Guía de resolución de problemas de PLC: consejos y trucos esenciales
Tabla de contenido
Entendiendo los PLC: ¿Qué es un controlador lógico programable?
Un controlador lógico programable es una computadora robusta que se utiliza para la automatización de procesos industriales, como el control de maquinaria en líneas de ensamblaje de fábricas. Los PLC están diseñados para soportar entornos industriales hostiles y pueden realizar tareas complejas con alta confiabilidad.
Componentes de un PLC:
- CPU (Unidad central de procesamiento): El cerebro del PLC que procesa datos.
- Módulos de entrada y salida: Interfaces que permiten al PLC recibir información (entrada) y enviar comandos (salida) a la maquinaria.
- Fuente de alimentación: Proporciona el voltaje necesario para que el PLC funcione.
- Dispositivo de programación: Se utiliza para crear y cargar el programa PLC.
Comprender estos componentes es fundamental porque pueden surgir problemas en cualquier parte del sistema PLC. Si se familiariza con el funcionamiento de un controlador lógico programable, estará mejor preparado para solucionar los problemas cuando surjan.
¿Por qué fallan los PLC? Causas comunes de mal funcionamiento de los PLC
Incluso los PLC más fiables pueden experimentar averías. Identificar la causa raíz es el primer paso en el proceso de resolución de problemas.
Causas comunes de fallas del PLC:
- Problemas con la fuente de alimentación:
- Las fluctuaciones de voltaje pueden interrumpir el funcionamiento del PLC.
- Un módulo de fuente de alimentación defectuoso puede provocar que todo el sistema falle.
- Cableado y conexiones defectuosos:
- El cableado suelto o dañado puede provocar problemas intermitentes.
- Las conexiones de cables pueden desconectarse o corroerse con el tiempo.
- Fallos del módulo:
- Los módulos de entrada o salida defectuosos pueden afectar partes específicas del sistema.
- Los fallos del procesador o de la CPU pueden detener el PLC por completo.
- Factores ambientales:
- La interferencia electromagnética y la interferencia de radiofrecuencia pueden alterar las señales.
- Las temperaturas extremas o la humedad pueden dañar los componentes.
- Problemas de software:
- Los errores en el programa PLC pueden provocar un comportamiento inesperado.
- Es posible que sea necesario actualizar el firmware para corregir errores.
Al comprender estos problemas comunes, puede diagnosticar rápidamente dónde está el problema y tomar las medidas adecuadas.
Cómo solucionar problemas en sistemas PLC: guía paso a paso
Cuando se enfrenta un problema con el PLC, un enfoque sistemático para la resolución de problemas puede ahorrar tiempo y recursos.
Paso 1: La seguridad es lo primero
- Desconecte la alimentación antes de inspeccionar el hardware.
- Asegúrese de que la maquinaria esté en un estado seguro para evitar accidentes.
Paso 2: Verifique los conceptos básicos
- Verifique que la fuente de alimentación esté funcionando y suministre el voltaje correcto.
- Inspeccione el cableado para detectar conexiones sueltas o daños visibles.
- Confirme que todos los módulos estén colocados correctamente en sus ranuras.
Paso 3: Examinar los indicadores
- Observe los LED en los módulos PLC y la CPU:
- Los indicadores de energía confirman que el PLC está recibiendo electricidad.
- Los indicadores de falla pueden señalar componentes defectuosos específicos.
Paso 4: Analizar la CPU y el procesador
- La CPU es el cerebro del PLC. Si no funciona correctamente, puede afectar a todo el sistema.
- Verifique si hay códigos de error o luces de falla en el módulo del procesador.
Paso 5: Probar entradas y salidas
- Utilice herramientas de diagnóstico para comprobar las señales de entrada y las respuestas de salida.
- Asegúrese de que los sensores y actuadores conectados al PLC estén operativos.
Paso 6: Revisar el programa del PLC
- Conéctese al PLC mediante su dispositivo de programación.
- Busque errores lógicos o anomalías en el programa del PLC.
Paso 7: Busque interferencias
- Identificar fuentes de interferencia electromagnética o interferencia de radiofrecuencia.
- Reubicar o proteger los cables para minimizar la interferencia.
Si sigue estos pasos, podrá solucionar sistemáticamente los problemas del PLC y aislar la causa del problema.
Consejos para el mantenimiento de sus sistemas de control PLC
El mantenimiento regular puede prevenir muchas fallas comunes del PLC y extender la vida útil de su sistema de control.
Inspección regular
- Revise periódicamente todo el cableado y las conexiones de cables.
- Inspeccione los módulos para detectar signos de desgaste o daños.
Control ambiental
- Mantenga el PLC en un entorno limpio y con temperatura controlada.
- Utilice recintos para protegerse contra el polvo, la humedad y otros contaminantes.
Actualizar software y firmware
- Mantenga el programa del PLC y el firmware actualizados.
- Utilice actualizaciones oficiales de fabricantes como PLC de Schneider para garantizar la compatibilidad y la seguridad.
