Guía esencial sobre fallos de PLC y técnicas de resolución de problemas
En esta guía, cubriremos las causas comunes de SOCIEDAD ANÓNIMA fallas, identificar señales de advertencia y describir técnicas de solución de problemas para ayudarlo a abordar los problemas rápidamente y minimizar el tiempo de inactividad.
Tabla de contenido
Causas comunes de fallas del PLC
Los PLC pueden fallar por diversas razones, desde factores ambientales hasta errores del operador. Comprender estas causas es fundamental para prevenir fallas.
- Fallas eléctricas:Las subidas de tensión, las fluctuaciones de voltaje o las fallas eléctricas pueden dañar los componentes del PLC y provocar averías. El mantenimiento preventivo, que incluye protección contra subidas de tensión y monitoreo constante de la fuente de alimentación, es esencial.
- Estrés ambiental:La exposición a altas temperaturas, polvo, humedad y productos químicos corrosivos puede degradar el rendimiento del PLC con el tiempo. La limpieza regular y la protección adecuada pueden mitigar estos riesgos.
- Problemas de software:Los fallos de software, como errores de programación o incompatibilidades, pueden detener el funcionamiento del PLC. Mantener el software actualizado y cumplir con las mejores prácticas de programación puede evitar estos fallos.
- Deterioro de componentes:Al igual que con cualquier sistema mecánico, las piezas de un PLC, como los ventiladores y los conectores, pueden desgastarse con el uso. Las inspecciones periódicas y los reemplazos oportunos ayudan a prevenir fallas.
- Interferencia electromagnética (EMI):La interferencia de equipos cercanos puede alterar el funcionamiento del PLC. La implementación de protección y una conexión a tierra adecuada minimiza estos problemas.
- Error humano:Los errores accidentales en la introducción de datos o el manejo inadecuado pueden provocar averías. La formación adecuada y el acceso controlado reducen la probabilidad de que se produzcan estos errores.
Indicadores clave de mal funcionamiento del PLC
Detectar señales tempranas de problemas en el PLC le permitirá abordarlos antes de que se agraven.
- Entradas y salidas erráticas:Las señales de entrada y salida inestables son una señal de posibles problemas en el sistema PLC.
- Inestabilidad energética:Una fuente de alimentación defectuosa a menudo provoca apagados del sistema o fallas intermitentes.
- Ruido eléctrico:La interferencia eléctrica de fuentes externas puede alterar las lecturas y generar comportamientos inesperados en el PLC.
- Fallas de comunicación:Cuando un PLC pierde la conectividad de red o muestra errores de comunicación frecuentes, podría indicar una falla interna.
- Calentamiento excesivo:El calor excesivo dentro del sistema puede indicar problemas con los componentes internos, dañando potencialmente piezas sensibles.
- Corrupción de la memoria:La memoria dañada dentro de un PLC puede provocar fallas del sistema y un rendimiento poco confiable.
Pasos básicos para la resolución de problemas del PLC
Un enfoque sistemático puede resolver muchos problemas de PLC de manera efectiva.
- Comprobar la fuente de alimentación: Asegúrese de que la fuente de alimentación del PLC sea estable y funcione correctamente. Probar los niveles de voltaje e inspeccionar las conexiones eléctricas es un buen punto de partida.
- Verificar la integridad de la conexión a tierra:Una conexión a tierra incorrecta puede provocar ruido eléctrico. Garantizar una conexión a tierra adecuada eliminará las interferencias y mejorará el rendimiento del PLC.
- Inspeccionar dispositivos de entrada y salida: Defectuoso sensoresLos actuadores o las conexiones mal cableadas pueden provocar errores en el sistema. Verificar las conexiones de entrada y salida ayuda a aislar los componentes defectuosos.
- Examinar los indicadores de estado:Los PLC suelen tener LED o indicadores de diagnóstico. Revisar estos indicadores y consultar el manual del PLC puede revelar códigos de falla o advertencias específicas.
Técnicas avanzadas de resolución de problemas
Los métodos avanzados son útiles para problemas complejos o fallas recurrentes del PLC.
- Monitorizar el comportamiento del sistema:El uso de registros de tendencias y eventos ayuda a identificar patrones en el rendimiento del PLC. El seguimiento de los cambios de temperatura, las fluctuaciones de voltaje y el historial de alarmas puede revelar problemas subyacentes.
