Introducción a los controladores lógicos programables: su puerta de entrada a la automatización industrial
Tabla de contenido
1. ¿Qué es un PLC (controlador lógico programable)?
Un controlador lógico programable (PLC) es una computadora industrial especializada diseñada para automatizar procesos industriales. El primer PLC se desarrolló para reemplazar los sistemas lógicos de relé cableados, ofreciendo una solución más flexible y eficiente.
Considero que los PLC son el cerebro detrás de muchos sistemas automatizados en fábricas y plantas. Reciben información de varios dispositivos, como sensores e interruptores, procesan la información según un programa de PLC y generan salidas para controlar maquinaria y equipo.
Los PLC son ampliamente utilizados en la automatización industrial debido a su robustez, confiabilidad y capacidad para soportar entornos industriales hostiles. Están diseñados para controlar y monitorear procesos con alta precisión, mejorando la eficiencia y reduciendo el error humano.
Como experto en automatización industrial, he visto cómo los PLC han revolucionado la fabricación, permitiendo que operaciones complejas se ejecuten sin problemas. El controlador digital modular está equipado con una memoria programable para almacenar instrucciones y realizar funciones para controlar máquinas y procesos.
2. ¿Cómo funciona un PLC?
Un PLC opera en un ciclo continuo, escaneando su programa y actualizando las salidas en función de las entradas actuales. Este proceso implica leer el estado de entrada, ejecutar la lógica de control escrita en el lenguaje de programación y luego actualizar el estado de salida en consecuencia. El PLC toma señales de los dispositivos de entrada y toma decisiones en función de la lógica programada.
El trabajo del PLC gira en torno al procesamiento de información y la toma de decisiones en tiempo real. Por ejemplo, si un sensor detecta un producto en una cinta transportadora, el PLC puede activar un actuador para mover el producto a la siguiente etapa.
Considero que la capacidad de los PLC para procesar información de forma rápida y precisa es lo que los hace tan valiosos en la automatización industrial. La CPU (unidad central de procesamiento) es el componente central que ejecuta el programa y toma estas decisiones.
3. ¿Cuáles son los componentes básicos de un PLC?
Los componentes básicos de un PLC incluyen la CPU (unidad central de procesamiento), módulos de entrada y salida, fuentes de alimentación y un dispositivo de programación. La CPU es el cerebro del PLC, ejecuta el programa y procesa los datos. Los módulos de entrada reciben señales de dispositivos externos, mientras que los módulos de salida envían señales de control a la maquinaria.
Componente | Descripción |
---|---|
UPC | Ejecuta el programa y procesa los datos. |
Módulo de entrada | Recibe señales de dispositivos externos. |
Módulo de salida | Envía señales de control a la maquinaria. |
Fuentes de alimentación | Proporciona energía a los componentes del PLC. |
Dispositivo de programación | Se utiliza para crear y modificar programas de PLC. |
En mi experiencia, comprender estos componentes es fundamental para cualquiera que trabaje con PLC. Por ejemplo, el módulo de entrada puede ser digital o analógico, según el tipo de señal que reciba. De manera similar, los módulos de salida pueden controlar varios dispositivos, como motores, válvulas y luces.
4. ¿Cuáles son los diferentes tipos de PLC?
Existen principalmente dos tipos de PLC: compactos y modulares. Los PLC compactos son unidades todo en uno con entradas y salidas integradas, adecuadas para aplicaciones a pequeña escala. Los PLC modulares, por otro lado, constan de módulos separados que se pueden configurar y ampliar según sea necesario.
Los PLC modulares ofrecen una mayor flexibilidad, lo que permite a los usuarios personalizar el sistema en función de sus requisitos específicos. A menudo recomiendo PLC modulares para sistemas complejos en los que la escalabilidad es importante. Por ejemplo, un PLC modular puede incluir módulos separados para entradas digitales, entradas analógicas, salidas digitales y salidas analógicas, cada uno adaptado a diferentes tipos de sensores y actuadores.
5. ¿Cómo se realiza la programación del PLC?
La programación de un PLC implica la creación de un conjunto de instrucciones que le indican al PLC cómo debe funcionar. Esto se hace normalmente mediante un software de programación especializado proporcionado por el fabricante del PLC; el PLC toma estas instrucciones y las ejecuta de forma secuencial. La programación de un PLC requiere comprender el proceso que se va a automatizar y la lógica de control deseada.