Formación y documentación
- Asegúrese de que el personal esté capacitado en el funcionamiento y la resolución de problemas del PLC.
- Mantener esquemas y manuales actualizados para referencia.
Protección contra sobretensiones
- Instale protectores contra sobretensiones para protegerse contra picos de tensión.
- Pruebe periódicamente el suministro de energía y los sistemas de respaldo.
El papel de los PLC en la automatización industrial
Los PLC son parte integral de la automatización industrial moderna y controlan todo, desde máquinas simples hasta procesos de fabricación complejos.
¿Por qué son esenciales los PLC?
- Flexibilidad: Fácilmente reprogramable para diferentes tareas.
- Fiabilidad: Diseñado para funcionar en entornos hostiles.
- Escalabilidad: Se puede ampliar con módulos adicionales según sea necesario.
Aplicaciones de los PLC:
- Líneas de Fabricación: Controlan operaciones de ensamblaje y dispositivos robóticos.
- Control de procesos: gestionar variables como temperatura, presión y flujo.
- Gestión Energética: Optimizar el consumo e integrar fuentes renovables.
Preguntas frecuentes
Si la CPU muestra indicadores de falla, no se comunica o no responde después de reiniciarla, es posible que sea necesario reemplazarla. Siempre consulte las pautas del fabricante antes de continuar.
Sí, la interferencia electromagnética puede alterar las señales dentro del PLC, lo que provoca fallas de funcionamiento. El blindaje de los cables y la reubicación de las fuentes de interferencia pueden mitigar este problema.
Utilice el software de programación oficial del fabricante de su PLC. Por ejemplo, PLC de Mitsubishi ofrece herramientas diseñadas específicamente para sus controladores.
Se debe realizar un mantenimiento regular al menos una vez al año, pero los sistemas críticos pueden requerir controles más frecuentes. Las inspecciones periódicas ayudan a minimizar el tiempo de inactividad y a prevenir fallas inesperadas.
Por supuesto. Mantener una copia de seguridad del programa del PLC garantiza que se puedan restaurar rápidamente las operaciones después de una falla o al reemplazar el hardware.
Potencie sus proyectos con PLC Omron, Mitsubishi y Schneider nuevos y originales: ¡en stock y listos ahora!
Conclusión
- Los PLC son componentes críticos en la automatización industrial y actúan como el cerebro de los sistemas de control.
- Las causas comunes de fallas del PLC incluyen problemas de suministro de energía, cableado defectuoso, fallas del módulo, factores ambientales y errores de software.
- Un proceso sistemático de resolución de problemas ayuda a identificar y resolver problemas de manera eficiente.
- El mantenimiento y las actualizaciones regulares prolongan la vida útil de su sistema PLC y mejoran la confiabilidad.
- Comprender y abordar las interferencias puede prevenir fallos de funcionamiento y mejorar el rendimiento.
- El uso de recursos de fabricantes acreditados mejora el soporte y la compatibilidad.
¿Buscas PLC nuevos y originales para tus proyectos? En Kwoco, tenemos en stock los PLC más recientes de las mejores marcas como Omrón, Mitsubishi, y SchneiderCompre con confianza: envío rápido, calidad garantizada. ¡Compre ahora!
Contáctenos
Simplemente complete su nombre, dirección de correo electrónico y una breve descripción de su consulta en este formulario. Nos comunicaremos con usted dentro de las 24 horas.
Categoría de producto
Productos en oferta
También te pueden interesar estos temas
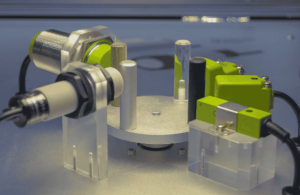
Sensores de proximidad inductivos de 3 cables: guía completa
¿Quiere comprender cómo funcionan los sensores de proximidad inductivos de 3 cables en la automatización industrial? Estos dispositivos de detección esenciales han revolucionado los procesos de fabricación modernos al proporcionar una detección confiable y sin contacto de objetos metálicos.
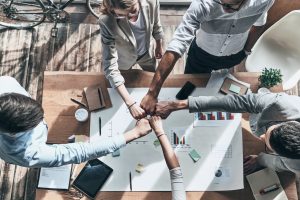
Casos de éxito de la alianza global de Kwoco
Historias de éxito de asociación global de Kwoco ¿Alguna vez se enfrentó al desafío de encontrar un proveedor confiable de productos de control industrial para una
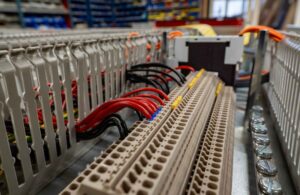
Todo lo que necesita saber sobre las fuentes de alimentación de los PLC
Las fuentes de alimentación son los héroes anónimos de los controladores lógicos programables (PLC), ya que garantizan un funcionamiento sin problemas al convertir la electricidad entrante en la forma y el voltaje que requieren los PLC. Desde la alimentación de la CPU hasta el soporte de los dispositivos de campo, las fuentes de alimentación de los PLC son cruciales para el rendimiento de un sistema.