- Realizar auditorías del sistema:Auditar periódicamente el cableado del PLC, las conexiones de los componentes y las configuraciones de programación ayuda a detectar posibles fallas antes de que afecten las operaciones.
- Ajuste de PID:El ajuste de los controladores PID (proporcional-integral-derivativo) garantiza un control preciso de las variables del sistema. Un ajuste adecuado es crucial para la estabilidad en circuitos de control complejos.
- Depuración del programa:La resolución avanzada de problemas puede implicar recorrer paso a paso el código del PLC para detectar errores de software o problemas lógicos. Muchas marcas de PLC ofrecen herramientas de depuración dentro de su software.
Mantenimiento preventivo de sistemas PLC
El mantenimiento de rutina es vital para extender la vida útil y el rendimiento de los sistemas PLC.
- Control ambiental:Mantener el PLC en un entorno estable y limpio evita daños causados por el polvo, la humedad y las fluctuaciones de temperatura.
- Reemplazo de componentes:Reemplazar periódicamente los componentes antiguos, como ventiladores y conectores, reduce el riesgo de fallas relacionadas con el desgaste.
- Actualizaciones de software:Las actualizaciones de software constantes mejoran la funcionalidad y la seguridad, garantizando la compatibilidad con otros componentes industriales.
Aprovechamiento de recursos y apoyo
Utilice los recursos disponibles para ayudar con la resolución de problemas y las reparaciones.
- Documentación del proveedor:Los manuales y las especificaciones técnicas son referencias valiosas a la hora de diagnosticar y solucionar problemas del PLC.
- Foros y tutoriales en línea:Los recursos en línea, incluidos foros y tutoriales en vídeo, brindan consejos prácticos y apoyo comunitario de otros profesionales.
- Expertos en consultoría:Para problemas complejos, comunicarse con un técnico de PLC experimentado o un equipo de soporte puede agilizar la resolución de problemas y garantizar que las reparaciones sean efectivas.
Potencie sus proyectos con PLC Omron, Mitsubishi y Schneider nuevos y originales: ¡en stock y listos ahora!
Conclusión
El mantenimiento de un sistema PLC es esencial para que las operaciones industriales no se interrumpan. Si comprende los fallos más comunes, identifica las señales de advertencia tempranas y sigue los pasos sistemáticos de resolución de problemas, podrá minimizar el tiempo de inactividad y mantener la fiabilidad del sistema.
Incorpore mantenimiento preventivo y manténgase informado sobre las mejores prácticas de resolución de problemas para mantener sus procesos de automatización funcionando sin problemas.
¿Buscas PLC nuevos y originales para tus proyectos? En Kwoco, tenemos en stock los PLC más recientes de las mejores marcas como Omrón, Mitsubishi, y SchneiderCompre con confianza: envío rápido, calidad garantizada. ¡Compre ahora!
Contáctenos
Simplemente complete su nombre, dirección de correo electrónico y una breve descripción de su consulta en este formulario. Nos comunicaremos con usted dentro de las 24 horas.
Categoría de producto
Productos en oferta
También te pueden interesar estos temas
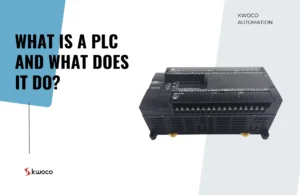
¿Qué es un PLC y qué hace?
¿Qué es un PLC y qué hace? En el acelerado mundo industrial actual, las empresas necesitan sistemas PLC inteligentes, confiables y eficientes.
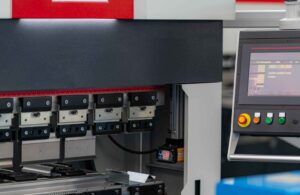
Comprensión de la programación de PLC Mitsubishi: lenguajes y herramientas
En el cambiante mundo de la automatización industrial, seleccionar el lenguaje de programación de PLC adecuado es crucial. Muchos ingenieros y técnicos tienen dificultades para comprender qué lenguajes son los más adecuados para los PLC de Mitsubishi y cómo utilizarlos de manera eficaz para obtener un rendimiento óptimo.
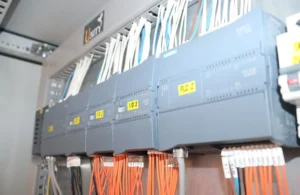
Lo que necesita saber sobre las entradas digitales y analógicas en los PLC
Lo que necesita saber sobre las entradas digitales y analógicas en los PLC ¿Alguna vez se ha preguntado cómo funciona su automatización industrial?