Componentes esenciales de los PLC explicados
Tabla de contenido
¿Qué es un PLC en automatización industrial?
Un controlador lógico programable (PLC) es una computadora especializada que se utiliza para controlar máquinas y procesos. En la automatización industrial, los PLC son esenciales porque brindan sistemas de control flexibles, confiables y eficientes.
Los PLC están diseñados para soportar entornos industriales hostiles y pueden programarse para realizar una amplia gama de funciones de control. Reemplazan los sistemas de control tradicionales basados en relés y ofrecen funciones más avanzadas y mayor confiabilidad.
Características principales de los PLC
- Programabilidad:Los PLC se pueden programar utilizando varios lenguajes de programación para satisfacer requisitos de control específicos.
- Robustez:Diseñado para funcionar en entornos industriales con temperaturas extremas, polvo y vibraciones.
- Operación en tiempo real:Procesa datos de entrada y ejecuta programas de control en tiempo real.
Para obtener información más detallada sobre los PLC, es posible que desee explorar nuestra Productos PLC.
Componentes esenciales de un sistema PLC explicados
Un sistema PLC consta de varios componentes clave que funcionan juntos para realizar funciones de control. Comprender estos componentes es fundamental para entender cómo funciona un PLC.
1. Fuente de alimentación
El módulo de fuente de alimentación proporciona el voltaje necesario que utiliza el PLC. Convierte el voltaje de entrada en los niveles requeridos por el procesador del PLC y otros módulos. La fuente de alimentación convierte el voltaje de CA en voltaje de CC, lo que garantiza que el PLC y sus componentes reciban energía estable.
Puntos clave:
- Suministra energía al PLC y sus módulos.
- Convierte el voltaje de entrada de CA en voltaje de CC utilizado por el PLC.
- Garantiza el funcionamiento confiable del sistema PLC.
2. Unidad central de procesamiento (CPU)
La unidad central de procesamiento (CPU) es el cerebro del PLC. Ejecuta el programa de control, procesa los datos de entrada y toma decisiones basadas en la lógica programada.
Puntos clave:
- Ejecuta el programa de control almacenado en la memoria.
- Realiza funciones lógicas, de secuenciación, de cronometraje, de conteo y aritméticas.
- Gestiona las comunicaciones con otros módulos y dispositivos.
3. Módulos de entrada y salida
Los módulos de entrada y salida (E/S) son componentes cruciales que permiten que el PLC interactúe con dispositivos externos.
- Módulos de entrada:Reciben señales de dispositivos de entrada como sensores e interruptores y las convierten en un formato que la CPU del PLC puede procesar.
- Módulos de salida: Envían señales de control desde el PLC a dispositivos de salida como motores, válvulas y relés. Convierten los comandos de la CPU en acciones.
Puntos clave:
- Interfaz entre el PLC y los dispositivos de campo.
- Los módulos de entrada manejan datos de sensores y dispositivos de entrada.
- Los módulos de salida controlan actuadores y dispositivos de salida.
Para obtener más información sobre los dispositivos de entrada y salida, considere consultar nuestra Sensores Omron y Productos de retransmisión.
4. Memoria
La memoria de un PLC almacena el programa de control y los datos necesarios. Garantiza que la CPU tenga acceso a las instrucciones y la información necesarias para realizar las funciones de control.
Puntos clave:
- Almacena el programa de control y los datos operativos.
- Los tipos de memoria incluyen RAM, ROM y EEPROM.
- Crítico para la ejecución del programa y la retención de datos.
5. Interfaz de comunicación
La interfaz de comunicación permite que el PLC se conecte con otros sistemas y dispositivos, como interfaces hombre-máquina (HMI), sistemas de control de supervisión y adquisición de datos (SCADA) y otros PLC.
Puntos clave:
- Habilita la capacidad de comunicaciones de red.
- Facilita el intercambio de datos con sistemas externos.
- Admite protocolos como Ethernet, Modbus y Profibus.
Explora nuestra gama de HMI para ver cómo complementan los sistemas PLC.
¿Cómo funcionan los módulos de entrada y salida en un PLC?