El lenguaje de programación de los PLC puede variar, pero el más común es la lógica de escalera, un lenguaje gráfico que se asemeja a los diagramas de lógica de relés. Otros lenguajes de programación de PLC incluyen el diagrama de bloques de funciones (FBD), el texto estructurado (ST) y el diagrama de funciones secuenciales (SFC). En mi trabajo, he descubierto que la lógica de escalera suele ser la preferida por su simplicidad y facilidad de comprensión, especialmente para los técnicos familiarizados con la lógica de relés.
6. ¿Cuáles son los lenguajes de programación de PLC comunes?
Los lenguajes de programación de PLC ofrecen distintas formas de crear programas de control. La lógica en escalera es el lenguaje de programación de PLC más utilizado, conocido por su representación visual de la lógica de relés. El diagrama de bloques de funciones (FBD) es otro lenguaje gráfico que utiliza bloques para representar funciones y sus interconexiones.
El texto estructurado (ST) es un lenguaje de alto nivel similar a Pascal, que ofrece capacidades de programación más avanzadas. El diagrama de funciones secuenciales (SFC) se utiliza para procesos complejos que implican múltiples pasos y transiciones. He utilizado todos estos lenguajes en varios proyectos y aprecio la flexibilidad que ofrecen. Por ejemplo, el texto estructurado es excelente para cálculos complejos, mientras que la lógica en escalera es ideal para un control de encendido y apagado simple.
- Lógica de escalera: se asemeja a los diagramas lógicos de relés eléctricos, lo que lo hace intuitivo para aquellos familiarizados con los sistemas eléctricos.
- Diagrama de bloques de funciones (FBD): utiliza bloques gráficos para representar funciones, adecuado para lógica compleja.
- Texto Estructurado (ST): Un lenguaje de alto nivel similar a Pascal, utilizado para tareas de programación avanzadas.
- Diagrama de funciones secuenciales (SFC): ideal para procesos con múltiples pasos y transiciones.
7. ¿Qué es la lógica de escalera y cómo se utiliza en la programación de PLC?
La lógica de escalera es un lenguaje de programación gráfico que representa la lógica de control de una manera similar a los diagramas lógicos de relés eléctricos. Utiliza contactos y bobinas para representar entradas y salidas, respectivamente. La lógica de escalera se utiliza ampliamente porque es fácil de entender y visualizar.
En la lógica de escalera, un escalón representa una única instrucción de control, con contactos a la izquierda (entradas) y bobinas a la derecha (salidas). El PLC ejecuta cada escalón de forma secuencial, actualizando las salidas en función del estado de las entradas. A menudo utilizo la lógica de escalera para tareas de control sencillas, como arrancar y detener motores o controlar luces. Por ejemplo, un escalón simple podría comprobar si se ha pulsado un botón de arranque (entrada) y, a continuación, activar un motor (salida).
A continuación se muestra un ejemplo sencillo de un peldaño de lógica de escalera:
Botón de inicio (entrada) –| |– Motor (salida)
8. ¿Cómo interactúan los PLC con otros dispositivos y sistemas?
Los PLC pueden interactuar con una amplia gama de dispositivos y sistemas mediante varios protocolos de comunicación. Los módulos de entrada y salida permiten que los PLC se conecten a sensores, actuadores y otros dispositivos de campo. Los PLC también pueden comunicarse con otros PLC, HMI (interfaces hombre-máquina) y sistemas SCADA (control de supervisión y adquisición de datos).
Por ejemplo, un PLC puede utilizar Modbus para comunicarse con un módulo de E/S remoto o EtherNet/IP para conectarse a un sistema SCADA. He trabajado en proyectos en los que se integraron PLC en redes industriales más grandes de Internet de las cosas (IIoT), lo que permitió el control y la supervisión remotos. Las capacidades de interfaz de los PLC son cruciales para construir sistemas de automatización inteligentes e interconectados.
9. ¿Cuáles son las aplicaciones de los PLC en la automatización industrial?
