation à grande échelle les rend indispensables dans les configurations industrielles complexes.
DeviceNet
Applications et cas d'utilisation : DeviceNet est un protocole robuste conçu pour la communication au niveau des appareils industriels. Il permet à différents appareils de communiquer sur un réseau commun, simplifiant ainsi les processus de contrôle et d'acquisition de données.
Marques prises en charge telles que Allen Bradleys et Mitsubishi PLC : DeviceNet est pris en charge par les principales marques d'automates programmables, telles qu'Allen Bradley et Mitsubishi. Ses performances fiables et sa large prise en charge en font un choix polyvalent pour de nombreuses applications industrielles, du simple contrôle d'appareils aux systèmes d'automatisation complets.
En comprenant ces quatre protocoles de communication PLC, vous pouvez mieux sélectionner et mettre en œuvre les solutions appropriées à vos besoins d'automatisation industrielle, garantissant des performances système efficaces et fiables.
Conclusion
La résolution des problèmes de communication des automates programmables est essentielle pour maintenir des systèmes d'automatisation industrielle efficaces et fiables. En vérifiant les connexions physiques, en vérifiant les configurations logicielles et en effectuant une maintenance régulière, vous pouvez prévenir et résoudre les problèmes de communication courants.
Les techniques de dépannage avancées, telles que l’utilisation d’outils de diagnostic, la consultation des directives du fabricant et la réalisation d’une analyse du réseau, améliorent encore votre capacité à maintenir des performances système optimales.
De plus, la compréhension des principaux protocoles de communication PLC tels qu'Ethernet/IP, Modbus, Profibus/Profinet et DeviceNet garantit une intégration et un fonctionnement transparents dans diverses configurations industrielles.
Si vous êtes confronté à des défis de communication PLC ou cherchez à optimiser vos systèmes d'automatisation, n'hésitez pas à nous contacter.
Notre équipe d'experts est prête à vous fournir des solutions automatisées professionnelles adaptées à vos besoins. Découvrez notre gamme de pièces d'automatisation originales de haute qualité de grandes marques telles que Siemens, Mitsubishi et Allen Bradley pour garantir les meilleures performances pour vos applications industrielles.