Módulos de entrada
Los módulos de entrada se utilizan para monitorear el estado de los dispositivos de entrada y enviar esos datos a la CPU del PLC. Manejan señales tanto digitales como analógicas.
- Entradas digitales: señales de encendido y apagado de dispositivos como pulsadores e interruptores de límite.
- Entradas analógicas: señales variables que representan temperatura, presión u otras mediciones continuas.
Puntos clave:
- Convierte señales físicas en datos que el PLC puede procesar.
- Aísla el PLC de las fluctuaciones de voltaje y el ruido.
- Maneja señales de varios dispositivos de campo.
Módulos de salida
Los módulos de salida controlan los dispositivos de salida enviando señales desde la CPU a los actuadores en el campo.
- Salidas digitales: operan dispositivos como luces indicadoras y solenoides.
- Salidas analógicas: dispositivos de control que requieren señales variables, como variadores de velocidad y válvulas de control.
Puntos clave:
- Convierte los comandos de la CPU en acciones.
- Interfaces con motores, relés y otros actuadores.
- Esencial para que el PLC influya en el proceso físico.
El papel de la programación PLC y del software en la automatización
La programación de PLC es el proceso de creación de un conjunto de instrucciones que el PLC sigue para realizar funciones de control. El programa se escribe utilizando un software de PLC especializado y luego se carga en el PLC, donde se almacena en la memoria.
Lenguajes de programación
Los PLC se pueden programar utilizando varios lenguajes de programación:
- Lógica de escalera:Se asemeja a la lógica del relé eléctrico; ampliamente utilizado por su simplicidad.
- Diagrama de bloques de funciones (FBD):Utiliza bloques para representar funciones.
- Texto estructurado (ET):Lenguaje de alto nivel parecido a Pascal.
- Diagrama de funciones secuenciales (SFC):Representa procesos como pasos y transiciones.
Puntos clave:
- Lenguajes de programación permitir flexibilidad en las estrategias de control.
- El programa dicta cómo funciona el PLC monitores Entradas y controles de salidas.
- Programación de PLC Requiere conocimiento de la lógica de control y del proceso específico.
Para obtener más información sobre la programación de PLC, nuestro PLC Schneider Las ofertas incluyen dispositivos que admiten varios lenguajes de programación.
Software de PLC
- Entorno de desarrollo: Proporciona herramientas para programación y simulación.
- Pruebas y simulación: permite probar el programa antes de su implementación.
- Herramientas de comunicación: Facilita la transferencia del programa al PLC.
- Esencial para una programación eficiente del PLC.
- Apoya a los ingenieros de automatización en el desarrollo de sistemas de control confiables.
- Mejora la funcionalidad y flexibilidad del PLC.
¿Por qué los ingenieros de automatización confían en los PLC?
Los ingenieros de automatización utilizan PLC porque proporcionan una solución versátil y confiable para controlar procesos industriales.
Beneficios de utilizar PLC
- Flexibilidad:Fácilmente reprogramable para diferentes tareas y procesos.
- Escalabilidad:Adecuado para máquinas pequeñas y sistemas grandes y complejos.
- Fiabilidad:Diseñado para entornos industriales con alta durabilidad.
- Integración:Compatible con varios dispositivos y protocolos de comunicación.
Aplicaciones
Los PLC se utilizan en una amplia gama de aplicaciones industriales, entre las que se incluyen:
- Líneas de montaje de fabricación
- Sistemas automatizados de manipulación de materiales
- Control de procesos en plantas químicas y petroquímicas
- Sistemas de gestión energética
Para PLC de alto rendimiento adecuados para aplicaciones complejas, considere nuestro PLC de Mitsubishi.
Preguntas frecuentes
Un PLC típico consta de:
- Fuente de alimentación
- CPU (Unidad central de procesamiento)
- Memoria
- Módulos de entrada
- Módulos de salida
- Interfaz de comunicación
Estos componentes trabajan juntos para permitir que el PLC monitoree las entradas, ejecute el programa de control y controle las salidas, formando un sistema de control efectivo.