Las aplicaciones de los PLC son amplias y variadas, y abarcan diferentes industrias y procesos. Los PLC se utilizan para automatizar todo, desde máquinas sencillas hasta líneas de producción complejas. Algunas aplicaciones comunes de los PLC incluyen el control de sistemas de transporte, la gestión de sistemas de calefacción, ventilación y aire acondicionado (HVAC), el funcionamiento de máquinas de envasado y la supervisión de procesos industriales.
En mi experiencia, los PLC son particularmente útiles en aplicaciones que requieren alta confiabilidad y precisión. Por ejemplo, en una planta de procesamiento de alimentos, un PLC puede controlar la temperatura, la presión y el caudal de los ingredientes para garantizar una calidad constante del producto. Los PLC también se pueden utilizar en aplicaciones críticas para la seguridad, como los sistemas de apagado de emergencia, donde su confiabilidad es primordial. Se utilizan para controlar una amplia variedad de máquinas y procesos, garantizando que funcionen de manera correcta y eficiente.
A continuación se muestran algunos ejemplos de aplicaciones de PLC:
- Sistemas transportadores
- Sistemas HVAC
- Maquinas de embalaje
- Brazos robóticos
- Plantas de tratamiento de agua
- Sistemas de parada de emergencia
10. ¿Cómo solucionar problemas en sistemas PLC?
La resolución de problemas de los sistemas PLC implica identificar y resolver los problemas que impiden que el sistema funcione correctamente. Los problemas más comunes incluyen entradas o salidas defectuosas, errores de programación y fallas de comunicación. Una resolución de problemas eficaz requiere un enfoque sistemático y un buen conocimiento del sistema PLC.
Siempre empiezo por comprobar los indicadores de diagnóstico y los registros de errores del PLC. La mayoría de los PLC tienen diagnósticos integrados que pueden proporcionar información valiosa sobre el estado del sistema. A continuación, verifico las entradas y salidas con un multímetro o un dispositivo de programación para asegurarme de que funcionan correctamente. Si el problema persiste, reviso el programa del PLC en busca de errores o inconsistencias.
A continuación se ofrecen algunos consejos para solucionar problemas en los sistemas PLC:
- Verifique los indicadores de diagnóstico y los registros de errores del PLC.
- Verifique las entradas y salidas utilizando un multímetro.
- Revise el programa PLC para detectar errores.
- Verifique si hay conexiones sueltas o cableado dañado.
- Asegúrese de que el suministro de energía sea estable.
- Pruebe los enlaces de comunicación con otros dispositivos.
Preguntas frecuentes
Si bien tanto los PLC como los microcontroladores se utilizan para aplicaciones de control, difieren en su diseño y uso previsto. Los PLC están diseñados para entornos industriales y ofrecen robustez, confiabilidad y facilidad de programación. Los microcontroladores, por otro lado, se utilizan normalmente en sistemas integrados y productos electrónicos de consumo. A menudo recomiendo los PLC para aplicaciones industriales debido a su durabilidad superior y sus características especializadas.
Sí, los PLC se pueden utilizar para la automatización del hogar, pero por lo general son excesivos para esas aplicaciones. Los sistemas de automatización del hogar suelen utilizar soluciones más simples y rentables, como concentradores domésticos inteligentes y microcontroladores. Sin embargo, para proyectos de automatización del hogar complejos o de gran escala, un PLC puede ser una opción viable.
La lógica de escalera ofrece varias ventajas, entre ellas su simplicidad, facilidad de comprensión y representación visual de la lógica de control. Es especialmente útil para los técnicos familiarizados con la lógica de relés eléctricos, lo que facilita la transición a la programación de PLC. Considero que la lógica de escalera es una excelente opción para tareas de control simples o moderadamente complejas.
La elección del PLC adecuado depende de varios factores, entre ellos la complejidad de la aplicación, la cantidad de entradas y salidas, la velocidad de procesamiento requerida y las necesidades de comunicación. Recomiendo comenzar por definir los requisitos específicos de su aplicación y luego seleccionar un PLC que satisfaga esas necesidades. Considere factores como la escalabilidad, la compatibilidad con lenguajes de programación y las condiciones ambientales.