- Módulos de entrada: convierten señales de dispositivos de entrada (como sensores) en datos que la CPU puede procesar.
- Módulos de salida: convierten los comandos de la CPU en señales que controlan los dispositivos de salida (como motores y válvulas).
Son esenciales para que el PLC interactúe con el mundo físico, permitiéndole monitorear y controlar los dispositivos de campo.
La CPU es el cerebro del PLC y realiza todas las operaciones lógicas y de control. Procesa los datos de entrada, ejecuta el programa de control y actualiza las salidas. La CPU garantiza que el PLC pueda tomar decisiones basadas en la lógica programada.
La programación del PLC define cómo funciona el PLC. El programa se almacena en la memoria y dicta cómo el PLC procesa las entradas y controla las salidas. Una programación adecuada es fundamental para que el PLC realice las funciones de control deseadas con precisión.
La fuente de alimentación proporciona el voltaje necesario que utilizan el PLC y sus módulos. Una fuente de alimentación estable convierte la energía entrante a los niveles requeridos por el PLC, lo que garantiza un funcionamiento confiable.
Sí, los PLC tienen capacidad de comunicación en red y se pueden integrar con HMI, sistemas SCADA y otros PLC. Esta integración permite aplicaciones de automatización avanzadas y control centralizado.
Potencie sus proyectos con PLC Omron, Mitsubishi y Schneider nuevos y originales: ¡en stock y listos ahora!
Conclusión
- Los PLC son fundamentales para la automatización industrial y proporcionan sistemas de control flexibles y confiables.
- Comprender los componentes esenciales de un PLC es crucial para diseñar y mantener sistemas automatizados.
- Los módulos de entrada y salida permiten que el PLC interactúe con el mundo físico procesando señales de los dispositivos de entrada y salida.
- La CPU ejecuta el programa de control, tomando decisiones y realizando funciones de control.
- La fuente de alimentación, la memoria y las interfaces de comunicación son vitales para el funcionamiento del PLC y su integración con otros sistemas.
- La programación de PLC permite a los ingenieros adaptar las operaciones del PLC a aplicaciones de control específicas.
¿Buscas PLC nuevos y originales para tus proyectos? En Kwoco, tenemos en stock los PLC más recientes de las mejores marcas como Omrón, Mitsubishi, y SchneiderCompre con confianza: envío rápido, calidad garantizada. ¡Compre ahora!
Contáctenos
Simplemente complete su nombre, dirección de correo electrónico y una breve descripción de su consulta en este formulario. Nos comunicaremos con usted dentro de las 24 horas.
Categoría de producto
Productos en oferta
También te pueden interesar estos temas
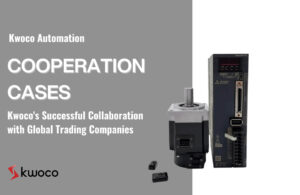
La exitosa colaboración de Kwoco con empresas comerciales globales
La exitosa colaboración de Kwoco con empresas comerciales globales En el mercado global actual, la confiabilidad de la cadena de suministro influye directamente en la
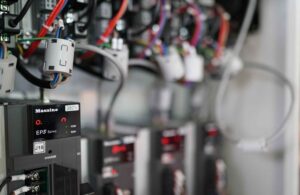
Dominio de los PLC SLC500 y ControlLogix: una guía completa
La automatización industrial ha revolucionado la fabricación y en el centro de esta revolución se encuentran los controladores lógicos programables (PLC). Entre los más destacados se encuentran las series SLC 500 y ControlLogix de Rockwell Automation. Esta guía completa profundizará en estos controladores y le ayudará a comprender sus características, aplicaciones y cómo pueden mejorar sus procesos de automatización.
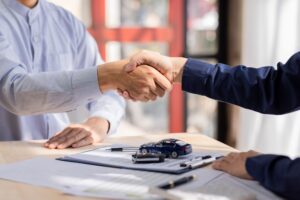
Experimente la tranquilidad con el servicio posventa de Kwoco
Experimente la tranquilidad con el servicio posventa de Kwoco Operamos con la creencia de que nuestro papel se extiende más allá de las meras ventas.