Los sistemas SCADA (Supervisory Control and Data Acquisition) se utilizan para supervisar y controlar procesos industriales desde una ubicación central. A menudo funcionan en conjunto con los PLC, lo que proporciona una interfaz de nivel superior para operadores y gerentes. Los sistemas SCADA pueden recopilar datos de varios PLC, mostrar información del proceso en tiempo real y permitir que los operadores realicen ajustes o emitan comandos. Considero que SCADA es una herramienta esencial para administrar sistemas de automatización complejos, que proporciona información valiosa y capacidades de control.
Potencie sus proyectos con servomotores Omron, Mitsubishi y Schneider nuevos y originales: ¡disponibles en stock y listos ahora!
Conclusión
- Los PLC son componentes esenciales de los sistemas de automatización industrial modernos.
- Comprender los diferentes tipos de PLC y sus lenguajes de programación es crucial para una automatización eficaz.
- La lógica de escalera sigue siendo una opción popular para la programación de PLC debido a su simplicidad y facilidad de uso.
- Los PLC pueden interactuar con una amplia gama de dispositivos y sistemas, lo que permite soluciones de automatización complejas.
- La resolución de problemas de los sistemas PLC requiere un enfoque sistemático y una buena comprensión de los componentes y la programación del sistema.
- La elección del PLC adecuado depende de los requisitos específicos de la aplicación.
- Puede familiarizarse con el mundo de los controladores lógicos programables explorando PLC de Mitsubishi, PLC Schneider, y Interfaz hombre-máquina Mitsubishi para comprender sus capacidades y cómo pueden mejorar la automatización industrial.
- Para necesidades de automatización más avanzadas, la integración Servo delta y Inversor Schneider Puede proporcionar un control preciso y eficiencia energética en sus sistemas.
- Al comprender y utilizar estas tecnologías, puede mejorar significativamente la eficiencia y la productividad de sus procesos industriales.
Aprovechando mi experiencia en productos de control y automatización industrial, mi objetivo es brindar soluciones que satisfagan las necesidades de fábricas de maquinaria y equipos, fabricantes y empresas de soluciones de fábrica.
Mi objetivo es ayudarlo a lograr una automatización perfecta, mejorar la productividad e impulsar el éxito en sus operaciones. Comuníquese conmigo hoy para obtener más información sobre cómo podemos transformar sus procesos industriales con soluciones PLC avanzadas.
Contáctenos
Simplemente complete su nombre, dirección de correo electrónico y una breve descripción de su consulta en este formulario. Nos comunicaremos con usted dentro de las 24 horas.
Categoría de producto
Productos en oferta
También te pueden interesar estos temas
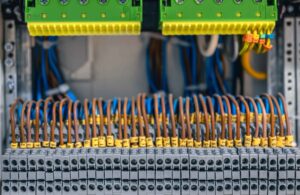
Solución de problemas comunes de los PLC: una guía para los controladores lógicos programables
Los controladores lógicos programables (PLC) son la columna vertebral de la automatización moderna y organizan el funcionamiento sin problemas de la maquinaria y los procesos industriales. Sin embargo, como cualquier tecnología, pueden encontrarse con problemas que interrumpan las operaciones.
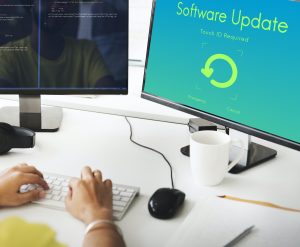
Cómo descargar y cargar programas para la serie Hitech (Beijer) HMI PWS6000: una guía completa
Cómo descargar y cargar programas para la serie Hitech (Beijer) HMI PWS6000: una guía completa La serie Hitech (Beijer) PWS6000
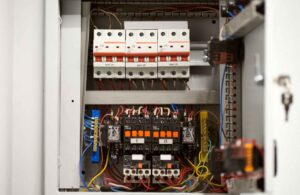
¿Qué es un panel de control eléctrico? Explicación de los conceptos clave
Un panel de control eléctrico es un componente crucial en la automatización industrial, ya que funciona como centro neurálgico para controlar y supervisar diversos dispositivos eléctricos. Este artículo profundiza en los conceptos básicos de los paneles de control eléctrico, sus componentes y su importancia para garantizar operaciones eficientes y seguras en entornos industriales.